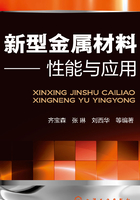
1.2 新型工程结构用钢及其发展
工程结构用钢是指专门用来制造各种工程结构的一大类钢种,它广泛用于国防、化工、石油、电力、车辆、造船、建筑等领域,如制造桥梁、船体、油井或矿井架、钢轨、高压容器、管道和建筑钢结构等工程结构件,故又称为工程构件用钢或简称构件钢。在钢总产量中工程结构用钢约占90%,其成本低、用量大,通常在热轧空冷状态下使用。
1.2.1 工程结构用钢的工作条件与性能要求
一般说来,工程结构件的工作特点是不作相对运动,承受长期静载荷,有一定使用温度要求,如有的(如锅炉)使用温度可达250℃以上,有的则在寒冷(-40~-30℃)条件下工作、长期承受低温作用;通常在野外(如桥梁)或海水(如船舶)条件下使用,承受大气或海水的侵蚀作用。此类工程构件常见的失效形式主要有变形、断裂以及遭受腐蚀等。因此构件用钢应满足以下使用性能要求。
(1)良好的加工工艺性能
通常工程构件的主要生产过程有冷塑性变形和焊接两个方面。所以工程结构用钢必须相应地具有良好的冷(热)成形工艺性和可焊性。在构件用钢的设计和选材上首先需要满足这两方面的要求。
(2)高强度与良好塑韧性
为使构件在长期静载下结构稳定,不易产生弹性变形、更不允许产生塑性变形与断裂,要求工程结构用钢要有大的弹性模量,以保证刚度;高的强度,以减轻结构自重、节约钢材和减少能耗;高的塑韧性,以免断裂和塑性变形;同时还应具有低的韧脆转变温度TK。
(3)良好的耐大气和海水腐蚀性
保证工程构件在大气或海水等腐蚀性工况下长期稳定工作。
总之,工程结构用钢应在保证工艺性能的前提下,达到其高强度高韧性等力学性能。这是与其他钢种不同之处。同时又要有低的成本。据此可将其分为三类,即碳素结构钢、低合金结构钢和微合金化低碳高强度钢。
1.2.2 铁素体-珠光体工程结构钢
由于此类钢服役时的显微组织是铁素体-珠光体,故称为铁素体-珠光体钢。它是工程结构钢中最主要、用量最大的一类钢,其组织系由片层状的珠光体+多边形铁素体组成,珠光体占10%~25%、铁素体占75%~90%,包括碳素结构钢、高强度低合金钢和微合金化高强度低合金钢。
(1)碳素结构钢与高性能细晶碳素结构钢
①碳素工程结构钢 这类钢大部分用作钢结构,少量用作机器零件。由于其易于冶炼、工艺性能好、价格低廉,虽含有较多有害杂质元素和非金属夹杂物,但在力学性能上一般能满足普通工程构件及机器零件的要求,所以工程上用量很大,约占钢总产量的70%~80%。它通常均轧制成钢板或各种型材供应,一般不经热处理强化。根据国标GB/T700—2006,将普碳钢分为Q195、Q215、Q235、Q255、Q275五类。
碳素工程结构钢大部分以热轧成品供货,少部分以冷轧成品供货,如冷冲压薄板钢、冷拔钢管、冷拉钢丝等。冷冲压薄板钢主要用于制造厚度在4mm以下的各种冷冲压构件,如车身、驾驶室、各种仪器及机器的外壳等。用于冷轧的钢有08F、08Al、06Ti等,冷轧成板后经再结晶退火,最后施以1%~3%平整变形,以消除上、下屈服点,保证深冲要求。
