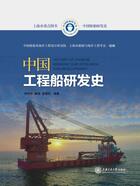
三、跨越创新进入世界先进行列阶段(2001年至今)
进入21世纪,世界船舶市场迎来了难得的发展机遇。党的十八大以来,为实现中华民族伟大复兴的战略,中央作出了建设海洋强国的决策,指引船舶工业前行。我国的综合国力显著增强,现代化的第二步战略目标已经实现,正向第三步战略目标迈进。在实现这一伟大目标的过程中,我国涉水工程项目进入跨越式发展新阶段。以港珠澳大桥为代表的建桥工程,以洋山港为代表的港口建设工程,以南海油田建设为代表的众多海上油田建设工程,以东海风电场为起点的海上风电场建设等海上涉水工程多项目、大规模地发展,急需一批大型、专业、高效、环保、先进的工程船舶。国家相关部委实施顶层设计,加大科技投入,建设了一批先进的实验设施,其中有国家能源海洋工程装备研发中心、大型深水波浪流水池、大型深水拖曳水池等,用以优化船舶性能。在这一阶段,我国船舶工业发展迅速,造船能力大幅度提升,已成为世界造船大国并向造船强国迈进。我国制造业迅猛全面发展,已成为联合国产业分类中唯一齐全的国家,足以向新型工程船舶提供先进的设备配套。
2005年开始执行的“十一五”规划纲要明确指出:依托重大工程,大力振兴装备制造业,提高先进技术装备的设计、制造和成套水平。随后出台的《国务院关于加快振兴制造业的若干意见》,为装备制造业,包括工程船舶和海洋工程装备制造业指明了发展方向和重点,并制订了促进发展的优惠政策,支持制造业的加快振兴计划。在国家振兴装备制造业的推动下,工程船舶研发迎来新的高潮,参与研发的机构增多,并找到了一条既符合国情、又瞄准国际先进水平,既贯彻国家方针政策、又能满足用户需求的,开展工程船舶和海洋工程装备的研发途径。
面对大型涉水工程急需专业装备的形势,又有国家强大工业制造能力的支撑,以及研发措施、设计手段提升的有利条件,我国工程船舶研发团队怀着建设海洋强国的信念,充满信心,继承传统,不懈努力,持续攻坚克难,紧紧抓住这一有利时机,在这新世纪的前20年中研发出许多令国际瞩目、且进入世界先进行列的新型工程船舶:以最大起重能力12 000吨,回转起重能力7 000吨,吊重能力位居世界第一的“振华30”号起重船为代表的起重船;以10万吨级、足以轻松地托运航空母舰的“新光华”号半潜船为代表的系列半潜船;以深水敷管起重船“海洋石油201”号为代表点的海底油管敷设船;以“深潜”号深潜支持母船携带我国自主研发的成套深水饱和潜水设备系统作为综合表征的深潜水支持母船;以能单月完成7台7兆瓦风机吊装的“福船三峡”号为代表的系列多型海上风电安装船等。
当人们在观看港珠澳大桥建造过程中巨型起重船吊起几千吨海底隧道段时;在看到大型海上钻井装备被半潜船举起进行远洋运送时;在看到耸立在海上的油气田通过海底管线源源不断向陆上输送油气时;当看到数以百计、高达百米的海上风电塔风扇高速飞转将绿色能源输入电网时,新型高效的工程船舶与它们紧密相连。
每一类型的工程船舶都有其独特的发展过程,在这过程中研发团队、建造单位都坚持创新的理念,艰辛地探索,贯彻绿色环保、智能和人性化的设计理念,以国际上最先进的同类船舶为标杆,努力赶超。所研发的每类船舶都在涉水工程中发挥相应的作用。
大型起重船为适应海上油气田建设和大型桥梁、港口建设工程日益增多的需要以及世界海上大型工程船舶租赁市场的发展,我国几大海洋工程作业部门开始投资建造大型起重船。起重量从2003年的2 600吨陆续提高到4 000吨、7 500吨到12 000吨,屡创亚洲乃至世界纪录;作业功能从单一到综合发展;移动能力从拖航向自航演变;定位由锚泊定位发展至锚泊和动力定位组合。在短短十几年时间已进入世界先进行列。
