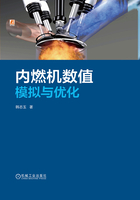
2.3 柴油机燃烧
与点燃式汽油机不同,常规柴油机的混合气形成和燃烧现象是不可分离的。在接近压缩行程末期、预期的燃烧开始之前,雾化的柴油喷雾(参见5.2.2小节)从喷油器的几个喷油孔喷入燃烧室。液态的燃油喷雾贯穿到燃烧室内的高温高压空气中,继而蒸发汽化,所产生的燃油蒸气与空气混合。在燃油喷射后的几度曲轴转角内,在喷雾外围的混合气会发生自燃(参见6.6.2小节),进而引发燃烧。由此升高的压力会压缩混合气未燃的部分,并缩短混合气的着火滞燃期,随后混合气会迅速燃烧开来。直到所需的全部燃油喷入气缸前,喷油器将持续喷射。燃油雾化、蒸发汽化、燃油与空气混合以及燃烧等过程将继续,直到所有燃油都经历了上述整个过程。同时在整个燃烧和膨胀过程中,气缸中剩余的空气与正在燃烧和已经燃烧的气体继续混合。
柴油机燃烧过程被称为非预混燃烧或扩散燃烧,因为气相燃油和空气必须相互扩散,然后发生反应。由于柴油机的燃烧是由自燃引起的,所以它也被称为压燃燃烧。在柴油机的大部分燃烧过程中,燃油的燃烧速率是由燃油与空气的混合速率控制的。在喷油开始后由气缸内的高温高压导致的自燃和由空气-燃油混合过程控制的燃烧速率是柴油机燃烧过程的显著特征。如上所述,压燃燃烧过程极其复杂。其燃烧过程的细节取决于燃油的特性、发动机燃烧室和燃油喷射系统的设计以及发动机工况等因素。它是一个伴有复杂化学反应的非定常、非均相燃烧过程。然而,可以根据混合过程控制反应速率这一机理来模拟其燃烧过程(参见6.2节)。
柴油机中没有像汽油机中那样由于末端混合气区域预混混合气自燃而产生的爆燃限制。因此,可以在柴油机中使用更高的压缩比,从而相对于汽油机提高其热效率。柴油机的非均相扩散燃烧特性会导致过量的碳颗粒物以黑烟的形式排出发动机,高温反应也会导致过量的氮氧化物排放。
图2-14(见彩插)展示了柴油机中的自燃和随后的火焰扩散过程。利用化学发光成像技术,对一台具有光学介入的重型直喷柴油机的自然发光进行了时间解析成像[29]。图像显示,柴油机自燃是一个渐进的过程,其同时发生在所有油束的下游区域。在喷射开始后不久(After Start of Injection,ASI)即1.0°~2.5°(CA)ASI时,第一次检测到化学发光。随着油束穿过燃烧室,它会变得更亮并向下游移动,直到碳烟的光度在放射源中占主导地位。在3.5°~4.0°ASI下,液相燃油从喷油器处沿油束标称轴线的最大贯穿距约为24~25mm。此时,油束中已经混入足够的热空气,足以蒸发所有燃油。随着燃油蒸气和空气混合气穿过燃烧室,喷雾液相油束长度保持相对恒定。随后,在预混合的燃气充分燃烧之后(在大约6.5°ASI时)形成扩散火焰,并且喷雾液相油束长度变短约4~5mm,这显然是扩散火焰的局部加热造成的。