②高性能的细晶碳素结构 钢随着经济建设的持续快速发展,对钢材的需求量猛增,各行业都要求开发高强度、长寿命的钢材。我国于2001年启动了973计划“500MPa碳素钢先进工业化制造技术”课题,研究的主要目标是在保证有良好塑韧性基础上,使原钢材强度提高1倍,其技术思路是以细化钢材的晶粒和组织为核心,同时提高钢的洁净度,并改善钢的均匀性。确定在现有工业生产条件下生产出以C、Mn为主要成分的500MPa级细晶钢,逐步代替该强度级别的低合金高强度钢。用Q235普碳钢,通过较低温度的TMCP技术,利用形变诱导铁素体相变机制使铁素体晶粒细化至3~5μm,强度提高1倍以上。现已在300~500MPa级系列细晶钢生产中获得实际应用。其用于生产卡车、轿车、农用车等的底盘纵梁、横梁、车桥等冲压件,使用效果良好,已实现了工业化生产。又如,首钢生产的Ⅲ级螺纹钢筋,已成功应用于国家大剧院、西直门交通枢纽等国家重点工程建设。细晶粒碳素结构钢在建筑、造船、桥梁、容器、工程机械等方面,有着广阔的应用前景。
(2)低合金高强度钢与微合金化低碳高强度钢
①低合金高强度钢(普低钢,HSLA钢) 钢铁材料80%以上是低碳钢。在低碳钢中,利用添加少量合金元素(wMe总量<5%,一般<3%)使钢在轧制或正火状态下的屈服强度超过275MPa的一类低合金钢,称为低合金高强度钢(简称普低钢,亦称HSLA钢)。
低合金高强度钢是为适应大型工程结构(如大型桥梁、大型压力容器及船舶等)减轻结构重量,提高使用的可靠性及节材的需要而发展起来的。这是一类高效节能、用途广泛、用量很大的一类钢。其强度尤其是屈服强度大大高于碳含量相同的普碳钢。如最常用的普碳钢Q235与低合金高强度钢Q345(16Mn,其碳含量相同)相比(如表1-3所示)。
表1-3 Q235与Q345(16Mn)钢的强度比较

a.化学成分特点
低碳 碳的质量分数一般<0.2%,主要是为获得较好的塑韧性,焊接性能。随钢中碳含量增加,钢的强度会增加,但却使其塑韧性下降、成形困难,而且在焊接过程中易引起严重的变形、开裂。而且随碳含量增加,钢中珠光体含量也相应增加,珠光体由于有大量脆性片状渗碳体,因而有较高的TK,如含0.3%C的钢材TK在50℃左右,而含0.1%的钢材TK则降至-50℃左右。因此HSLA钢的碳含量一般限制在0.2%以下。
主加元素Mn 其固溶强化效果较好。由于Mn能降低钢的Ar1温度,降低奥氏体向珠光体转变温度范围并减缓其转变速度,因此表现出细化珠光体和铁素体的作用。晶粒细化既可使钢的屈服强度升高,又可使TK下降,有利于钢的韧性提高。但应注意Mn的含量应控制在2%以内。此外,Mn的加入可使铁碳相图中的S点左移,基体中珠光体数量增多,因而在相同的碳含量下,随铁素体量减少,珠光体增多,使钢的强度不断提高。
辅加元素Al、V、Ti、Nb及Cu、P、Cr、Ni、RE等 加入Al形成AlN的细小质点,细化晶粒,既可提高强度,又可降低TK。由于Nb、V、Ti在钢中能形成细小弥散的碳化物、氮化物和碳氮化物起着阻止奥氏体晶粒长大同时又具有很强的析出强化作用。加入一定量的Cu和P,Cu元素沉积在钢表面,具有正电位,成为附加阴极,使钢在很小的阳极电流下达到钝化状态。P在钢中可起到固溶强化的作用,也可提高耐蚀性能。Ni和Cr都能促进钢的钝化,减少电化学腐蚀。加入微量RE,可脱硫去气,净化钢材,并改善夹杂物的形态与分布,从而改善钢的力学性能和工艺性能。
总之,HSLA钢合金化的思路是:低碳,以Mn为基础,适当加入Al、V、Ti、Nb、Cu、P、Cr、Ni、RE等元素。
