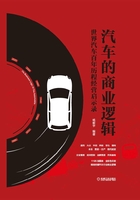
6.4 降低成本
为了降低成本,通用汽车还采取了以下措施:
降薪裁员:由于1980年通用汽车出现亏损,刚刚上台的罗杰·史密斯就开始了大规模的裁员降薪计划。1980年通用汽车美国时薪工人比1979年减少了9.2万人(见图2-107),同时还减少了员工股票购买计划,绩效提升项目被暂停,管理层的奖金被取消。不仅如此,1982年和UAW签署的新劳资协议放缓了工资上涨的速度(见图2-108)。

图2-107 通用汽车美国时薪工人数量(万人)
资料来源:通用汽车

图2-108 通用汽车工人时薪指数与薪酬/营业收入
资料来源:通用汽车
合资生产:在工业机器人方面,通用汽车与日本发那科在美国合资生产用于通用汽车工厂的工业机器人;在汽车生产方面,1983年和丰田在加利福尼亚州合资成立新联合汽车制造公司(NUMMI),搭建S平台,共同生产丰田卡罗拉和雪佛兰NOVA等车型;商用车方面,1985年和沃尔沃合资,在北美共同研发生产重型货车;在加拿大小型车市场,和五十铃合资生产小型车与运动型轿车;柴油机部门和彭斯克合资生产柴油机;到了1989年还与克莱斯勒合资生产汽车零部件。对于非核心业务,合资经营能够帮助通用汽车减少研发投入,降低市场开拓成本;而对于汽车制造方面的合作,通用汽车可以通过合资经营学习日本企业制造小型汽车的经验与管理技术,改进小型车的生产,降低独立开发小型车的成本。
精益生产和JIT库存管理:通用汽车通过合资向丰田学习精益生产,分析汽车生产的每一项任务,减少不创造价值的活动,改进创造价值的活动。其中一个关键例子就是“Just-in-Time”库存管理系统的开发。通用汽车和EDS共同开发的系统使得整车厂能够和供应商交流物料需求,授权原材料根据需求进行配送,大大地减少了生产时间和存货(见图2-109)。

图2-109 通用汽车存货周转率和存货占流动资产比例
资料来源:通用汽车
质量网络(Quality Network):由于美系车零部件的良率低于日系车,这造成了客户满意度的损失以及保修费用的增加。为了改善生产质量,1987年通用汽车提出了质量网络的管理模式,让车间管理人员、工会代表以及车间工人共同参与到质量管理当中,这个措施帮助通用汽车将零部件不合格率从1987年的7%降低到了1990年的2%。