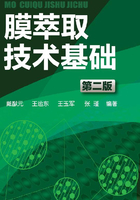
2.6 乳状液膜分离技术的工艺流程及影响因素
2.6.1 乳状液膜分离技术的工艺流程
乳状液膜分离技术的工艺流程比较复杂,其主要工序为乳状液膜制备、接触分离、沉降澄清、破乳等,一般流程如图2-16所示。

图2-16 液膜分离的一般性工艺流程
图2-17是一连续式乳化液膜工艺的流程图。它主要是由超声波制乳器、转盘塔和静电破乳等几部分组成。

图2-17 液膜废水脱酚转盘塔连续小试设备流程[2]
1—废水输送泵;2—废水高位槽;3—超声波制乳器;4—油膜溶液储槽;5—NaOH水溶液储槽;6—乳状液膜高位槽;7—转盘塔;8—静电破乳器;9—油膜溶液储槽;10—转盘马达;11—流量计
(1)乳状液膜的制备 将含有膜溶剂、表面活性剂、流动载体以及其它添加剂的液膜溶液同内相试剂溶液混合,可以制得所需的水包油(O/W)型或油包水(W/O)型乳状液。在制乳过程中,主要应注意表面活性剂加入方式,制乳的加料顺序,搅拌方式和乳化器材质的浸润性能等。
为制得稳定的乳状液,内包相液滴的大小需保持在1~3μm,这就要求有很高的能量输入,通常可通过高速搅拌机、超声波乳化器在实验室制备稳定的乳状液。对于大规模乳状液的制备,一般采用胶体磨、动态均质器或静态均质器[36]。
通过外界能量的输入或高剪切力使液滴变形破碎,分散在体系中,传统的制乳方法在一定程度上都存有能耗大、效率低、能量输入不均、制得的乳液滴粒径较大、分布广、容易发生聚并、不稳定等问题。骆广生等[37]选择陶瓷微孔膜制乳。微孔膜对于低界面张力体系及中等界面张力体系,可以制得粒径小、分布窄、较为稳定的乳状液,而且能耗小、操作简单。
(2)接触分离 在接触分离阶段,乳状液膜与料液相进行混合接触,实现传质分离。在间隙式混合设备中,适当的搅拌速度是极其关键的工艺条件之一。与溶剂萃取类似,乳状液膜用的传质设备可以是混合-澄清槽或塔设备。混合澄清槽操作灵活,可适应料液、相比及流量的变化,其缺点是设备庞大,可能有较大的试剂损耗。与混合-澄清槽相比,塔式设备占地少、效率高。在连续塔式接触器中(如转盘塔),需选择适当的流量和塔内转盘的转速,以降低塔内的轴向混合,提高塔内乳状液的滞留量,为传质提供有利的条件。
在间隙式混合设备中,一般使用传统的搅拌桨,当搅拌速度较慢时,无法使乳状液和料液相充分接触,影响传质;若搅拌速度加快,又往往会影响乳状液的稳定性。李明玉等[38]采用气泡搅拌方式,通过调节气流量的大小,控制乳状液在料液相中的分散程度,使乳状液和料液相均匀接触,使传质速率和提取效果得到改善。
液膜分离过程中,乳状液和外水相混合接触是传质分离的基础。乳状液与水相混合分散过程中生成大量细小的乳状液滴,提供了巨大的传质比表面积,是使液膜技术具有高效和快速等特点的重要原因之一。另外,液膜的溶胀和破损也与乳状液的分散程度及乳状液滴的大小密切相关,因此,有关乳状液膜的分散研究受到广泛关注。
通常以Sauter平均直径(体积/比表面积平均直径,d32)表征分散过程中乳状液滴的直径大小。Sharma等[39]在对液膜体系中乳状液滴作用力分析的基础上,同时考虑乳状液与外水相的体积比以及乳状液中油相与水相体积比的影响,推导出下列半经验关联式:
(2-20)
(2-21)
d0=C1(1+α1ϕ1)1.2(1+α2ϕ2)1.2We-0.6L (2-22)
式中,We=N2L3ρ c/σ;B、C1为无因次经验常数;L为搅拌桨直径;N为搅拌速度;N vi为黏性因子;d32为Sauter平均直径;d0为非黏滞性液滴直径;ρ c为连续相密度;ρ d为分散相密度;α1、α2为湍动耗散常数;μ d为分散相黏度;ε为单位质量的平均能量耗散率;ϕ1为乳状液中内水相的体积分数;ϕ2为乳状液的体积分数;σ为乳/水界面张力。