b.典型牌号简介 其典型牌号Q345(16Mn)和Q420(15MnVN),一般采用正火作为最终热处理状态。
Q345(16Mn)钢 属于屈服点为345MPa级,有较高的强度,良好的塑性和低温韧性以及焊接性,是我国这类钢中产量最多、用量极广的钢种。其中,Mn(1.2%~1.6%)起着固溶强化的作用,锰降低A3温度,增大钢的奥氏体过冷能力,细化F晶粒,降低钢的冷脆性和TK温度。16Mn钢广泛用于生产钢筋和建筑钢结构,也应用于多种专用钢,如主跨度160m的桥梁、容器、造船等用钢(而Q235建造的主跨度128m的武汉长江大桥)。
Q420(15MnVN)钢 屈服点则属于440MPa级别,钢中加入微量V起细化晶粒和沉淀强化作用,微量N(≤0.022%)以形成稳定的VN,比VC更有效地起细化晶粒和沉淀强化作用。它是为适应建筑和桥梁工程而开发的钢种,如主跨度216m的九江长江大桥。
多年来低合金结构钢发展迅速,在生产和科研上取得一系列重要成果,相继开发了一系列新型工程结构用钢。
②微合金化低碳高强度钢
a.成分与强韧化特点 其成分特点:低碳,高Mn并加入微量合金元素V、Ti、Nb、Zr、Cr、Ni、Mo及RE等。常用碳含量范围wC=0.12%~0.14%,甚至降至wC=0.03%~0.05%。其另一个特点是微量合金元素的复合加入,复合量范围一般控制在0.01%~0.1%之间(质量分数)。微量合金元素对钢的组织性能影响如下:
抑制奥氏体形变再结晶 在热加工过程中,通过应变诱导析出Nb、Ti、V的氮化物,使其沉淀在晶界、亚晶界和位错上,起钉扎作用,有效地阻止奥氏体再结晶的晶界和位错运动,抑制再结晶过程的进行。在高温区,Nb以固溶原子对晶界迁移的拖拽作用为主;在低温奥氏体区,以应变诱导析出的Nb(C,N)粒子的钉扎晶界作用为主。Nb、Ti、V对形变再结晶温度的影响如图1-3所示。Nb在阻止形变奥氏体的回复和再结晶方面作用最强,Ti次之,V较弱。
细晶强化(阻止奥氏体晶粒长大) 在锻造和轧制过程中,一方面加热时奥氏体晶粒会自发长大;另一方面,每一道次再结晶后晶粒就会长大。通过加Nb、Ti形成了Nb(C,N)或TiN(它们在高温下非常稳定),其弥散分布对控制高温下的晶粒长大有强烈的抑制作用。其中,微量Nb(wNb<0.06%)形成的Nb(C,N)在1250℃时也未完全溶于奥氏体,而在1150℃以下又有部分Nb重新以Nb(C,N)析出,因而阻止奥氏体晶粒长大作用的温度可达1150℃。微量Ti(wTi<0.02%)以TiN形式从高温固态钢中析出,呈弥散分布,对阻止奥氏体晶粒长大很有效。Nb、Ti、V对正火态的低合金钢的晶粒度的影响如图1-4所示,Nb最有效,Ti次之,V则基本上不起细化晶粒的作用。

图1-3 Nb、Ti和V对形变再结晶临界温度的影响

图1-4 Nb、Ti和V对正火态低合金钢晶粒度的影响
沉淀强化 Nb和Ti的碳化物和氮化物有足够低的固溶度和高的稳定性,V只有在氮化物中才起作用。一般微合金化钢中的沉淀强化作用主要是低温下析出的Nb(C,N)和VC。微合金元素Nb、Ti、V对钢的屈服强度的影响如图1-5所示。当wNb≤0.04%时,细化晶粒造成屈服强度的增量ΔσG>沉淀强化引起的增量Δσph;wNb≥0.04%时,Δσph增量大大增加,而ΔσG保持不变。V引起沉淀强化使钢的屈服强度增量Δσph最显著,而Ti的作用处于Nb和V之间。

