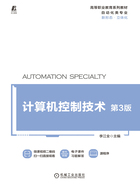
1.1 计算机控制系统的含义与工作原理
1.1.1 计算机控制系统的含义
自动控制就是在没有人直接参与的情况下,应用控制装置自动地、有目的地控制或操纵机器设备或生产过程,使它们具有或达到一定的状态或性能。
按照任务的不同,控制系统可以分为3大类,即检测系统、控制系统和测控系统。
1)检测系统:单纯以检测为目的的系统,主要实现数据的采集,又称为数据采集系统。
2)控制系统:单纯以控制为目的的系统,主要实现对生产过程的控制。
3)测控系统:测控一体化的系统,即通过对大量数据进行采集、存储、处理和传输,使控制对象实现预期要求的系统。
所谓计算机控制,就是利用传感器将被监控对象中的物理参量(如温度、压力、液位、速度等)转换为电信号(如电压、电流等),再将这些代表实际物理参量的电信号送入输入装置中转换为计算机可识别的数字量,并且在计算机的显示器中以数字、图形或曲线的方式显示出来,从而使操作人员能够直观而迅速地了解被监控对象的变化过程。
计算机还可以将采集到的数据存储起来,随时进行分析、统计和显示,并制作各种报表。如果还需要对被监控对象进行控制,则由计算机中的应用软件根据采集到的物理参量的大小和变化情况与工艺要求的设定值进行比较判断,然后在输出装置中输出相应的电信号,驱动执行装置(如调节阀、电动机)动作,从而完成相应的控制任务。
计算机控制系统就是利用计算机来实现生产过程自动控制的系统,有时称之为计算机测控系统或计算机监控系统,这些称呼虽然在应用场合上存在一定的区别,但结构和工作过程没有本质区别,一般习惯上都称为计算机控制系统。
计算机控制系统作为当今工业控制的主流系统,已取代常规的模拟检测、调节、显示、记录等仪器设备和大部分操作管理的人工职能,并具有较高级、复杂的计算方法和处理方法,以完成各种参数检测、过程控制、人机交互、数据通信以及操作管理等任务。
图1-1所示为某火电厂计算机控制室,操作员可以通过显示终端对生产过程进行监督和操作。键盘和显示屏替代了庞大的控制仪表盘以及大量的开关和按钮,控制室已变得越来越小,只需很少几个人就能完成对生产过程进行监督和操作的任务。

图1-1 某火电厂计算机控制室
计算机控制系统包含的内容十分广泛,它包括各种数据采集和处理系统、自动测量系统、生产过程控制系统等,广泛用于航空、航天、科学研究、工厂自动化、农业自动化、实验室自动测量和控制以及办公自动化、商业自动化、楼宇自动化、家庭自动化等人们工作生活的各个领域。
计算机在控制领域中的应用,有力地推动了自动控制技术的发展,扩大了控制技术在工业生产中的应用范围,使大规模的工业生产自动化系统进入崭新的阶段。
1.1.2 计算机控制系统的结构形式
1.控制系统的结构形式
工业生产中的自动控制系统随控制对象、控制算法和采用的控制器结构的不同而有所差别。其结构形式一般分为闭环和开环两种形式。
图1-2是控制系统的闭环控制形式,它是自动控制的基本形式。图中,系统通过测量装置(传感器)对被控对象的被控量(如温度、压力、流量、液位、位置及速度等物理量)进行测量,再由变送装置将这些量转换成一定形式的电信号,反馈给控制器。控制器将反馈信号对应的工程量与系统给定的设定值工程量比较,并依据比较的误差产生控制信号来驱动执行机构进行工作,使被控量的值与给定值保持一致。
这种控制,由于控制量是控制系统的输出,使被控量的变化值又反馈到控制系统的输入端,与作为系统输入量的设定值相减,所以称为闭环负反馈系统。
图1-3是控制系统的开环控制形式,它与闭环形式的控制系统的区别在于:它不需要控制对象的反馈信号,是直接根据给定信号去控制被控对象工作的。这种系统不会自动消除被控参数与给定值的误差,其控制结构简单,常用在一些要求不高的控制场合。

