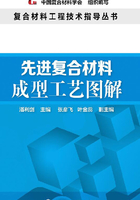
第2章 预成型体
2.1 自动铺放
自动铺放技术包括自动铺带技术和自动铺丝技术,这两项技术的共同优点是采用预浸料,并能实现自动化和数字化制造,高效高速。自动铺放技术特别适用于大型复合材料结构件制造,在各类飞行器,尤其是大型飞机的结构制造中所占比重越来越大。
2.1.1 自动铺带
自动铺带机由美国Vought公司在20世纪60年代开发,用于铺放F-16战斗机的复合材料机翼部件。随着大型运输机、轰炸机和商用飞机复合材料用量的增加,专业设备制造商(如Cincinnati Machine公司、Ingersoll公司)在国防需求和经济利益的驱动下开始制造自动铺带设备,此后自动铺带技术日趋完善,应用范围越来越广泛。
自动铺带技术采用有隔离衬纸的单向预浸带,剪裁、定位、铺叠、辊压均采用数控技术自动完成,由自动铺带机实现。利用多轴龙门式机械臂可完成铺带位置自动控制,核心部件——铺带头(图2-1)中装有预浸带输送和预浸带切割系统,根据待铺放工件边界轮廓自动完成预浸带特定形状的切割,预浸带加热后在压辊的作用下铺叠到模具表面。自动铺带技术是复合材料成型自动化的典型代表,集机电装备技术、CAD/CAM软件技术和材料工艺技术于一体,其具有高效、高质量、高可靠性、低成本的特点,主要用于平面型或低曲率的曲面型构件,或者说准平面型复合材料构件的层铺制造,特别适合大尺寸和复杂构件的制造,减少了拼装零件的数目,节约了制造和装配成本,极大地降低了材料的废品率和制造工时。按所铺放构件的几何特征,自动铺带机分为平面铺带(FTLM)和曲面铺带(CTLM)两类。FTLM有4个运动轴,采用150mm和300mm宽的预浸带,主要用于平板铺放。CTLM有5个运动轴,主要采用75mm和150mm宽的预浸带,适于小曲率壁板的铺放,如机翼蒙皮、大尺寸机身壁板等部件。

图2-1 自动铺带头
复合材料自动铺放系统由预浸带供料盘、自动铺放机(包含铺带头)、构件模具、数控系统、复合材料构件、CAD/CAM软件等组成。自动铺带的主要工作过程为:将复合材料预浸带安装在铺放头中,多轴机械臂对铺带位置进行自动控制,预浸带由一组滚轮导出,预浸带加热后在压辊的作用下铺叠到工装或上一层已铺好的材料上,切割刀将预浸带按设定好的方向切断,能保证铺放的材料与工装的外形相一致,铺放的同时,回料滚轮将背衬材料回收。
工业实践表明,应用自动铺放装备生产的复合材料构件,和传统人工/半自动层铺复合材料构件工艺相比,在层铺劳动量、铺放生产率、材料利用率、制造精度、生产成本等方面均具有很大的优势,其中铺放生产率可达到10~40kg/h,是人工层铺的数十倍,适合于复杂复合材料结构的制造。
自动铺带技术可提高复合材料产品的质量和生产效率、降低制造成本、减轻结构重量,因此该技术已广泛应用于B787(中央翼盒、主翼蒙皮、尾翼)、A400M(机翼、翼梁)和A350XWB(机翼、蒙皮、中央翼盒)等型号飞机,如图2-2所示。

图2-2 自动铺带设备成型A350壁板蒙皮
2.1.2 自动铺丝
