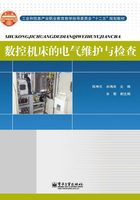
单元三 华中数控系统接口应用及数控机床电气结构解析
一、学习任务
1.结合单元二数控系统接口的功能,查看并分析各个接口具体的使用方法,画出系统连接框图。
2.阅读电源模块原理图,通过自学、讨论或教师的讲解、掌握电源分配的规则及设计方法。
3.掌握数控机床电气原理图的绘制原则。
4.针对机床实际情况,分析数控机床进给轴的控制方式,分析全闭环、半闭环和开环的区别。
5.根据机床实际情况,初步了解数控机床主轴变频控制的连接和原理。
二、学习目标
1.掌握数控机床电源模块的设计方法。
2.掌握数控系统接口的应用及连接框图。
3.熟悉数控机床进给轴常用的驱动器和电动机类型,以及它们的连接方式。
4.熟悉数控机床主轴常用的驱动器和电动机类型,以及它们的连接方式。
5.对数控机床输入/输出PLC转接板的作用及数控机床上常有的输入/输出信号有初步认知。
三、着重关注的引导性问题
1.数一数华中数控车床一共有几个电动机,认识这些电动机的外形并记下它们的型号和名称。
2.每个电动机机身上都有一块铭牌,记录电动机的主要参数,对照铭牌记录每种电动机的参数,通过查找资料和小组成员讨论初步了解这些参数的含义。
3.数控系统的进给轴接口是如何和后续驱动模块及电动机连接的?
4.数控系统的主轴接口是如何和后续驱动模块及电动机连接的?
5.画出数控系统各接口的应用连接框图。
6.在电气柜里找到PLC输入接口板的位置,并查看此电路板上有几个插座,分析每个插座的作用。
7.在电气柜里找到PLC输出接口板的位置,并查看此电路板上有几个插座,分析每个插座的作用。
8.根据强电电源模块原理图,找到电源模块用到的电气元件,列表写出这些元器件的名称、型号、功能和参数等。
9.电源模块有四个空气开关QF1~QF4,分析这四个空气开关的作用,它们分别控制哪些元器件的电源。
10.PLC输入信号转接板的作用是什么,分析光耦的工作原理,NPN型和PNP型的区别是什么?
11.分析PLC输入接口板上有哪些输入信号,掌握这些输入信号的地址分配,并在机床上找到输入信号(与12对应)的安装位置。
12.分析PLC输出接口板上有哪些输出信号,掌握这些输出信号的地址分配,并在机床上找到输出信号的控制对象。
四、任务学习知识基础
(一)数控系统接口应用连接框图
数控系统的接口虽然较多,但还是有规律可循的,一般由下面几部分组成,连接框图如图3-1所示。

图3-1 华中数控系统接口连接框图
① 电源接口:每个电气设备的必备接口,华中数控系统的工作电源是直流 24V,不过在系统内部还有电源模块,对24V进行变换得到5V、12V分别给内部不同元件供电。
② 人机交换接口:键盘、软驱、以太网、RS-232接口都是属于这一类,这类接口负责将数控系统和外部信息进行交换,例如将数控程序传入系统,以太网口还可以将数控机床连入局域网,实现远程控制。
③ 进给轴控制接口:一般而言车床有两个进给轴,铣床有三个进给轴,分别用到2个、3个进给轴接口。华中数控系统通过XS40~XS43控制HSV-11型伺服驱动器,此驱动器是华中数控公司生产的;通过XS30~XS33 控制其他类型的进给装置。一套系统中的进给装置类型可以相同,也可以不同,但最多只能连接四个进给轴。
④ 主轴控制接口:通过XS9接口控制变频器驱动三相交流异步电动机,实现主轴控制。
⑤ 开关量输入/输出接口:开关量主要有两部分,机床操作面板按键和机床外部各种传感器。
⑥ 手摇脉冲发生器接口:通过XS8连接手摇脉冲发生器,该接口是选件。
将上述六个方面再进行分析,发现数控机床电气控制主要是围绕下面三个方面:
第一方面是进给控制,其主要线路是,计算机数控装置(CNC)给进给驱动装置发出指令,进给驱动装置驱动电动机带动刀具或工件实现进给。闭环系统还要增加反馈器件和反馈控制环节。
第二方面是主轴控制,这个电气控制方面主要是CNC通过驱动器实现主轴的速度、方向调节,通过接近传感器实现定位控制。
第三方面是刀具控制,主要控制功能是CNC系统通过各种电气控制环节实现刀具选择与定位功能,加工中心与普通数控机床相比要复杂一些。
所有种类的数控机床电气控制都是如此,围绕CNC系统如何控制上述三个电气控制方面,因此可以将数控机床电气控制组成图进行简化,如图3-2所示。