图1-5 微合金元素对钢屈服强度的影响
σG—晶粒细化的贡献;σph—沉淀强化的贡献
改变钢的显微组织 Nb、Ti、V等合金的碳化物和氮化物随奥氏体温度升高有一定的溶解量,如Nb(C,N)在1150℃时溶于奥氏体的Nb约为0.03%,而V(C,N)更易溶于奥氏体。在轧制加热时,溶于奥氏体的微合金元素提高了过冷奥氏体的稳定性,降低了发生先共析铁素体和珠光体的温度范围,低温下形成的先共析铁素体和珠光体组织更细小,并使相间沉淀Nb(C,N)的粒子更细小。
必须指出,上述方法均采用控制轧制、控制冷却和控制沉淀,因为它是微合金化低碳高强度钢获得高强韧性的基础。
b.冶金工艺特点。
积极引入冶炼新技术 控制夹杂物形态,提高冶金质量。钢中夹杂物最理想的形态是呈球状,最坏的是共晶体的棒状物。由于炉外冶炼新技术的发展,如钢液真空处理、钢包精炼等,能很好地脱气和脱硫,生产高质量的纯净钢。
采用先进的控制轧制与控制冷却技术 微合金化必须与控制轧制、控制冷却相结合,才能发挥其强韧化作用(见图1-6)。首先,在高温再结晶区的变形,使粗大奥氏体晶粒经多道次变形和再结晶而得到细化,但此时由奥氏体转变而来的铁素体晶粒仍较粗大;继而在较低温度下的未再结晶区的变形,其发生在紧靠Ar3以上的温度范围,此时在伸长而未再结晶的奥氏体内形成变形带,铁素体在变形带和奥氏体晶界上形核,从而形成细小晶粒的铁素体组织;然后在低温下(奥氏体-铁素体)两相区的变形,此时铁素体也发生变形,产生位错亚结构,在随后的冷却过程中未再结晶的奥氏体转变为等轴的细小铁素体晶粒,铁素体中的亚结构得以保留。应说明,控制冷却是在奥氏体相变的温度区间进行某种程度的快速冷却,它使相变组织比单纯控制轧制更加微细化,获得更高的强度。

图1-6 控轧3阶段及每阶段变形与显微组织的变化
c.应用特点。微合金化低合金高强度钢汽车零部件可减轻车身重量、减少油耗。目前,宝钢、武钢、攀钢、本钢生产的超级钢板已供应一汽、东风汽车及其他汽车厂。宝钢生产的400MPa超级钢用于一汽集团卡车底盘发动机前置横梁,各项性能指标全部满足要求,且吨钢成本较原来可节省200~300元。卡车纵梁是关键承重件,500MPa级超级钢在这方面的应用经济效益更加明显。目前我国采用超级钢生产的汽车梁已经装在10多万辆卡车上。
在现有设备条件下,我国科技工作者实现了将碳素钢和低碳微合金化钢的组织(铁素体,F)尺寸细化至几微米,实现了将其强度翻番的目标。例如,我国研制的超细晶普碳钢Q235钢筋的最小晶粒尺寸可以达到4μm以下,屈服强度可达460MPa以上,而正常轧制的Q235钢的屈服强度仅为235MPa。
首钢生产的超级钢筋用于国家大剧院、北京西直门交通枢纽及朝阳中央商务区,并且出口新加坡。低成本高强度的超级钢棒材将为建筑业提供有力的支撑。
(3)低合金高强度钢的发展趋势
低合金高强度钢的主要发展方向有以下几个方面。
①低碳和超低碳 随碳含量的降低,能显著提高HSLA钢韧性和改善焊接性。由于现代冶金技术的提高,使钢中的碳含量降低到<0.06%甚至<0.02%得到保证,这可显著提高钢的焊接性、韧性和成形性等。因此,低碳和超低碳是今后HSLA钢发展的一个重要方向。