自动铺丝技术由美国航空制造界在20世纪70年代开发,用于复合材料机身结构制造,主要针对缠绕技术的不足进行创新,其技术核心是铺放头的设计研制和相应材料体系与设计制造工艺开发。波音公司研制出“AVSD铺放头”,解决了预浸纱、切断与重送和集束压实的问题,1985年完成了第一台原理样机,法国宇航公司(Aerospatial)1996年研制出欧洲第一台六轴六丝束自动铺丝机,德国BSD公司2000年研制出七轴三丝束热塑性窄带铺丝试验机。20世纪80年代后期,专业数控加工设备制造商积极介入,进一步研发自动铺丝机,Cincinnati Machine公司1989年设计出其第一台自动铺丝系统并投入使用,该系统申请注册的专利多达30余项。其在硬件方面也不断进步:机型从原来的Viper 1200、Viper 3000、Viper 4000升级到Viper 6000,数控系统从模拟量控制的A975升级到全数字控制的CM100,开发了专用的CAD/CAM软件和ACES系统。Ingersoll公司1995年研制出其第一台自动铺丝机,该自动铺丝机采用FANUC数控系统和自行开发的CPS软件,其铺丝头结构独特、特性好,适于大型产品生产,尤其是该公司最新开发的大型立式龙门铺丝机,效率之高,可以与自动铺带机相媲美,适于大面积、大曲率构件成型,为制造飞机复合材料构件提供了成型手段。美国的其他公司,包括设备制造商、飞机部件制造商和研究机构也不断开发自动铺丝技术,包括双向铺丝技术、丝束重定向控制、预浸纱整型、纤维连续平滑移动铺放、柔性压辊、热塑性自动铺丝、超声固结成型等技术。最新进展包括预浸纱气浮轴承传输、多头铺放、可换纱箱与垂直铺放、丝-带混合铺放等。
自动铺丝技术综合了自动铺带和纤维缠绕技术中的优点,铺丝头把缠绕技术中不同预浸纱独立输送和自动铺带技术的压实、切割、重送功能结合在一起,由铺丝头将数根预浸纱在压辊下集束成为一条宽度可变的预浸带,宽度大小通过程序控制预浸纱根数自动调整后铺放在芯模表面,加热软化预浸纱并压实定型。典型的自动铺丝机系统包括7个运动轴和12~32个丝束预浸纱或带背衬的切割预浸窄带输送轴。
与自动铺带技术相比,自动铺丝技术有两个突出的优点。
〈1〉 采用多组预浸纱,具有增减纱束根数、根据构件形状自动切纱以适应边界的功能,几乎没有废料,且不需要隔离纸就可以完成局部加厚、混杂、加筋、铺层递减和开口铺层补强等多种设计要求。
〈2〉 由于各预浸纱独立输送,不受自动铺带中自然路径轨迹的限制,铺放轨迹自由度更大,可以实现连续变角度铺放,适合大曲率复杂构件成型。
纤维束自动铺放设备成型的机头和机身段如图2-3所示。

图2-3 纤维束自动铺放设备成型的机头和机身段
2.1.3 自动铺放的国内外发展
20世纪70年代末期至80年代初,第一批商业生产的自动铺带机(平面、曲面)推出,并用于军用轰炸机B-1、B-2的飞机部件制作。
20世纪80年代以后,自动铺带技术开始广泛应用于商业飞机的制造领域。同期,美国航空制造商将自动铺带技术广泛应用于其他项目,主要包括:F-22战斗机(机翼)、波音777民用飞机(全复合材料尾翼、水平和垂直安定面蒙皮)和军用C-17运输机(水平安定面蒙皮)、V-22倾转旋翼飞机(旋翼蒙皮)等。欧洲复合材料铺带成型的产品含有机翼蒙皮、尾翼、翼梁、增强肋等,主要包括空客A330/A340(水平安定面蒙皮)、A340-500/600(尾翼蒙皮)和A380(安定面蒙皮、中央翼盒)等。
自动铺带技术经过20世纪90年代的蓬勃发展,在成型设备、软件开发、铺放工艺和原材料标准化等方面得以深入发展,相关软件界面更加友好,铺放机铺放效率和可靠性更高。2006年以后,欧美将自动铺带技术应用于Boeing787(中央翼盒、主翼蒙皮、尾翼)、A400M(机翼、翼梁)、A350XWB(机翼、蒙皮、中央翼盒)等型号飞机上。
