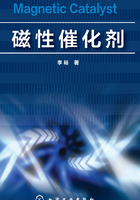
2.1 磁性催化剂的复合原理
磁性复合催化剂的构造类型有混合型和壳核型两大类。其中,混合型复合催化剂多采用两种或几种粉体经过物理手段进行混合,主要借助撞击、扩散和剪切等外力作用将一种粒子均匀掺杂于另一种粒子,从而形成聚集体混合物。
构成的混合型磁性催化剂的内部和表面均存在磁性颗粒或活性组分,这种类型的复合催化剂通常先分别制备好磁性粒子和活性组分粒子,然后通过机械方式进行物理混合,混合过程必须添加黏结剂,根据磁性催化剂使用的场合选择黏结剂的种类。
混合型磁性催化剂的构造要注意以下条件:
①活性组分粒子和磁性粒子的大小与比例;
②活性组分粒子和磁性粒子的形状;
③进行活性组分粒子成膜化处理时,活性组分粒子的软化转变点;
④混合比由加工目的和用途来确定。
优良的混合型磁性催化剂不仅要具有快速的磁响应性能,更要具备较高的催化活性,与此同时,还要求磁性催化剂在液相或气相中磁性载体与活性组分结合牢固,在强力机械搅拌下活性组分不发生分离或脱落。
混合型磁性复合催化剂是将纳米级磁性物质和活性组分进行物理混合包杂,在黏结剂的作用下将两者紧密黏合(见图2-1)。混合型磁性催化剂制备的关键是如何防止复合过程中活性组分的比表面积和孔体积的大幅度损失,也就是如何保护孔隙结构问题。有效解决这些问题不仅涉及所选用的黏结剂为有机型或无机型,更重要的是针对使用的黏结剂采用的孔隙保护措施。

图2-1 混合型磁性催化剂复合过程
混合型复合催化剂具有制备工艺简单、易于调配比例和制备成本低的优点。但是,混合型复合催化剂存在微观不均匀性、粒子间的结合力较弱、宏观颗粒粒径较大需要粉碎的缺点。
2.1.1 机械力化学复合过程
机械力化学复合是指专门研究通过对粉状物质施加机械力而引起的物理或化学性质的变化以及发生系列化学反应的学科。机械力化学效应主要表现在以下几个方面:
①机械力化学作用可以引起晶体物质产生晶格畸变、晶格缺陷和无定形化,表面自由能增大,外激电子发射,生成游离基及出现等离子区等。
②机械力化学作用可以引起化学键的折断和重组,可使新鲜的断裂表面上出现不饱价键和带正电或负电的截断单元等。
③机械力化学效应可以引起非晶体物质的无序或有序化。
④机械力化学效应在宏观上表现为系列物理化学性质变化,如热稳定性降低,耐酸碱性降低、溶解性、活性、反应速率等提高,吸附性、粘接性、水化性、流变性、亲和性、离子交换和置换能力、密度、分散性等发生变化,引起粉体均化及化学反应等。
固体颗粒在复合过程中,由于机械力化学作用导致其表面活性增强的机理主要表面在以下几个方面:
①颗粒在机械力作用粉碎生成新表面,颗粒粒度减小,比表面积增大,从而使颗粒表面自由能增大,活性增强。随着固体颗粒粒度的减小,规整的晶面在颗粒体系总表面上所占的比例减小,键力不饱和的质点(原子、分子)点全部质点数的比例增多,在尖角、棱边处不饱和程度高的质点也增多,从而大大提高了颗粒的表面活性。
②颗粒在机械力作用下,表面层产生晶格缺陷,发生晶格畸变和格子变形,这些缺陷和变形储存了部分能量,使表面层位能升高,活性能降低,活性增强。颗粒受机械力作用,随着颗粒的细化将脆性破坏变化为塑性变形,塑性变形的实质是位错的增殖和移动。颗粒发生塑性变形需消耗机械能,同时在位错处又储存能量,这就形成机械力化学的活性点,增强并改变固体颗粒的化学反应活性。
