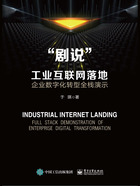
1.4 企业数字化转型是什么?
杨询再去旭霓公司时,张舵介绍了跟杨询对接的装备设计事业部,这是旭霓公司内部研发自用设备和进行非标准自动化工位改进和设计的部门,部门的主要职能是通过研发设计的非标设备、工位或产线提升公司的生产效率,包括把外部采购来的标准自动化设备进行外围拓展,使自动化设备能在旭霓公司发挥最大产能。装备设计事业部下面有自动化组、机械结构组、电气组。朱总是旭霓公司四个副总之一,兼管装备设计事业部,是装备设计事业部的总监。但考虑到朱总工作较多,还负责对接7个制造车间的检修组,而且年龄较大,未必能快速接受时下的一些热点技术和理念,张舵与他提前商量过,由副总监吴健来对接杨询的工作,并在公司管理会上增加工作进度汇报环节,这样总经理张舵和副总就都能够了解工作的进度。
吴健是3年前加入旭霓公司的,在IT行业工作过9年,软件技术娴熟,年轻好学,当时旭霓公司想成立一个“信息技术部”(相当于“研发部”),把公司使用的各种大型软件利用数据库、中间件等进行打通,并自研一些小的软件供公司内部使用。吴健是作为系统架构师应聘进来的,但是,由于旭霓公司当时并没有很好地规划此事,对这个事情所需要的资源估算、部门之间的配合流程、执行过程中的部门间的一致性和考核方式都没有详细规划,这个计划执行得磕磕绊绊,加上公司这几年业务量增长带来的新问题消耗了管理层很多精力,这个部门就没有运行成功,招聘进来的IT人员在做事没有头绪和外部薪资吸引力强的多重因素下几乎全部流失,吴健成了公司招聘来的资深IT人员中唯一留下的,主要原因也是张舵比较器重他,让他担任装备设计事业部的副总监,参与管理工作,而从技术转型到管理,做个技术型的管理人员也符合吴健的期望。
吴健与杨询可以算是“目击道存”,杨询第一次来旭霓公司时,吴健也参加了会议,杨询风趣的比喻、对行业和企业弊病的理解,让吴健觉得能跟这样的专家合作非常荣幸。杨询也希望能跟学习能力强、愿干实事的人合作。吴健作为旭霓公司的代表,与杨询对接企业数字化转型的事,两人都对这次的项目合作充满信心。
吴健平时也学习了这方面的知识,对企业数字化转型相关的问题也有自己的见解,但还是更想从专家的角度来深入了解,印证一下自己的想法是否全面。所以他说:“杨工,跟您合作还请多多指导,有需要配合的我一定尽力做好。我能不能请教您一个问题—关于企业数字化转型大家众说纷纭,从您的角度看,它到底是什么?要做什么?”
杨询:“这个问题没有标准答案,解读可大可小。我就简单说说自己的理解吧。”
一边说,杨询一边翻开电脑,打开了一个文件,展示给吴健等人看,如图1-2所示。

图1-2 工业发展路径(工业化与精益化)
工业的发展路径(如图1-3所示),从机械设备代替人力的“机械化”开始,随着电力的使用,每个工厂不再自建能源供应中心,而是把电网集中供应的电力作为能源,把电动机等作为主要的运动部件,这个阶段为“电气化”,“机械化”和“电气化”统称为“工业化”。
随后引入“流程化”,并注重发挥白领在工作中的串接作用和管理价值,制造业的生产效率进一步提高,再后来,“自动化”技术可以让机器按照参数设定或状态指令自动运行,很多环节不需要人为干预,降低了出错率并进一步提高了生产效率。“流程化”和“自动化”,这是传统精益非常关注的环节,你如果看过精益方面的书,标准作业、缩短准备时间、错误预防等概念内容主要都涵盖在“流程化”和“自动化”这两个方面里。

