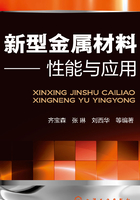
1.1 超级钢(新一代钢铁材料)概述
1.1.1 新一代钢铁材料(超级钢)的概念
(1)何谓“新一代钢铁材料”?
新一代钢铁材料系指具有组成单元超细晶、化学成分(杂质)高洁净度、显微组织高均匀性的组织、成分和结构特征,以及高强度、高韧性的力学性能特征的新一代钢铁材料。即在环境性、资源性和经济性的约束下,采用先进制造技术生产具有高洁净度、高均匀度、超细晶粒特征的钢材,强度和韧度比传统钢材提高,钢材使用寿命增加,满足21世纪国家经济和社会发展的需求。新一代钢铁材料,亦称超级钢,或称超细晶粒钢等。
(2)新一代钢铁材料(超级钢)的开发是经济建设和社会发展的需求
1995年日本发生大地震,当地钢铁建筑毁于一旦,引发日本学界对钢铁材料重要性的思考。为适应未来发展,很多学者提出要开发更坚固的钢铁材料,这就是研发“超级钢”的起源。日本钢铁界和国家金属研究院经过1995~1996两年的调研,在日本科技厅支持下,于1997年4月正式启动了“超级钢材料国家研究计划”,目标是在10年内开发出把钢的“实际使用强度提高1倍,结构的寿命提高1倍,降低总成本,降低对环境的污染度”的超级钢,用于道路、桥梁、高层建筑等基础设施建材的更新换代。此举措被认为是对世界上最重要的工程结构材料——钢铁的再认识,是“第二次铁器时代”来临的前期征兆,吹响了“向钢铁进军”的新号角(表1-1)。
表1-1 日本新世纪结构材料(超级钢铁材料)研究课题与目标

在日本超级钢项目的影响下,1998韩国启动了“21世纪高性能结构钢发展”的10年国家计划。2001年欧盟启动了“超级晶粒钢开发”计划。2002年美国在钢铁研究指南中公布了两个新一代钢铁材料开发项目。
我国钢产量自1996年以来一直稳居世界第一,但在钢铁品种、质量方面与世界先进水平仍有很大差距,沿用了几十年的钢种体系急需更新换代。1998年在国家重点基础研究发展规划项目“973计划”中启动了“新一代钢铁材料的重大基础研究”项目,并将超级钢思路发展成“超细晶粒钢”。该课题的目标是在生产成本基本不增加的前提下将现有碳素钢、低合金结构钢和合金结构钢的强度目标提高1倍,即分别达到400MPa、800MPa和1500MPa,并满足韧性和各种使用性能要求。超级钢(新一代钢铁材料)的深入研究和应用开发正成为21世纪钢铁材料界的历史使命。到2001年后,全球范围的新一代钢铁结构材料研发工作已蓬勃展开,陆续取得了阶段性成果和成效(如开发出原型钢、进行中试等)。
我国研究工作的主要目标是在保证有良好塑韧性基础上大幅度提高钢材强度,其技术思路是以细化钢材的晶粒和组织为核心,同时提高钢的洁净度,并改善钢的均匀性。在理论研究基础上,把钢的强度提高1倍。此外还须满足:生产成本不增加或增加不多;塑韧性基本不下降以保证符合生产、应用要求。即做到低成本和高性能的统一,把传统材料改造、提升为低成本高性能的新型材料。其优越性是节约资源、能源,降低生产成本,改善废钢的可循环使用性,利于可持续发展。
近几年,国内外的新一代钢铁材料项目主要以高强度化与长寿命化为研究主题,以800MPa高强度钢、1500MPa级超高强度钢、耐热钢和耐蚀钢为研究对象。
1.1.2 新一代钢铁材料(超级钢)的主要特征
新一代钢铁材料的主要特征是:在充分考虑经济性的条件下,钢材具有高洁净度、超细晶粒、高均匀度的特征,强度比常用钢材提高1倍,钢材使用寿命增加1倍。
(1)超细晶
钢只有获得超细晶组织才能使强度翻倍并具良好的强韧性配合。在众多强化方式(如固溶强化、第二相强化、位错强化等)中,细晶强化是唯一可使屈服强度ReL(σS)大幅度提高的同时韧性提高或不降低的强韧化途径。正如Petch公式所表达:
