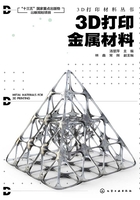
2.2 金属3D打印用粉末制备技术及国内外发展现状
2.2.1 金属3D打印用粉末代表性制备技术
从目前的发展趋势来看,气雾化、等离子旋转电极雾化、等离子熔丝雾化和射频等离子球化是目前3D打印粉末制备领域的主要技术,如表2-2所列。
表2-2 3D打印用金属粉末制备技术概览

(1)气雾化技术
气雾化制粉技术是目前制备球形粉末最普遍的方法。其历史起源于20世纪20年代,属于二流雾化范畴,是采用高速惰性气体直接将熔融金属或者合金液体击碎凝固冷却得到粉末的方法。高速运动的气流和金属液流接触,这个过程既有动量的传递又有热量的交换,气流既提供破碎的能量又是冷却介质,整体连续的液体流受到气体流的冲击,在剪应力的作用下分散破碎为尺寸不一的液滴。具体过程如下:首先,母合金置于真空感应炉熔炼至熔融状态,熔融态的合金液流流入雾化喷嘴被高速气流击碎形成细小液滴,液滴在雾化室飞行过程中迅速冷却凝固为粉末颗粒,粉末颗粒最终被粉末收集系统收集。根据熔炼方式的不同,衍生出了多种气雾化技术,最适合于3D打印用金属粉末制备的技术有真空感应熔炼雾化(vacuum induction gas atomization,VIGA)和电极感应熔炼雾化(electrode induction gas atomization,EIGA),如图2-28所示。
VIGA是将金属在真空状态下在坩埚中进行熔炼[如图2-28(a)所示],陶瓷坩埚主要适用于Fe基合金、Ni基合金、Co基合金、Al基合金和Cu基合金等非活性金属粉末的制备。对于钛合金等活性金属及其合金而言,熔化条件下会与陶瓷坩埚剧烈反应,从而对粉末造成污染,故需采用水冷铜坩埚。

图2-28 不同气雾化技术[42,43]
EIGA属于惰性气体雾化中的一种,其基本原理是将合金加工成棒料安装在送料装置上,对整个装置进行抽真空并充入惰性保护气体,电极棒以一定的旋转速度和下降速度进入下方锥形线圈,棒料尖端在锥形线圈中受到感应加热作用而逐渐熔化形成熔体液流,在重力作用下,熔体液流直接流入锥形线圈下方的雾化器,高压氩气经气路管道进入雾化器,在气体出口下方与金属液流发生交互作用,经过高压气体作用将液流破碎成小液滴。液滴在雾化室飞行过程中,由于自身表面张力球化凝固形成金属粉末[如图2-28(b)所示]。
EIGA制备金属粉末具有以下特点:①其熔化过程不与坩埚接触,故适用于制备各种活性金属,例如Ti、Zr、Nb等;②粒度分布宽,可满足多种工艺用粉,例如,注射成形、3D打印、粉末冶金、喷涂、激光熔覆、焊接修复等;③粉末纯度高、球形度好、组织均匀;④相比于PREP,细粉收得率高,D50一般在40~100μm左右。
气体雾化法具有产量大、效率高的优点,是目前制备3D打印用合金粉末中最成熟的工艺之一。相比于离心雾化法,采用气体雾化法制备的合金粉细粉收得率较高、平均粒度较小、夹杂物尺寸小。但是由于采用气体雾化法制备的合金粉末粒径较小,粉末比表面积较大,导致氧含量不可避免的有所提高;同时由于雾化流场的特点,容易出现小尺寸液滴与大尺寸液滴撞击,二者没有发生完全熔合,冷却后小颗粒便依附在大颗粒表面形成卫星球,这些缺陷从一定程度上影响了粉末的性能,因此必须对工艺进行优化控制。例如,通过调节气雾化压力以及喷嘴结构,可以有效改善粉末球形度,如图2-29所示。