图3-2 数控机床电气控制组成框图
(二)华中数控车床的四大电动机模块
根据上面分析,数控机床电气控制主要是三方面:进给驱动控制、主轴驱动控制、刀具选择与定位。以华中数控车床电气试验台为例,两个进给轴,一个主轴,一个四工位刀架,所以一共有四个电动机。在这个单元,主要了解这些电动机的类型,电动机、驱动器和CNC系统的连接方式,下面分别进行讲解。
1.进给驱动控制单元
进给驱动控制单元是上述三方面最复杂的一个单元,它的控制原理框图如图3-3所示。

图3-3 进给驱动与控制路径原理框图
如图3-3所示进给驱动系统适用于所有种类的数控机床进给系统,其中驱动器涉及的元件有伺服驱动器或步进驱动器等,相应电动机使用伺服电动机或步进电动机,测量装置使用光电编码器或光栅尺。如果是数控车床,电动机驱动的对象就是X、Y轴的滑板运动,同样的控制也适用于数控线切割设备;如果是数控铣床,电动机控制对象就是X、Y、Z三个轴工件运动,同样的控制也适用于数控雕刻机等数控设备控制。可以看到,这样的数控机床电气控制方面划分适用于所有种类的数控机床,下面参照华中数控车床试验台进行具体讲解,学生应按照这种思路结合具体机床主动进行学习。
华中数控车床试验台的进给轴采用了不同的电动机控制,让学生了解多种形式的进给单元控制方法。其中X轴是通过步进电动机驱动器带动步进电动机实现开环控制,电气框图如图3-4示。

图3-4 步进电动机开环控制电气框图
步进驱动器和步进电动机采用深圳雷塞M535型步进驱动器和57HS13型步进电动机。M535 型步进驱动器是细分型高性能步进驱动器,适合驱动中小型的任何两相或四相混合式步进电动机。电流控制采用先进的双极性等角度恒力矩技术,每秒两万次的斩波频率。在驱动器的侧边装有一排拨码开关,可以用来选择细分精度,以及设置动态工作电流和静态工作电流,驱动器接口如图3-5所示。57HS13型步进电动机是四相混合式步进电动机,其外形图和引线定义图如图3-6所示,步距角为1.8°,静转矩1.3N.m,额定相电流2.8A,详细参数见表3-1。

图3-5 MS535型步进电动机驱动器外形图

图3-6 57HS13型步进电动机外形图和引线定义图
表3-1 57HS13型步进电动机参数说明表

在本单元,主要是了解和熟悉这些元器件的外形和简单的参数,不需要掌握CNC、驱动器及电动机的具体接线,在以后的单元会有具体介绍,由简到难,容易掌握。有兴趣的同学可以通过上网,查找相关资料,了解这些元器件的使用方法。
什么是相数,什么是步距角,这两个重要参数,每个小组通过查资料、同学讨论一定要明白。
2.交流伺服电动机进给单元
华中数控车床试验台的进给轴采用了不同的电动机控制,学生应了解多种形式的进给单元控制方法。前面介绍了X轴的开环控制,现在讲解Z轴的半闭环控制,Z轴是通过交流伺服电动机驱动器带动交流伺服电动机,并通过编码器实现反馈的半闭环控制,电气框图如图3-7所示。

图3-7 交流伺服电动机半闭环控制电气框图
交流伺服驱动器和交流伺服电动机采用SANYO Q系列的QS1A01AA0M601P00和P50B05020DXS00。QS1A01AA0M601P00和P50B05020DXS00构成闭环控制系统,提供位置控制、速度控制、转矩控制三种控制方式(需设置交流伺服参数和相应连线)。QS1A01AA0M601P00为三相220输入,输入电流为2.5A,输出电流为2.2A;P50B05020DXS00为小型小惯量电动机,配2000P/r增量式码盘,功率0.2kW,额定转速3000r/min,额定转矩0.64N·m。图3-8和图3-9分别为交流伺服电动机型号和驱动器型号含义图。