ReL(σS)=Ri(σⅰ)+Kd-1/2;TK=a-bd-1/2。
式中,Ri(σⅰ)为F晶格摩擦力;K、a、b均为常数;d为晶粒直径;TK为韧脆转变温度。超细晶理论和技术是发展超级钢的理论基础和关键技术,晶粒尺寸应在0.1~10μm之间。超细晶是新一代钢铁结构材料的核心。
(2)高洁净度
洁净度是指钢材允许的杂质含量和夹杂物形态能满足使用要求。由于钢的强度翻番,材料在使用时承受更大应力,使裂纹形成和扩展的敏感性增加。新型材料应具有更高的洁净度,但并非洁净度越高越好,而是达到能满足使用要求所需洁净度,称为“经济洁净度”。钢中S、P、O、H、N等杂质元素的总含量应<0.008%;另外是严格控制钢中夹杂物的数量、成分、尺寸、形态和分布。
(3)高均匀性
高均匀性系指钢中化学成分、组织和性能的高度均匀。要尽可能地减少钢在凝固过程中的偏析和争取获得全等轴晶粒。钢液凝固过程中,由于传热规律造成顺序凝固,带来低熔点元素的宏观偏析,形成了难以克服的中心偏析。为改善钢的均匀性,在凝固过程中应尽可能阻止柱状晶的发展,目标是在性能要求高的钢的铸坯中争取基本为全等轴晶。在杂质总量不变情况下,提高均匀性相当于提高洁净度。
其中核心技术是超细晶。钢的理论强度可高于8000MPa,而现在大量应用的碳素钢的强度仅200MPa,低合金钢只有400MPa,合金结构钢也只有800MPa。因此在已有科研成果基础上,进一步探索提高钢材强度和使用寿命的规律,把钢材强度成倍提高,在技术上是可行的。在钢的化学成分-工艺-组织-性能的关系中,强调了组织的主导地位,即其超细的微观组织表现出优异的综合性能。
生产中常见的标准晶粒度等级为8级,其中1~3级为粗晶(d=250~125μm),4~6级为中等晶粒(d=88~44μm),7~8级为细晶(d=31~22μm)。目前还没有一个被广泛接受的标准,对超细晶的尺寸给出确切的定义。有人建议把晶粒尺寸为3~10μm的热轧带钢称为细晶;1~3μm称为超细晶粒;0.1~1μm称为微细晶粒;而把晶粒尺寸在0.1μm以下称为纳米晶粒;10μm以上即为普通晶粒。
1.1.3 超级钢研发的两个关键——“微合金化”与“新型TMCP”
(1)话说微合金化与合金化
①微合金化与微合金化钢 所谓“微合金化”,即指采用现代冶金生产流程生产的高技术钢铁产品。它是在普通低碳C-Mn钢中添加微量(通常小于0.1%)的强碳(氮)化物形成元素(如Nb、V、Ti及N等)进行合金化,通过高纯洁度的冶炼工艺(脱气、脱硫及夹杂物形态控制)炼钢,在加工过程中施以控制轧制-控制冷却等新工艺,通过控制细化钢的晶粒和碳(氮)化物沉淀强化的物理冶金过程,在热轧状态下获得高强、高韧、高可焊接性、良好的成型性能等最佳力学性能配合的工程结构材料。
微合金化钢是采用现代冶金生产出的高技术含量、高附加值的产品,是国民经济建设中用量最大、用途最广的钢铁材料。微合金化钢的强度高、韧性好,可为用户节能节材而降低成本。纵观工业发达国家,发展工业走的就是微合金化钢的道路。在我国,许多企业都把发展微合金化钢作为企业钢材品种结构调整的主要内容和首要工作来抓。微合金化的钢材的研究和开发,已为国内许多钢铁企业带来生机,带来了市场竞争力的提高和更多的经济效益。
我国的钢铁工业要想赶超世界先进水平,只有坚定不移地走微合金化钢的道路。
②微合金化高强度低合金钢与普通高强度低合金钢的不同
a.基本概念的不同 普通高强度低合金钢是指在碳素结构钢(wC<0.2%)基础上,加入少量合金元素(一般合金元素总量wMe<3%)而发展起来的、具有较高强度的工程结构用钢。其化学成分特点是低碳,随钢中碳含量增加,钢的强度会增加但塑性降低;其主加合金元素为Mn,固溶强化、降低相变温度而细化珠光体和铁素体的作用,同时还可增加基体中珠光体数量,使钢的强度增加;辅加合金元素是Al、V、Ti、Nb等,起到细化晶粒、弥散强化的作用,其可一种加入,也可两种及以上同时加入。
