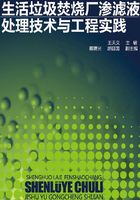
3.3 厌氧生物处理的反应器类型
厌氧生物处理技术在污水处理中的应用已有一个多世纪,其中厌氧反应器是该技术发展最快的领域之一。厌氧反应器高效、稳定运行的关键是能够保持足够多的生物量并且能够促进污水与活性污泥的充分接触。下面介绍具有代表性的不同类型的厌氧反应器:AF、UASB、UBF、EGSB、IC。
3.3.1 厌氧生物滤池(AF)
厌氧生物滤池(Anaerobic Filter,AF)也称厌氧滤池,是国际上使用最早的废水厌氧生物处理构筑物之一。20世纪60年代末,美国McCarty和Young在Coulter等研究的基础上,发展并确立厌氧生物滤池作为厌氧生物膜法的代表性工艺之一,并成为第一个高效厌氧反应器。厌氧生物滤池的工作过程为:有机废水通过挂有生物膜的滤料时,废水中的有机物扩散到生物膜表面,并被生物膜中的微生物降解转化为沼气;净化后的废水通过排水设备排至池外,沼气则被收集利用。
据Bonastre和Paris报道,至1989年至少有30多个厌氧滤池用于工业规模的废水处理,其容积负荷通常在5~12 kg COD/(m3·d)。厌氧滤池适用于低分子量的溶解性废水处理,悬浮物较高的废水易于引发堵塞。
(1)工艺构造
按水流方向,厌氧生物滤池可分为升流式厌氧生物滤池和降流式厌氧生物滤池两类,近年来又出现了一种升流式混合型厌氧反应器,实际上是厌氧生物滤池的一种变形。这三种不同类型的厌氧生物滤池如图3.2所示。无论哪种类型的厌氧生物滤池,其构造类似于一般的好氧生物滤池,包括池体、滤料、布水设备以及排水、排泥设备等;也可以按功能不同将滤池分为布水区、反应区(滤料区)、出水区、集气区四部分。

图3.2 厌氧生物滤池的三种类型
厌氧生物滤池的中心构造是滤料,滤料的形态、性质及其装填方式对滤池的净化效果及其运行有着重要的影响。滤料要求质地坚固、耐腐蚀;滤料是微生物的固着部位,进而形成生物膜,因此需要具有大的比表面积,同时,又要有一定的空隙率以便废水均匀扩散。滤料的形状及其在生物滤池中的装填方式等对厌氧滤池的运行性能有很大影响。
升流式厌氧生物滤池的流态接近于平推流,纵向混合不明显。降流式厌氧生物滤池一般采用较大回流比,其流态接近于完全混合状态。因此,在升流式厌氧生物滤池中,反应器内存在较明显的有机物浓度梯度,进而出现明显的微生物分层现象;而在降流式生物滤池内,上、中、下层的生物量接近。
(2)反应器特点
由于厌氧微生物在厌氧滤池中附着于载体表面并形成生物膜,微生物浓度较高,因此有机物去除能力强,出水悬浮固体SS较低,出水水质较好;微生物停留时间长,可缩短水力停留时间,生成的剩余污泥可不需要专设泥水分离和污泥回流设施,运行管理方便;耐冲击负荷能力较强,适用的废水有机物浓度范围宽;启动时间短,停止运行后的再启动也较容易,无搅拌与回流设施,整个工艺能耗低,系统运行稳定;主要问题为布水不易均匀,滤料易堵塞。此缺点可通过改变滤料和运行方式而克服。
由于垃圾焚烧厂渗滤液的SS、COD、硬度等指标较高,使用AF易堵塞滤料,清洗频繁,故AF在垃圾焚烧厂渗滤液处理中使用较少。
3.3.2 上流式厌氧污泥床反应器(UASB)