②高纯净化 净化钢中的有害杂质,可改善钢的韧性和提高其综合性能。随着冶金技术的发展,铁水预处理、转炉炼钢和钢水精炼等先进技术已普遍应用,这些先进的冶炼新技术能使钢中S、P、H、O、N等杂质大大降低,显著提高了钢的纯净度,因此现代HSLA钢正逐步向高纯净化方向发展。
③微合金化 在低碳、超低碳和高纯净化基础上,HSLA钢普遍采用微合金化,微合金化技术已由单一合金元素(Nb、V、Ti等)发展到多元复合如Nb-V、Nb-Ti、V-Ti、Nb-Ti-B等,并配合先进的TMCP技术进一步提高钢的综合性能。
④采用先进的控制轧制和控制冷却(TMCP)技术 通过TMCP,可调整奥氏体的原始组织晶粒大小,使转变后的铁素体晶粒尽可能细化,从而得到尽可能高的强度和最佳的塑韧性。现代TMCP技术已从原控制终轧温度发展到奥氏体再结晶区控轧、奥氏体非再结晶区控轧和两相区控轧工艺,轧后的控制冷却工艺已有层流冷却、水幕冷却、雾化冷却和穿水冷却等。应用先进的在线TMCP工艺也是进一步提高现代HSLA钢质量的重要发展方向。
⑤超细化晶粒 通过加大轧制变形、铁素体的应变诱导析出、稍高于A3点的低温轧制和采用合适的冷却速度,可使钢的铁素体晶粒尺寸细化到微米级,可大幅度提高钢的强度,普通碳素钢的强度可由235MPa提高至400MPa,HSLA钢的屈服强度可由400MPa提高至800MPa。因此,HSLA钢的组织微细化亦是今后的发展方向。
⑥计算机控制和性能预报 随着计算材料学的进步,使得材料的发展逐步由经验走向定量化系统化。以前材料设计都是根据大量的统计结果,通过回归分析建立经验公式,然后据此组织生产和管理,这种方法精度很低,有一定局部性,一旦改变条件就不适用,因此缺乏普遍的指导意义。计算材料学是利用钢铁材料的基本冶金原理,通过计算机建立各种冶金模型,达到预测材料组织和性能的效果。近年来,物理冶金学已能准确把握钢铁材料内部产生的基本冶金现象并建立相应的冶金模型,通过预报材料的组织,就可使准确预测材料的性能成为可能。这样可大大减少实验研究工作和缩短研究时间,加速新产品的开发。目前,工业发达国家已经开发出钢的组织和性能预测系统,并成功用于热轧带钢在线生产系统。
1.2.3 低合金高强度钢的发展——低碳贝氏体钢、针状铁素体钢、马氏体钢与双相钢
具有铁素体-珠光体组织的高强度低合金钢和微合金化高强度低合金钢的屈服强度的极限,约460MPa。若要求更高强度和韧性的配合,就需考虑选择其他类型组织的低合金钢,其主要原理同样亦是在微合金钢的基础上,通过在控轧控冷后调整成分或组织,从而获得低碳贝氏体或马氏体等组织来提高工程构件用钢的强韧性。
(1)低碳贝氏体钢
低碳贝氏体型钢是通过向钢中加入能显著推迟珠光体转变而对贝氏体转变影响很小的元素(如在wMo0.5%+wB0.003%基本成分基础上,加入Mn、Cr、V等元素),从而使大截面的构件在热轧或正火后控制冷却,利用贝氏体相变强化,直接获得单一贝氏体组织。与原相同碳含量的F-P钢相比,它具有更高的强度和良好的韧性,此时钢的屈服强度可达490~780MPa。Mo和B对过冷奥氏体等温转变曲线的影响如图1-7所示,可以看出>0.3%Mo能显著推迟珠光体转变,而微量的B(0.002%)在奥氏体晶界上有偏析作用,可有效地推迟铁素体转变,但对贝氏体转变推迟较少。