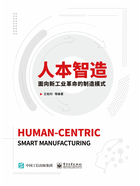
1.4 面向新一代智能制造的HCPS 2.0的技术体系
1.4.1 基于HCPS的智能制造总体架构
基于HCPS的智能制造总体架构可以从智能制造的价值维度、技术维度和组织维度进行描述[66,67](见图1-9)。

图1-9 基于HCPS的智能制造总体架构
1.4.1.1 智能制造的价值维度与HCPS的功能属性
智能制造的根本目标是实现价值创造、价值优化,而构建与应用HCPS是实现价值创造、价值优化的手段。智能制造的价值实现主要体现在产品创新、生产智能化、服务智能化、系统集成四个方面[68,69],与此相对应,HCPS从用途上也可划分为产品研发HCPS、生产HCPS、服务HCPS和集成复合型HCPS。
产品创新一方面通过智能化等技术提高产品功能,带来更高的附加值和市场竞争力;另一方面通过设计创新提高设计质量与效率[70]。产品创新根据需要进一步细分为产品设计、评估验证等环节,产品研发HCPS也可依此进行细分。
生产智能化通过全面提升生产和管理水平实现生产的高质、柔性、高效与低耗[69,71]。生产方面一般可细分为工艺设计、工艺过程、质量控制、生产管理等环节,其中某些环节还可进一步层层细分,例如,工艺过程可细分为若干产线及其集成,其中产线又可细分为若干装备及其集成。同理,生产HCPS也可相应层层分解。
服务智能化包括以用户为中心的产品全生命周期的各种服务[52,68,72,73],如定制服务、远程运维等,延伸发展为服务型制造业和生产型服务业。由此,智能服务HCPS亦可相应分解为定制服务HCPS、远程运维HCPS等。
系统集成作为新一代智能制造的重要特征,也是新一代智能制造实现价值创造的重要方面[4]。从HCPS的功能属性看,系统集成的结果将形成多功能的集成复合型HCPS系统。
1.4.1.2 智能制造的技术维度与HCPS的技术属性
智能制造从技术演变的角度体现为数字化制造(HCPS 1.0),数字化网络化制造(HCPS 1.5)和新一代智能制造(HCPS 2.0)三个基本范式(见图1-10)。数字化制造是智能制造的基础,贯穿于三个基本范式,并不断演进发展;数字化网络化制造将数字化制造提高到一个新的水平,为智能制造提供必要的网络基础设施,打通了企业价值链;新一代智能制造是在前两种范式的基础上,通过先进制造技术与新一代人工智能技术集成所发挥的决定性作用,使制造具有真正意义上的人工智能,是新一轮工业革命的核心技术。

图1-10 基于HCPS的智能制造三个基本范式
基于HCPS的智能制造的三个基本范式体现了智能制造发展的内在规律,一方面,三个基本范式次第展开,各有自身阶段的特点和需要重点解决的问题,体现着先进信息技术与制造技术融合发展的阶段性特征;另一方面,三个基本范式在技术上并不是完全分离的,而是相互交织、迭代升级的,体现着智能制造发展的融合性特征[30]。
1.4.1.3 智能制造的组织维度与HCPS的系统属性
实施智能制造的组织包含单元级、系统级和系统之系统级三个层次,与之相对应,HCPS也包括单元级HCPS、系统级HCPS和系统之系统级HCPS三个层次[34,74,75]。
单元级HCPS是实现智能制造功能的最小单元,是由人、信息系统和物理系统构成的单元级HCPS。系统级HCPS通过工业网络集成多个智能单元,实现更大范围更广领域的数据自动流动,提高制造资源配置的广度、精度和深度,包括生产线、车间、企业等多种形式,形成系统级HCPS。系统之系统级HCPS是多个智能系统的有机结合,通过工业互联网平台,实现了跨系统、跨平台的集成,构建了开放、协同、共享的产业生态。面向智能制造的HCPS的三层结构模型如图1-11所示。

图1-11 面向智能制造的HCPS的三层结构模型
综上所述,基于HCPS 2.0的新一代智能制造的总体架构可用多层次分层结构模型描述(见图1-12)。

图1-12 基于HCPS 2.0的新一代智能制造分层结构模型
1.4.2 单元级HCPS 2.0的关键技术
对于单元级HCPS 2.0,无论系统的用途和大小如何(设计系统、生产装备等),其关键技术都可划分为制造领域技术、机器智能技术、人机协同技术三大方面(见图1-13)。