UASB是目前应用最为广泛的一种厌氧反应器。如图3.3所示,UASB反应器在运行过程中,废水以一定的流速自反应器底部流入,一般为0.5~1.5m/h,多宜在0.6~0.9m/h之间。UASB底部有大量厌氧污泥,废水从底部进入并通过污泥层,废水中的有机物与其中的微生物充分接触进而得到降解。产生的沼气附着在污泥颗粒上,使其悬浮于废水中,形成下密上疏的悬浮污泥层。悬浮的气泡逐渐上浮、聚集、变大,能够起到一定的搅拌作用;污泥颗粒被附着的气泡带到上层后撞在三相分离器上使气泡脱离,污泥颗粒又沉降到污泥层,部分进入澄清区的微小悬浮固体也由于静沉作用而被截留下来,最终滑落到反应器下层。这种反应器的污泥浓度可维持在40~80g/L,容积负荷达3~15kg (COD)/(m3·d)。

图3.3 上流式厌氧污泥床反应器
(1)工艺构造
UASB反应器的基本构造主要包括以下几个部分:污泥床、污泥悬浮层、沉淀区和三相分离器,各组成部分的功能、特点及工艺要求分述如下。
①污泥床:污泥床位于UASB反应器的底部,具有很高的污泥生物量,其混合液悬浮固体浓度(Mixed Liquid Suspended Solids,MLSS)一般为40~80g/L。污泥床中的污泥由活性生物量(或细菌)占70%~80%以上的颗粒污泥组成,正常运行的UASB中的颗粒污泥的粒径一般在0.5~5mm之间,具有优良的沉降性能,其沉降速度一般为1.2~1.4cm/s,典型的SVI为10~20mL/g。颗粒污泥中的生物相组成较复杂,主要为杆菌、球菌和丝状菌等。污泥床一般占UASB容积的30%左右,但它对有机物的降解量一般可占到整个反应器全部降解量的70%~90%。污泥床在对有机物降解的同时,产生的微小沼气气泡经不断地积累、综合而逐渐形成大气泡,气泡在上升过程中实现污泥混合。
②污泥悬浮层:污泥悬浮层位于污泥床的上部,占整个UASB容积的70%左右,其污泥浓度低于污泥床,通常为15~30g/L。污泥高度絮凝,一般为非颗粒状,其沉降速度明显小于颗粒污泥,SVI一般在30~40mL/g之间,靠来自污泥床中上升的气泡实现混合。污泥悬浮层中絮凝污泥的浓度呈自下而上逐渐减小的分布状态。该层负责降解整个UASB反应器10%~30%的有机物。
③沉淀区:沉淀区位于UASB反应器顶部,其作用之一是使随水流上升的固体颗粒(主要是污泥悬浮层中的絮凝性污泥)沉淀下来,并沿沉淀区底部的斜壁滑落至反应区内(包括污泥床和污泥悬浮层),以减少反应器污泥流失、保证污泥床中污泥浓度。另一个作用是,可以通过调整沉淀区的水位高度来保证集气室的有效体积,防止集气空间破坏。
④三相分离器:三相分离器是UASB反应器的主要特点之一,三相分离器的合理设计是其正常运行的重要保证。三相分离器一般设在沉淀区下部,也可设在反应器顶部,主要作用是将气体(沼气)、固体(污泥)和液体(被处理的废水)三相加以分离,沼气被引入集气室,而污泥和出水则进入上部的静置沉淀区,泥水在重力的作用下发生分离,固体污泥颗粒下沉至反应区。三相分离器由气体收集器和折流挡板组成。实质上,沉淀装置也可看作三相分离器的组成部分,相当于传统污水处理工艺中的二次沉淀池,并同时具有污泥回流功能。
(2)工艺设计
①反应器的有效容积计算公式如式(3-3)所示。
(3-3)
式中 Q——设计处理流量,m3/d;
C0——进出CODCr浓度,kg COD/m3;
E——去除率,一般取65%~80%;
Nv——容积负荷,m3/(m2·h)。
②反应器的形状和尺寸。工程设计反应器n座,横截面积为圆形。从布水均匀性和经济性考虑,单池高径比设计为1.2∶1较合适。
反应器有效高度计算公式如式(3-4)所示。