图3-8 三洋Q系列交流伺服电动机型号含义图

图3-9 三洋P5系统交流伺服驱动器型号含义图
① 代表Q系列伺服驱动器。
② 表示电源输入及其电源部分:A——200V;C——400V;E——100V。
③ 表示驱动器容量:
01——15A;03——30A;05——50A;10——100A;15——150A;30——300A。
④ 电动机类型:A——旋转型电动机。
⑤ 控制单元硬件类型:
A——具有标准型I/F的省配线增量式编码器(INC-E)和绝对编码器(可选)。
H——ABS-RⅡ,RM062M,有请求信号的绝对编码器。
R——ABS-E,带增量功能的绝对编码器。
T——全闭环。
⑥ 适用电动机系列的描述:
0——与P系列电动机组合或是与Q系列电动机的标准组合;
除0之外——与Q系列电动机的定制组合(如降低功率、定制开关频率、使用中空轴电动机)。
⑦ 适用电动机(想要详细了解,详见电动机和驱动器的标准组合图)。
⑧ 编码器类型:
01——省配线增量式编码器,2000P/R;
02——省配线增量式编码器,6000P/R;
03——具有增量功能的绝对编码器,2048 P/R,11BIT/每转,13BIT/多转;
06——绝对编码器ABS-RⅡ,13BIT/每转,13BIT/多转;
A3——省配线绝对编码器(光电)17BIT/每转,16BIT/多转,传输速率:2.5Mb/s;
A8——省配线绝对编码器(变压)17BIT/每转,14BIT/多转,传输速率:2.5Mb/s。
⑨ 接口规格说明:
S——速度控制;T——转矩控制;P——位置控制;X——速度和转矩控制,可切换;
Y——位置和转矩控制,可切换;U——位置和速度控制,可切换。
⑩ 个别说明:
00——标准产品;A1——单相电源规格(200V AC)。
在使用驱动器和电动机时,一定要参照相关表格,核对该系列的伺服电动机和伺服驱动器的型号,如果组合不一致,系统将会工作不正常,表3-2是P系列旋转电动机和Q系列伺服驱动器(200V AC输入型)的部分组合表。伺服电动机和伺服驱动器的铭牌分别如图3-10和图3-11所示。
表3-2 P系列旋转电动机和Q系列伺服驱动器(200V AC输入型)的部分组合表


图3-10 伺服电动机铭牌

图3-11 伺服驱动器铭牌
3.主轴变频控制
现代数控机床的主轴大多采用矢量控制的变频器配三相异步电动机的变频无级调速或直接将主轴作为电动机转子的“电主轴”形式,此类机床通常采用Sxxxx指令直接指定主轴转速大小。经济型数控机床的主轴变速还保留用传统的齿轮减速箱的手动换挡变速形式,这类机床通常不接收S指令功能。数控车床的主轴转速由脉冲编码器进行实时检测,车螺纹时系统将根据螺纹车削时转速与进给的关系实施螺纹进给控制,由此取代了螺纹加工时复杂的挂轮装置。
华中数控车床试验台的变频主轴采用日立SJ100-007HFE型变频器配三相异步电动机。变频器采用正弦波脉宽调制(PWM)控制,额定容量1.9kVA,额定输入电压三相交流380V,额定输出电流 2.5A,输出频率范围 1~360Hz,适用电动机容量 0.75kW。三相异步电动机采用普通三相异步电动机,功率0.55kW,转速1390r/min。
日立变频器的外形图如图3-12所示,三相交流异步电动机的外形图如图3-13所示。

图3-12 日立变频器的外形图

图3-13 三相交流异步电动机的外形图
数控系统控制变频器的接口是XS9,该接口输出一对模拟电压信号至变频器,通过改变电压值的高低改变变频器的频率,从而改变三相交流异步电动机的转速。而电动机的方向信号是通过PLC输出接口控制的,变频器本身有一些智能端子,可以接收外部的开关量,因此主轴电动机的控制框图如图3-14所示:

图3-14 主轴电动机的控制框图
4.刀架电动机控制
刀架电动机是以脉冲电波的形式接收指令的,刀架内部有一端带蜗轮的蜗杆,刀架和底座接触面上各有一个端面齿轮和两个限位块。正常情况下两个端面齿轮是咬合的,底座上面装有电动机并有连轴蜗杆。当接收到换刀指令时,电动机正转,蜗杆带动蜗轮同时刀架蜗杆转动使刀架上升,端面齿轮分离。当刀架升高到一定程度时,刀架连同刀架蜗杆一起旋转,旋转90°后遇到限位块阻挡,由于电动机受阻力量达到一定时开始反转,自然刀架下降与底座端面齿轮咬合,限位块锁死,完成换刀。刀架外形图如图3-15所示。