为进一步推迟先共析铁素体和珠光体转变,并使贝氏体转变开始点下降,获得下贝氏体组织,需再加入Mn、Cr、Ni等元素,与上贝氏体相比,下贝氏体有更高的强度和低的TK,如图1-8所示。另外,通过微合金化,充分发挥Nb、Ti、V的细化晶粒和沉淀强化的作用,低碳贝氏体钢的化学成分范围为:wC=0.10%~0.20%,wMo=0.3%~0.6%,wMn=0.6%~1.6%,wB=0.001%~0.005%,wV=0.04%~0.10%,wNi或wTi=0.01%~0.06%,并常加0.4%~0.7%的Cr。我国已成功研制出的几种低碳贝氏体钢的化学成分与力学性能如表1-4所示。

图1-7 低碳钼、钼硼钢的C开始曲线

图1-8 低碳贝氏体钢上、下贝氏体的σb与TK的关系
表1-4 我国研制的几种低碳贝氏体钢的化学成分与力学性能

14MnMoV和14MnMoVBRE钢是我国发展的低碳贝氏体钢,其屈服强度为490MPa级,用于制造容器的板材和其他钢结构。当板厚<14mm时,在热轧态即可得到贝氏体;板厚>14mm时需正火热处理方可得到贝氏体,低碳贝氏体型钢空冷后的组织通常是粒状贝氏体(即贝氏体铁素体条间存在细小的岛状马氏体),所以需高温回火以消除内应力。14MnMoVBRE钢的焊接性能不好,厚板在焊前需预热至150℃以上,单层板焊后可用工频感应加热以消除焊缝残余应力。
为进一步提高钢的室温和低温韧性,改善焊接性,又发展了超低碳B钢,其碳含量可降低至0.02%,并加入0.01%的Ti,成为Mn-Mo-Nb-Ti-B超低碳B钢。通过先进的TMCP技术,可得到高位错密度的细小B组织,其可在0℃以下进行服役。
(2)针状铁素体型钢
针状铁素体钢(AF,Acicular Ferrite)是在低合金钢的基础上,当钢中碳含量<0.06%时,添加适量的Mn、Mo、Nb等合金元素,形成一种具有高密度位错亚结构的“针状铁素体”的钢。它是为满足北方严寒条件工作的大直径石油和天然气输出管道用钢需要而发展起来的,并通过轧制以获良好强韧化效果。此类钢的显微组织是极细的低碳或超低碳的针状铁素体(属于无碳化物贝氏体)片上分布着高位错密度的细小亚结构+弥散的Nb(C,N)粒子沉淀。其通过合理的成分设计并采用先进的TMCP技术,在空冷过程中通过切变和扩散相变形成由位错列阵和位错胞组成的非等轴铁素体,可以保证得到极细的晶粒和针状铁素体片,产生更高位错密度的细小亚结构和更弥散的Nb(C,N)沉淀析出。其主要强化机制是:极细的贝氏体型铁素体晶粒或板条、高的位错密度、细小弥散分布的碳氮化物、固溶在贝氏体铁素体中的碳等间隙原子的强化和固溶在铁素体中合金元素的置换式固溶强化。
针状F型钢合金化的主要特点如下:①采用低碳或超低碳含量(wC0.04%~0.08%);②主要用Mn、Mo、Nb等进行合金化;③对V、Si、N及S含量加以适当限制。其典型成分如wC≤0.06%、wMn1.6%~2.2%、wSi0.1%~0.4%、wMo0.25%~0.40%、wNb0.02%~0.10%、wAl约0.05%、wN≤0.01%、wS≤0.02%、wP≤0.02%。针状F型钢经TMCP后可使σs达490MPa以上,TK在-100℃以下。其性能特点是:高的强韧性,良好的低温韧性和焊接性能,可用普通电弧焊焊接。因此此类钢被称为“21世纪的控轧钢”,已成功应用于寒冷地带输送石油和天然气的管线等场合。