微合金化高强度低合金钢中,晶粒细化强化仍是最重要的强化方式,微合金碳氮化物的沉淀硬化也是重要的强化方式,Mn的固溶强化也是普遍采用的强韧化方式;其成分特点是低碳、高锰并加入微量合金元素V、Ti、Nb、Zr、Cr、Ni、Mo及RE元素等,常用碳含量为0.12%~0.14%,甚至降至0.03%~0.05%,降低碳含量主要是从保证塑性、韧性和可焊性等方面考虑,微量合金元素复合(0.01%~0.1%之间)加入对钢的组织、性能的影响主要表现在:改变钢的相变温度、相变时间,从而影响相变产物的组织和性能;细晶强化;沉淀强化;改变钢中夹杂物的形态、大小、数量和分布;可严格控制P的体积分数,从而获得少珠光体钢、无珠光体钢(如针状铁素体)乃至无间隙固溶钢等新型微合金化钢种。
b.积极引入冶炼新技术,控制夹杂物形态,提高冶金质量 在微合金化高强度低合金钢中,采用的是现代冶金生产流程生产的高技术钢铁产品,通过高纯度的冶炼工艺(脱气、脱硫及夹杂物控制等)炼钢,如广泛采用的氧气炼钢使钢中氮量降低,再加上用铝脱氧并固定氮,形成AlN,对细化钢的晶粒,减少应变时效,起了良好作用。用铝脱氧,还保证了微合金化元素钛、铌、钒的收得率。
钢中夹杂物最理想的形态是呈球状,最坏的是共晶体的棒状物。往钢中加入钙,可改变硫化物与氧化物的形态,并可降低钢中夹杂物含量。加入RE元素可强烈降低氧和硫在钢液中的溶解度,硫化物、氧化物夹杂在凝固前可上浮,因而使钢去硫,并强化了硫化物。
由于炉外冶炼新技术的发展,如钢液真空处理、钢包精练等,能很好地脱气和脱硫,生产高质量的纯净钢。
c.多元、复合、微合金化必须与新型的控制轧制与控制冷却相结合,才能发挥其强韧化作用 即多元、复合微合金化的成分特点,必须在新型控制轧制、控制冷却状态下才能获得高强度、高韧性、高可焊性、良好的成形性能等最佳力学性能配合的微合金化高强度低合金钢。
(2)新一代TMCP与传统TMCP究竟有何不同?
TMCP(Thermal Mechanical Control Processing),热机械处理工艺即控制轧制和控制冷却技术,其目标是实现晶粒细化和细晶强化。
所谓控制轧制,是对奥氏体硬化状态的控制,即通过变形在奥氏体中积累大量的能量,在轧制过程中获得处于硬化状态的奥氏体,为后续的相变过程中实现晶粒细化做准备。硬化的奥氏体内存在大量“缺陷”,例如变形带、位错、孪晶等,它们是相变时铁素体形核的核心。这种“缺陷”越多,则铁素体的形核率越高,得到的铁素体晶粒越细。控制轧制的基本手段是“低温大压下”和添加微合金元素。所谓“低温”是在接近相变点的温度进行变形,由于变形温度低,可抑制奥氏体的再结晶,保持其硬化状态;“大压下”是指施加超出常规的大压下量,这样可增加奥氏体内部储存的变形能,提高硬化奥氏体程度;增加微合金元素,例如Nb,是为提高奥氏体的再结晶温度,使奥氏体在较高温度即处于未再结晶区,因而可增大奥氏体在未再结晶区的变形量,实现奥氏体的硬化。控制冷却的核心思想,是对处于硬化状态奥氏体相变过程进行控制,以进一步细化铁素体晶粒,甚至通过相变强化得到贝氏体等强化相,进一步改善材料的性能(如图1-1所示)。然而,目前控制冷却上存在的主要问题是高冷却速率下材料冷却不均而发生较大残余应力、甚至翘曲的问题;另外,微合金元素的加入甚至合金元素的加入,会大幅度提高材料的碳当量,这又会恶化材料的焊接性能等。从节能环保、低成本、可循环等方面考虑,科技工作者研发了以超快冷技术为核心的新一代TMCP技术。

图1-1 控制轧制和控制冷却技术示意
