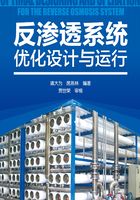
1.5 反渗透技术的发展
随着反渗透技术应用领域的不断扩展、相关工程规模的不断扩大,反渗透膜技术的自身水平也在不断地提高。反渗透膜技术与膜工艺主要沿着加强分离功能、提高工艺水平与克服膜体污染三条主线向前发展。加强膜分离功能方面主要包括提高脱盐率、降低工作压力等项内容;提高工艺能力方面主要包括提高抗氧化能力、加大膜元件规格、提高膜元件承受压力、减少过膜元件压力损失等项内容;克服膜体污染方面主要包括增强材料亲水性、降低膜表面粗糙度、膜表面电荷中性化等项内容。
1.5.1 膜材料与膜结构
工业用反渗透膜的材料主要分为醋酸纤维素(CA)与芳香聚酰胺(PA)两大类,醋酸纤维膜与芳香聚酰胺膜相比,前者亲水性好、抗氧化性强、表面光滑,而后者的工作压力低、耐酸碱性强、耐生物污染、产水量高,具有更强的化学稳定性。醋酸纤维素膜是反渗透膜的早期产品,日本东洋纺公司目前尚在坚持醋酸纤维素中空膜产品的生产,而绝大部分其他膜厂商已相继转用芳香聚酰胺膜材料。目前芳香聚酰胺膜技术以其优越的性能得到了快速发展与广泛应用。
早期CA单质膜结构的分离材料较厚,同时起着分离与支撑作用,其透速率较低、工作压力较高、膜工艺效率较差。后期PA复合结构的分离层与支撑层材料相异,有效分离层极薄,透速率较高,工作压力较低,大大提高了膜工艺的效率。复合结构不仅已成为卷式膜的基本膜体结构,中空式膜体也开始向复合结构发展。
早期的纳滤膜沿用聚酰胺材料,其脱盐率长期居高不下,因而限制了其使用的效果与范围。近期的纳滤膜材料开始使用磺化聚醚砜等多种材料,有效地降低了脱盐率,扩展了其应用领域。
1.5.2 元件结构的演化
反渗透膜元件的结构形式中,板式、中空及管式结构的市场相对狭窄。作为早期中空膜厂商代表的美国杜邦公司(Du Pont)已经停止其中空膜的生产,著名的日本东洋纺(Toyobo)中空膜的销量也极其有限。卷式膜结构因性价比高、对给水预处理要求低、应用领域广,而赢得了巨大的市场份额。目前,卷式膜因发展的高速度及广阔的市场占有率,使其几乎成为反渗透膜的代名词。
1.5.3 提高脱盐率水平
反渗透工艺的主要目的是脱除给水中的盐分,反渗透膜的主要技术指标是脱盐率。醋酸纤维素膜脱盐率仅有约95%,芳香聚酰胺复合膜脱盐率可高达99.5%,近年来各膜厂商又相继推出了更高脱盐率的膜品种。高脱盐率膜品种不仅可提高产水水质,提高系统工作效率,减轻树脂交换床或EDI等后处理工艺的负荷,甚至可使一级高脱盐率膜系统的脱盐水平达到两级较低脱盐率系统水平,从而有效地简化了系统结构。
1.5.4 降低膜工作压力
反渗透工艺是以膜两侧压差为工作动力,因此施于膜元件给浓水侧的工作压力水平成为重要的技术指标。早期芳香聚酰胺复合膜的工作压力为1.5MPa,近20年来陆续面世的低压及超低压复合膜的工作压力降至1.0MPa及0.7MPa。工作压力的降低既可降低给水泵的设计压力与管路的额定压力,减少了设备投资;更可以直接降低膜系统的电功率损耗,尽显膜技术的低能耗优势。降低工作压力是以特定产水通量(也称水通量、膜通量或通量)为基准,故降低工作压力的另一提法是在特定工作压力条件下提高膜体产水通量。
当膜工作压力低于1.0MPa时,系统浓水渗透压将与纯驱动压位于同一数量级。低压膜系统中,在高系统收率、高给水温度、高给水盐量及长系统流程工况下,将造成系统流程中各膜元件通量的严重失衡。因此,超低压膜的优势主要体现于商用及民用小系统或低含盐量给水的限定环境。
1.5.5 提高抗污染能力
膜污染是膜过程的伴生现象,故增强膜材料的抗污染能力始终是膜制备技术发展的重要目标之一。提高反渗透膜的抗污染能力,主要是改善膜的粗糙度、电荷性及亲水性等方面。