图2-29 雾化工艺改进前后制备的镍基粉末形貌[44]
气雾化机理以及喷嘴结构是优化气雾化工艺的重要基础。雾化过程对于雾化制粉而言是最核心的阶段,研究雾化过程的机理可以有效地对液滴生成控制起指导作用。
在初始阶段,主要存在波动破碎和膜状破碎两种方式。Bradley在Rayleigh和Taylor的基础上提出了众多学者较为认可的雾化模型,该模型用Kelvin-Helmholtz不稳定波理论描述液流破碎过程。Bradley破碎模型参照了Rayleigh的毛细管不稳定理论,从导流管流出的金属流体在雾化气流的作用下,首先在液态金属表面形成扰动波,随着时间的增长,波的振幅逐渐增大,当达到临界振幅时,波峰与主流剥离形成棒状液滴,这些棒状液滴又在表面张力的作用下迅速收缩、破碎成较小的球形液滴(图2-30)。这种剥离作用是由气体作用在液流表面突起和小波纹上的压力变化引起,雾化过程中液流的分散主要依赖于液体与周围气体的压力差所产生的驱动力,这种驱动力与气体的动压成正比,所以气、液相对速度是决定雾化过程的重要因素。

图2-30 Bradley破碎模型(a)[45]和液体表面破碎过程(b)[46]
气雾化喷嘴结构是气雾化机理的核心体现。它的主要作用是将液态金属在高速气流的作用下破碎成细小的液滴。根据不同的方式,雾化器可以分成不同的类型。按金属液和雾化气体交汇位置的不同,可以分为自由落体式雾化器、紧密耦合式雾化器(图2-31)[47];按雾化气体喷出的方式,可以分为环孔雾化器、环缝雾化器;按喷出气体的速度又可以分为亚音速雾化器、超音速雾化器。雾化器设计应满足以下条件:①能使雾化气体获得尽可能大的出口速度和所需要的能量;②雾化气体和金属液流之间形成最合理的交汇角度;③使金属液产生最大的紊流;④工作稳定性好,导流管不易堵塞;⑤拆卸安装方便。

图2-31 两种典型气雾化喷嘴示意图[47]
A—气流出口与液流距离;a—喷射角;L—导液管突出长度;D—导液管直径
为了提高雾化气体动能,在雾化器设计中加入了一定的喷管结构。用于气体加速目的的喷管有两种结构:汇聚型结构和汇聚发散型结构,其中汇聚发散型喷管又称为Laval喷管,可以将气流加速至超音速。
(2)等离子旋转电极雾化
等离子旋转电极雾化(plasma rotating electrode process,PREP)技术是一种通过将高速旋转的棒料端部熔化,金属液滴在离心力作用下飞出并在惰性介质环境中冷却成固态而制备球形金属粉末的方法。这种制粉方法在1974年由美国核金属公司首先开发成功。在等离子枪的作用下,利用大功率熔化超高转速的电极棒,在合金电极棒一端产生约20000℃的高温,以形成10~20μm厚度的金属熔化层,在电极棒超高转速旋转的条件下,金属液滴所受的离心力逐渐克服金属熔化层的黏滞力,在合金棒的径向形成小液滴,就是“冠”。随着“冠”的积累,形成“露头”,最终在大尺寸的雾化室内通过自由落体和低温氦气的冷却而形成近似球状的金属粉末颗粒脱离合金棒,如图2-32所示。其基本的流程包括:等离子旋转电极制粉→筛分(在真空或者惰性气体保护条件下,将粉末按照粒度分级)→包装。
PREP法制得粉末颗粒直径可由下式确定:
(2-1)