如图1-2所示,与传统的低温大压下TMCP相比,新一代TMCP在高温区进行大压下后,进行快冷,而后控制冷却路径,实现减量化轧制以及性能的多样化控制。新一代TMCP的中心思想:在奥氏体区间,趁热打铁,在适于变形的温度区间完成连续大变形和应变积累,得到硬化的奥氏体;轧后立即进行超快冷(对3mm厚钢板的冷却速度可达400K/s以上),使轧件迅速通过奥氏体相区,保持轧件奥氏体硬化状态;在奥氏体向铁素体相变的动态相变点终止冷却;后续依照材料组织和性能的需要进行冷却路径的控制(图1-2)。

图1-2 新一代TMCP与传统TMCP生产工艺的比较
新一代TMCP技术要点:在现代连轧过程提供加工硬化奥氏体的基础上,以超快速冷却为核心,对轧后硬化奥氏体进行超快速冷却,并在动态相变点终止冷却,随后进行冷却路径控制。利用这项技术可获得具有优良性能、节省资源和能源、利于循环利用的钢铁材料。
经过人类不懈地努力和创造,在钢铁材料科技上取得巨大进步。先进的冶金生产工艺技术(如铁水脱硫、超高功率电炉冶炼、炉外精炼、连铸、控轧控冷、微合金化等)又为钢铁材料的设计和生产提供了技术基础。而计算机等技术发展也为钢铁材料设计和生产提供了先进的控制手段。纵观钢铁材料的发展史,人们不难得出一个结论:根据当前的理论和技术发展,钢铁材料本身在21世纪还会发生重要变革,最终将会导致钢铁材料的性能显著提高,并将对整个社会发展起到巨大的推动作用。
1.1.4 新一代钢铁材料(超级钢)在我国的研发
微合金化(指添加量很少,一般不超过0.2%,有时甚至低于0.001%,即能对钢的某一性能或某些性能产生显著影响的合金元素)与TMCP技术相结合,发展了高强高韧钢,成为钢铁材料近30年最活跃的领域。现行的TMCP技术是将含Nb、V、Ti等微量元素的低碳钢,在高温奥氏体再结晶区逐级变形,反复再结晶细化奥氏体晶粒,随后控制冷却导致铁素体晶粒细化;或者在奥氏体未再结晶区,获得热变形奥氏体,增加晶内形变带等相变形核的部位,再结合轧后控冷,促进铁素体晶粒细化,可将铁素体晶粒细化至10μm以内。为获得超细晶组织、提高钢的强韧性,对不同类型的钢研究开发了相应的理论和控制技术。
(1)超细晶铁素体-珠光体钢
通过形变诱导(强化)铁素体相变和铁素体动态再结晶细化晶粒,提高强韧性。
①形变诱导铁素体相变 对低碳钢或低(微)合金钢在较低温度(靠近相变点A3)以较大的积累变形量和较高的应变速率进行热变形时,其变形能不能完全释放,使系统的自由能变化,成为相变驱动力,在形变过程中诱发奥氏体→铁素体相变。该相变以形核不饱和机制进行,使晶粒细化,称为形变诱导铁素体相变(DIFT)。
②形变强化铁素体相变 对低碳钢或低(微)合金钢的过冷奥氏体(在A3温度以下)以与DIFT其他条件相同的情况下进行变形时,其相变驱动力进一步增加,形成的铁素体晶粒更细,称作形变强化强化相变(DEFT)。
③低碳碳素钢的奥氏体形态 为产生形变诱导(强化)铁素体相变,必须控制奥氏体的组织形态。形变使奥氏体呈“薄饼状”,晶内产生大量晶体缺陷,将部分形变能储存为相变驱动力。研究表明,对低碳钢随形变速率的提高和变形温度的降低可使奥氏体只发生回复而不发生再结晶,即可通过未再结晶控轧和DIFT细化铁素体晶粒。
④铁素体动态再结晶 奥氏体转变为铁素体后,由于第二相渗碳体的存在,在与第二相交界处往往受不均匀变形,具较高畸变能,成为铁素体动态再结晶形核的有利部位。铁素体动态再结晶使晶粒进一步细化。
上述理论是对传统TMCP理论的发展。原TMCP的奥氏体→铁素体相变发生在形变后的冷却过程中,而新型TMCP是发生在形变过程中。
(2)超细组织低(超低)碳贝氏体(B)钢
为了开发强度高于600MPa的经济型低合金钢,人们研究了低(超低)碳贝氏体钢的组织超细化理论与控制技术。通过研究发展了TMCP技术,在工艺中增加了一个弛豫控制阶段。在此阶段,在变形奥氏体中实现晶体缺陷的重新排列、组合,让微合金元素的析出质点在特定部位析出,分割原奥氏体晶粒,从而控制随后冷却时的贝氏体相变在已被分割的小空间内进行,实现组织超细化。该技术称作弛豫-析出-控制技术(RPC)。