图3-15 刀架外形图
(1)三相交流异步电动机工作原理
定子三相绕组通入三相交流电即可产生旋转磁场。当三相电流不断地随时间变化时,所建立的合成磁场也不断地在空间旋转。旋转磁场的旋转方向与三相电流的相序一致,任意调换两根电源进线,则旋转磁场反转。
定子旋转磁场旋转切割转子绕组,转子绕组产生感应电动势,其方向由“右手螺旋定则”确定。由于转子绕组自身闭合,便有电流流过,并假定电流方向与电动势方向相同,转子绕组感应电流在定子旋转磁场作用下,产生电磁力,其方向由“左手螺旋定则”判断。该力对转轴形成转矩(称电磁转矩),并可见,它的方向与定子旋转磁场(即电流相序)一致,于是,电动机在电磁转矩的驱动下,顺着旋转磁场的方向旋转,且一定有转子转速。有转速差是异步电动机旋转的必要条件,异步的名称也由此而来。
三相异步电动机从接通电源开始运转,转速逐渐上升直到稳定运转状态,这一过程称为启动。按照启动方式不同,它可以分为直接启动和降压启动。
直接启动的启动电流大,对供电变压器影响较大,容量较大的鼠笼异步电动机一般都采用降压启动。降压启动就是将电源电压适当降低后,再加到电动机的定子绕组上进行启动,待电动机启动结束或将要结束时,再使电动机的电压恢复到额定值。这样做的目的主要是为了减小启动电流,但是因为降压,电动机的启动转矩也将降低。因此,降压启动仅适用于空载或轻载启动。在刀架控制过程中,通过两个接触器控制刀架正反转实现换刀,因为要切削零件,所以采用的是全压启动。
(2)交流接触器工作原理
接触器是一种根据外来输入信号利用电磁铁操作,频繁地接通或断开交、直流主电路及大容量控制电路的自动切换电器。主要用于控制电动机、电焊机、电热设备、电容器组等。其工作原理为:当电磁铁线圈得电,电磁铁吸合时,带动接触器触点闭合,使电路接通。线圈失电时,电磁铁在弹簧力作用下释放,接触器触点断开,使电路切断。交流接触器外形图如图3-16所示。

图3-16 交流接触器外形图
接触器不仅能实现远距离集中控制,而且操作频率高、控制容量大,具有低压释放保护、工作可靠、使用寿命长和体积小等优点,是继电器—接触器控制系统中最重要和最常用的元件之一。
接触器的基本参数包括:主触点的额定电压、主触点允许切断电流、触点数、线圈电压、操作频率、机械寿命和电寿命等。现代生产的接触器,其额定电流最大可达2500A,允许接通次数为150~1500次/h,总寿命可达到1500万~2000万次
接触器的结构及工作原理。如图3-17所示,交流接触器主要由电磁机构(包括电磁线圈1、铁芯2和衔铁3)、触点系统(主触点5和辅助触点4)、灭弧装置(如图3-19所示)及其他部分组成。

图3-17 交流接触器结构图

图3-19 交流接触器的灭弧装置
如图3-17所示,当接触器线圈1通电后,在铁芯2中产生磁通及电磁吸力。此电磁吸力克服弹簧反力使得衔铁3吸合,带动触点机构4和5动作,触点的结构形式如图3-18所示,常闭触点打开,常开触点闭合,互锁或接通线路。线圈失电或线圈两端电压显著降低时,电磁吸力小于弹簧反力,使得衔铁释放,触点机构复位,断开线路或解除互锁。接触器的型号含义和电气符号如图3-20所示。

图3-18 触点的结构形式

图3-20 接触器的型号含义和电气符号
常见的接触器有CJ20系列、3TH和CJX1(3TB)系列。其中CJ20系列是较新的产品,而3TH和CJX1(3TB)系列是从德国西门子公司引进制造的新型接触器。在网上可以查到各种型号接触器的功能参数、安装尺寸及型号和价格,可以利用网络资源扩展知识面,掌握学习的方法。
(三)解读华中数控车床的PLC模块设计
PLC用于通用设备的自动控制,称为可编程控制器。PLC用于数控机床的外围辅助电气的控制,称为可编程程序机床控制器。因此,在很多数控系统中将其称之为PMC (Programmable Machine tool Controller)。数控系统有两大部分,一是NC、二是PLC,这两者在数控机床所起的作用范围是不相同的。可以这样来划分NC和PLC的作用范围:
① 实现刀具相对于工件各坐标轴几何运动规律的数字控制。这个任务是由NC来完成;
② 机床辅助设备的控制是由PLC来完成。它是在数控机床运行过程中,根据CNC内部标志及机床的各控制开关、检测元件、运行部件的状态,按照程序设定的控制逻辑对诸如刀库运动、换刀机构、冷却液等的运行进行控制。
在数控机床中这两种控制任务是密不可分的,它们按照上面的原则进行了分工,同时也按照一定的方式进行连接。
(1)PLC与数控系统及数控机床间的信息交换
相对于PLC,机床和CNC就是外部。PLC与机床及CNC之间的信息交换,如图3-21所示,对于PLC的功能发挥,是非常重要的。PLC与外部的信息交换,通常有四个部分:

图3-21 PLC与机床及CNC之间的信息交换
① 机床侧至PLC:机床侧的开关量信号通过I/O单元接口输入到PLC中,除极少数信号外,绝大多数信号的含义及所配置的输入地址,均可由PLC程序编制者或者是程序使用者自行定义。数控机床生产厂家可以方便地根据机床的功能和配置,对PLC程序和地址分配进行修改。
② PLC至机床:PLC的控制信号通过PLC的输出接口送到机床侧,所有输出地址也是由PLC程序编制者或者是使用者自行定义。
③ CNC至PLC:CNC送至PLC的信息可由CNC直接送入PLC的寄存器中,所有CNC送到PLC的信号含义和地址(开关量地址或寄存器地址)均由CNC厂家确定,PLC编程者只可使用不可改变和增删。如数控指令的M、S、T功能,通过CNC译码后直接送入PLC相应的寄存器中。
④ PLC至CNC:PLC送至CNC的信息也由开关量信号或寄存器完成,所有PLC送至CNC的信号地址与含义由CNC厂家确定,PLC编程者只可使用,不可改变和增删。
数控机床强电电路通常由电源变压器、控制变压器、各种断路器、保护开关、继电器、接触器等等构成,为其他电动机、电磁阀、电磁铁等执行元件供电。这些相对于数控系统来讲,属于强电回路。这些强电回路不能和控制系统的弱电回路直接相连,只能通过中间继电器等电子元件转换成直流低压开关信号,才能成为PLC或继电器逻辑控制电路的可接收的电信号。反之,从PLC或继电器逻辑控制来的控制信号,也必须经过中间继电器或转换电路变成能连接到强电线路的信号,再由强电回路驱动执行元件工作。
(2)PLC输入/输出转接板元件布置图
I/O端子板分输入端子板和输出端子板两种,通常作为HNC-21型数控装置XS10、XS11、XS20、XS21 接口的转接单元使用,以方便连接使用和提高可靠性。输入接线端子板提供NPN型和PNP型两种类型开关量信号输入,每块输入接线端子板有20个NPN型或PNP型开关量信号输入接线端子,最多可接20路NPN型或PNP型开关量信号输入。
输出继电器板集成八个单刀单投继电器和两个双刀双投继电器,最多可接16路NPN型开关量信号输出及急停(两位)与超程(两位)信号,其中8路NPN型开关量信号输出用于控制8个单刀单投继电器,剩下的8个NPN型开关量信号输出通过接线端子引出,可用来控制其他电器,两个双刀双投继电器可由外部单独控制。
试验台输入/输出开关量采用HC5301-8型输入接线端子板(如图3-22和图3-23所示)和HC5301-R型继电器板(如图3-24和图3-25所示),作为HNC-21型数控装置XS10、XS11、XS20、XS21接口的转接单元使用。

图3-22 HC5301-8型输入接线端子板示意图

图3-23 HC5301-8型输入接线端子板实物图

图3-24 HC5301-R型继电器板示意图

图3-25 HC5301-R型继电器板实物图
(3)输入/输出电路设计
对PLC而言,由机床或NC等外部设备向PLC传送的信号称为输入信号,由PLC向机床或NC等外部设备传送的信号称为输出信号;若信号的幅值是连续变化的称为模拟量信号,若只有导通和断开两种状态则称为开关量信号;开关量接口一般采用直流24V供电,低电平有效,即NPN型开关量接口,也有些采用或同时具备高电平有效的接口,即PNP型开关量接口。
① 典型的开关量输入接口等效电路如图3-26所示。

图3-26 开关量输入接口等效电路
外部触点闭合时,+24V电压加到接收器电路上,经滤波和电平转换处理后,输出至NC内部,成为内部电子电路可以接收和处理的信号。图3-26中接收电路采用光电耦合转换电路(虚线框内),开关量输入信号是机床侧的开关、按钮、继电器触点、检测传感器等采集的闭合/断开状态信号。这些状态信号需经上述接口电路处理,才能变成PLC或NC能够接收的信号。当采用有源开关器件(如无触点开关、霍尔开关等)时,必须采用DC 24V规格,检测元件的NPN(图3-26(a))/PNP(图3-26(b))型号必须与PLC接口的型号一致。
② 开关量输出接口。PLC输出电路一般为晶体管输出,如图3-27虚线内所示,最大输出电流一般为 100mA 左右,可以驱动发光二极管、灯丝指示灯、继电器线圈等。另外还可以经过继电器、晶闸管等放大后再输出到外部接口,继电器和晶闸管输出的负载能力较大,可以达到 2A 以上,能够驱动电磁阀和交流接触器线圈等。晶体管输出为直流输出,双向晶闸管输出为交流输出,继电器输出则交直流负载都可以。对于交流感性负载(如交流接触器线圈)必须在负载两端加阻容吸收电路,可以选用成品也可自行用 100~200Ω/1W 的电阻和0.1mF/630V的电容组装;对于直流感性负载(如继电器线圈)需加续流二极管。有些继电器自带续流二极管;在公共输出端必须串接短路保护器件(熔断器或空开)。