③固体颗粒在机械力作用下,表面层结构发生破坏,并趋于无定形化,内部储存了大量能量,使表面层位能更高,活性能更小,表面活性更强。研磨系统输入能量的大部分将转化热能,使颗粒物料表面温度升高,这在很大程度上,提高了颗粒的表面活性。
④粉碎可截断颗粒内部的价键,这种断裂时所产生的新表面上的游离不饱和价键在没有外来物质时,驱使邻近颗粒的相互黏附和聚集,在存在表面活性剂或其他化学物质时,可发生化学反应。
⑤机械力作用导致晶格松弛与结构裂解激发出的高能电子和离子形成等离子区。高激发状态诱发的等离子体产生的电子能量可以超过10eV,而一般化学反应在温度高于1000℃时电子能量只有4eV,即使光化学的紫外电子能量也不会超过6eV,物质内部迅速发展的裂纹使其顶端温度和压力增高,顶端温度可达1300K以上。
⑥机械化学力效应增强的原因,因其产生的各自场合而异,在含有扩散过程的固相反应中,颗粒内含有的缺陷构造是活化的根本原因,接触反应的颗粒中,电子缺陷和电子浓度却起到更大的作用。
机械化学力复合利用挤压、冲击、剪切、摩擦等机械力将改性剂均匀分布在粉体颗粒外表面,各种组分相互渗入和扩散形成包覆。目前,主要应用的有球石研磨法、搅拌研磨法和高速气流冲击法。其优点是处理时间短,反应过程容易控制,可连续批量生产,比较有利于实现各种树脂、石蜡类物质以及流动性改性剂对粉体颗粒的包覆。但是,也存在着机械处理过程中无机粒子的晶型被破坏、包覆不均匀等缺点,且机械化学改性多用于微米级粉体的包覆。机械力化学效应在无机粉体复合方面主要有以下几方面:
①促进无机粉体表面化学改性,将无机粉体粉磨过程产生的机械化学力作用与无机粉体表面化学改性结合,充分利用机械力化学效应强化无机粉体的表面改性。
②利用机械力化学作用在无机粉体表面直接实施改性,如无机粉体表面聚合接枝改性、改善吸附性、机械合金化等。
③机械力化学改性是无机粉体微胶囊化改性的重要手段。
2.1.2 气相沉积复合过程
气相沉积法主要包括气相化学沉积法和雾化液滴沉积法,利用过饱和体系中的改性剂在颗粒表面聚集而形成对粉体颗粒的包覆。气相化学沉积法是通过气相中的化学反应生成改性杂质分子或微核,在颗粒表面沉积或与颗粒表面分子化学键合,形成均匀致密的薄膜包覆。雾化液滴沉积法是将改性剂通过雾化喷嘴产生微细液滴,液滴分散于颗粒表面,经过热空气或冷空气的流化作用,溶质或熔融液在颗粒表面沉积或凝集结晶形成表面包覆。
2.1.3 超临界流体复合过程
流体在超临界状态下具有气相的高扩散系数和液相的强溶解能力的特点。超临界流体快速膨胀包覆法利用超临界流体在流化床的快速膨胀,使改性微核在颗粒表面形成均匀的薄膜包覆。超临界流体在快速膨胀过程中,超临界相向气相的快速转变引发流体温度、压力的急剧降低,从而导致溶质在超临界溶剂中溶解度的急剧变化,在高频湍动的膨胀射流场中瞬间均匀析出溶质微核。膨胀气流携带这些微核与流化床中的颗粒碰撞,产生均匀接触,从而在细颗粒表面形成均匀包覆。通过控制膨胀前温度、包覆时间达到控制释放,从而控制包覆致密度与包覆厚度。由于超临界流体快速膨胀后的溶剂与溶质颗粒容易快速彻底分离,不会对产品产生任何污染。
2.1.4 非均相生长复合过程