①位错胞状结构(亚晶)的限制作用 钢变形后,位错密度很高。弛豫时,位错重新排列,形成位错墙,进而出现胞状结构,较完整的亚晶,将原奥氏体晶粒分割为更细小的亚晶。
②微细析出相的钉扎作用 钢中含有Nb、V、Ti、B等微量元素,在形变和弛豫过程,通过形变诱导析出细微析出相。析出相对位错亚结构的钉扎作用是实现组织超细化的另一因素。
③针状铁素体的空间分割作用 形变、弛豫后在冷却过程中,在较高温度首先形成针状铁素体。针状铁素体将原奥氏体晶粒分割为更细小的空间。
RPC技术使中温转变组织细化的机制是:位错亚结构的限制作用;微细析出质点的钉扎作用;针状铁素体的分割作用。三者结合使贝氏体组织超细化。这类钢具有高强度、高韧性、低韧脆转变温度(TK)和良好的焊接性。
(3)无碳化物B/M复相钢
合金结构钢的强度高于1200MPa后,其延迟断裂抗力低,韧性不足,疲劳极限分散。利用新的合金成分和微观组织设计,使钢形成无碳化物贝氏体/马氏体+膜状残余奥氏体。用无碳化物贝氏体改善钢的韧性,用膜状残余奥氏体提高钢的抗延迟断裂性能。此类钢有如下特点。
①采用低碳Mn-Si-Cr合金系,保证钢有一定淬透性,在空冷条件下,直径小于20mm的棒材可获得无碳化物贝氏体、少量马氏体及膜状残余奥氏体,具有较高韧性。
②Si作为非碳化物形成元素,在发生贝氏体相变时阻止碳化物的析出。冷却过程中,在贝氏体和马氏体板条束界、板条界形成残余奥氏体膜。膜状残余奥氏体使疲劳裂纹尖端钝化,提高疲劳性能。奥氏体的析氢能力比铁素体高1个数量级,明显提高钢的抗延迟断裂性能。
③该钢奥氏体化后自高温冷却时,在奥氏体晶粒内先形成无碳化物贝氏体,分割原奥氏体晶粒,使随后形成的马氏体细化,提高钢的强韧性。
④含Si合金钢有较高的回火抗力,适当提高回火温度使钢具有良好的综合性能。
(4)耐延迟断裂高强度M钢
为改善高强度合金结构钢的耐延迟断裂性能,根据强化晶界、细化晶粒、控制氢陷阱的技术思路,在42CrMo钢基础上设计了中碳Cr-Mo-V-Nb钢,其有如下特点。
①强化晶界 钢中加入Mo和V,回火时析出Mo2C、VC,产生二次硬化,提高回火温度而不降低钢的强度。低温回火时,碳化物沿奥氏体晶界呈连续薄膜状析出。氢在晶界富集,导致高的延迟断裂敏感性。高温回火时晶界的碳化物聚集,呈不连续粒状;同时晶内的碳化物析出增加,成为氢陷阱。因此,强化晶界,提高钢的耐延迟断裂性能。P、S在晶界偏聚,降低钢的晶界结合力,可提高钢的洁净度以降低其危害。Mo可降低P在晶界的偏聚,强化晶界。
②细化晶粒 Nb和V的析出相钉扎晶界,阻止钢淬火加热时奥氏体晶粒长大,细化晶粒。增加晶界面积,相对提高钢洁净度,净化晶界,提高钢的强韧性和耐延迟断裂性能。
③控制氢陷阱 随回火温度的提高,晶内析出碳化物,成为氢陷阱,把氢捕集在晶内的氢陷阱中,提高钢的耐延迟断裂性能。
总之,“高性能”是钢铁材料研发的永恒主题。对于不同的钢类,高性能的含义不尽相同,所采用的基体组织类型也不同(如表1-2所示)。控制冶炼和凝固过程可得到高洁净度和高均匀度的钢坯(锭),通过加工过程中的相变、再结晶、固溶和析出等现象控制可获得期待的高均匀度和精细组织,从而达到高性能的目标。所以,钢铁材料的生产工艺技术进步、物理金属学和力学金属学的发展促进了钢铁材料的发展,钢铁材料是不断发展的新材料。现在使用的数千种钢铁材料都是在近代液态钢铁冶金技术出现以后,经过人们不断研发而产生的。通过持续的技术研发活动,钢铁材料已经和必将不断发展和更新,形成了以“高性能、低成本、易加工、高精度、绿色化”为特征的先进钢铁材料。
表1-2 各钢类的基体组织与性能特征