创制针状F型钢的主要着眼点在于:通过轧制后冷却时形成非平衡针状F提供大量位错亚结构,为以后K弥散析出创造条件,并保证原板成形时有较大加工硬化效应,以防强度降低;利用Nb(C、N)为强化相,使在轧后冷却中及575~650℃时效时从F中弥散析出以造成弥散强化,可使σs提高70~140MPa,但又相应使TK提高约8~19℃,为此需采取相应补救措施;采用控制轧制细化晶粒,将终轧温度降至740~780℃,并使在900℃以下形变量达65%以上,每道轧制后用喷雾快冷,以防K从A中析出,减弱时效强化效果。
(3)积极开发低碳马氏体钢
工程机械上对运动和低温下使用的部件,要求有更高强度和良好焊接性,因而开发出低碳M钢。所谓“低碳马氏体钢”系指低碳钢或低碳合金钢以经淬火+低温回火处理后获得的低碳马氏体组织作为使用状态的钢。为使其得到好淬透性,防止发生先共析铁素体和珠光体转变,加入Mo、Nb、V、B及控制合理含量的Mn和Cr与之配合,Nb还可作细化晶粒的微合金元素起作用。常见的有BHS系列钢种。其中BHS-1钢的成分为wC0.10%,wMn1.80%,wMo0.45%,wNb0.05%。其生产工艺为锻轧后空冷或直接淬火并自回火,锻轧后空冷得B+M+F混合组织,其性能为:σ0.2828MPa,σb1049MPa,室温AK96J,可用来制造汽车的轮臂托架。若直接淬火成低碳M,性能为σ0.2935MPa,σb1197MPa,室温AK50J,-40℃下AK32J,缺口疲劳断裂大于500kHz,可制造下操纵杆。
由此看来,低碳M钢具有极高强度,好的低温韧性和超群的疲劳性能,可保证部件的高质量和安全可靠。BHS钢还用来生产车轴、转向联动节和拉杆等,也可用于冷镦、冷拔及制作高强度紧固件。另一种Mn-Si-Mo-V-Nb系低碳Mn钢,其屈服点860~1116MPa、室温AK为46~75J。低碳Mn钢具有高强度、高韧性和高疲劳强度,达到了合金调质钢经调质热处理后的性能水平,若采用锻轧后直接淬火并自回火工艺,最能发挥其潜力。
低碳马氏体钢经淬火+低温回后后,形成位错板条马氏体+板条相界残余奥氏体薄膜+板条内部自回火或低温回火析出的细小弥散的碳化物,可实现强度、韧性、塑性的最佳配合。其强化是综合了固溶强化、位错强化、细晶强化及第二相强化四种强化效果,因而强化作用十分显著。常用的低碳马氏体钢的热处理工艺和力学性能如表1-5所示。15MnVB、20SiMn2MoV、25SiMn2MoV等是我国研制的低碳马氏体钢,在生产上已获得广泛应用。低碳马氏体钢在矿山、汽车、石油、机车车辆、农业机械等制造工业得到广泛的应用,在提高产品质量、减轻零件重量及降低成本等方面均有良好效果。
表1-5 一些常用的低碳马氏体钢的热处理工艺和力学性能

(4)发展低碳索氏体型钢
采用低碳低合金钢淬火获得低碳马氏体,然后进行高温回火得到低碳回火索氏体组织,使钢材具有更高的强度和良好的焊接性。为使钢得到好的淬透性和回火稳定性,防止先共析铁素体和珠光体转变,此类钢典型合金成分是美国的T-1型钢,规定成分为wC0.1%~0.2%,wMn0.6%~1.0%,wSi0.15%~0.35%,wNi0.7%~1.0%,wCr0.4%~0.8%,wMo0.4%~0.6%,wV0.04%,wCu0.15%~0.5%,wB0.002%~0.006%。T-1型钢板在不同状态下的力学性能如表1-6所示。
