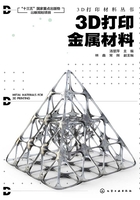
2.1.1 粉末特性对金属3D打印工艺过程的影响
(1)粉末形貌、流动性对3D打印工艺过程的影响
粉末形貌包括颗粒的形状和表面光滑度,会对粉末流动性产生重要影响[4]。粉末形状越接近于球形、表面光滑度越高,则粉末流动性能越好。目前针对粉末颗粒形貌的表征手段主要以光学显微镜和扫描电子显微镜为代表的图像法为主,例如全自动静态图像法粒度分析仪可以直接给出粉末颗粒的球形度及其赘生指数(表示金属粉末的卫星化程度)[5]。
粉末的形貌与制备技术直接相关。图2-1比较了不同技术制备的粉末形貌:气雾化粉末多为近球形,表面卫星球较多;旋转雾化与等离子旋转电极雾化粉末表面光滑,但是旋转雾化粉末球形度差,其中哑铃形颗粒较多,而等离子旋转电极雾化粉末无论球形度还是表面质量都相对优异。

图2-1 不同粉末制备技术对粉末形貌的影响[6]
华中科技大学采用自主研发的HRPM-Ⅱ SLM设备[7],研究了水雾化(water atomization,WA)和气雾化(gas atomization,GA)工艺制备的316L粉末激光选区熔化(selective laser melting,SLM)打印件致密度。结果表明,GA粉末由于具有良好的球形度和较高松装密度,在激光能量密度为64~84J/mm3时,其打印件致密度高于WA粉末,如图2-2所示。另外,需要指出的是,当激光能量密度提高到104J/mm3时,两种粉末均可实现相对致密(96%~97.5%)[8]。

图2-2 气雾化与水雾化粉末形貌(a)及打印样件截面组织图(b)[7]
M.N.Ahsan[9]则对比了GA粉与等离子旋转电极雾化(plasma rotating electrode process,PREP)粉在定向能量沉积工艺中对打印制品的影响(打印使用1.5kW二极管双波长激光器配合同轴喷头)。微区CT扫描显示PREP粉具有更好的球形度,卫星颗粒附着更少,其空心粉比率不到GA粉的1/3。因此PREP粉末的打印制品的打印层间孔隙率更低,沉积速率更高,如图2-3所示。

图2-3 气雾化粉与等离子旋转电极雾化粉形貌(a)及其对打印样品性能的影响(b)[9]
保证粉末良好的流动性能是金属3D打印工艺的重要基础。无论是粉末床熔融技术中粉末的均匀铺展,还是定向能量沉积技术中粉末输送的稳定性,都需要粉末具有优良的流动性。A.Strondl[10]研究了激光选区熔化和电子束选区熔化技术中颗粒形状对流动性的影响。分析表明,表面光滑的球形颗粒可以减小颗粒之间的摩擦,使粉末容易沉积而获得良好的致密度。此外,通过监控粉末连续循环利用过程中颗粒球形度的变化发现,即使很小的形状变化,也将会显著改变粉末的流动行为,降低打印样品的质量。Sun[11]通过计算粉末“球形因子”,研究电子束选区熔化(SEBM)工艺循环利用中粉末的形貌演化,发现随着打印次数增加,粉末颗粒形貌的“球形因子”减小,颗粒间摩擦力增加,进而导致粉末流动性降低。因此,高度球形化、表面光滑且干燥的粉末是保证粉末颗粒间最小摩擦力、获得最佳流动性的必要条件。
粉末流动性是休止角、崩溃角以及压缩率等不同参数指标的综合表征,不仅限于单个指标的测量。根据测量结果[12],来自不同生产商(EOS、LPW、Raymor)的3D打印用Ti-6Al-4V粉末的休止角(angle of repose,AOR)差异较大,但是在打印过程中(EOS DMLS M270)的粉末床密度(powder bed density,PBD)却无显著差别,如图2-4所示。

图2-4 不同供应商Ti-6Al-4V粉末的休止角(a)与粉末床密度(b)[12]
Spierings[13]采用旋转粉末分析仪(revolution powder analyzer)系统地评价了23种SLM技术专用Fe、Ni合金粉末的流动性指标,并与豪斯纳比率(Hausner ratio)、压缩率、崩溃角以及崩溃表面分数等参数进行对比分析后认为,在不考虑粉末粒径分布和形状的情况下,豪斯纳比率[14]不能很好地表征细粉的流动性,而崩溃角以及崩溃表面分数则与旋转粉末分析仪所获得的流动性结果一致(图2-5),并建议将其作为3D打印粉末流动性测试的ASTM标准。值得一提的是,金属粉末流动性的量化指标与储粉、铺粉技术和设备相关:同样的粉末材料,采用不同的铺粉尺(ruler)和粉辊(roller)的铺粉密度也不相同[15]。