图2-32 PREP设备示意图(a)、液滴形成过程图(b)[48,49]
1—雾化室;2—电极系统;3—粉末收集罐;4—等离子枪;5—电机
式中,d代表粉末平均粒径;k代表系数;γ代表熔体表面张力;ρ代表金属密度;D代表棒料直径;n代表棒料转速。由公式可见,制得粉末平均粒径与液滴表面张力成正比关系,与金属密度ρ、棒料直径D与棒料转速n成反比。
由于每次等离子雾化制粉过程严格控制充入雾化室的Ar气体量,故在整个制粉过程中等离子弧电压的变化不大,等离子弧电流的强度变化基本上反映了等离子枪输出功率的变化。研究发现,粉末平均粒径随等离子弧电流强度的增大而有明显细化的趋势。但是,提高电流会带来诸多弊端,其一,粉末粒度的分布范围随电流强度的增大而变宽的趋势十分明显,如图2-33所示。其二,电流增大直接反映了等离子枪能量增大,也意味着等离子弧温度增高,容易造成低熔点元素的烧蚀。

图2-33 不同电流强度下粉末粒度分布[50]
根据实验结果,若热源是转移弧等离子枪,在保持电流与电压不变情况下,等离子有效功率与等离子体和棒材端部间距有关,并影响棒料端部熔池大小与形状。间距越小,等离子枪有效功率越大,熔池和熔化速率也随之增大,粉末粒径细化明显。但是间距的减小会加剧钨电极和喷嘴的损耗,部分熔化的材料会对粉末造成污染。
PREP法制备粉末特点为:①粉末粒径分布窄,粒度更可控,球形度高。制备合金粉末粒度主要分布在20~200μm之间。②制得粉末基本不存在空心球和卫星球。③粉末陶瓷夹杂少、洁净度高。④粉末氧增量少,PREP粉末氧增量可控制在0.005%以下。
上述特点使得PREP法制备的粉末应用于3D打印具备以下优势:①粉末粒度分布窄,在打印过程中少球化、团聚现象,表面光洁度高,打印的一致性和均匀性可得到保障。②粉末球形度高,流动性好,铺粉均匀性好,松装密度高,打印制品致密度更高。③基本不含空心球,在打印过程中不会存在空心球带来的卷入性和析出性气孔、裂纹等缺陷。④粉末氧含量低,表面活性小,润湿性好,熔化效果好。以上优势保障了3D打印件具有较高的强度、塑性与持久性能,延长了3D打印件的寿命。PREP制备钛合金粉末形貌图见图2-34。

图2-34 PREP制备钛合金粉末形貌图
PREP制粉技术的问题在于:受电极棒转速与工艺的限制,细粉收得率低,导致细粉生产成本较高。目前,通过动密封技术的应用,可使电极棒转速达到30000r/min以上,极大提升了设备制备细粉的水平。对于钛合金粉末,虽然<45μm的粉末收得率较低,但45~100μm的粉末收得率较高,可适用于EBM技术。通过工艺参数的合理匹配提高细粉收得率,同时通过静电去除夹杂技术进一步提升粉末的纯净度,对实现PREP粉末批量化生产具有重要意义。
(3)等离子熔丝雾化
等离子熔丝雾化(plasma atomization,PA)技术是利用等离子热源制备球形粉末的技术,由加拿大Pegasus Refractory Materials公司的Peter G.Tsantrizos, Francois Allaire,Majid Entezarian 等人[51,52]于1995年发明。随后加拿大AP&C公司将等离子雾化技术商业化,由于其母公司Arcam被美国GE公司收购,因此目前等离子雾化技术所有权归美国GE公司。等离子雾化技术原理是将金属及其合金、陶瓷材料以丝材、棒料或液流的方式通入汇聚的等离子射流中心,在超音速等离子射流撞击下发生雾化,随后冷却凝固形成球形粉末。伴随着等离子枪技术的发展,等离子射流获得了更高的速度,雾化粉末的中位径由最初的100~300μm降低为30~60μm,使之适合于激光和电子束增材制造工艺。
AP&C公司丝材等离子射流雾化技术原理如图2-35所示,首先将丝材校直后送入三束汇聚的等离子射流中心,在高焓的等离子射流加热条件下,丝材端部发生熔化,熔融液体在汇聚的超音速等离子射流撞击下发生雾化,破碎液滴在表面张力作用下发生球化,随后在飞出等离子射流后冷却凝固形成高球形粉末。三个非转移弧等离子枪按照与垂直方向成30°均匀排列,等离子枪的功率一般为20~40kW,氩气的流量一般为100~120L/min。