经过几十年的发展,带有双超声波切刀切割系统和在线检测系统的10轴铺带机已经成为自动铺带系统的标准配置,铺带宽度最大达到300mm,生产效率达到1000kg/周,铺带成型质量显著提高。
自动铺丝技术在第四代战斗机的典型应用包括S形进气道和中部机身翼身融合体蒙皮。波音直升机公司率先应用自动铺丝技术研制V-22倾转旋翼飞机的整体后机身,原有后机身由9块手工铺叠的壁板装配构成,改为整体铺放后,减少了34%的固定件、53%的工时,废品率降低了90%。Raytheon公司率先在商用飞机机身的研制中应用自动铺丝技术,包括Premier Ⅰ和霍克商务机的机身。Premier Ⅰ机身采用整体成型蜂窝夹层结构,取消了框架和增强肋,没有铆钉和蒙皮接点。前机身从雷达罩壁板一直延伸到后压力舱壁板(长8m),包括行李舱、座舱和驾驶舱后机身从后压力壁板延伸到机尾(长5m),采用整体复合材料结构的机身比铝合金机身减重273kg。
自动铺丝技术在Premier Ⅰ上的成功应用为其在大型飞机上应用奠定了坚实的基础。自动铺丝技术最早在大型飞机上的应用包括B747及B767客机的发动机进气道整流罩试验件,该整流罩试验件在制造过程中采用自动铺放与固化分离技术。自动铺放技术在A380飞机上的应用以自动铺带为主,用于生产垂尾、平尾和中央翼盒等,并开始在尾段采用自动铺丝技术。
举世瞩目的B787,其复合材料使用量达到50%,这在很大程度上得益于自动铺放技术:所有翼面蒙皮均采用自动铺带技术制造,全部机身采用自动铺丝技术整体制造,首先分别由不同承包商分段制造,然后在西雅图工厂组装。
国内自动铺带技术研究起步较晚,起步于“十五”初期,南京航空航天大学率先开始自动铺放技术的研制。2004年起,与北京航空材料研究院联合开发自动铺带设备,并完成了小型铺带机的研制工作,南京航空航天大学设计了具有3轴平移、双摆角运动的5轴台式龙门机械臂,研制了力矩电机收放、步进电机驱动的预浸带输送、预浸带气动切割与超声辅助切割、主-辅压辊成型等技术。应用开放式数控系统技术开发出5轴联动、3轴随动切割和温度与压力控制的自动铺带控制系统软硬件,实现了预浸带定位、剪裁、热压铺叠基本功能。在此基础上,2005年研制成功国内第一台自动铺带原理样机,实现了自动铺带的基本功能。北京航空材料研究院应用这台样机开展了环氧预浸料和双马来酰亚胺预浸料铺带适应性与铺带工艺试验。上述基础性的研究工作为进一步发展具有自主知识产权的自动铺放技术奠定了基础。
国内同时开展自动铺带技术与应用研究的有哈尔滨飞机工业公司、北京航空材料研究院、北京航空制造工程研究所、武汉理工大学和天津工业大学等。武汉理工大学和天津工业大学在自动铺带机机构设计分析、控制系统架构与仿真等基础研究方面开展了诸多有益探索。2006年,中航工业北京航空制造工程研究所启动了大型复合材料构件自动铺带设备的研制及应用研究项目,与Forest-Line公司合作,采用引进自动铺带头关键部件集成的技术路线研制翼面大型自动铺带机,该研究所自主开发了大型复合材料自动铺带专用设备,为国内自动铺带技术的发展奠定了材料基础。哈尔滨飞机工业公司于2007年引进西班牙自动铺带机,应用进口预浸料实现了试验翼面的自动铺带工艺,并用国产预浸料开展了工程应用试验研究。“十一五”期间,国内已经突破了自动铺带装备和软件关键技术,铺带材料和铺带工艺技术成为制约自动铺带技术发展的关键。进一步完善装备功能,实现设备专用化和多样化以满足不同需求将是今后一个时期自动铺带技术的发展重点。