图3-27 PLC输出开关量接口等效电路
当负载的工作电压或工作电流超过输出信号的工作范围时,应先用PLC输出接口驱动小型继电器(一般工作电压DC 24V),然后再用它们的触点驱动强电线路的继电器、接触器或直接驱动这些负载。
可使用NPN型输出或PNP型输出,控制发光二极管时需串联一个电阻,控制流经发光二极管的电流,一般约为10mA,如图3-28所示。

图3-28 驱动发光二极管
使用NPN型输出或PNP型输出,控制灯丝型指示灯时需外接一预热电阻,如图3-29所示,以减少导通时的电流冲击,预热电阻阻值大小以指示灯点亮为原则。

图3-29 控制灯丝型指示灯
可根据需要选择NPN型或PNP型输出控制继电器,如图3-30所示,须在线圈附近接入续流二极管,以保护输出电路,减少干扰,有些继电器自带续流二极管。注:应选择线圈电压为DC 24V。

图3-30 驱动电感性负载(如继电器)
(四)解析电源模块的电气设计
电源模块是机床电气的一个重要组成部分,在这个模块,可以分析出机床所有电气元件的电源分配方法,当机床出现故障时,其实电源故障可能是其中重要原因,如果对电源模块非常熟悉,就可以尽快查明是否是由电源故障引起的。
1.电源电气原理分析
下面以华中数控车床试验台电源模块为例,讲解电源模块的分析方法,如图3-31所示为电源模块电气图。

图3-31 华中数控车床试验台电源模块电气图
首先,每个小组根据前面的学习内容及试验台的实物,列出所有需要电源的元器件,写在本单元的课业工作单上,如变频器、步进电动机驱动器、伺服电动机驱动器、2个接触器、2个继电器、PLC输入接口板、PLC输出接口板、刀架电动机、刀架霍尔传感器等,不仅要列出名称,而且还要有元件代号,如KM1。
然后分析电源模块电气图,写出图中(1)~(7)的电源值和线套的标号。
图3-31中7部分的电源就是机床所有电气元件的电源提供出处,然后就是要找出每个元器件和7个位置的对应关系,写在课业工作单里。
最后就是分析4个空气开关QF1、QF2、QF3和QF4的作用,这4个空气开关分别控制哪些电气元件,在机床调试时,是每一部分分别调试的,有时候没必要给全部元器件通电。
2.机床电气原理图绘制原则
下面以试验台强电电源模块的电气图为例,说明电气原理图的绘制原则。
① 电气控制线路的图形及文字符号。为了便于进行电气元件的安装、调整、使用和维修,在绘制电气线路图时,电气元件的图形符号和文字符号必须符合国家标准的规定。我国电气设备有关行业标准和国家标准有:JB/T 2739《工业机械电气图用图形符号》、JB/T 2704《工业机械电气设备电气图、图解和表的绘制》、GB4728《电气图用图形符号》及GB6988《电气制图》和GB7159《电气技术中的文字符号制定通则》,需采用最新的行业标准或国家标准。
例如,试验台用到的4个电源开关,从图3-31中可以判断它们的相数和额定电流大小,根据标号可以查看线路的连接情况。如QF1是试验台的总空开,三相输入,额定电流是6A,输入三相标号是L1、L2、L3,对应输出三相标号是U、V、W,它们要给主轴强电和伺服强电提供电源。根据标号可以查看机床电气线路的来龙去脉,便于检查和分析电气设备的故障。
② 图面区域的划分。为了便于检索电气线路,方便阅读和分析,图面分区时,竖边从上往下用拉丁字母A~F,横边从左到右用阿拉伯数字1~10分别编号。以附录B中强电/控制回路图为例,空气开关QF1和QF4对应的图形位置分别是A3和B7;伺服变压器TC2对应的位置是D4,输入三相电压是交流 380V,对应标号U11、V11、W11,输出三相电压是交流 200V,对应标号R、S、T。图区横向编号下方的“主轴强电”、“伺服强电”、“刀架电动机”等字样,表明它对应的下方元件或电路的功能,以利于理解全电路的工作原理。
③ 符号位置的索引。在较复杂的电气原理图中,对继电器、接触器的线圈的文字符号下方要标注其触点位置的索引,即在原理图中相应线圈的下方,给出触点的图形符号,并在其下面注明相应的索引代号。有时也可以采用省去触点图形符号的表示法。
符号位置的索引,用部件代号、页次和图区编号的组合索引法,索引代号的组成如下:

如在强电模块图中,图区D8中交流接触器KM1线圈下方是交流接触器KM1相应触点的位置索引,1-2触点位置索引为01/01/C5,表示KM1的1-2触点在部件代号为01,页次是第1页的C5位置。
④ 电气原理图中技术数据的标注。电气元件的技术数据,除了在电气元件明细表中表明外,有时也可用小号字体注在其图形符号的旁边。如空开QF1的图形符号的旁边的小号字体“9A”,表示空开QF1正常工作时的额定电流为9A。图中“3×2mm2”BK Cu等字样表示导线的根数、导线的截面积、导线的颜色和导线的材质。
⑤ 原理图一般分为主电路和辅助电路两部分。主电路就是从电源到电动机绕组的大电流通过的路径。辅助电路包括控制回路、照明电路、信号电路和保护电路等,由继电器的线圈和触点、接触器的线圈和触点、按钮、照明灯、信号灯、控制变压器等电气元件组成。
⑥ 原理图中电器的状态。原理图中所有电器的触点状态,都按没有通电或没有外力作用时的开闭状态画出。如继电器、接触器的触点,按线圈未通电时的状态画;按钮、行程开关的触点按不受外力作用时的状态画;控制器按手柄处于零位时的状态画等。
⑦ 原理图中交叉导线的表示方法。原理图中,有直接电联系的交叉导线的连接点要用黑圆点表示。无直接电联系的交叉导线,交叉处不能画黑圆点。
另外还要注意以下几点。
① 属于同一电器的线圈和触点,都要用同一文字符号表示。例如:同是KM,根据电气符号来区分是线圈还是触点;当使用相同类型电器时,可在文字符号后加注阿拉伯数字序号来区分。如KM1、KM2。
② 原理图中,各电气元件的导电部分(如线圈和触点的位置),应根据便于阅读和分析的原则来安排,绘在它们完成作用的地方。同一电气元件的各个部件可以不画在一起。
③ 原理图中,无论是主电路还是辅助电路,各电气元件一般应按照动作顺序从上往下、从左到右依次排列,可水平或垂直布置。
思考:试验台上电气元件琳琅满目,找出这些元件正常工作时的电压值,了解用数字万用表分析电压故障的方法。通过分析电源模块电路,了解各个电器的电源是如何被提供的,对照试验台查看电源的接线,熟悉各个电气元件的电源标号和接线的来龙去脉。
3.电源模块常用的电气元件
(1)空气开关
低压断路器又称自动空气开关或自动空气断路器,简称自动开关。用于电动机和其他用电设备的电路中,在正常情况下,它可以分断和接通工作电流;当电路发生过载、短路、失压等故障时,它能自动切断故障电路,有效地保护串接于它后面的电气设备;还可用于不频繁地接通、分断负荷的电路,控制电动机的运行和停止。
塑料外壳式断路器由手柄、操作机构、脱扣装置、灭弧装置及触点系统等组成,均安装在塑料外壳内组成一体。触点系统和灭弧装置用于接通和分断主电路,为了加强灭弧能力,在主触点处装有灭弧装置。脱扣器是断路器的感测元件,当电路出现故障时,脱扣器收到信号后,经脱扣机构动作,使触点分断。工作原理如图3-32所示,有三重保护,欠压脱扣器、过电流脱扣器和过载脱扣器。脱扣机构和操作机构是断路器的机械传动部件,当脱扣结构接收到信号后由断路器切断电路。断路器型号含义和电气符号如图3-33所示。

图3-32 断路器工作原理图

图3-33 断路器型号含义和电气符号图
塑料外壳式断路器外形图如图3-34右图所示,左图是小型断路器,主要用于照明配电系统和控制回路。

图3-34 断路器外形图
(2)变压器
变压器是一种将某一数值的交流电压变换成频率相同但数值不同的交流电压的电器。机床控制变压器适用于交流50~60Hz,输入电压不超过660V的电路,作为各类机床、机械设备等一般电器的控制电源、步进电动机驱动器、局部照明及指示灯的电源。常见机床变压器外形如图3-35所示,单相变压器图形符号如图3-36所示。

图3-35 机床控制变压器外形图

图3-36 单相变压器图形符号
现在普遍采用的三相交流系统中,三相电压的变换可用三台单相变压器也可用一台三相变压器,从经济性和缩小安装体积等方面考虑,可优先选择三相变压器,三相变压器外形图如图3-37所示。图3-38是三相变压器图形及文字符号,在数控机床中三相变压器主要是给伺服动力等供电。

