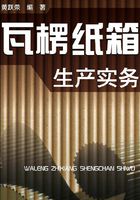
第三节 常见瓦楞纸板毛病与解决办法
瓦楞纸板线生产机速很快,如发现问题应当即立断进行处理,方能将损失减少到最小,因此对各种原纸质量毛病要有快速检查的方法和处理问题的思路。发现问题时,可通过下述方法来检查处理这些问题。
① 用眼看。
② 用手摸纸板。
③ 用手撕单面纸板的黏合情况。
④ 先排查和解决易处理的问题,再解决难度较大的环节,最后解决较复杂的因素。
在自动线上,瓦楞纸板产生毛病的根源概括起来,不外乎是纸、设备、黏合剂、蒸汽温度、生产机速和操作方法。下面就针对这些具体因素提出相应的解决办法。
一、瓦楞纸板翘曲产生的原因
瓦楞纸板翘曲与各层原纸的含水率、定量差、厚薄均匀度、各层单面瓦楞纸板的施胶量、整条瓦线的生产机速、加热温度、各处制动装置的张力调节等有关。
纸板向上翘:里纸含水率高,生产机速慢,里纸定量低,在双面机上A瓦楞的施胶量太大,自动线热板温度过高。纸板朝下翘:机速太快,面纸水分含量太大,在双面机上B楞的施胶量太大,热板温度不够。
S形翘曲:纸板两边上胶不均匀,原纸水分横向不均匀,天桥或面纸的张力调节不当。
做好产生不合格瓦楞纸板的预防工作应从三个方面进行。
1.把好原纸关
① 原纸含水率一般应控制在8%±1%,在整个纸幅宽度上的水分要求分布均匀,含水率高与含水率低的原纸不要搭配生产,否则易导致生产出来的瓦楞纸板出现“S”形或对角翘曲。
② 在配纸方面,面纸、里纸的克重不能相差太大,一般应控制在50g/m2以内,且所用纸的纤维构成最好相近,防止因原纸的收缩率不一致而出现翘曲。
③ 原纸的吸水性和脱水性要稳定。
2.生产过程中的操作控制
① 原纸在预热器上烘干面积的控制 面纸、里纸含水不均则要通过预热烘烤来调控,如果面纸、里纸或瓦纸含水率高,则烘干面积要大,使含水率下降幅度大。如果面纸、里纸或瓦纸含水率低,则烘干面积要小,使含水率下降幅度小。
② 控制热板温度 如果面纸含水率高,可适当提高热板温度,使面纸含水率下降;反之,则减少热板加热量。
③ 控制生产机速 纸板向上翘的原因是里纸含水率高。应该在保证瓦楞纸板黏合良好的前提下,提高生产机速,缩短面纸的烘烤时间,减少面纸的水分蒸发。纸板向下翘,说明面纸水分含量高,应降低生产机速。
④ 控制施胶量 对湿度大的单面瓦楞纸板减少施胶量,对湿度小的单面瓦楞纸板加大施胶量,来调整合成纸板的含水率,减少纸板翘曲。
3.对已生产出来的翘曲瓦楞纸板进行后处理
因刚下生产线的瓦楞纸板是热的,湿度较大,且水蒸气还没全部散发出来或被瓦楞纸板吸收,采用以下办法进行补救处理可提高瓦楞纸板的平整度。
① 将每一手纸板按正反不同的方向整齐码放压平,或者马上用带吹风的压平机,将纸板压平后迅速将其吹冷。
② 将纸板用湿抹布在翘纸板的外面抹湿后,再一手正一手反整齐地堆码压2天。
二、纸板黏合不良产生的原因
设备的温度不够,生产机速过快会引起黏合剂未糊化,或者是温度达到要求而生机速过慢引起黏合剂提前糊化后失去黏性。另外,黏合剂固含量太低,黏合剂的黏度太小或储存时间太长已变质,黏合剂的糊点太高,施胶间隙过大或过小导胶没有糊化或者施胶太少无法形成黏接,原纸水分含量太高或原纸太厚,蒸汽温度不够也会影响纸板黏合。
解决方法:提高蒸汽压力,检查疏水阀的排水情况;适当控制自动线的生产机速,检查黏合剂的质量参数是否合格;检查相关机台的施胶间隙是否符合工艺要求,检查单面机的压力辊与瓦楞辊的间隙是否符合工艺规定;换掉不合格的原纸。
三、瓦楞纸板裁切尺寸不稳定
横切刀齿轮间有纸屑纸灰,或是齿轮轴承损坏,天桥单面瓦楞纸板堆积过多或者是运行阻力过大。热板输送皮带老化与纸板的摩擦力小而打滑,横切机无级变速齿轮啮合间隙过大或转动链条老化、松弛。横切电脑控制程序紊乱,受强磁干扰。