图2-35 等离子射流雾化粉末技术示意图[53]
PA技术采用超音速等离子气体雾化粉末,相较于VIGA和EIGA工艺,耗气量非常低,粉末空心缺陷得到较大改善;另外破碎雾化液滴在飞出等离子射流前有足够时间球化,因此等离子雾化粉末具有和PREP工艺和射频等离子球化(radio frequency plasma spheroidization,RFPS)工艺制备的粉末相当的球形度,故粉末具有较好的流动性;再者,等离子射流具有极高的温度,覆盖所有的金属及其合金熔点范围,因此等离子雾化技术几乎可以制备所有能拉成丝材的金属及其合金材料。
①活泼类金属及其合金粉末 由于等离子雾化技术采用丝材作为原材料,粉末制备过程中不使用坩埚,避免了在熔炼过程中坩埚的污染,因此可以像EIGA、PREP和RFPS工艺一样制备高纯粉末。加拿大AP&C公司制备的钛合金Ti-6Al-4V粉末形貌如图2-36所示,粉末有高球形度、高流动性和低氧含量(低至0.07%),占据全球高端钛合金粉末在航空航天及医疗应用领域80%份额。

图2-36 加拿大AP&C公司等离子雾化技术制备的Ti-6Al-4V合金粉末形貌[54]
②高温合金粉末 高温合金是指在650℃以上和一定应力条件下长期工作的高温金属材料,具有优异的高温强度、良好的抗氧化和抗热及燃气腐蚀性能、良好的抗高温疲劳性能和断裂韧性等综合性能。随着工业的高速发展,高温合金在各个领域中展现了良好的应用前景,比如制造燃气涡轮发动机的涡轮叶片、导向叶片、涡轮盘、高压压气机盘和燃烧室等高温部件。镍基高温合金材料的制备工艺主要有VIGA、EIGA和PREP等,VIGA和EIGA工艺制备的高温合金粉末含有较多卫星球,PREP工艺制备的高球形粉末,不含空心粉,但粉末在细粒径区间收得率较低。加拿大AP&C公司的PA技术为制备高品质的镍基高温合金粉末材料提供了新的选择,然而需要指出的是,PA技术的生产效率低于其他几种工艺。
③难熔金属及其合金粉末 由于等离子射流的温度高达上万度,因此可以高效地熔化高熔点金属及其合金,如W、Ta金属及其合金材料,实现高球形度W、Ta粉末的制备。
④稀贵金属粉末 稀贵金属Au、Ag粉末通常采用化学反应进行制备,如银粉是通过化学还原硝酸银进行制备,金粉末通过锌粉、铁粉等还原氯金酸进行制备,制备的粉末形貌不规则,且细粉容易团聚。采用丝材等离子雾化技术可以实现稀贵金属粉末的制备,满足3D打印工艺对粉末粒径和流动性的要求。
⑤改性高强铝合金粉末 铝合金材料以其优异的性能在航空、航天、汽车、机械制造、船舶及化学工业等领域获得广泛应用,但是3D打印高强铝合金材料仍然存在困难,尤其针对6系和7系的铝合金,打印制品中含有较多的凝固裂纹,这主要是由于微型熔池在快速凝固过程中熔融铝合金未能补缩粗大枝晶间的间隙,并在凝固后期在拉应力的作用下形成裂纹。如果能将凝固组织优化为等轴晶组织,那么可以极大抑制枝晶裂纹的产生。将高强铝合金丝材校直后送入到三束汇聚等离子射流的中心,同时将TiCl4和CH4混合气体通入等离子射流中,发生化学反应合成碳化物TiC[TiCl4(g)+CH4(g)TiC(s)+4HCl(g)],那么生成的纳米TiC就会在雾化破碎的高强铝合金液滴表面形核生长,冷却凝固后形成陶瓷颗粒相分布相对均匀的复合粉末;同样可以将碳化物SiC加入高强铝合金粉末中[SiCl4(g)+CH4(g)
SiC(s)+4HCl(g),CH3SiCl3(g)
SiC(s)+3HCl(g)],从而实现丝材熔化、雾化破碎和碳化物陶瓷相形核剂的化学合成及同步添加。
AP&C公司采用等离子雾化技术制备的钛及钛合金粉末以其优异的性能在航空航天和医学领域获得广泛应用。因此,基于等离子雾化技术及装备具有重要的潜在研发价值与市场应用前景,我国亟待自主研发丝材低压等离子雾化装备,打破国外垄断,解决阻碍增材制造技术发展的“卡脖子”装备及材料,从而提升及推动增材制造行业技术水平及市场竞争力。
(4)射频等离子球化
射频等离子球化技术是利用射频等离子体的高温特性把送入到等离子体中的不规则形状粉末颗粒迅速加热熔化,熔融的颗粒在表面张力和极高的温度梯度共同作用下迅速凝固而形成球形粉体。球形粉末具有纯度高、粒径分布均匀、流动性好、空心粉少等优点。射频等离子球化过程如图2-37所示。