表1-6 T-1型钢板在不同状态下的力学性能

低碳索氏体型钢在重载车辆、桥梁、水轮机及舰艇等方面得到应用。生产这种钢的主要困难是钢材在淬火时容易变形,所以钢板和型钢必须在淬火机上进行淬火,而截面厚的钢板不易完全淬透。
(5)发展双相钢
由于传统的高强度低合金钢对汽车压力加工件来说,没有具备足够的冷成形性,因而需要改善传统钢强度-成形性的综合性能以满足汽车冲压成形件的要求。而双相钢是通过对过冷奥氏体相变的有效控制以得到20%~30%马氏体和80%~70%铁素体组织的钢种,其组织特征为马氏体呈小岛状分布在铁素体基体上。
双相钢的性能特点:①低屈服强度,一般应<350MPa;②钢的应力-应变曲线是光滑连续的,无屈服平台;③高的均匀伸长率和总伸长率;④高的加工硬化指数及高的塑性应变比。化学成分是获得双相钢组织的技术关键,C、Si、Mn、Mo等合金元素对钢双相组织的控制、钢板强度、塑性等影响较大。另外,生产工艺对第二相组织的相组成、性质和数量也有影响。根据生产工艺,双相钢可分为热轧双相钢和退火双相钢两大类,两者有不同的合金化方案。
热轧双相钢,是指在热轧状态下通过控制冷却得到铁素体+马氏体的双相组织。要求钢在热轧后从奥氏体状态冷却时,首先出现适量的多边形铁素体,其体积分数为70%~80%,然后未转变的奥氏体有足够的稳定性,避免产生珠光体和贝氏体,冷却后转变为马氏体。这就要求从合金元素含量和风冷速度上来控制。其生产方式主要有两种:①Si-Mn-Cr-Mo合金化系,采用普通的热轧工艺进行生产;②Si-Mn-Cr系,1150~1250℃加热,采用TMCP、870~925℃终轧,空冷至低温635~455℃时卷取。一般热轧冲压双相钢的化学成分为:wC=0.04%~0.10%,wMn=0.8%~1.8%,wSi=0.9%~1.5%,wMo=0.3%~0.4%,wCr=0.4%~0.6%以及微合金元素V等。加入合金元素Si和极低C是为提高钢的临界点A3,促使形成所要求含量的多边形先共析铁素体;加入Mn、Mo、Cr是为防止卷取时剩余奥氏体转变为主个体和贝氏体或最终冷至低温转变为马氏体。
退火双相钢又称热处理双相钢,典型成分为wC0.055%-wMn1.4%-wSi1.2%钢和wC0.1%-wMn1.5%-wCr0.8%钢。其工艺是在铁素体和奥氏体两相区进行精轧后退火,然后空冷或快冷,即将型材急冷至Ms点以下卷取,得到铁素体+马氏体组织。为控制硫化物形态,可加入RE元素。当钢长时间在铁素体和奥氏体两相区退火时,合金元素将在奥氏体和铁素体之间重新分配,奥氏体形成元素如C、Mn等将富集于奥氏体,提高了奥氏体在过冷条件下的稳定性,抑制了珠光体转变,在空冷条件下即能转变成马氏体,这时要控制退火温度,以控制奥氏体量和奥氏体中合金元素的浓度及其稳定性。
双相钢首先是为了适应汽车用薄板冲压成型时保持表面光洁,无吕德斯带,并在少量变形后就提高了强度的需要;也用于冷镦钢、冷拔钢、Ⅳ级螺纹钢筋无缝钢管、冷拉钢丝、冷轧钢带等产品。如用于高速线材轧制生产散卷控制冷却得到的双相钢丝用09Mn2Si、07Mn2SiV钢;热轧双相冷镦钢棒用08SiMn2钢;薄壁双相无缝钢管用07MnSi钢等。