解决方法:检查热板部位的主电动机是否缺相,电压是否稳定,轴承是否损坏,清除横切刀转动齿轮间的纸屑,更换齿轮轴承,控制天桥纸板储存量;对天桥各导纸辊转动不灵活的轴承加注润滑油或进行更换,控制好天桥上的单面纸板张力真空吸风量;更换热板部位老化的主皮带,纠正无级变速齿轮间的间隙,更换新链条或适当调整链条张紧装置;排除强磁干扰。
四、瓦楞纸板表面出现皱折
(1)合成纸板后的面纸出现皱折原因 面纸水分不均匀,原纸在无轴芯支架上两边的张力调节不当。
解决方法:加大面纸在预热器上的包角,调紧面纸起折那边的张力。
(2)单面瓦楞纸板的瓦纸出现皱折的原因 上、下瓦楞辊平行度未调好,导致压瓦时瓦纸的收缩率不一致。原纸两边的水分含量不一致或者两边的张力调节不当。
解决方法:调好瓦辊平行度,调紧瓦纸起折那边的张力。
(3)瓦楞纸板里纸或夹层纸出现皱折的原因 压力辊与瓦楞辊两边的间隙未调好,压力辊与瓦楞辊的平行度未调好,原纸两边的水分不均匀;原纸未预热或者预热不够,纸送入瓦楞机内未对齐,里纸在无轴芯支架上两边的张力调节不当。
解决方法:检查压力辊与瓦楞辊的间隙和平行度,换掉水分不均匀的原纸,使原纸在预热器上有足够的预热,送齐原纸,重调张力。
五、面纸或里纸露瓦楞痕迹
面纸或里纸露瓦楞痕迹的产生原因:纸的克重太低,生产机速太慢,原纸水分过大,施胶量太大,压力辊的压力太大。
解决方法:调换克重高的纸,适当控制机速,减小施胶量,适当调轻压力辊的压力。
六、高低瓦楞
产生的原因:瓦楞辊的楞沟内有浆渣草节,卷筒纸被摔扁不圆,导致压制瓦楞时卷筒纸出现两边甩动。瓦楞辊的温度不够,导致瓦楞成型不好,原纸水分过大,瓦纸张力过大。瓦楞辊或者瓦楞辊轴承已磨损,导致瓦楞辊在运行过程中跳动和振动。修复的瓦楞辊再次磨损,致使瓦楞辊的直径更小,导致气缸达不到规定的行程,而出现高低瓦楞、倒楞、跳楞等。
解决方法:将瓦楞辊上的浆渣草节清除干净,换掉不圆的卷筒纸;升高瓦辊温度或者适当降低生产机速,清除瓦辊上的胶渣,适当减小瓦纸张力,加大瓦楞原纸在预热器上的包角;换掉已磨损的瓦楞辊或对瓦楞辊进行修复,对经多次修复过的瓦楞辊再次被磨损的,只有作报废处理。
七、面纸、里纸过窄,出现瓦楞外露或者瓦纸短缺
产生的原因:面纸、里纸幅宽太窄,各层纸的收缩率不一样,或者是各层纸未对齐。
解决方法:将面纸、里纸换成幅宽与收缩率一致的原纸,对齐各层纸的边缘。
八、横切小规格纸板造成瓦楞纸板面、里纸横切刀口破损
产生的原因:横切刀不快,横切机瞬时加速调节不当引起阻纸。
解决方法:换刀、磨刀、调好瞬时加速调节器的微调;将纸板规格改成双连片进行裁切。
九、瓦楞纸板纵切产生毛刺
产生的原因:碗刀的上下刀片配合有较大的间隙,或者是刀口有缺损。如果是薄刀,则是刀片不快,刀口咬合太深,生产出的瓦楞纸板太湿。
解决方法:定期磨刀,换掉刃口变钝的刀,重新调整刀的咬合深度;将上、下纵切刀靠紧,降低生产机速,烘干瓦楞纸板水分。
十、瓦楞纸板压线后面纸炸裂和纸箱摇盖折叠时断裂
产生的原因:纸板线机速太慢导致瓦楞纸板面纸失水严重,纸质太差,带线轮压力太重将面纸压破;或者是压线轮的压力太轻,导致压线处的瓦楞未受压,当折叠纸箱摇盖时因瓦楞太硬而造成摇盖折叠断裂;压线轮公母线轮未居中,导致压出的母线受力不均匀,出现纸箱摇盖折叠时、外摇盖线单边受力。
解决方法:提高机速,保证压线轮的压力适中,换纸,在摇盖压痕线处湿水,对准上、下压线轮。
十一、白板纸泛黄
产生的原因:机速过慢,施胶量太大,黏合剂中用碱量过大。
解决方法:提高机速,减少施胶量,严格控制黏合剂的用碱量。