2004年广州打捞局瞄准国内海上工程建设急需大起重量起重船的趋势,委托中国船舶及海洋工程设计研究院设计,上海振华港口机械(集团)有限公司(以下简称“振华重工”)建造4 000吨全回转起重打捞船。这是我国起重船研发从中、大型向高效能、超大型发展的重要节点,是当时国内最大的、包括船舶和起重机构均是完全自主研发的全回转多功能起重船。为充分发挥该船的作用,除起重、打捞功能外还预留了布置铺管作业设备的部位,船舶性能、结构设计均作综合考虑,只要需要就可在短期内安装,并投入海底大管径油气管道铺设作业,从而提高船舶的使用效率,增加经济效益。
2016年,振华重工利用一艘30万吨级旧油船改装成12 000吨全回转起重船,同时安装DP-2动力定位系统。该船甲板面积为18 000平方米,约等于2.5个标准足球场大,具备超大物件的吊运安装能力,被誉为“海上大力士”。
该船交船后参加了举世瞩目的超级工程——港珠澳大桥最终连接段的安装。这次安装是将一个重6 000吨的巨大的钢筋混凝土结构,准确安装在30米水深的海底,完成港珠澳大桥海底隧道的贯通。要完成这个最终连接段双侧的对接难度相当大,因为水下安装余量仅有十几厘米,即使水面风平浪静,海底涌动的洋流也会形成巨大的扰动。6 000吨重的最终连接段吊装工程要确保扰动平衡,任何倾斜都将是灾难性的。安装的误差只允许在1.5厘米以内,这在世界水下安装领域是史无前例的,无异于海底穿针。该船成功地完成了这一作业,为我国海洋工程事业的延伸提供了强大的装备支撑和技术支持。
随着我国水下设施安装、检修和水下应急救援等深水作业工程发展的需要,饱和潜水技术逐步发挥作用。2016年振华重工承建了当时全球最先进的潜水工作船“PLEAG”号。该船配有DP-3动力定位和全球最先进的24人全自动双钟饱和潜水系统,可分批次不间断地进行最大深度300米的饱和潜水作业。配置的潜水钟由具有升沉补偿功能的收放系统通过两个月池放入水中;设有两座水下机器人基座,用于搭载大型作业级机器人等。
中国船舶及海洋工程设计研究院组建的详细设计团队对挪威的基本设计进行分析研究,吸收其优点,同时修正了基本设计存在的问题,在维持技术指标的同时,完成了全船总布置、设备配置、节能环保等优化工作。振华重工以雄厚的船舶制造能力,按期顺利交船,打破了深潜工作母船设计和建造技术被挪威、美国、法国几个工业发达国家垄断的局面。
随后,中船黄埔文冲船舶有限公司和上海佳豪船舶设计院合作完成了一艘ST-246型饱和潜水作业支持船“海龙”号设计建造,于2019年顺利竣工交付。
海底输送油气管线是海洋油气开采生产的重要一环。进入21世纪,海洋石油工程股份有限公司为承揽这一重要且经济价值高的工程项目,开始组建铺管船船队。
铺管船为促进我国自主研发设计铺管船,打破美国、欧洲国家的垄断局面,中国海洋石油工程股份有限公司于2006年委托中国船舶及海洋工程设计研究院自主设计潜水铺管船“海洋石油202”号,委托上海船舶研究设计院按荷兰GUSTO公司提供的基本设计进行深水铺管船“海洋石油201”号的详细设计。
“海洋石油202”自2009年7月投产后旋即进行渤南二期、锦州25-1、金县1-1、渤中19-4、渤中25-1油田应急复产,曹妃甸二期、渤中26-3油田等海底管线敷设,作业性能良好,获得船队和船员的好评。该船各项性能、作业指标均达到世界先进水平,其研发建造成功开启了我国自主设计该类船的进程。2011年获得中国船舶工业集团公司科学技术进步奖三等奖等多项荣誉。
上海船舶研究设计院(以下简称“上海船院”)会同船东对荷兰GUSTO公司的“海洋石油201”号铺管船基本设计进行审查,提出多项修改意见,完善基本设计。该船是当时海洋工程领域中第一艘铺管作业水深可达3 000米,配DP-3动力定位系统,装有3 500吨全回转起重机的敷管船。该船于2012年4月交船。其敷管能力高效,2013年在南海荔湾3-1项目深水段作业中,将78.9千米的6英寸管道铺设在1 405米水深处,在陵水17-2项目E3至E2段铺管作业水深达到1 542米,已成为我国深海海洋油气开采的重要装备。该船荣获上海市科学技术进步奖二等奖等多项荣誉。