图3-37 三相变压器外形图

图3-38 三相变压器图形及文字符号
(3)开关电源
开关电源被称为高效节能电源,因为内部电路工作在高频开关状态,所以自身消耗的能量很低,电源效率可达80%左右,比普通线性稳压电源提高近一倍。开关电源的外形图和图形及文字符号分别如图3-39和3-40所示。

图3-39 开关电源的外形图

图3-40 开关电源的图形及文字符号
目前生产的无工频变压器式小功率开关电源,仍普遍采用脉冲宽度调制器(简称脉宽调制器PWM)或脉冲频率调制器(简称脉频调制器PFM)专用集成电路。它们利用体积很小的高频变压器来实现电压变化及电网隔离,因此能省掉体积笨重且损耗较大的工频变压器。
(4)各类导线
① 数控机床上主要有三种导线:动力线、控制线和信号线。
选择导线应考虑下面几方面因素。
工作条件:如电压、电流、电击的防护。
外界影响:如环境温度、湿度或存在腐蚀物质或燃烧危险和机械应力(包括安装期间的应力)。
导线的横截面积、材质(铜或铝等)、绝缘材料等都是设计时需要考虑的,可以参照相关书籍手册。
② 连线和布线一般要求:
a)所有连接,尤其是保护接地电路的连接应牢固,没有意外松脱的危险。
b)连接方法应与被连接导线的截面积及导线的性质相适应。对铝或铝合金导线,应特别考虑电蚀问题。
c)只有专门设计的端子,才允许一个端子连接两根或多根导线。但一个端子只应连接一根保护导线。
d)只有提供的端子适用于焊接工艺要求才允许焊接连接。
e)接线座的端子应清楚做出与电路图一致的标记。
f)软导线管和电缆的敷设应使液体能排离该装置。
g)当器件或端子不具备端接多股芯线的条件时,应提供拢合绞线束的办法。不允许用焊锡来达到此目的。
h)屏蔽导线的端接应防止绞合线磨损并应容易拆卸。
i)识别标牌应清晰、耐久,适合于实际环境。
j)接线座的安装和接线应使用内部和外部配线,不跨越端子。
③ 导线的颜色标志。
a)保护导线(PE)必须采用黄绿双色。
b)动力电路的中线(N)和中间线(M)必须是浅蓝色。
c)交流或直流动力电路应采用黑色。
d)交流控制电路采用红色。
e)直流控制电路采用蓝色。
f)用于控制电路联锁的导线,如果是与外边控制电路连接,而且当电源开关断开仍带电时,应采用橘黄色或黄色。
g)与保护导线连接的电路采用白色。
五、单元学习活动
本单元主要目标是熟悉并掌握数控系统接口的应用和连接框图,查看数控机床上的各种电动机,并初步了解这些电动机的铭牌含义。通过自学、教师讲授获取PLC输入/输出转接板的作用,查看数据机床上输入/输出信号的安装位置;再采用案例教学的方式,各组针对电源模块电气原理图自主分析电源模块的作用,分析4个空气开关的作用并向全班解读,比较各组分析的结果以达到共同提高的目的;最后要求各组认真完成课业工作页的内容,本单元学习活动计划见表3-3。
表3-3 本单元学习活动计划

六、单元学习的资源要求
1.学习所需的场所、设备及工具
本单元学习不涉及车间机床设备,整个学习活动可在数控原理实训室开展。
数控原理实训室应配置工具展柜和资料柜,以提供常用电工工具和仪器仪表、机床常用电气元件实物和阅读学习所需要的各类资料。
根据个性教学的特殊需要,最好配置能进行网络资料查询的计算机。
2.技术资料
设备使用说明书、维护保养手册、电气原理图、电气元件安装图和接线图,安全操作规程、岗位职能要求及相关管理资料等;开展单元学习活动所需的学习指南、卡片纸及课业工作页(课业练习)等。
七、单元学习的考核评价
单元学习的考核评价不要仅仅局限于对学习结果的考评,更要注重工作学习活动的参与过程。考评围绕学习活动的各个环节,根据参与程度、工作学习态度、学习方法与技巧、小组合作情况、目标实现状况等全面考评,本单元主要考评项目组成参考如下。
成果评定:根据课业学习及工作页内容完成的质量情况进行评定,占60%;
学生自评:学生根据评分标准,对实施过程进行自评,给出相应的成绩,占10%;
学生互评:学生间互相交流,互相评价,占10%;
教师评价:教师根据学生的学习态度、工作态度、团队协作精神、出勤率、敬业爱岗和职业道德等情况,结合工作任务实施过程的各个环节进行评价,占20%。