十二、纸板倒楞、溃楞(瓦楞纸压破)
纸板倒楞、溃楞产生的原因与解决方法如下。
① 瓦楞辊的温度没有升起来,需提前预热瓦楞辊。
② 瓦楞两边出现对称的压倒,使瓦纸穿绕次数多且包夹角太小,张力过大。减少穿绕次数,降低纸的穿绕夹角或减小在预热器上的包夹角。
③ 无轴芯支架上的张力调得太紧,或者是无轴芯支架上的轴承无油和卷筒纸被摔扁。重新调节张力、换掉摔扁的原纸。
④ 吸附式单面机的吸力不够,检查吸气装置,包括抽真空的吸力、气孔、管道、过滤器是否通畅,密封性能是否良好。
⑤ 瓦楞原纸太湿或生产机速太快,需降低生产机速。
⑥ 瓦楞辊间的压力太大,将上瓦楞辊压力缸的压力杆距离调大,达到减小两瓦楞辊压力的目的。
⑦ 瓦楞辊的平行度未调好。瓦楞朝前倒,调整瓦楞辊的偏心轮要向后调;瓦楞朝后倒,调整瓦楞辊的偏心轮要向前调。
十三、加工工艺不良导致瓦楞纸板边压强度和平压强度低
产生的原因:原纸水分含量过大,生产机速太快,用纸克重低,纸板施胶量过大,印刷大面积满版实底图案,印刷压力过大,纸箱生产环节过多,原纸环压强度低。
解决方法:在预热器上把所有原纸都包满。降低生产机速,把瓦纸改用低克重箱纸板,用鼓风机把刚下瓦线的热纸板中的水蒸气吹干,当印刷满版实底图案时改用回弹性好的树脂版,降低满版面的印刷压力,减轻印刷过程中每一个滚筒间对纸板的压力,减少产品加工环节,提高用纸的质量。
十四、生产过程中断纸频率高
生产过程中断纸频率高产生的原因如下。
① 原纸内的断头未接好,或天桥上的单面瓦楞纸的接头未接好。
② 天桥上的单面瓦楞纸板堆放太多,被拉断。
③ 无轴心支架上的张力太大。
④ 原纸被摔扁。
⑤ 原纸太干。
⑥ 原纸在预热器上的包入夹角不适当。
解决办法:换掉断头未接好的原纸和被摔扁的原纸,在遇到原纸接头时马上松动制动器或按原纸运转方向推动卷筒纸。待接头过去后,再收紧制动器,减小原纸在预热器上的包夹角,翻动天桥上被堆压的纸板。
十五、压出的瓦楞纸成荷叶边
产生的原因:瓦楞纸太宽,瓦楞辊边上的温度太低。
解决方法:使用规定幅宽的原纸,提高瓦楞辊的温度。
十六、纸箱抗压强度低
纸箱抗压强度低,可从工艺、材料、设备、设计、箱型、保管方面采取如下办法加以解决和提高。
① 加工瓦楞纸箱时不能让箱身四条棱的瓦楞受损伤。
② 严格控制水分,保证纸箱尽可能干燥。因为纸箱含水率每增加一个百分点,其抗压强度就会降低5%~10%。
③ 开槽不要走规,开槽深度要控制在摇盖压痕线的二分之一处,因为箱角是受力的主要部位。
④ 在价格相同的情况下,承接抗压强度要求低的纸箱。
⑤ 纸箱舌头采用黏合时,一定要黏结牢固,面、里纸不要用容易分层的再生纸,要选用紧度高的原纸。
⑥ 多用生料瓦纸,少用熟料瓦纸,或者用高强度、低克重瓦楞原纸和高强度牛皮卡纸生产纸箱。
⑦ 在印刷机上要最大限度地减少各种滚筒对瓦楞纸板的压力,适当提高印刷机车速,使纸板快速通过印刷机,减少纸板受压时间,尤其不要印刷热瓦楞纸板,达到减小印刷机对瓦楞纸板强度的损伤。
⑧ 提高瓦楞纸板的黏合强度。
⑨ 纸箱的尺寸尽量走下公差,让可承受压力的内装物承受一点支撑。
⑩ 在双面机处要严格控制施胶辊的间隙,防止瓦楞被压伤或受损。
⑪增加纸箱附件进行补强。
⑫用低克重、高强度纸来提高纸箱抗压强度。
⑬尽量减少纸箱加工环节对瓦楞纸板强度的损伤。
⑭改机械黏箱为手工黏箱,减少纸板受压环节。
⑮在纸箱抗压指标一样时选纸箱高度小的纸箱承接。因为纸箱高度为20cm的比25cm的抗压强度略高,高度为10cm的比25cm的抗压强度可提高20%。纸箱超过25cm时抗压强度的变化不大。
⑯纸箱长宽比例设计选(1∶1.3)~(1∶1.5),其抗压强度值可处于峰值状态。