非均相生长机理从结晶化学角度从发,在某pH环境下,有异相物质存在时,如溶液超过它的过饱度就会有大量的晶核立即生成,沉积到异相颗粒表面形成包覆层,此时晶体析出的浓度低于溶液中无异相物质时的浓度,这是由于在非均相体系的晶体成核与生长过程中,新相在已有的固相上成核或生长,体系表面自由能的增加量小于自身成核或者均相成核体系表面自由能的增加量,所以分子在异相界面的成核与生长优于体系中的均相成核。非均相生长复合常用方法有沉淀法、溶胶-凝胶法、异相凝聚法、微乳液法和化学镀法等。
(1)沉淀法
沉淀法是通过向溶液中加入沉淀剂(如氨水)或引发体系中沉淀剂的生成(如尿素的热解反应),使改性离子发生沉淀反应,在颗粒表面析出,对颗粒进行包覆。调节体系温度、蒸发溶剂等物理方法可用来增大沉淀生成物的过饱和度。
(2)溶胶-凝胶法
溶胶-凝胶法首先将改性剂前驱物溶于水或有机溶剂形成均匀溶液,溶质与溶剂经水解或醇解反应得到改性剂(或其前驱物)溶胶;再将经过预处理的被包覆颗粒与溶胶均匀混合,使颗粒均匀分散于溶胶中,溶胶经处理转变为凝胶,最后高温煅烧凝胶得到外表面包覆有改性剂的粉体。
(3)胶体凝胶法
胶体凝胶法由金属盐溶液和金属氧化物或氢氢化物溶胶制备得到。通过溶液中的改性组分沉淀反应条件的控制,使生成的颗粒不产生大量的沉淀析出,而直接得到溶胶,亦可先将改性组分沉淀出来,再经解凝,使凝集的沉降颗粒分散成胶体粒子,制备成溶胶。溶胶制备好后,与被包覆颗粒均匀混合,凝胶化后经高温处理得到包覆型粉体。
(4)异相凝聚法
异相凝聚法是根据表面带有相反电荷的微粒会相互吸引而凝聚的原理提出的。如果一种微粒的粒径远小于另一种带异种电荷微粒的粒径,那么这两种微粒在凝聚过程中,小微粒就会吸附在大微粒的外表面,形成包覆层。其关键在于微粒的表面电荷,通过温度调节来控制溶液中非离子型表面活性剂的活性,对微粒表面进行修饰,或直接调节溶液的pH值,从而改变微粒的表面电荷。异相凝聚法可用于各种组成的微粒之间的包覆,但包覆过程对溶液的pH值要求非常严格,两种微粒的粒径也要相配,通常情况下这种依靠电荷吸引而产生小微粒在大微粒外表面的包覆不是很紧密牢固。
(5)微乳液法
微乳液法是两种不互溶液体在表面活性剂作用下形成的热力学稳定、各相同性、外观透明或半透明分散体系,其分散相为纳米尺寸,介于10~100nm。微乳液法包覆是结合了微乳液纳米反应器和微乳聚合两种技术。纳米反应器即通常所说的W/O(油包水)型微乳液(其水核被表面活性剂所组成的单分子界面层所包覆),它提供了一个微小的水核,可以用来制备所需的纳米颗粒,即被包覆颗粒。微乳聚合是限制在微乳核内的分散聚合,因此,利用微乳聚合可以形成对W/O型微乳液水核中纳米颗粒的包覆改性。微乳液法包覆改性技术的关键在于设计一个适当的微乳体系,首先设计一个用来制备纳米颗粒的纳米反应器,然后选择一个可以增溶有关试剂的微乳聚合。
(6)化学镀法
化学镀法主要用于粉体表面包覆金属或复合涂层,实现陶瓷与金属的均匀混合,从而制备复合材料。其实质是镀液中的金属离子在催化作用下被还原剂还原成金属粒子沉积在粉体表面上,是一种自动催化氧化还原反应过程,因此可以获得一定厚度的金属镀层,且镀层厚度均匀,孔隙率低。此法关键在于合理配比镀液中的稳定剂、复合物和金属离子的浓度,以稳定镀液,同时保证镀液的镀覆能力。
一般来说,磁性催化剂的复合与构造多数在液相中完成,磁性颗粒和催化活性颗粒在液相中分散行为、相互作用以及聚集特性对于磁性催化剂的构建会产生重要的影响,了解单分散颗粒的制备、单分散性颗粒的再分散、颗粒间相互间作用以及颗粒团聚对于磁性催化剂的复合与构造至关重要。