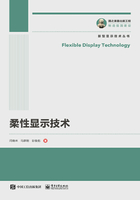
2.2.2 超薄玻璃的制造技术
单张超薄玻璃的制造工艺分为一次成型和二次减薄两种方法,还可以通过对贴合好的两张玻璃基板进行减薄来实现柔性衬底的功能。采用不同方法制造的超薄玻璃,后续的处理方式不同。在超薄玻璃的制造过程中,运输、清洗、切割等工序需要进行特别处理。
1.单张超薄玻璃的制造
如图2-7所示,UTG的生产包括UTG母玻璃材料的制造、薄化、切割、切割边缘处理、强化等环节。UTG 母玻璃材料的制造方法有浮法、溢流下拉法、窄缝下拉法等。

图2-7 UTG盖板制作工艺流程
浮法属于水平生产方式,产量大,玻璃宽度和厚度容易控制,但是玻璃拉薄区域长,所需锡槽长度大,占地面积大,存在渗锡层,在柔性玻璃后续处理方面困难。浮法生产的玻璃通常需要进行后续研磨处理以实现玻璃表面的光滑。溢流下拉法和窄缝下拉法属于垂直生产方式,生产的玻璃不需要进行后续研磨处理也能获得良好的表面特性。如图2-8(a)所示,溢流下拉法将熔融的玻璃液注入溢流槽内,使玻璃液溢流到两侧后在溢流槽下方汇合成连续式玻璃带下拉,经退火生产出优质玻璃。使用溢流下拉法生产玻璃时,玻璃两外表面除与空气接触外,不得与任何固体或液体接触,可以在玻璃两侧安装温度调节装置,更好地调节玻璃两侧的温度,从而消除玻璃板面的不平整度。如图2-8(b)所示,窄缝下拉法将均质的玻璃液导入坩埚炉中,坩埚炉下端装有铂金漏板,玻璃液在重力作用下从铂金漏板窄缝中流出,经过辊轮拉成超薄玻璃后进行退火。使用溢流下拉法生产玻璃,所需空间小,易于拉制更薄的玻璃板。

图2-8 垂直生产方式制作超薄玻璃的工艺技术
图2-9列出了玻璃表面特性。图2-9定义了一个测试设备40mm扫描长度内的20mm评估窗口。在该评估窗口内,样品的最大波纹度(Waviness)和粗糙度出现在最短跨度的起伏区域。LCD 玻璃衬底规格的典型值为波纹度小于0.1μm;波筋(20mm/4mm)小于0.02μm;坡度(20mm/2mm)小于0.025μm;在没有经过后续研磨处理的情况下,溢流下拉法生产的玻璃的表面平均粗糙度在1nm左右。

图2-9 玻璃表面特性
使用不同的表面涂层材料,所获得的玻璃边缘强度σ不同。没有经过表面涂层处理的玻璃,在加工过程中,玻璃边缘强度下降。经过表面涂层处理的玻璃,在同样的加工过程中,玻璃边缘强度下降不明显。选择合适的聚合物涂层,可以有效保护玻璃,以减少玻璃制作与玻璃加工过程中形成的损伤。聚合物涂层的存在甚至可以减少已经存在的玻璃缺陷对玻璃造成的影响。图2-10所示为使用聚合物涂层后的“治愈”效果。图2-10中的玻璃,表面经过喷砂处理,并在进行聚合物涂层前后分别测得玻璃边缘强度σ。经过聚合物涂层处理后,玻璃破损点减少了,玻璃在生产过程中变得更稳定。

图2-10 使用聚合物涂层后的“治愈”效果
玻璃的一个重要参数是下垂量,下垂量取决于玻璃的杨氏模量E。超薄玻璃要兼容现有的生产设备,下垂量越小越好。但是,玻璃的下垂量越小,玻璃的柔性越差。超薄玻璃在加工制造工艺上既可进行单张的片处理,也可进行卷对卷的卷筒输送连续处理。玻璃作为一种脆性衬底,最好采用片处理工艺。因为超薄玻璃在卷筒上传输时会出现破损,在实际使用时由于玻璃破损,最终的合格率将会非常低。
超薄玻璃在切割过程中容易产生破裂现象。目前,常用的玻璃切割方法是刀轮或金刚石轮切割技术,以及激光切割技术。采用激光切割技术(Full-body laser Cut),在高温激光束打到玻璃上后快速冷却玻璃,形成应力切(Stress-induced Cut),玻璃被完全切断。如图2-11所示,采用改善后的传统切割设备,可以获得与激光切割技术相同的效果。玻璃经过钻石切割后,也可以获得良好的边缘特性。