图2-5 3D打印金属粉末流动性分析[13]
此外,粉末流动性能也受颗粒表面湿度的影响。颗粒表面湿度可以增加颗粒间的摩擦系数,导致粉末流动性变差。因此研究粉末的湿度与其流动性能的关系,可以帮助研究人员了解打印过程中粉末、环境以及工艺之间的交互影响,但是目前相关研究尚不多见。LPW公司研究发现[16],潮湿粉末会导致部件内部卷入气体,打印时释放出氧元素和氢元素,恶化打印部件性能。N.Vluttert[17]研究了Ti-6A1-4V、AlSi10Mg和Inconel 718 SLM粉末湿度随时间的变化,尽管粉末湿度变化不大,但是粉末已经出现结块现象。需要指出的是,文献中的研究时间跨度为23天,对粉末产生的影响十分有限,同时粉末的生产、存储历史难以回溯,需要进一步的评估。
粉末形貌随粉末循环使用次数而改变。粉末熔融过程中,靠近熔池附近的颗粒受到热影响作用以及熔池飞溅作用,颗粒之间发生焊合,形成异形颗粒以及卫星球。图2-6是Inconel 718高温合金在EOS-M400设备上第1次使用与循环使用10次以后粉末的形貌对比[18]。从图中可以看出,在循环使用10次以后,粉末的卫星球增多,造成粉末流动性降低。而在Arcam A2型设备上打印Ti-6Al-4V时,第1次使用与循环使用21次的粉末对比表明,虽然形貌明显由球形变为了非球形,但流动性的变化不大,卫星球也很少见,对打印工艺没有影响,这可能与SEBM技术对粉末经高压气体吹散并过筛后使用有关。

图2-6 Inconel 718合金原始粉末(a)与循环使用10次后的粉末形貌(b)[18]
(2)粉末的粒度分布对3D打印工艺过程的影响
粉末的粒度直接影响3D打印特征熔池的最小厚度,从而影响打印部件最小特征尺寸。研究表明,粒度分布越宽,在SLM工艺中,更易获得高的松装密度、振实密度以及铺粉密度,从而使制件致密度更高。Liu等[19]使用MCP-HEK公司的商用SLM工作站“MCP SLM-Realizer 100”,对比研究了Osprey公司和LPW公司提供的316L不锈钢粉末,结果发现,相较于LPW粉末,Osprey粉末粒度分布宽、球形度偏低、粉末松装密度和铺粉密度高。在相同激光参数下,宽粒度分布的Osprey粉末制件内部孔隙少,致密度更高(如图2-7所示)。

图2-7 不同粒径分布的316L粉末及SLM打印样品的致密度[19]
Gu[12]表征了EOS、LPW和Raymor三家粉末供应商生产的3D打印用Ti-6Al-4V合金粉末(图2-8),并在EOS DMLS M270系统上统一采用Raymor粉末的优化打印工艺时,EOS和LPW粉末SLM打印致密度不佳(图2-9),而采用各供应商给出优化的3D打印参数,均可以实现理想致密度(图2-10)。由此可以看出,粉末粒度与分布直接影响到3D打印工艺参数的调整优化策略。

图2-8 不同粉末供应商提供的Ti-6Al-4V粉末粒径分布[12]

图2-9 相同打印参数下不同Ti-6Al-4V粉末SLM打印样品的致密度[12]

图2-10 优化打印参数下不同Ti-6Al-4V粉末SLM打印样品的致密度[12]
J.Karlsson[20]利用Arcam A1 EBM设备打印Ti-6Al-4V合金,使用的粉末粒径分布分别为25~45μm和45~100μm,通过对比发现样件在化学成分、宏观和微观组织以及力学性能上差异不大,仅在表面粗糙度上存在差别,如图2-11所示。这是因为相较于激光束,电子束光斑尺寸和能量利用率更大,从而降低了打印过程对粉末粒径分布的敏感性。