Sharma等[39]制备了一系列W/O及O/W乳状液,并改变ϕ1及ϕ2,测定了W/O/W及O/W/O体系中乳状液滴的大小,按上述公式进行回归,得出式中常数B=4.08,C1=0.053,α1=α2=2。同时,将文献中的实验结果和按上述公式的计算结果进行了比较,结果吻合良好。
(3)沉降澄清 沉降澄清步骤是使富集了迁移物质的乳状液与残液之间沉降澄清分层,以减少两相的相互夹带。液膜工艺中的澄清操作与常规溶剂萃取类似,不做详细讨论。
(4)破乳[5] 使用过的乳状液需要回收并重新使用,富集了溶质的内相也需要汇集,这就需要破乳。在这一步骤中,希望减少膜相物质的损失,并降低能量消耗、药品消耗和投资费用。破乳效果的好坏直接影响到整个乳状液膜分离工艺的经济性。
破乳方法有两种类型,一种是化学法破乳,另一种是物理法破乳。加破乳剂属于化学法。离心、加热、施加静电场等属于物理法。
① 破乳剂法。破乳剂是一种有机溶剂或有机溶剂混合物,它与液膜中任一组分不发生化学反应,并具有挥发性强、沸点低、可回收的特点。破乳剂通过界面吸附引起表面活性剂在油/水界面脱附,从而达到破乳的目的。常用的有机溶剂有异丙醇和丙酮等。破乳剂法在一定范围内是有效的,缺点是加入破乳剂会提高乳化剂的消耗、其成本高,且增加了污染,工业应用价值不大。
② 高速离心法。把乳状液经过高速离心机分离,借助于乳液的膜相和内相的密度差,迅速分层澄清,回收膜相。这一方法的投资费用和操作费用很高,特别在含水量很高时,更是如此。
③ 静电破乳法。把乳状液置于常压或高压电场(直流或交流均可)中,使乳状液中分散的微细液滴聚结形成大液滴,并在重力作用下沉降分离。这一方法操作简便、设备简单,容易实现连续化,是国内外乳状液膜研究及应用中普遍采用的破乳方法。
④ 加热破乳法。将乳状液加热,随着温度上升,膜相黏度下降,同时乳状液聚结加剧,促使液膜破裂。这一方法的缺点是费用太高,不常采用。
⑤ 研磨破乳法。利用具有不同粒径的球形亲水材料为研磨剂,在电动搅拌耙推动下,进行旋转研磨,在摩擦力和剪切力的作用下达到破乳目的。吴子生等[40,41]开发了研磨破乳技术,并设计出研磨破乳器。实验结果表明,研磨法对于高含水量的乳状液的破乳率可达98%,且原料廉价易得,设备简单,操作方便,是有应用前景的破乳技术。褚莹等[42]通过实验研究认为,研磨破乳可分两个步骤。首先是过滤破乳,过滤过程中乳状液内相液滴在研磨剂表面铺展成膜,并进一步聚并;然后是研磨破乳,研磨剂的相互碰撞使乳状液的分散液滴受到摩擦和剪切,导致液滴的聚并。
⑥ 膜破乳法。倪邦庆等[43]采用无机微孔膜,骆广生等[44]采用聚四氟乙烯微滤膜,分别进行了膜法破乳的实验研究。研究结果表明,膜破乳法具有分离效率较高、能耗和操作费用低、不需要添加试剂、装置相对简单、通用性较强等优点。应用微滤膜破乳时,膜材料的选择十分重要。当所处理的乳状液为O/W型乳液时,选用亲油的高分子聚合物;当处理的乳液为W/O型乳液时,则应该选用亲水材料的微滤膜,如金属微滤膜等。
⑦ 联合破乳法。将上述方法结合进行,如将高速离心与加热相结合、高速离心与破乳剂相结合,均可达到较好的破乳效果。宋友等[45]研究提出,对于W/O乳状液,利用电场和研磨联合破乳,可以大大提高破乳的程度。李思芽等[46]的研究结果表明,对稳定的乳状液膜体系,只在离心条件下破乳是困难的;在低电压下,高频脉冲电压破乳的效率也是不高的;但是,在离心及脉冲电压联合条件下破乳,效果则较好,破乳率达到99%以上。
上述的几种破乳方法中,静电破乳比较成熟,特别是高压静电破乳。