图1-3 工业发展路径(信息化与智能化)
当然,精益概念的出现已30年了,那时候的“自动化”主要还是简易自动化、半自动化。“自动化”应该也是“信息化”的一部分,尤其是高级自动化,它已经是“信息化”不可分割的一部分。
如果说自动化主要是控制机器设备高效地完成加工或制作工作,“电子化”就是使用计算机进行归档、整理、统计、查询,从而提高白领的工作效率。“网络化”则更进一步,是在“电子化”的基础上,把信息集成形成资产,部分白领的工作在企业的“网络化”进程里可以被取代。
再后一个阶段就是“智能化”,在制造领域被称为“智能制造”(如图1-4所示)。理论上,制造企业的瓶颈应该出现在从现有的智能水平迈向“强人工智能”的阶段,因为那里面临着技术瓶颈。但现实状况是,系统之间的打通、对接,技术与流程等因素的磨合,成为了绝大多数企业遇到的瓶颈,所以真正的瓶颈发生在了从“电子化”迈向“网络化”的阶段,如图1-5所示。

图1-4 工业发展路径的技术瓶颈

图1-5 工业发展路径的现实瓶颈
“数字化”可以理解为介于“网络化”和“智能化”之间的一个过渡阶段,它不等同于“网络化”或“信息化”。单纯地用系统将企业的各个流程串联起来,用数据库、表单等将企业的各个维度的数据存储起来,都不算是完全的数字化,这只能算是企业信息的网络化(信息化的高级阶段),如图1-6所示。企业的数字化与非数字化之间的核心差异在于:是否已实现数据在线?数据是否可以支撑分析驱动业务的改善?是否可以通过数据产生业务洞察,实现业务增长?

图1-6 数字化位于哪个阶段
吴健点头,说:“您这一解读我就清楚多了,但我仍有一个疑问,精益生产的杜绝浪费和无间断地作业流程理念,应该是生产企业一直追求的内容,但看起来跟数字化有点割裂,是这样的吗?”
杨询笑了,眨眨眼说:“您这个问题很好,问到点子上了。看您怎么理解‘精益’了。我刚才在图片里说的‘精益’是一种工业发展的阶段,而且强调了是‘传统精益’。那就是另一个角度,这个角度的‘精益’是不过时的,哪怕到了‘智能化’的工业时代也要以追求‘精益’为目标。如果把“精益”作为一种理念来看待,企业数字化转型追求的就是“数字化精益”。
吴健又紧接着问:我倒是听过一些“‘数字化精益’的概念,但没真正明白,它具体包括什么您能给讲讲吗?”
杨询:“嗯,这个内容跟上一个数字化的话题类似,没有标准答案,众说纷纭,我也根据自己的理解跟您交流下,我觉得算是一个比较有新意的总结。”
杨询打开了自己画的另一张图,展示给吴健等人。如果“数字化精益”与“传统精益”不割裂,看作用数字化手段结合传统精益的工具和精益理念,基本上可以画这样一张图,如图1-7所示。
这张图里有传统精益的部分,包括传统精益最常用的工具,如5S和目视化管理、价值流图等。数字化的部分包括:同步化物流、性能仿真、预测性维护等。
传统精益与数字化并不是割裂的,有很多交叉融合的地方,如JIT拉动生产、均衡化生产,虽然是传统精益提出的理念,但是现在可以用数字化手段实现这一理念,比如使用MES的排程模块或者高级排程软件。
再如标准作业,这是传统精益提出的理念,利用数字化手段,提供电子作业指导书或通过MES模块,相当于是用数字化手段实现了精益理念的要求。
全面生产维护,也是精益理念的要求。以前的传统手段是用纸质的设备台账记录和维护,但现在可以用数字化工具,比如用电子台账或MES设备模块进行管理。类似的例子还有很多,总之,就是用数字化手段实现精益理念,或者把数字化与传统精益相结合,这就是“数字化精益”。

图1-7 数字化精益是传统精益与数字化技术的结合
杨询总结说:“‘企业数字化转型’就是要在企业中实现‘数字化精益’,而‘IT+OT’是实现转型的核心。”