图2-14 柴油机中由自然火焰发光显示的自燃和火焰现象的时间序列图像[29](喷油器位置由图中细小白点表示)
早期微弱的化学发光主要是甲醛(CH2O)和CH发光的结果,这对应于浓混合气中的“冷焰”现象。柴油喷雾的前部区域包含相对混合良好的浓燃油蒸气-空气混合气,其燃油空气当量比在2~4的范围内。大约4.0°~4.5°ASI时,碳烟颗粒辐射产生了更亮的发光图像。在5.0°~5.5°ASI内,来自油束前端部分(液态燃油的下游)的发光要明亮得多,说明在该区域开始形成碳烟。这表明放热化学反应早已在所有油束前部宽广的燃油蒸气区域中进行,此时燃油蒸气已经分解,并且在液态燃油下游的主要化学发光区域的整个油束截面中形成了PAHs(多环芳烃)。这表明在碳烟发光出现时,油束中的高温预混燃烧反应已经开始了。
在最后两幅图像中,即在6.5°和7.0°ASI时,随着碳烟浓度的升高,发光明显变得更亮。这些图像显示了各个喷雾油束周围扩散火焰的发展。这些扩散火焰位于具有浓混合气的喷雾边缘,由火焰内部的燃油蒸气,部分反应的燃油分子、多环芳烃、碳烟颗粒、CO和H2以及火焰外部的空气组成,这构成了柴油混合过程控制燃烧第二个阶段,大部分热量在这个阶段释放。
基于大量的研究[30],人们对柴油燃烧和碳烟/NOx生成有了更全面的理解。图2-15(见彩插)给出了直喷柴油机燃烧的理论模型。液相燃油被喷入气缸后,雾化形成的喷雾迅速和热空气以及其它物质混合。存在一个喷雾液相油束长度,当超过这个长度时,燃油蒸气-空气混合气持续卷吸高温气体,并最终经过预混燃烧过程,在其浓混合气燃烧中的高温产物中产生大量的碳烟前体产物(PAHs和C2H2)。这些碳烟前体产物继续反应并形成碳烟颗粒。同时,围绕高温产物的扩散火焰继续向上游扩展。喷雾液相油束长度决定了燃油喷雾的射程,继而影响混合气的卷吸。在此长度之外,扩散燃烧继续在燃烧区域的外部发展,在氧浓度较低的下游区域继续形成碳烟。由于扩散火焰区域的温度和氧气浓度较高,因此NOx的形成主要发生在这些区域里。总结起来,燃油和空气首先在浓混合气中反应,导致碳烟生成,然后这些浓混合气在油束边缘的高温扩散火焰中燃烧掉,从而形成NOx。值得注意的是,此处阐述的概念是基于弱气体流动的大缸径重型柴油机的燃烧。对于车用高速柴油机,情况可能会发生变化,因为采用的强气体涡流会影响燃油及混合气的物理和化学场分布。

图2-15 柴油机燃烧的概念图[30]
由于柴油机燃烧是多点自燃的,并且没有爆燃燃烧限制,因此柴油机的缸径范围跨度为70mm至900mm。不同的喷油系统和燃烧室设计适用于不同尺寸的柴油机,如图2-16所示。对于车用高速柴油机而言,实现燃烧室的形状、进气流动(涡流运动)和喷油策略良好匹配以实现高效和清洁燃烧很具有挑战性[31]。通常使用螺旋进气道形成强烈的涡流运动,并采用缩口型ω燃烧室生成湍流以实现更好的混合和燃烧,如图2-16c所示。

图2-16 常见的直喷式柴油机燃烧系统[2]
a)用于大型柴油机的弱空气涡流、多孔喷油器的开式燃烧室
b)用于中型柴油机的中等强度空气涡流、多孔喷油器的活塞凹坑燃烧室
c)用于小型高速柴油机的高强度空气涡流、多孔喷油器的缩口型ω燃烧室
柴油机燃烧的一个重要研究方向是优化喷油策略以提升发动机性能。利用电控共轨喷射技术实现的多次喷射具有很多优越性。已经证实预喷射可以有效地控制柴油机燃烧噪声并且减少NOx排放[32],分段喷射或多次喷射可以同时减少碳烟和NOx排放[33]。因为柴油机的碳烟和NOx排放具有此消彼长的特性,同时减少它们很具挑战性。
韩志玉等[34]对使用分段喷射降低碳烟和NO生成的机理进行了研究(参见8.1.1小节)。他们发现NO生成减少的机理与推迟喷油的单次喷射相似。就碳烟生成机理而言,在第一次喷射间隔后,碳烟的生成减少,这是因为喷雾前端产生碳烟的浓混合气区域不再得到燃油补充。在两次喷油之间的间隔内,混合气变得更稀。采用分段喷射时,燃烧室内会形成多个生成碳烟的区域,但由于随后的燃油被喷入第一次喷射的燃烧高温环境中,燃油会燃烧得更快,所以碳烟生成率降低,并且总的碳烟生成量会大大减少。
近年来,多达5个喷油脉冲的多次喷射策略已在量产柴油机上应用。每个喷油脉冲的目的有所不同。每个喷油脉冲中的燃油量和脉冲之间的间隔时间必须通过试验标定仔细调整。在喷油脉冲中,主喷射发生在上止点附近,这是为了产生转矩。主喷射前的预喷射是为了降低预混燃烧率,从而控制发动机噪声和NOx排放,后喷射的目的是减少碳烟排放,原理如上所述。在后喷射之后,有两个晚喷射用以辅助发动机排放后处理装置。其中一个晚喷射发生在膨胀行程中期,旨在提高排气温度,激活柴油机DPF中的颗粒再生过程。最后一次晚喷射发生在排气门开启(Exhaust Valve Opening,EVO)前附近,以满足SCR系统使用还原剂(碳氢化合物)还原NOx时的需求。