图1-13 单元级HCPS的技术构成
1.4.2.1 制造领域技术
制造领域技术是指HCPS中的物理系统所涉及的技术,是通用制造技术和专用领域技术的集合[9]。智能制造的根本在于制造,因此制造技术是面向智能制造的HCPS的基础关键技术。同时,智能制造既涉及离散型制造和流程型制造,又覆盖产品全生命周期的各个环节,因此相应的制造领域技术极其广泛[9],可从多个角度对其进行分类,如按工艺原理可分为切削加工技术、铸造技术、焊接技术、塑性成型技术、热处理技术、定向凝固技术、增材制造技术等。
1.4.2.2 机器智能技术
机器智能技术是指HCPS 2.0中的信息系统所涉及的技术,是人工智能技术与相关领域知识深度融合所形成的、能用于实现HCPS特定目标的技术。信息系统是HCPS的主导,其作用是帮助人对物理系统进行必要的感知、学习认知、分析决策与控制,以使物理系统尽可能以最优的方式运行,因而机器智能技术主要包括智能感知、自主认知、智能决策和智能控制四大部分。
1.智能感知
感知是学习认知、分析决策与控制的基础与前提。机器智能感知的任务是有效获取系统内部和外部的各种必要信息,包括信息的获取、传输和处理。部分关键技术包括感知方案的设计、高性能传感器、实时与智能数据采集等[76,77]。
2.自主认知
认知的任务是有效获得实现系统目标所需的知识,是决定决策和控制效果的关键。HCPS 2.0的认知任务一般需由信息系统和人共同完成,因此需要解决机器自主认知和人机协同认知两大方面问题。其中,机器自主认知的核心任务是系统建模(包括参数辨识),关键技术涉及模型结构设计、参数辨识(学习)、评估优化等[78]。
3.智能决策
决策任务是评估系统状态并确定实现系统目标的行动方案。HCPS 2.0的决策任务一般也需由信息系统和人共同完成,因此需要解决机器智能决策和人机协同决策两大方面问题。其中,机器智能决策的关键技术涉及目标准则和决策函数的确定与优化等[67]。
4.智能控制
控制任务是根据决策结果对系统进行操作调整以实现系统目标,需要解决人机控制的分工协同和机器自主控制两方面问题。其中,智能控制的核心是控制模型和控制策略的确定,其本质上属于认知与决策问题[78,79]。
1.4.2.3 人机协同技术
智能制造面临的许多问题具有不确定性和复杂性,单纯的人类智能和机器智能都难以有效解决。人机协同的混合增强智能是新一代人工智能的典型特征[65],人机协同技术是实现面向新一代智能制造的HCPS 2.0的核心关键技术,包括认知层面的人机协同、决策层面的人机协同和控制层面的人机协同[54,55]。
单元级HCPS 2.0是新一代智能制造系统的基础。单元级HCPS 2.0的智能机床如图1-14所示,设计研发人员开发先进的信息系统,信息系统通过自主感知、自主学习、自主决策和自主控制等实现对机床加工(物理系统)的智能控制。

图1-14 单元级HCPS 2.0的智能机床
1.4.3 系统级与系统之系统级HCPS 2.0的关键技术
系统级与系统之系统级HCPS 2.0的本质特征均在于集成,以实现更大范围的信息集成与资源优化配置[4]。根据集成的广度与深度的不同,可划分为多个层次,如产线级、车间级(部门级)、企业级、行业级的开放、协同与共享的产业生态。各种层次的HCPS尽管集成的内容以及系统的功能不尽相同,但都具有本质上基本一致的组成与实现架构,企业级HCPS 2.0的系统组成与实现架构如图1-15所示,该架构通过建立企业级智能管理与决策系统并基于工业互联网与云平台实现对智能设计HCPS、智能生产HCPS、智能服务HCPS三个系统级HCPS的集成与优化。

图1-15 企业级HCPS 2.0的系统组成与实现架构
在单元级HCPS 2.0关键技术的基础上,系统级与系统之系统级HCPS 2.0的关键技术主要是系统集成技术,包括工业互联网、云平台、工业大数据等共性关键技术[12,45,46,73,80,81],以及与实现系统集成管理与决策相关的技术,如智能决策技术与系统、智能生产调度技术与系统、智能安全管控技术与系统、智能能耗计量与管控技术与系统、智能物流仓储技术与系统等。
系统级HCPS[82](见图1-16)可以让用户全流程参与进来,包括从提出设想到设计、下单,再到最后拿到产品的全过程。其精髓在于以用户为中心,核心是和用户的互联,即用户和全要素的互联、用户和机器的互联、用户和全流程的互联,最终实现大规模定制模式。

图1-16 系统级HCPS