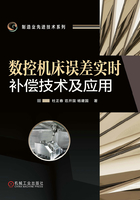
1.2 数控机床误差补偿的基本概念
误差补偿技术(Error Compensation Technique,简称ECT)是随着精密工程发展水平的日益提高而出现的一门新兴技术,是由于科学技术的不断发展对机械制造业的加工精度要求越来越高而发展起来的。
1.2.1 误差补偿的基本概念及特性
1. 基本概念
误差补偿是人为地造出一种新误差去抵消或削弱当前成为问题的原始误差,通过分析、统计、归纳及掌握原始误差的特点和规律,建立误差数学模型,使人为造出的误差和原始误差两者数值相近、方向相反,从而减小误差,并提高加工或测量精度。
最早的误差补偿是通过硬件实现的。例如:根据测出的传动链误差曲线,制造滚齿机的凸轮校正机构;根据测出的螺距误差曲线,制造丝杠车床的校正尺装置等。硬件补偿属机械式固定补偿,在机床误差发生变化时,要改变补偿量必须重新制作凸轮、校正尺或重新调整补偿机构。硬件补偿还有不能解决随机性误差、缺乏柔性的缺点。
近来发展的软件补偿,其特点是在对机床本身不做任何改动的前提下,综合运用当代各学科的先进技术和计算机控制技术来提高机床加工精度。软件补偿克服了硬件补偿的许多困难和缺点,把补偿技术推向了一个新的阶段。
2. 误差补偿的特性
误差补偿(技术)具有两个主要特性:科学性和工程性。
(1)科学性 误差补偿技术的迅速发展极大地丰富了精密机械设计理论、精密测量学和整个精密工程学,成为精密工程学的重要分支。
与误差补偿相关的技术有检测技术、传感技术、信号处理技术、光电技术、材料技术、计算机技术以及控制技术等。作为一门新技术分支,误差补偿技术具有自己的独立内容和特色。进一步研究误差补偿技术,使其理论化、系统化,将具有非常重要的科学意义。
(2)工程性 误差补偿技术的工程意义是非常显著的,它包含如下三层含义:
1)采用误差补偿技术可以较容易地达到“硬技术”要花费很大代价才能达到的精度水平。如一台普通的数控机床空间位置误差为30~40μm,经误差补偿后,其位置误差可降为10μm,甚至更小。
2)采用误差补偿技术可以解决“硬技术”通常无法达到的精度水平。如通过提高机床本身精度来提高机床精度有一定的限度,因为机床本身各零部件的加工也是由机床完成的,而零部件的加工精度受到机床精度的限制,即被加工工件的精度高不过加工机床的精度。而误差补偿的奥妙之处就在于,被加工工件的精度可高过加工机床的精度,我们认为这是一种“精度进化”或“精度自愈”的概念和过程。
3)在满足一定精度要求的情况下,采用误差补偿技术,可大大降低仪器和设备制造的成本,具有非常显著的经济效益。例如,对于相同类型和规格的数控机床,一般来说,普通精度的数控机床与精密数控机床的价格相差一倍,即100%,而误差补偿实施的成本仅为数控机床价格的5%~10%。
1.2.2 误差补偿的步骤
机床误差补偿主要步骤为误差源的分析和检测、误差运动综合数学模型的建立、误差元素的辨识和建模、误差补偿的执行和误差补偿效果的评价。
1. 误差源的分析和检测
数控机床误差源的分析是从误差补偿的角度深入了解和分析机床误差及误差产生源,认识各误差环节及其形成机理,掌握误差的性质、产生规律和对加工精度的影响,并确切掌握各误差之间的关系,对于热误差最好还要进行热变形模态分析,以获取表征机床温度场并用于机床热误差建模的关键温度点,为建立该误差的补偿模型做好准备。
数控机床误差元素的检测是误差建模及补偿的基础。数控机床具有几何误差、热误差、切削力引起的误差、刀具磨损引起的误差等众多误差元素,全面研究以上误差元素的检测原理和方法是进行误差元素建模及补偿的基础。不同的误差元素其检测原理和方法各不相同。几何误差通常由激光干涉仪、球杆仪、平面光栅等检测装置进行精密检测。为提高其检测效率,近年开发了机床空间体积误差的激光向量多步法,该方法的优点是通过一次测量可获得12项误差元素。热误差的检测方法涉及温度传感器的优化布置,而温度传感器在机床上的安装位置是热误差补偿的主要障碍,在几乎所有应用的热误差补偿系统中,温度传感器位置的确定在一定程度上是根据经验和试凑的过程。它通常是先基于工程判断,在不同位置安装大量传感器,再采用统计相关分析来选出少量的温度传感器用于误差分量的建模,这种经验过程更像是一种艺术,而不是科学。选择适当的温度传感器位置就成为机床热误差精确建模的关键。试凑法还导致大量的时间和传感器的浪费,这些浪费的传感器并不用在最终的误差建模中。力误差的检测方法分为直接测量和间接测量,直接测量是通过测力仪等检测装置直接检测机床在某方向的受力,间接测量通常采用的方法是建立电动机电流和切削力的关系,进而通过检测电动机电流来预测切削力。随着检测技术的不断发展,机床误差元素的检测正向着高效、高精度、智能化发展,为数控机床误差元素的检测奠定坚实的基础。