①降低膜表面粗糙度 由于聚酰胺材质及复合结构的特征,聚酰胺复合膜表面较为粗糙,易于污染且难于清洗,故各膜厂商竞相采取措施以降低膜表面的粗糙程度。海德能公司的低污染膜(LFC1、LFC3系列)在原有的聚酰胺复合膜上再复合一层抗污染材料,以增强复合膜表面的平整度,并增强了膜表面的化学抗污染能力。陶氏化学公司的低污染膜(BW30-FR系列)直接提高了聚酰胺膜表面的光滑度,即具有较强的物理抗污染性能。
②调整膜表面电荷极性 聚酰胺膜表面一般带有少量负电荷,易于形成正电性胶体污染。为了同时降低膜表面的正负电性胶体污染,部分膜厂商推出电中性膜品种。在脱盐效果方面,带正电荷膜对于正离子的脱除率更高,带负电荷膜对于负离子的脱除率更高。如将带不同性质电荷的膜品种用于前后两级反渗透系统,可分别对水体中的正负离子产生较高脱除率,从而有效提高两级系统的整体脱盐率水平。
③提高膜材料的亲水性 聚酰胺等有机膜材料的原始性能是疏水性,而疏水膜的水透过性能及抗有机物污染性能均差,故各膜厂商均在材料改性即提高膜亲水性方面进行各种努力并取得了显著进展。
1.5.6 提高抗氧化能力
在水处理工艺领域内,水体中氧化剂含量是一个重要指标,它是工艺流程中染菌或生藻的有效抑制物,也是高分子膜材料降解的主要原因。反渗透工艺流程中最佳的氧化剂分布是:在预处理工艺首端投放适量氧化剂,在各预处理工艺中保持氧化剂浓度,以维护工艺过程的无菌藻状态;在膜处理工艺中截留氧化剂,并防止膜系统的微生物污染。实现这一理想抑菌过程的重要一环是反渗透膜的高抗氧化性。
聚酰胺材料的抗氧化性较差,对给水中的游离氯含量一般只存在1000h·mg/L及0.1mg/L浓度的耐受能力。对自来水水源,游离氯本已经达到杀菌要求浓度,而对地表水等无氯含量水源,预处理系统首端需要加氯灭菌。为满足反渗透膜的低氯浓度要求,预处理系统末端需增加除氯工艺,从而增加了系统的预处理成本。此外,从除氯工艺位置开始至整个膜系统流程均无杀菌剂保护,微生物的滋生在所难免。特别是在膜元件的给浓水流道中,有机物的截留与无杀菌剂保护状态,必然会导致微生物污染。降低系统成本且免于膜系统微生物污染的根本解决方案是提高膜材料自身的抗氧化性能。
目前,时代沃顿等厂商推出的抗氧化聚酰胺反渗透膜的抗氧化能力可达26000h·mg/L及0.5mg/L浓度。
1.5.7 提高耐高压能力
对于一般低含盐量水体,以节能为目的的膜工艺,应具有低工作压力性能;但对于高含盐量水体,给浓水的高渗透压推高了膜工艺的工作压力,这一现象在海水淡化工艺中达到了极致。
一般海水淡化用反渗透膜元件的耐压在8.3MPa范围以内。在15℃给水温度及35000mg/L给水含盐量的标准海水条件下,回收率达到45%时的浓水渗透压已达4.3MPa,保持20L/(m2·h)产水通量水平的工作压力超过7MPa,这几乎已达一般海水膜承受压力的极限状态。
如进一步提高海水淡化系统的回收率,膜元件的最高耐压即成为一个重要的限制因素。日本东丽公司等膜厂商已开发出了耐压为10MPa的超高压海水淡化膜。用段间加压泵与超高耐压膜构成的两段式海水淡化系统可以使全系统回收率增至60%。
1.5.8 提高耐高温水平
反渗透水处理系统面对的工业环境即地表水、地下水及市政污水的温度多低于45℃,故45℃的最高给水温度工作条件可以满足绝大部分工程要求,但部分化工过程中的水体温度较高。
不少化工分离过程中,被处理料液需要始终保持较高温度,膜元件的低工作温度将限制反渗透工艺的使用。一些可降温处理的料液,在反渗透处理前的降温处理过程将增加工艺流程与工艺成本。一些后续工艺需再次加温的料液处理过程,还将再次增加工艺成本,从而大大削弱了反渗透工艺的节能优势。
美国GE/Osmonics/Desal公司推出的工作温度为70℃的反渗透膜产品,为高温特殊环境下反渗透技术的应用提供了条件。
1.5.9 增大膜元件规格