乳状液膜静电破乳的影响因素主要包括与破乳器电性能相关的参数及影响乳状液性能的一些因素,如电极的绝缘材料、破乳电压、频率和波形、温度、搅料以及乳状液本身的组成、配比等。此外,迁移过程中的溶胀现象和静电破乳过程可能发生的絮状物也对静电破乳有影响。
静电破乳用电极绝缘材料一般耐高压、介电常数高、化学稳定性好。
破乳电压的大小对破乳过程有明显影响。随着破乳电压的升高,破乳速率亦升高。必须注意的是,升高电压是有一定限度的,过高的电压对水滴具有分散作用,还有可能击穿电极绝缘层,产生火花,对油相造成破坏。
大量研究表明,频率对破乳影响极大,但有关频率对破乳的作用机理尚不十分清楚。交流电的波形对破乳也具有影响,采用方波的破乳效果优于三角形波、正弦波和锯齿形波。在相同峰值电压下,方波对乳液中的水滴作用时间长。同时,方波及其谐波频率范围广,包含了破乳所需的频率范围。
温度升高可以降低乳状液的黏度或引起表面活性剂分子热运动的加剧,导致脱附,使水滴在电场作用下更容易聚结,加速破乳。然而,过高的温度也会使部分表面活性剂因挥发或反应而损失,不利于操作。
破乳过程中,适当的搅拌有利于增大内水相水滴相互碰撞的概率,提高破乳速度。同时,适当的搅拌有利于减少静电破乳过程中海绵状第三相的形成和积累。
此外,改变乳状液的组成配比会对乳液的性能产生影响,从而影响破乳的效果。
目前,乳状液膜技术虽然有工业化应用报道,但距大规模工业应用尚有一定距离,而破乳技术的进一步完善将是该技术工业化进程中的关键课题之一。
2.6.2 乳状液膜分离中工艺条件的影响
(1)搅拌速度 搅拌速度包括制乳时的搅拌速度及乳液与待分离体系两相接触分离时的搅拌速度。在制乳阶段,通过搅拌输入外加能量,使内包相呈微滴状分散到膜相中去。此时,搅拌速度愈大,形成乳液滴的直径愈小,一般采用2000r/min的速度即可达到制备稳定乳状液膜的要求。当连续相与乳状液接触时,加入搅拌使乳状液与待分离溶液充分接触,提供尽可能大的表面积。这里,搅拌速度有其最佳的范围,速度过快,液膜容易破裂;过慢的搅拌速度则难以实现乳液相的分散。混合强度对液膜除酚过程的分离效果的影响如图2-18所示[2]。

图2-18 混合强度对分离效果的影响[2]
(2)接触时间 接触时间是指在适当的搅拌速度下,料液与液膜互相混合接触的时间。由于液膜体系两相接触表面积大、液膜薄、渗透快,两相往往在较短时间内即可达到分离要求。若进一步延长接触时间,分离效果并无提高,相反可能会使少量液膜破裂,分离效果反而下降。
(3)料液的浓度和酸度 液膜分离特别适用于低浓物质的分离提取,一般浓度范围可以从几个毫克/升到质量分数1%~2%。若料液浓度较高,一级处理达不到要求时,可以采用多级处理。采取逆流操作时效果更好。一般在使用液膜技术处理废水时,为达到排放标准并简化其操作,往往要求废水浓度有一定的上限。
料液中的酸度即pH值对液膜分离效果的影响是不容忽视的。一些分离过程在一定的pH值条件下,待分离物质能与膜相中的载体形成络合物而进入液膜相,取得明显的分离效果。然而pH值条件不能满足时,这类过程则难以进行。例如,黏胶纤维生产中的含锌废水的pH值较低(0.5),在这种情况下,D2EHPA、Cyanex272及PC88A均不能有效萃取锌。
(4)操作温度 液膜分离操作一般是在常温或料液温度下进行的。提高温度虽然可能加快传质速率,但降低了液膜的黏度,增大了膜相的挥发性,甚至可能加速表面活性剂的水解,降低液膜的稳定性和分离效果。
综上所述,影响液膜分离效果的因素很多,且往往相互关联、相互制约。进行这方面的研究探讨工作,综合分析和确定体系的配制条件和工艺操作参数,提出一个经济、高效的乳状液膜分离工艺,是很有意义的。