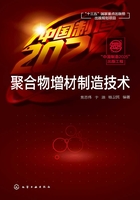
2.1 熔融沉积成形技术的原理、设备和材料
2.1.1 熔融沉积成形原理
熔融沉积成形技术的工作原理是将加工成丝状的热熔性材料经过送丝机构送进热熔喷头,在喷头内丝状材料被加热熔融,同时喷头沿零件切片轮廓和填充轨迹运动,并将熔融的材料挤出,使其沉积在指定的位置后凝固成形,与前一层已经成形的材料黏结,层层堆积最终形成产品模型。熔融沉积成形系统组成和工作原理如图2-1所示。

图2-1 熔融沉积成形系统组成和工作原理
2.1.2 熔融沉积成形设备
如图2-2(a)所示,熔融沉积成形设备主体由三维移动机构、挤出装置、喷头与成形平台组成。三维移动机构控制喷头与成形平台相对运动,进而实现空间立体成形。图2-2(b)所示为熔融沉积成形设备挤出装置,大多为电机控制的两齿轮相对旋转啮合丝状耗材[见图2-2(c)]送入热熔喷头,使其熔融挤出并堆积在成形平台上。喷头与成形平台通过控制系统精确联动控制挤出耗材的三维空间,精确定位沉积堆叠。

图2-2 FDM打印机结构示意
熔融沉积成形设备的移动机构按驱动方式划分,可分为同步带传动和丝杠传动。同步带传动是由电机驱动同步带的主动轮转动,进而由皮带带动直线导轨上的滑块前后移动。同步带具有噪声低、移动速度快、成本较低等特点,可以实现比丝杠更高的速度,但同步带传动的定位精度比丝杠要低。丝杠传动即由电机通过联轴器或同步带轮驱动丝杠转动,进而推动固定在直线导轨上的滑块前后移动。丝杠传动具有定位精度高、摩擦力小、刚性高、负载能力强特点,可实现精准定位。
熔融沉积成形设备的成形坐标系可分为空间直角坐标系(笛卡儿坐标系)和极坐标系。大多数设备采用空间直角坐标系,其结构和控制系统相对简单。目前快速发展的以极坐标系为成形坐标系的设备相比于空间直角坐标系的设备而言,具有设备零件少、设备体积小、成形空间大等优点,也为使用者提供了另一种成形结构和算法。
2.1.3 熔融沉积成形材料
熔融沉积成形技术所采用的材料为圆形截面的热塑性高分子聚合物丝状耗材,丝的直径通常为1.75mm或3mm。为保证挤出装置供料的稳定性,要求材料具有一定的模量,因此常规的熔融沉积成形设备不适应TPU等软弹性材料的成形要求,否则在供料过程中容易出现材料折弯等不稳定现象,如图2-2(c)所示。
材料在加工过程中要经过固态、熔融态、冷却固化三个阶段,这就要求材料具有熔融温度较低、熔融状态下黏度低、较低的收缩率和足够的黏结强度等性质。具体而言,材料熔融温度越低,对喷头加热元件以及设备流道密封要求低;材料熔融状态下黏度低可使材料具有较好的流动性,有助于材料顺利挤出,且有利于与上一层的黏结;较低的收缩率可避免已沉积材料在冷却过程中产生严重的翘曲变形,保证打印过程的顺利进行与打印精度。目前最常见的熔融沉积成形材料为ABS(丙烯腈-丁二烯-苯乙烯共聚物)和PLA(聚乳酸)。