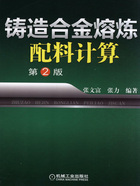
第二节 合金元素对铸铁组织及性能的影响
铸铁的金相组织及力学性能,是由铸铁中所含的除铁以外的碳、硅、锰、硫、磷俗称五大元素的多少所决定的。当铸铁中加入不同合金元素及实行不同的热处理工艺时,所得到的铸铁组织及力学性能也有所不同。因此,正确地进行配料计算必须掌握铸铁中主要化学元素对铸铁金相组织和力学性能的影响和作用。
一、碳
碳(C)是铸铁的主要化学成分,是铸铁的重要标志,铸铁与铸钢的主要区别在于碳含量的多少。铸铁碳的质量分数为2%~4%,而铸钢碳的质量分数在2%以下。
碳是最强的促进石墨化元素。碳在铸铁中以游离碳或化合碳(Fe3C)的形态存在,铸铁中的游离碳就是石墨,化合碳是碳化三铁,金相组织中称为渗碳体。铸铁中石墨析出的多,使铸铁的金相组织粗大,降低力学性能和硬度。如果石墨析出物过少,又使铁液流动性降低,铸造性能不好,铁液冷凝时收缩增大。铸铁中的渗碳体可提高铸铁硬度。
为了获得好的铸造性能和力学性能,铸铁中碳的质量分数多在3.0%~3.6%之间。
二、硅
硅(Si)也是较强的促进石墨化元素,硅在铸铁中溶解度比碳大得多,在一般铸铁中硅的质量分数为1.3%~3%。硅的质量分数增加到1.5%时就显著增加游离碳,而促进石墨化,减少铸件白口倾向,改善加工性能。所以在熔炼铸铁过程中加入75%硅铁或45%硅铁来增加铸铁的硅含量。
在生产实践中严格控制碳、硅含量来得到铸铁所需要的金相组织和力学性能。通过试验发现一个规律:每增加1%(质量分数)的硅,相图共晶点相应下降1%~3%,即硅对铁碳相图的影响。说明硅可以使共晶点向左移,其移动量点约相当于碳量的1/3,根据这一关系可以把硅含量简化折合成碳量,并把这个碳和硅含量的总和称为“碳当量”,采用符号CE表示,即

共晶点处碳的质量分数为4.26%,当碳当量值大于4.26%时为过共晶铸铁,小于4.26%时为亚共晶铸铁。
三、锰
锰(Mn)是中等程度阻碍石墨化元素,锰在铸铁中的作用和硅正相反,能延缓或阻止碳化物分解析出游离碳,使铸铁变硬。锰的质量分数超过4%~5%时会使铸铁变成硬而脆的白口铸铁。锰只有在质量分数为1%以下时,才能有效地提高铸铁的力学性能和硬度。锰的质量分数超过0.8%时会增加铸铁的收缩,所以铸铁中锰的质量分数一般控制在0.5%~0.8%,对薄壁小件锰含量控制低限。
锰能溶解在铁的固溶体中,和碳组成碳化物(Mn3C),锰还可以与铸铁中硫化合成为硫化锰(MnS)形成熔渣而上浮于金属液面,有利于减少硫对铸铁性能的危害。
四、硫
硫(S)是强烈阻碍石墨化元素,铁液中硫含量高时会使铁液变稠流动性不好,也阻碍气体从铁液中逸出,浇注的铸铁件容易产生气孔,硫含量过高铸件表面粗糙。硫与铁形成低熔点(985℃)的硫化铁(FeS)而使铸件产生热裂。硫是铸铁的有害元素,配料计算时应严格控制硫的含量,且硫含量越低越好,即硫的质量分数不宜超过0.1%。铸铁中由于有锰的存在,锰与硫形成高熔点的硫化锰(MnS),从而抵消了一部分硫的有害作用。
五、磷
磷(P)是弱的促进石墨化元素,增加含磷量使铁液的流动性增加和减少铸件缩孔,但增加了铸件的冷脆性。磷的质量分数在0.12%以下时,可以提高铸铁的耐磨性;当磷的质量分数超过0.3%时铸件容易产生缩孔,多于溶解度磷与铁形成磷铁化物——磷化铁(Fe3P),又与铁中的碳化铁(Fe3C)及铁形成三元共晶体,增加铸件的脆性。磷是有害元素,所以对重要机器零件应严格控制磷的含量。
六、铸铁中铬、钼、铜、镍、稀土合金等其他元素
铸铁中加入的其他元素如铬、钼、铜、镍等合金元素,是为了提高铸件特殊的力学性能,或者改善其他铸造性能,形成低合金铸铁或者高合金铸铁。尤其加入稀土合金元素后能有效使铁液脱S除气净化,改善铸铁的石墨化组织形状,因而形成球墨铸铁和蠕墨铸铁,显著增加了铸件力学性能和铸造性能。