图1-2 控制系统的闭环形式

图1-3 控制系统的开环形式
自动控制系统的各个环节中,控制器是最重要的部分,决定了控制系统的性能和应用范围。
2.计算机控制系统的基本结构
控制系统中引进计算机,可以充分运用计算机强大的运算、逻辑判断和记忆等功能。
如果把图1-2中的控制器用计算机系统代替,就构成计算机控制系统,其基本框图如图1-4所示。计算机控制系统在结构上,与一般自动控制系统一样,同样分为开环系统和闭环系统两种。

图1-4 计算机控制系统的基本结构
计算机控制系统由控制计算机和生产过程两大部分组成,控制计算机是指按生产过程控制的特点和要求设计的计算机系统;生产过程包括被控对象、测量变送器、执行机构等装置。
由于生产过程的各种物理量一般都是模拟量,而计算机的输入和输出均采用数字量,因此在计算机控制系统中,对于信号输入,需使用A-D转换器将连续的模拟信号转换成计算机能接收的数字信号;对于信号输出,需使用D-A转换器将计算机输出的数字信号转换成执行机构所需的连续模拟信号。
1.1.3 计算机控制系统的工作原理
下面以一个计算机温度控制系统为例,简要说明计算机控制系统的工作原理,图1-5为其系统组成示意图。
根据工艺要求,该系统要求加热炉的炉温控制在给定的范围内并且按照一定的时间曲线变化。在计算机显示器上用数字或图形实时地显示温度值。

图1-5 计算机温度控制系统组成示意图
假设加热炉使用的燃料为重油,并使用调节阀作为执行机构,使用热电偶来测量加热炉内的温度。热电偶把检测信号送入温度变送器,将其转换为标准电压信号(1~5V),再将该电压信号送入输入装置。输入装置可以是一个模块,也可以是一块板卡,它将检测得到的信号转换为计算机可以识别的数字信号。
计算机中的软件根据该数字信号按照一定的控制算法进行计算。计算出来的结果通过输出装置转换为可以推动调节阀动作的电流信号(4~20mA)。通过改变调节阀的阀门开度即可改变燃料流量的大小,从而达到控制加热炉炉温的目的。
同时,计算机中的软件还可以将与炉温相对应的数字信号以数值或图形的形式在计算机显示器上显示出来。操作人员可以利用计算机的键盘和鼠标输入炉温的设定值,由此实现计算机监控的目的。
上述计算机温度控制系统对生产过程实现的自动控制过程可以分为以下4步:
1)生产过程的被控参量(过程信号)通过测量环节转化为相应的电量或电参数,再由变送器或放大器转换成标准的电压或电流信号。
2)电压或电流信号经过A-D转换后变成计算机可以识别的数字信号,并将其转换为人们易于理解的工程量(测量值)。
3)计算机根据测量值与给定值的偏差,输出控制信号。
4)控制信号作用于执行机构,通过调节物料流量或能量的大小来实现对生产过程的调节。
以上这4个步骤是周而复始进行的。
计算机控制系统的工作过程可归纳为以下3步。
1)实时数据采集:对来自测量变送器的被控量的瞬时值进行检测和输入。
2)实时控制决策:对采集到的被控量进行分析、比较和处理,按预定的控制规律运算,进行控制决策。
3)实时输出控制:根据控制决策,实时地向执行机构发出控制信号,完成系统控制任务或输出其他有关信号,如报警信号等。
上述过程不断重复,使整个系统按照一定的品质指标正常、稳定地运行,一旦被控量和设备本身出现异常状态,计算机能够实时监督并迅速做出处理。
计算机控制系统中,生产过程和计算机直接连接并受计算机控制,这样的方式称为“在线方式”或“联机方式”。如生产过程不和计算机相连,不受计算机直接控制,而是靠人工进行联系并执行相应操作的方式,称为“离线方式”或“脱机方式”。
如果计算机能够在工艺要求的时间范围内及时对被控参数进行测量、计算和控制输出,则称为实时控制。
实时的概念不能脱离具体过程,一个在线的系统不一定是一个实时系统,但一个实时控制系统必定是在线系统。