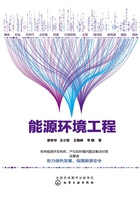
2.6.2 煤炭间接液化
煤炭间接液化是先将煤气化制出以CO和H2为主的煤气,经过变换和净化送入反应器,在一定温度、压力和催化剂的作用下,生产出烃类燃料油及化工原料和产品的加工过程,也称煤基费托(F-T)合成法。
2.6.2.1 煤基F-T合成的工艺过程
煤基F-T合成烃类油一般要经过原料煤预处理、煤炭气化、气体净制、部分气体转换(也可不用)、F-T合成和产物回收加工等工序。其工艺过程如图2-32所示。

图2-32 煤基F-T合成工艺过程
(1)原料煤预处理
根据所选用气化炉对原料煤的要求进行预加工,以提供符合气化要求的原料。通常包括破碎、筛分、干燥等作业。
(2)煤炭气化
煤在高温下与气化剂(氧、水蒸气、CO2等)反应,生成煤气。为了生产合成原料气(CO+H2),通常选用水蒸气和氧气(或空气)作气化剂,在一定范围内通过控制水蒸气/氧气比来调节原料气中H2与CO的比值。
(3)气体净制
由气化炉出来的粗煤气,除有效成分CO+H2外,还含有一定量的焦油、灰尘、H2S、H2O等杂质,这些杂质是F-T合成催化剂的毒物,CO2虽不是毒物,但是非有效成分,会影响F-T合成效率。因此,原料气在进入F-T合成前,必须先将粗煤气洗涤冷却,除去焦油、灰尘;再进一步净制,脱除H2S、CO2、有机硫等。净制方法有物理吸收法、化学吸收法和物理化学吸收法。脱除净煤气中的酸性气体,具体选用哪一种净化工艺,要考虑经济问题,需根据原料气的组成、要求脱除气体的程度及净化加工成本诸因素决定。
(4)气体转换
由气化炉产出的粗煤气经净制后,净煤气中的有效成分H2与CO之比一般为0.6~2,一些热效率高、成本低的第二代气化炉,生产的原料气H2与CO比值很低,只有0.5~0.7,往往不能满足F-T合成工艺的要求,所以在合成工艺前,需将部分净化气或尾气进行气体转换,调节合成原料气的H2与CO比值,以达到合成工艺要求。转换方法一般分为CO变换法和甲烷重整法两种。
气体转化工序的设置取决于F-T合成工艺对原料气组成(H2/CO)的适应性。
(5)F-T合成和产物回收加工
经过气体净制和转换,得到符合F-T合成要求的原料气,再送F-T合成,合成后的产物经冷凝回收并加工成各种产品。F-T合成,由于操作条件、催化剂和反应器的形式不同,形成许多不同的合成工艺。工业上采用的是中压铁剂固定床Arge合成和中压铁剂气流床Synthoil合成。例如SASOL-Ⅰ合成厂采用Arge合成和Synthoil合成联合流程,如图2-33。SASOL-Ⅱ、SASOL-Ⅲ合成厂均采用Synthoil合成工艺,如图2-34,其他工艺尚处于开发阶段。

