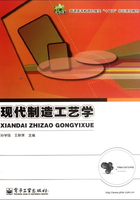
2.1.2 切屑形成过程中的变形特点
1.切屑的形成
切屑的形成是被切削的金属受到刀具的剪切和挤压,产生“剪切滑移”,使切削层与本体金属分离的结果。
如图2-5所示的被加工工件,当切削层受到刀具的挤压时,切削层产生弹性变形。由于工件是被固定的,切削层便沿OM线产生滑移,形成塑性变形。当塑性变形量超过极限时,切削层脱离本体金属,切屑便形成了。OM线与作用力的方向大约成40°~50°,称为滑移线。

图2-5 金属的挤压变形
2.切削时的变形区
如图2-6 所示,根据实验,切削时塑性变形由OA开始,至OM终了,形成AOM塑性变形区。由于塑性变形的主要特点是晶格间的剪切滑移,因此这一区域称为剪切区或第Ⅰ变形区;当切削层经剪切后形成的切屑以速度Vch沿前刀面流出时,摩擦力使切屑底层的金属又以剪切滑移的方法再一次变形。由于这种变形主要由摩擦所引起,因而称为摩擦变形区或第Ⅱ变形区;刀具后刀面和工件已加工表面之间,由于挤压、摩擦,使已加工表面产生变形,称为第Ⅲ变形区。

图2-6 切削时的三个变形区
这三个变形区汇集在切削刃附近,内应力比较集中而且复杂。金属就在此处被分离,一部分变成切屑,一部分形成已加工表面。刀具的几何角度、切削刃的形状及锋利程度、切削用量的大小等因素,决定着这三个变形区的大小。其中,切削刃对切屑的切除和已加工表面的形成影响最大。
3.剪切区的变形
剪切区(第Ⅰ区)是金属切削过程中,切应力最大,变形最剧烈的区,切屑的形成就是从这个区开始的。
如图2-7 所示,当切削层中的某一质点P,以切削速度v向刀具接近,未到达剪切区时,只产生弹性变形。随着P点向刀具的逐步逼近,弹性变形越来越大,被切削金属的内应力也随之增大。当P点到达滑移线OA上的1点时,内应力达到材料的屈服点而产生剪切滑移,于是P点未能到达2′点,而是沿滑移线OB滑移到 2 点。同样,P点也未能到达滑移线OC、OM上的3′、4′点,而是沿3、4点从前刀面流出。我们将2-2′、3-3′、4-4′称为滑移量;将金属开始产生滑移的滑移线OA称为始滑移线,结束滑移的滑移线OM称为终滑移线。这个区域就是我们所说的剪切区。在这个区域内,金属沿滑移线产生剪切滑移形成塑性变形,从而形成切屑。

图2-7 剪切区与剪切面
图2-7(a)中,每条滑移线都代表一个切应力相等的曲面,不同的滑移线上的切应力大小不相等。OA上的切应力值等于被加工金属的屈服点,而OB、OC、OM上的切应力,则由于加工硬化而依次升高,在OM达到最大值τmax。当τ未达到金属的抗剪极限时,产生的切屑为带状切屑;当τ达到抗剪极限时,就产生挤裂切屑。
剪切区是一很窄的区域,在一般切削速度范围内大约宽度为0.02~0.2 mm。为方便起见,常用一个平面OM代表这个区域,称为剪切面。如图2-7(b)所示,剪切面OM与切削速度v之间的夹角φ称为剪切角。
我们可以把金属切削过程粗略地模拟为图2-8 的示意图。金属的被切削层好比一叠卡片1′、2′、3′、4′等,当刀具切入时,叠迭卡片被推挤到1、2、3、4等的位置。卡片之间沿剪切面发生滑移。卡片与刀具前刀面接触部

图2-8 金属切削过程示意图
分由于刀具的挤压和摩擦变得较为平整,而外侧则呈锯齿形,或呈不明显的毛茸状,并产生卷曲,便形成切屑。
4.切屑的基本形态
金属切削时,由于工件材料、刀具几何角度、切削用量等的不同,会出现不同形态的切屑,一般可归纳为四种基本形态。
(1) 带状切屑 切屑呈连续条带形状,与刀具前刀面接触的底层较光滑,背面呈毛茸状。一般在加工塑性材料(如碳钢),采用大前角、小的切削厚度、高的切削速度时,会形成这种切屑。这也是正常切削条件下最常见的切屑形态,如图2-9(a)所示。

图2-9 切屑的基本形态
(2) 挤裂状切屑 切屑背面呈锯齿形,内表面时有裂纹。在加工塑性材料、采用小前角、大切削厚度和小切削速度时,会形成这种切屑,如图2-9(b)所示。
(3) 单元状切屑 切削塑性很大的材料,如铅、纯铜等,切屑容易在刀具前刀面上黏结而不易流出,从而产生很大变形,使材料达到断裂极限,形成较大的变形单元,从而形成这种切屑,如图2-9(c)所示。
(4) 崩碎状切屑 切削脆性材料,如铸铁、黄铜时,切削层通常在弹性变形后未经塑性变形,突然崩碎而成为不规则的碎粒状切屑。工件材料越硬,刀具前角越小,越容易形成这类切屑,如图2-9(d)所示。
切削时,在产生带状切屑的过程中,切削力变化较小,切削过程稳定,已加工表面质量好。但切屑为很长的带状,影响机床的正常工作和人员安全,因此要采取卷屑、断屑措施。在产生挤裂和单元状切屑的过程中,切削力有较大的波动,尤其是单元状切屑,在其形成过程中,可能产生振动而影响加工质量。