铺设海底管线工程中的一环是开挖埋管沟,长期以来均由非专业工程驳船携带开沟机作业,效率低下。为改变这一现状,2015年9月海洋石油工程股份有限公司委托中国船舶及海洋工程设计研究院设计动力定位管道挖沟船。船上配置自行式挖沟机、浅水射流挖沟机和深水挖沟机,可根据作业海域的水深、底质情况进行挖沟、膨胀管安装、清管试压等作业,还可承担管道应急抢修、潜水作业、遥控无人潜水器(remode operated vehicle,ROV)支持和海底电缆敷设等作业。该船由中船黄埔文冲船舶有限公司建造,于2017年交船。经作业效果证实,该船挖沟与起重铺管匹配作业,实现了海底管道挖沟、敷设同步进行,有力提升了敷管效率。
在“十五”期间,交通部于2003年3月“全国救助工作会议”上确立了海上救助系统工作以海上人命救生为主,并由国家投资建造一批海洋救助船。上海船舶研究设计院2002年6月开始研发8 000千瓦、14 000千瓦海洋救助船。该船以人为本,强化海上人命救生能力,既要充分提高救助船在恶劣海况中救助的可能性,也要考虑救助船及船员的自身安全。中船黄埔文冲船舶有限公司于2005年交付首制船。从2005年到2015年期间建造8 000千瓦海洋救助船7批22艘,14 000千瓦海洋救助船2艘。该项目荣获中国船舶工业集团公司科学技术进步奖一等奖。
半潜船运送超长、超重等大件物品的特点引起国内海洋工程作业、海上打捞作业部门的关注。2014年5月中国船舶及海洋工程设计研究院受中远航运股份有限公司(以下简称“中远航运”)委托设计10万吨级载重量自航半潜船。该船最大潜深达30.5米,配DP-2动力定位系统,服务航速14.5节,续航力20 000海里
。该船是当时吨位为世界第二、沉深世界第一的半潜船。开敞的甲板面积达到13 500平方米,装载能力突出。2017年2月中旬成功下潜托起我国为国外海洋油气开发公司建造的大型圆柱形浮式生产卸油平台,航行1万多海里运往荷兰鹿特丹港。顺利到港之时引起欧洲同行的惊叹。我国也由此打破欧洲公司对超大型海工装备远距离交付市场的垄断。该船于2019年荣获中国船舶工业集团公司科学技术进步奖一等奖。
风力发电是提供绿色电源中较为成熟的一种发电方式。我国于2009年开始海上风电场建设。安装海上风机必须依靠工程船舶进行作业。如东海大桥海上风电场建设时,采用起重船进行风机吊装。同期建设的江苏洋口滩风电场则利用在驳船上停放陆用履带式起重机进行吊装。这样的作业方式时间长,安装效率低。为提升作业效率,南通海洋水建工程有限公司于2009年8月委托中国船舶及海洋工程设计研究院设计专用的风机安装平台。该院以设计海洋工程装备的理念,通过现场调查,根据风电场海域的环境和海底地质条件,仅用一年时间,就完成了我国最早的非自航坐底式风电安装船和自升式风电安装平台的研发。此后,多艘多型风电安装船或平台如雨后春笋纷纷通过改造或新建投入海上风电场建设。设计方包括了中国船舶及海洋工程设计研究院、振华重工、上海船院等,建设方有江苏韩通、厦门中远
、启东中远
等。典型的一代代新型风电安装船包括:“福船三峡”号、“顺-1600”号、“龙源振华三号”、“铁建风电01”号等,为我国兴起的海上风电场的建设起到了重大的作用。这些船舶装载量越来越大,装载甲板面越来越宽阔,能装运越来越多的组合风电大件。起重机吊装能力强,吊高已经超过100米,可满足10兆瓦级大型风机吊装要求。船舶或平台定位能力强,使风电安装的安全性、效率大为提高,同时船舶设备国产化也上了新台阶。
仅用10年时间,我国的风电安装船舶研发就赶上了西方工业强国用时30年的发展历程,攀登上大型化、大水深、能自航、多功能的风机安装船的技术高峰,为海上风电场建设提供了最有力的技术保障和装备支撑。到2020年全国海上风电累计装机规模达到900万千瓦。
在这20年里,其他工程船舶亦都随涉水工程的发展而升级换代,创建新船型,融合新技术,装置新设备。
一艘艘新颖、硕大的工程船舶建成下水,百舸争流。在中国盛世船队大军中,呈现出别样的灿烂。