图2-37 射频等离子球化过程示意图[55]
射频等离子体具有温度高(约104K)、等离子体炬体积大、能量密度高、无电极污染、传热和冷却速度快等优点,是制备组分均匀、球形度高、流动性好的高品质球形粉末的良好途径,尤其在制备稀有难熔金属、氧化物、氮化物、碳化物等球形粉末方面优势明显,如W、Mo、Ta、Nb、WC、TiN、ZrO2等。射频等离子球化制粉设备一般包括等离子发生装置、球化反应系统、水冷却及气体循环系统、控制系统等,设备构造非常复杂。加拿大TEKNA公司是全球顶尖的等离子研究与球化设备制造单位,应用等离子体技术已实现W、Mo、Re、Ta、Ni、Cu等金属粉末和SiO2、ZrO2、YSZ、Al2O3等氧化物陶瓷粉末的球化处理。国内北京科技大学、核工业西南物理研究院、中国科学院过程工程研究所等科研机构自行研发组装等离子设备,但所组装的设备自动化程度较低、安全隐患大、生产效率低、可持续稳定运行时间短,难以规模化工业生产,因此目前国内以引进加拿大TEKNA公司的设备开展相关领域的研究和生产为主。
原料在射频等离子体高温作用下容易发生物理和化学变化:低熔点或低沸点的金属在等离子球化过程中,难免发生不可控的蒸发、气化,制备的球形粉末表面存在大量由于蒸发、凝固得到的纳米或亚微米级超细粉体,后续收集、清洗、分级工序较为繁琐、困难,造成粉末收得率较低;对于成分敏感的原料,例如铸造碳化钨,等离子体作用下存在碳元素流失问题。另外,等离子球化以不规则粉末为原料,原料粉体粒度过细(<10μm)易造成流动性差、团聚严重等问题,操作过程中送粉困难,球化无法顺利进行。制备过程中需根据原料粉体特性,通过调控送粉速率、载气流量、等离子体功率等工艺参数以实现粉体的充分球化。
随着送粉速率增加,单位时间内通过等离子体的粉末增多,使粉末完全球化所需要的能量也增加,而系统在固定的工艺条件下所能提供的能量为有限的定值,不能满足过多粉末的吸热、熔化和球化的需要,致使粉末的球化率降低。另外,提高送粉速率,使粉末在等离子体炬中的运动轨迹变得混乱,部分颗粒未能穿过高温区也会造成球化率降低。不同送粉速率下球化钽粉形貌如图2-38所示。