图2-11 超薄玻璃的不同切割方式
2.大板玻璃贴合后的减薄技术
在柔性、轻薄化等高品质的需求下,需要通过用化学或物理方法将玻璃减薄40%左右。玻璃减薄分为单张玻璃的减薄和大板玻璃贴合后的减薄。大板玻璃贴合后的减薄流程是玻璃封边→化学刻蚀→抛光清洗并干燥。单张玻璃的减薄不需要进行玻璃封边。
玻璃封边是指用UV胶水将贴合好的上下玻璃基板之间的边缘缝隙封住,防止酸碱溶液从边缘处进入液晶盒内,破坏液晶盒内固有的封框胶,从而进入液晶层内部,影响产品性能。玻璃封边的基本流程是首先加盖遮光垫,然后在边缘四周进行涂胶,涂胶后静置1分钟,接着擦去多余的胶水,最后对胶水进行UV硬化。具体的封边技术如表2-2所示。目前普遍采用的是针筒涂胶方式与盖印涂胶方式两种,其他(如滚筒涂胶方式、Dummy胶框取代涂胶方式等)方式也开始导入实际应用。
表2-2 具体的封边技术

把贴合好的两张大板玻璃封边后,浸入刻蚀液中进行刻蚀。刻蚀是指用氢氟酸或含氢氟酸的混酸与待减薄的玻璃基板表面接触,通过化学反应的方式溶解表面层的玻璃,以达到玻璃基板减薄的目的。玻璃刻蚀反应的化学方程式为

一般,刻蚀反应时间越长,玻璃质量的损失越大。影响反应速率的因子包括温度、浓度、生成物去除率和药液成分等。如图2-12(a)所示,适当的高温可以使分子带有足够能量进行有效碰撞。如图2-12(b)所示,适当的高浓度可以增加分子的碰撞概率。及时清除覆盖于反应物表面的生成物可以增加刻蚀的实际作用时间。刻蚀的精度与刻蚀厚度相关,刻蚀厚度越大,精度误差越大。

图2-12 影响反应速率的因子
表2-3所示为现有化学刻蚀减薄方式。浸泡式可以同时处理多张玻璃,但是外围产生的沉淀物、白色粉末容易黏附在玻璃上。顶喷式和侧喷式可以满足玻璃两面不同的刻蚀要求,药液可以有效回收,但是刻蚀表面容易产生凹点,需要进行抛光处理。瀑布流式的玻璃上不需要任何压力,药液容易回收,废液少,表面最光滑,甚至可以不用抛光,但是效率低,上下端均一性差。
表2-3 现有化学刻蚀减薄方式

通过化学反应进行的刻蚀技术减薄速度较快,适合工业化生产,并且可以根据需要调节酸液浓度以控制减薄速度。但是,减薄后的玻璃基板表面质量较难控制,许多化学减薄方式需要进行后续抛光处理。在刻蚀后,容易产生刮伤、辊轮痕、表面脏污、流水纹、刻蚀不均等现象,其中影响最大、最不易消除的是刮伤。
玻璃减薄还可以采用物理研磨技术。物理研磨技术通过在玻璃基板上进行机械研磨,利用研磨粉将玻璃切削,去除微量厚度,同时获得光滑、平整的玻璃表面。物理研磨技术可以精确控制厚度,但是研磨时间较长,不利于大批量生产。物理研磨既可以单面研磨,也可以双面研磨。如图2-13所示,单面物理研磨使用抛光粉加纯水形成抛光液作为加工介质,加工介质在一定的压力下流经机台托盘与玻璃之间,借机台运转做相对运动,使硬质磨料直接接触玻璃表面进而切削。单面物理研磨主要用于短时间抛光以消除玻璃表面伤痕或其他不良。研磨抛光相关的不良有破片和微裂纹、磨痕等。

图2-13 单面物理研磨示意图
3.玻璃的强化
玻璃的强化是指通过物理或化学的方法,在玻璃表面形成一个压应力层。当玻璃受到外力作用时,这个压应力层可将部分拉应力抵消,避免玻璃的破裂,从而达到提高玻璃强度的目的。
物理强化玻璃又称为淬火强化玻璃。首先将玻璃在加热炉中加热到接近玻璃的软化温度(600℃)时,通过自身的形变消除内部应力,然后将玻璃移出加热炉,用多头喷嘴将高压冷空气吹向玻璃的两面,使其迅速且均匀地冷却至室温,即可制得物理强化玻璃。物理强化玻璃有波浪阴影,气泡多,表面有点状,易有滚轮斑,并且刮伤、压伤较多。物理强化玻璃的翘曲度大于0.5mm,不能强化3mm厚度以下的玻璃。
化学强化玻璃主要以3mm厚度以下(包括3mm)的玻璃为主,采用高纯度的硝酸钾溶液及搭配的催化剂混合加热至420℃左右,玻璃结构表面的钠离子和钾离子进行离子交换而形成强化层,如图2-14所示。钾钠离子交换速度较慢,要使玻璃具有较大的压应力和符合使用要求的压应力层厚度,交换时间需要4~10小时不等。化学强化玻璃表面光亮度均匀,无波浪阴影,气泡少,并且无刮伤、压伤,翘曲度小于0.5mm。

图2-14 超薄玻璃化学离子交换强化工艺示意图