2. 误差运动综合数学模型的建立
综合数学模型是进行误差检测及误差元素建模的基础。在机械加工中,机床加工精度最终是由机床上刀具与工件之间的相对位移决定的。机床上刀具与工件之间的相对位移误差可用运动学建模技术来计算。早期的研究是用三角关系来推导几何误差模型。1977年开始用向量表达法建立空间误差模型;近年来开发了标准齐次坐标变换和螺旋量理论等方法,建立了几何和热误差两者的综合数学模型,用该方法可对非刚体误差进行补偿。
3. 误差元素的辨识和建模
误差元素建模是在误差元素辨识与检测的基础上,依据误差综合数学模型,通过各种方法建立误差与自变量的数学关系。常用的建模方法有最小二乘法、回归法、神经网络法、正交试验设计法、正交多项式法、综合最小二乘法、模糊算法、遗传算法、蚁群算法等,各方法的基本思路都是建立误差目标函数并令目标函数取极值,从而得到误差模型的相关系数,区别是建模的过程不同,当然模型的形式也不尽相同。
因为运动学模型计算最终位置和方向误差是基于机床的各个独立误差元素,因而,需要精确和有效地辨识误差元素。误差辨识方法可以分为直接测量误差元素和间接估计误差元素。直接测量误差元素是在机床不同的位置和温度分布条件下,使用诸如激光干涉仪或其他机械或光学方法来测量误差元素。间接估计误差元素是用诸如可伸缩式球杆仪等测量仪器测量机床上工件表面形状误差或最终误差,而后基于运动学模型估计各误差分量。
直接测量误差分量更精确、更简单明了,但有时更耗时,甚至不可能。间接估计误差分量提供了一种快速和有效估计机床误差分量的方法。还有一种方法是将工件尺寸和形状误差的测量值用于估计机床误差。通常,机床几何误差的测量不是很困难,但由于机床热误差在很大程度上取决于诸如加工周期、切削液的使用以及周围环境等多种因素,所以要精确测得热误差是相当困难的。
在获得了各误差元素分量后需进行建模,把各误差分量表达为机床位置或温度的函数。各几何误差分量与位置有关,故为位置的函数;各热误差分量与温度有关,故为温度的函数;还有的误差分量不仅和位置有关还和温度有关,既是位置的函数又是温度的函数。针对不同的误差需采用不同的建模方法。几何误差用位置的多项式来拟合,热误差用多元温度来拟合。对于几何和热的双重误差,在建模前要对其检测信号进行几何误差部分和热误差部分的分离。误差元素建模是误差补偿技术中最为关键的步骤,也是最为复杂和困难的工作。
4. 误差补偿的执行
在补偿过程中,补偿系统根据误差运动综合数学模型、误差分量模型以及实时反馈(如温度、位置等值)预报机床最终误差,并实时补偿该误差。误差补偿的具体执行是通过移动运动副使刀具或工件在机床空间误差的逆方向上产生一相对运动而实现的。
在早期的误差补偿研究中,补偿是通过离线修改数控代码而实现的。该方法相当耗时,且假定离线辨识的误差在实际加工中保持相同。近年来,开发了两种不同的技术来实现误差补偿:反馈中断法和原点平移法。
(1)反馈中断法 是将相位信号插入伺服系统的反馈环中而实现的。补偿用计算机获取编码器的反馈信号,根据误差运动综合数学模型计算机床的空间误差,将等同于空间误差的脉冲信号与编码器信号相加减。伺服系统据此实时调节机床拖板的位置。该技术的优点是无须改变CNC控制软件,可用于任何CNC机床,包括一些具有机床运动副位置反馈装置的老型号CNC机床。然而,该技术需要特殊的电子装置将相位信号插入伺服环中。这种插入有时非常复杂,需要特别小心,以免插入信号与机床本身的反馈信号相干涉。
(2)原点平移法 补偿用计算机计算机床的空间误差并将该误差作为补偿信号送至CNC控制器,通过I/O口平移控制系统的参考原点,并加到伺服环的控制信号中以实现误差量的补偿。这种误差补偿法既不影响坐标值,也不影响CNC控制器上执行的工件程序,因此,对操作者而言,该方法是不可见的。原点平移法不用改变任何CNC机床的硬件,但它需要改变CNC控制器中机床的可编程序控制器(PMC)单元,以便在CNC端可以接收补偿值。这种改变在老型号的CNC控制器中是不可能的。
5. 误差补偿效果的评价
当一个补偿系统建立起来后,应对该系统的补偿效果进行分析评价,以便改进补偿模型或系统,从而达到更好的加工精度。有三种评价补偿效果的方法:
第一种是传感器主轴热漂检测法,即用位移传感器检测主轴热漂移误差补偿的效果。
第二种是激光斜线测量评价法,即用激光测量仪在机床空切削中拖板走斜线进行线性位移误差的检测,主要检测对机床几何误差补偿的效果。
第三种是实际切削试验法,即通过实际生产中工件的切削,用补偿加工获得的工件尺寸误差、形状误差和位置误差来评价补偿的效果,这是最终最重要的补偿效果验证,验证补偿技术能否真正用于实际生产,转化为劳动生产力,这是最终目的。