图2-33 SASOL-I合成工艺流程

图2-34 SASOL-Ⅱ合成工艺流程
2.6.2.2 煤基F-T合成的机理
F-T合成反应的化学计量式因催化剂的不同和操作条件的差异将导致较大差别,但可用以下两个基本反应式描述。
(1)烃类生成反应
CO+2H2(—CH2—)+H2O (2-33)
(2)水气变换反应
CO+H2OH2+CO2 (2-34)
由以上两式可得合成反应的通用式:
2CO+H2(—CH2—)+CO2 (2-35)
(3)烷烃生成反应
nCO+(2n+1)H2CnH2n+2+nH2O (2-36)
2nCO+(n+1)H2CnH2n+2+nCO2 (2-37)
3nCO+(n+1)H2OCnH2n+2+(2n+1)CO2 (2-38)
nCO2+(3n+1)H2CnH2n+2+2nH2O (2-39)
(4)烯烃生成反应
nCO+2nH2CnH2n+nH2O (2-40)
2nCO+nH2CnH2n+nCO2 (2-41)
3nCO+nH2OCnH2n+2nCO2 (2-42)
nCO2+3nH2CnH2n+2nH2O (2-43)
间接液化的主要反应就是上面的反应,由于反应条件的不同,还有甲烷生成反应、醇类生成反应(生产甲醇就需要此反应)和醛类生成反应等。
CO+H2合成气通过各种不同的路线可以制取许多的化工产品,通过F-T合成得到汽油、柴油、石蜡等各种产物。
2.6.2.3 煤基F-T合成过程的工艺参数
以生产液体燃料为目的产物的F-T合成,提高合成产物的选择性至关重要。产物的分配除受催化剂影响外,还由热力学和动力学因素所决定。在催化剂的操作范围内,选择合适的反应条件,对调节选择起着重要作用。
(1)原料气组成
原料气中有效成分(CO+H2)含量高低影响合成速率的快慢。一般是CO+H2含量高,反应速率快,转化率增加,但是反应放出热量多,易造成床层超温。另外制取高纯度的CO+H2合成气的成本较高,所以一般要求其含量为80%~85%。
提高合成气中H2与CO比值和反应压力,可以提高H2和CO利用比。排除反应气中的水汽,也能增加H2与CO利用比和产物产率,因为水汽的存在增加一氧化碳的变换反应(CO+H2OH2+CO),使CO的有效利用率降低,同时也降低合成反应速率。
对于铁催化剂合成,利用残气(尾气)循环可以提高H2与CO利用比。再者,要求合成原料气中含硫量小于2mg/m3(CO+H2),因为含硫量高,易使催化剂中毒失去活性。
(2)反应温度
F-T合成反应温度主要取决于合成时所选用的催化剂。对每一系列F-T合成催化剂,只有当它处于合适的温度范围时,催化反应是最有利的,而且活性高的催化剂,合适的温度范围较低。
(3)反应压力
反应压力不仅影响催化剂的活性和寿命,也影响产物的组成与产率。对铁催化剂采用常压合成,其活性低,寿命短,一般要求在0.7~3.0MPa压力下合成比较好;钴剂合成可以在常压下进行,但是以0.5~1.5MPa压力下合成效果更佳。
压力增加,反应速率加快,尤其是氢气分压的提高,更有利于反应速率的加快,这对铁催化剂的影响比钴崔化剂更加显著。
(4)空速
对不同的催化剂和不同的合成方法,都有最适宜的空间速度范围。如钴催化剂合成的适宜空间速度为80~100h-1,沉淀铁剂Arge合成的适宜空间速度为500~700h-1,熔铁剂气流床合成的适宜空间速度为700~1200h-1。在适宜的空间速度下合成,油收率最高。但是空间速度增加,一般是转化率降低,产物变轻,并且有利于烯烃的合成。
2.6.2.4 煤炭间接液化工艺的特点
煤炭间接液化工艺具有以下特点:
① 合成条件较温和,无论是固定床、流化床还是浆态床,反应温度均低于350℃,反应压力2.0~3.0MPa。
② 转化率高,如沙索公司SAS工艺采用熔铁催化剂,合成气的一次通过转化率达到60%以上,循环比为2.0时,总转化率即达90%左右。壳牌公司的SMDS工艺采用钴催化剂,转化率甚至更高。
③ 受合成过程链增长转化机理的限制,目标产品的选择性相对较低,合成副产物较多,正构链烃的范围可从C1至C100;随合成温度的降低,重烃类(如蜡油)产量增大,轻烃类(如CH4、C2H4、C2H6等)产量减少。
④ 有效产物-CH2-的理论收率低,仅为43.75%,工艺废水的理论产量却高达56.25%。
⑤ 煤消耗量大,一般情况下,约5~7t原煤产1t成品油。
⑥ 反应物均为气相,设备体积庞大,投资高,运行费用高。
⑦ 煤基间接液化全部依赖于煤的气化,没有大规模气化便没有煤基间接液化。
2.6.2.5 煤炭直接液化和间接液化工艺过程的比较
煤炭直接液化和间接液化工艺过程的比较如表2-7。
表2-7 煤炭直接液化和间接液化工艺过程的比较

表2-8为煤炭直接液化工艺和间接液化工艺特点的比较。
表2-8 煤炭直接液化和间接液化工艺特点的比较

通过直接液化和间接液化相组合以优化最终油品性能,通过煤炭分级利用以提升能量利用效率,通过油煤混炼或引入焦炉煤气以实现原料的多元化,通过IGCC和其他化学品装置实现多联产,是我国煤制油行业的发展趋势。