图2-38 不同送粉速率下球化钽粉形貌
载气流量直接影响粉末射入等离子体高温区的速度和粉体分散状态,进而决定了颗粒在等离子体内的滞留时间、运动轨迹与分散状况。载气流量过大,粉末进入等离子体炬的速度就会过大,粉末在等离子体炬滞留的时间缩短,会导致最终球化效果降低。同时,载气量过大时,粉末的分散状态变差,存在颗粒彼此碰撞而导致颗粒黏结,也会导致粉末的球化率下降。不同载气流量下球化铸造碳化钨粉形貌如图2-39所示。

图2-39 不同载气流量下球化铸造碳化钨粉形貌
1slpm=0.06m3/h
此外,适中的射频等离子体功率,对等离子体球化的效果也十分重要。在球化过程中功率过低时,粉末不能得到足够的能量以使之完全球化;功率过高时,粉末会发生过烧结与蒸发损失现象,同样导致球化率较低。另外等离子球化效果与粉末的粒度及分布也息息相关,这是因为粉末的熔化温度与其粒径有关,原始粒度越细,比表面积越大,熔化温度越低,越容易被蒸发;粉末原始粒度越细,粉末之间的范德华力越强,易以团聚状态存在,导致最终的球化率下降;而粒度分布不均匀时,在穿越等离子体炬时,受热及熔化程度不均匀,使粒径较细的粉末易出现蒸发,最后会导致颗粒的增大。
目前,针对射频等离子球化制粉技术的研究主要集中在球化工艺参数的优化方面,而对射频等离子体温度场、速度场、流场等特性对工艺参数和球化过程影响机理缺乏了解。近年来,随着计算机数据处理能力与数值模拟技术的快速提高,有限元等分析软件日趋完善,北京科技大学、西南核物理研究院等单位越来越多地借助数值模拟的方法来认识、分析并解决射频等离子球化的实际问题[53]。等离子体流场、温度场特征,粉体粒度及工艺参数等是影响等离子体球化的主要因素,借助数值模拟的方法,可避免实际球化过程监测困难、成本高、产品开发周期长等问题。北京科技大学曲选辉团队将射频等离子体视为磁流体(MHD),利用FLUENT有限元流体分析软件研究了等离子体的传热与流动,计算了流场、温度场和速度场,利用DPM离散相模拟研究颗粒在等离子体中的运动轨迹,并根据颗粒运动轨迹对收粉率等问题进行了探讨。
射频等离子球化的数值模拟涉及几何建模、网格划分、基本假设、湍流与层流判断、控制方程选择、边界条件与求解器设置以及计算分析等方面。其中基本假设一般为:
①等离子体发生器完全满足轴对称结构;
②发生器内部等离子体处于局部热力学平衡(LTE)状态;
③等离子体炬区为纯氩气等离子体;
④等离子体炬为光学薄的,即辐射的重新吸收和总的辐射损失相比可以忽略不计;
⑤等离子体射流是不可压缩状态的流体;
⑥等离子体在炬内的流动属于定常、湍流运动等。
对于流体流动状态通常用雷诺数Re来判定。当Re小于2300时,管流为层流,大于3000时为湍流。
(2-2)
式中,ρ为流体密度;ν为平均流速;d为流道截面特征尺寸;μ为流体黏度系数。
整个等离子体系统可视为由电磁场、温度场和流场三部分构成,流过感应线圈变化的电流产生振荡磁场,进而诱发感应电场,电离气体的焦耳热效应形成温度场,射频等离子体炬内气流速度分布用流场来描述,它由入口速度、上下压力差、管壁约束以及气体黏性等因素决定。其控制方程包括电磁场方程和流体力学方程:
①电磁场方程(麦克斯韦方程组)




