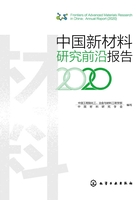
5.1 梯度纳米结构材料研究背景
塑性变形是指材料在外力作用下发生非断裂永久变形的现象[1]。强度是单向拉伸载荷条件下材料抵抗塑性变形的能力,用来衡量承载能力的大小。而塑性(尤其是均匀塑性)表征材料在拉伸时承担不可逆塑性变形但未发生断裂的能力,其大小常作为评价构件在过载等特殊条件下安全服役的准则[2]。因此,强度和塑性不仅是评价材料性能的重要指标,也是工程构件设计和安全服役的关键依据。
近一个世纪以来,材料科学研究的核心问题一直围绕如何提高材料的强度展开[1,3]。20世纪30~50年代发展起来的位错理论表明晶体材料主要通过位错增殖和运动来承担、协调塑性变形[4]。因而通过引入阻碍位错运动的各种缺陷,即可提高材料强度。其中,合金化是大多数工程材料提高性能最常用的策略之一[1,3]。材料合金化的本质是通过加入合金元素改变原有晶格的电子态和应变场,或形成具有不同晶体结构的新相来阻碍位错运动,实现固溶强化或弥散强化。例如,获得高强度钢铁材料的有效手段之一便是在纯铁中添加一定含量的碳形成高硬度渗碳体或马氏体[1]。但是,材料合金化使得材料的发展严重依赖资源,另外也使得资源的回收再利用变得更加困难。
迄今为止,已发展出一系列与材料缺陷相关的强化技术和机制,包括固溶强化、弥散强化、形变强化、细晶强化等[3,5,6]。以细晶强化为例,将材料结构单元(如多晶材料中的晶粒尺寸)减小至纳米尺度,其强度可高达粗晶金属的数倍甚至数10倍。遗憾的是,这些纳米晶材料几乎没有均匀塑性[7-12]。因此,高强度金属材料的强度和塑性倒置关系愈加突出。
究其原因,高强度金属的低塑性源于其有限的加工硬化能力[7,9]。加工硬化能力是指拉伸过程中材料流变应力随应变的变化率[3]。根据Considère准则,当加工硬化能力小于流变应力时,材料发生失稳(即颈缩)。因此,较高的加工硬化能力是获得良好塑性的前提。而加工硬化能力主要与材料在塑性变形过程中位错密度增加,尤其是可以协调塑性变形的可动位错密度的增加有关[9]。例如,对固溶和弥散强化材料而言,由于第二相往往与基体化学成分、弹性模量的显著差异,变形过程中易在相界面处出现应力集中、应变局域化和裂纹,从而降低承载和加工硬化能力。形变强化则主要是通过初始塑性变形在晶内引入高密度位错,致使在后续变形过程中无法继续存储更多位错。细晶强化则因其结构单元(晶粒)尺寸过小,晶内无法存储位错,而晶界变形行为(如晶界滑移或扩散) 在室温条件下也无法启动,加工硬化能力十分有限[3,9]。因此,从本征机制上来看,利用传统强化机制同时实现高强度和良好加工硬化几乎不可能。
而今,“高强度-低加工硬化”的倒置关系已成为严重制约高强度材料工程应用的关键瓶颈问题。在日益严峻的资源短缺和环境污染严重的当下,为了减少对稀缺资源的使用,降低构件制备过程中的能耗,同时又要保障其服役安全性,探索能够提高高强度结构材料的位错存储和加工硬化能力的有效策略迫在眉睫。