一般而言,膜元件的规格越大,则单位体积内的有效膜面积越大,单位膜面积的成本越低,膜系统配套管路越少,膜系统占用空间越少。由于不同的系统规模需要不同的元件规格与之匹配,随着反渗透系统规模的不断扩大,要求膜元件规格不断增长。
较大规格膜元件的制备具有较高的技术含量,元件规格的增长也具有一个发展过程。20世纪80年代产生了4in膜元件,90年代产生了8in膜元件,近年来各膜厂商不断出现了10in、12in、15in甚至18in膜元件。一支18060规格(18in直径60in长度)元件相当于7支8040规格元件的膜面积与产水量,但占用空间减少了50%,管路长度减少了60%。大规格膜元件的广泛应用将有效降低大型膜系统的元件成本、管路成本与空间成本,并可大幅提高系统可靠性。
日产淡水62.7×104m3的以色列Sorek海水淡化厂,由于采用了16in规格膜元件而节省3/4的系统管路及其他硬件成本。
1.5.10 增加膜元件面积
除增大膜元件的规格之外,也可以在特定的膜元件直径与长度规格范围内,通过优化相关的材料、结构与工艺来有效提高元件内的有效膜面积,进而提高特定规格膜元件的工作效率。近二十年来,8040规格膜元件的有效面积已经从早期的34.0m2增长到37.2m2甚至达到40.9m2。
1.5.11 改变隔网的厚度
卷式膜结构优于中空膜结构的主要原因是卷式结构具有更强的耐污染能力,具体体现在由浓水隔网形成的可迂回流道及较大的流道高度。较大的隔网高度,不仅可以防止污染物堵塞流道,还可以降低流道阻力。在特定规格元件内,以保持有效膜面积为基础,不断提高浓水隔网高度是膜制备技术的又一发展方向。早期34m2面积膜元件的浓水隔网高度仅有28mi,而一些膜厂商已将该高度提升到34mil,因而具有了更好的耐污染能力与更小的膜压降指标。
1.5.12 改进隔网的形状
早期膜元件浓水隔网多成正方形网格,而为形成更好的紊流流态,以降低浓差极化指标,一些膜厂商已将隔网形状改为不同经纬线夹角的菱形,以形成更好的耐污染能力与更小的膜压降指标。此外,一些厂商还采用具有抑菌性能的隔网材料,以有效抑制浓水流道中微生物的滋生,降低微生物污染的速度,延长膜元件的清洗与寿命周期。
1.5.13 增加膜袋的数量
以膜两侧压力差为推动力的反渗透工艺中,降低膜元件的淡水背压可有效降低工作压力与工艺能耗。构成淡水背压的各项内容中,元件淡水流道压降占据一定比例。提高元件淡水流道的高度受到元件内膜面积容积率的限值;而膜袋数量越少,淡水流道越长,淡水背压越高。因此,各厂商将8040元件中膜袋数量不断增加,以有效降低膜元件的淡水背压。
1.5.14 改进膜元件端板
一般8in膜元件的端板呈圆形平面,串联膜元件之间只有很小的缝隙。在初装系统的启动过程中,膜壳与元件间的空气通过端板缝隙被逐步压入元件给浓水流道,并随元件浓水排出系统。由于元件间的缝隙狭窄,空气排出速度较慢,致使系统启动过程较长。
海德能公司在元件端板处设置了排气槽,使串联膜元件之间形成了较大间隙,大大加快了系统启动时膜壳与元件间气体的排出速度,有效减少了系统的启动时间,降低了水锤效应损伤膜元件的概率。
反渗透膜技术是一项高速发展的工业技术,各膜厂商竞相推出更高性能的膜产品。如海德能公司1989年推出其低压聚酰胺复合膜CPA2,1995年推出超低压复合膜ESPA1,1996年推出纳滤膜ESNA,1998年推出更高脱盐率的ESPA2与更高产水通量的ESPA3,并在同年推出耐污染膜LFC系列,2000年推出更低工作压力膜ESPA4,2003年推出的CPA2-HR具有更高的脱盐率与产水通量,2004年推出膜面积为40.9m2的ESPA2+,2005年推出低压降膜CPA3-LD,2009年推出PROC-10与PROC-20等更低压降膜,2010年推出抗菌性34mil隔网。
反渗透膜材料与制膜技术的进步,提高了材料性能、降低了工作能耗,增加了膜系统的效率、减小了预处理的负荷,使反渗透膜技术具有了更大的技术优势与市场竞争力。