图2-11 Ti-6Al-4V合金45~100μm(层厚70μm)(a)、25~45μm(层厚50μm)(b)的EBM打印样品表面质量[20]
通过研究粉末粒度分布对3D打印工艺的影响,可以对3D打印用金属粉末参数进行优化。Lee等[21]将模拟与实验研究相结合,研究了粉末床激光熔池的传热与流动性,阐明了粉末粒径分布对熔池边缘“球化(balling)”缺陷以及激光飞溅效应的影响。研究发现通过增加粉末堆积密度(从38%到45%),可以减少3D打印中球化缺陷的产生(如图2-12所示)。

图2-12 不同粒径分布对SLM打印过程中熔池的影响
(a)采用细粒径粉末的熔池形貌平滑;(b)采用粗粒径粉末的熔池边缘波动较大[21]
综上所述,对于SLM、EBM为代表的粉末床基3D打印技术而言,粉末粒度对打印样品表面质量、致密度、力学性能等均有显著的影响,打印样件的质量和性能是所选用金属粉末的特性与3D打印工艺参数相互影响与作用的结果,两者的关系是密不可分的。
(3)粉末性能对3D打印工艺过程影响机理
针对粉末性能对3D打印工艺与制件质量的影响,特别是粉末床熔融技术中,粉末性能的影响,需要研究粉末颗粒与能量束的相互作用、能量与动量传输等机理,从而阐明粉末性能对3D打印的调控机制。尽管,在SLM技术研究中,激光熔池的传热、传质难以通过实验手段观察,基于计算机模拟研究粉末床熔融、凝固过程的方法是当前研究的主要手段,然而,原位监控作为3D打印技术规模化应用的保证,其研发越来越多地受到了各设备供应商的重视。激光与粉末颗粒/粉末床的作用十分复杂,包括粉末颗粒对激光的吸收、透射和反射;粉末颗粒熔化与熔池内的流动;粉末的气化与熔池蒸发;蒸汽对激光的散射作用;熔池的传热与凝固等现象,此外还需考虑能量束的运动轨迹,如图2-13所示[22]。

图2-13 激光与材料相互作用示意图[22]
粉末性能中,比较关注的是粉末粒度分布对激光吸收效果的影响。首先,粉末粒度分布的差异可以影响入射能量束吸收系数。除了材料本身固有吸收系数,随着粉末粒径减小,表面积增大,入射能量束的散射作用增强,粉末颗粒间存在空隙,这使得打印前铺就的粉末层可以被视为多孔介质层。美国劳伦斯利弗莫尔国家实验室基于第一性原理射线追踪(ray tracing)模型计算了粉末对激光的吸收系数[23],如图2-14所示。计算结果和实验证明,粉末粒度分布对激光吸收系数影响非常大。粗粒径粉末的吸收系数(0.55)明显低于细粒径粉末(0.70),说明在同样的激光束条件下,粒径小的粉末吸收的激光能量更多。

图2-14 基于第一性原理射线追踪模型(a)、局部细节(b)及粒度分布对激光吸收系数的影响(c)[23]
此外,粉末颗粒在粉末层中处于较松散状态,粉末颗粒间的接触点越多,传热越均匀,传热系数越高[24]。在同样的激光束照射下,由于细粉的存在,粉末床密度更高,粉末传热性能更优,因此粉末层累积热量更容易传导至成形底板,从而使粉床具有更低的温度[12]。根据传热理论,将粉末层视为开放多孔介质,建立网状传热模型。根据计算结果,粉末性能,特别是粉末粒径分布,对传热系数的提高有重要影响。随着粉末粒径的减小和粒径分布变宽,传热系数明显提高。
研究显示(如图2-12所示)[21],细粉末可以增加熔池稳定性,但是该研究忽略了熔池中的反冲压力和蒸发作用,然而相对全面的熔池物理模拟(如图2-15所示)[25]却没有讨论粉末粒径分布的影响。实验手段方面,最近有研究通过原位同步X射线研究了SLM沉积第一层和第二层焊道粉末飞溅、熔池飞溅对剥蚀、孔隙缺陷形成的影响,以及Marangoni对流驱动下孔隙的运动,如图2-16所示[26]。可以预见随着研究的深入,模拟和实验手段日益精准和完善,揭示粉末性能对粉末床熔融3D打印技术的影响规律及其机理将进一步推进3D打印技术的应用普及。

图2-15 粉末熔化和熔池凝固的3D模拟结果,模型考虑蒸发、辐射、对流、热传导和质量传输等多物理场的作用[25]

图2-16 原位X射线高速成像技术观察激光与粉末相互作用及其对组织的影响:沿激光扫描方向出现金属蒸气、粉末卷入熔池、Marangoni对流、粉末溅射和液滴溅射[26]