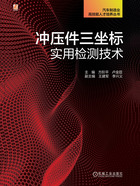
1.1 新项目开发流程
1.1.1 时间节点
通常情况下,一个全新的车型开发周期长达50~60个月。从最开始的产品调研、概念设计及规范的制定,到设计和建造过程、样车测试、试生产、生产爬坡、正式量产,每个时间节点的顺利进行,都对项目的开发起着至关重要的作用。
冲压件测量系统的规划开始于设计和建造阶段,当整车技术规范发放、设计冻结、初版量产曲面数模完成后,即可开始冲压件的测量系统规划。冲压件测量系统的规划一般包括测量计划的制订、测量点开发、测量方案的制定、测量支具开发及测量程序和报告开发等。测量计划制订一般可以根据之前车型的经验进行制订,需要考虑到测量成本、测量产能、生产频次等信息。测量点的开发可以与模具开发同时进行,并由模具厂测量部门根据选点规范进行选取。测量支具的开发应从数据冻结开始设计,在模具厂出首件时将合格的测量支具运送至测量室。测量程序及报告模板应在测量点选取完毕之后开始进行,并在测量首件时保证测量程序及报告模板能够正常使用。
报告模板、数据库与测量程序的编制有着密切的关系,它们之间息息相关,且变更成本较大。通过以往项目经验教训的总结,秉承变更成本最小的原则,从技术角度对项目任务进行了规划。
第一阶段:测量支具在验收结束后会借给模具供应商使用,在使用期间,要求模具供应商严格按照规范进行报告模板的制作。当测量报告制作完成后,需要发回厂检查,至少进行三轮检查,直到没有错误为止。检查的内容包括零件数模是否正确、封面标注是否正确、夹紧顺序是否正确、测量方法是否正确、建系原则是否正确、测量点选择是否正确、测量点公差标注是否正确、测量值是否合理等,这样做可以减少回厂后的变更工作。
第二阶段:模具供应商测量支持,与冲压规划工程师及时沟通,了解变更信息,确认正确的版本信息。根据具体情况制订特殊测量计划。
第三阶段:当模具供应商测量报告完善后,就要开始回厂前的编程准备,编程包括测量报告模板制作、测量程序离线编程和测量数据库规划等。这些工作需要在模具回厂之前就完成。
第四阶段:当支具和模具回厂后,需要第一时间拆箱,检查测量支具,同时通知支具供应商进厂支持支具检验,并提前安排测量任务,释放平台压力,优先安排测量支具精度检验工作。所有支具定位主控方向精度需要在±0.1mm以内,辅控方向精度需要在±0.2mm以内。
第五阶段:支具精度验收后,需要保存程序与验收截图,以备查看和支具定期校验。接下来进行测量程序的在线调试工作,需要保证测量程序能够正常使用。保证测量机不会与支具碰撞,完成测量结果上传设置,测量结果能正确显示在测量报告中。
第六阶段:通常情况程序调试是为了满足首件测量,因此调试时间有限,只能保证基本功能。程序的精细调整需等待第二轮优化,首件报告不做分享,只发送对应冲压规划工程师,以熟悉回厂模具状态。
第七阶段:当冲压规划工程师第二次送检测量时,需要进行测量程序及报告的第二轮优化,同时进行现场操作员的培训工作,明确上件手法,并进行测量程序使用教学。
第八阶段:自制冲压件一般会经历6轮重要时间节点的全尺寸报告状态放行。在会上,装焊工程师、AK工程师、质量工程师会对零件及报告提出优化整改意见。在第一轮报告放行会后,送检的第一批零件,针对会上提出的修改意见,进行报告及测量程序的第三轮优化,保证程序及报告的成熟度(在第二轮与第一轮优化之间,根据客户工程师反馈,也会对相关问题进行记录与优化)。
第九阶段:当零件设计发生较大变更时,会对测量程序及报告进行特殊轮优化。
第十阶段:在完成首轮试生产阶段放行会后,需要对报告模板及测量程序进行第四轮也是最后一轮优化,成熟的报告模板及程序将沿用至正式量产阶段,量产后特殊更改需求需要进行评估后方可添加,否则视为特殊测量,遇到工程变更需及时更新程序。
可靠的测量计划,可以帮助主机厂监控项目进度,及时有效地进行零件尺寸问题的整改。