式中,E为电场强度;B为磁感应强度;μ0为自由空间的磁导率;ε0为自由空间的介电常数;Jc为线圈电流密度;Ji为感应等离子体的电流密度。
②流体力学方程

式中,u为轴向速度分量;v为径向速度分量;ρ为密度;μ为黏度系数;λ为热导率;Cp为比热容;h为焓;p为压力;QJ为单位体积内的焦耳热;QR为单位体积内辐射热;Fx为洛伦兹力轴向分量;Fr为洛伦兹力径向分量。
北京科技大学王建军[56]采用数值模拟分析了射频等离子体发生器的温度场。模拟发现:等离子体炬最高温度可达10100K,为难熔金属及化合物粉体、陶瓷粉末的球化提供足够的能量保障;等离子体炬具有较大的温度梯度,等离子体球化过程中送粉枪需选择合适的插入位置,方可保证原料粉末能经过高温区,充分吸热熔融;另外,温度在等离子体炬石英管壁附近降低得很快,有利于延长石英管的使用寿命。
(5)其他技术方法:丝材电爆技术
当圆柱形金属导线中通过高电流密度(>105A/cm2)的脉冲电流时,会发生电爆炸,此时金属导线被加热到熔点,熔化后爆炸,这个过程伴随闪光、金属颗粒的飞溅及导线周围气体的冲击波。通过精确控制能量的输入,可以产生不同尺寸分布的金属颗粒。不同尺寸金属颗粒产生的机理并不相同,纳米级的颗粒主要是由类气相冷凝形成,亚微米和微米级的颗粒主要由熔融金属液相——类液相聚集形成。两种机理形成的颗粒在表面张力的作用下,最终都呈球形。丝材电爆设备以及制备的5~25μm钨粉如图2-40所示。

图2-40 丝材电爆设备(a)以及制备的5~25μm钨粉(b)
在制备微米粉的过程中,金属丝在脉冲电流作用下大部分瞬间被雾化成液滴,这些液滴经工作气体冷却,迅速凝结为球形金属颗粒。在整个过程中,物料多数时间处于常温状态,仅雾化到冷凝的过程处于高温状态(约毫秒)。在接触到容器壁之前,粉末已完全冷却到室温。在成形过程中,粉末不接触任何容器,避免了污染。
与其他制备技术相比,丝材电爆技术具有以下的特点:①丝材电爆技术能耗低,不需要长期维持高温;②以金属丝材作为原材料,有利于一些指标的控制,以氧含量为例,目前各种金属丝(包括难熔金属)的氧含量能降低到相当低的水平(小于0.015%),因此在制粉过程中,采用低氧的金属丝,控制好工作气氛,就能够制备出氧含量很低的金属粉末;③粒径分布容易控制,不同的能量输入,可获得不同粒径分布的粉末,尤其适合制备0~1μm、1~10μm的球形难熔金属粉末;④小批量试制容易实现,100~200g丝材即可制粉末;⑤粉体球形度好,无空心球、卫星球。同样该技术目前仍然存在一些限制:产能较低,单台设备12h的产能只有5kg左右,故适合于高密度难熔金属;在制备合金时,存在明显成分偏离,需要调整原材料的成分。
(6)金属粉末的后处理技术
3D打印用金属粉末后处理技术主要包括以下步骤。
①粉末初级筛分 初级筛分处理设备常选用超声波振动筛,配套60目、100目、150目、270目筛网。采用60目筛网去粗,采用100目和270目筛网进行分级处理。在270目筛分过程中为防止粉末颗粒堵塞筛网,需结合超声波筛分系统对粉末分级处理,以提高筛分效率和质量。
②粉末精细分级 粉末精细分级采用设备为精细气流筛分机,依据气体动力学原理对粉末进行精准分级。通常用来处理53μm以下粉末,可精确分级成0~15μm和15~53μm两个粒度范围。其他粒度范围也可根据调整设备频率及送料参数获得。
③粉末烘干处理 粉末水分含量对金属粉末增氧及流动性有重要影响,使用前需采用一定手段对粉末进行烘干处理。
④粉末储存防护 由于粉末比表面积较大,极易吸附空气中的水分,对粉末质量造成不利影响。因此,粉末在处理过程中,应采用气体保护,并密切关注环境温湿度。粉末储存时,应采用真空塑封或氩气保护包装,并密封存放于干燥通风处,防止粉末氧氮含量发生变化。