(3-4)
计算可得到单体的横截面积S和高度H。
利用公式(3-5)可得反应器的水力负荷。
(3-5)
对于颗粒污泥,水力负荷Vr一般在0.1~0.9m3/(m2·h)。
③布水系统的设计计算。反应器布水点数量设置与进水浓度、处理流量、容积负荷等因素有关。当颗粒污泥的Nv为4kg COD/(m3·d)左右时;每个布水点服务区域2~5m2;出水宜为流速2~5m/s;配水中心距池底一般为20~25cm。
④污泥总量计算。UASB的污泥床主要由沉降性能良好的厌氧污泥组成,平均浓度为20g VSS/L,则UASB反应器中污泥的总量可由式(3-6)计算,总产泥量可由式(3-7)计算。
G=VC (3-6)
式中 V——反应器有效容积,m3;
C——悬浮颗粒物浓度,mg/L。
X=γQC0E (3-7)
式中 γ——污泥常数,kg VSS/kg CODCr,一般取0.05~0.10;
Q——每日进水量,m3/d;
C0——反应器内CODCr浓度,kg/m3;
E——CODCr去除率,%。
(3)UASB反应器特点
反应器中有高浓度的活性污泥。这种污泥是通过严格控制反应器的水力特性和容积负荷,通过污泥的自身絮凝、结合及逐步的固定化过程而形成的。污泥特性的好坏直接影响UASB反应器的运行性能;反应器具有三相分离器。这种三相分离器具有可以自动将泥、水、气加以分离的功能;反应器无搅拌装置。反应器的搅拌是通过产气的上升迁移作用而实现的,因而操作管理比较简单。
(4)渗滤液处理设计案例
宿迁某生活垃圾发电厂渗滤液处理规模为250m3/d,采用“调节池+加温池+UASB厌氧反应器+MBR系统(SBR系统+内置式帘式膜)+深度处理系统(纳滤系统+反渗透系统)”组合工艺,其进水水质如表3.1所示。出水达到《城市污水再生利用 工业水水质》(GB/T 19923—2005)中表1敞开式循环冷却水水质标准,在全量处理渗滤液的同时,实现其全回用的目标。
表3.1 设计进出水水质

①进出水水质
②设计参数
UASB反应器容积负荷:Nv=3.5kg COD/(m3·d);
沼气产气率:0.35m3(标准)/kg COD;
沼气热值参考值:21000~25000kJ/m3(标准);
沼气产气总量:Q≈2350m3(标准)/d(CH4含量按65%考虑);
单格平面尺寸:φ=10m×16.5m;
设计总容积:V=1150m3;
总水力停留时间:HRT=9.2d;
有效水深:14.70m;
结构形式:地上式钢结构;
数量:2座。
③设备清单及仪表
排泥泵:Q=29m3/h,H=12.7m,N=3.0kW,数量1台;
循环泵:Q=160m3/h,H=16m,N=11.0kW,数量4台;
电动蝶阀:DN100,数量6台;
沼气点火器:Q=100m3/h,H=7m,数量1台;
流量计:介质为气体,型号DN100,Q=30~200m3/h,数量2台;
温度计:DN100,数量6台。
该渗滤液处理站目前已稳定运行6年,UASB反应器能有效地截留有机物,去除率仍可保持在80%左右。反应器设有三相分离器,可以有效地收集沼气,便于沼气回收利用。另外,该反应器操作管理比较简单。然而,因为渗滤液水质的SS及硬度较大,在运行后期,该反应器经常会出现进水管路结垢,出水带泥等现象,仍存在较多需要改善的地方。
3.3.3 升流式厌氧污泥床—滤层反应器(UBF)
升流式厌氧污泥床-滤层反应器,又称厌氧复合反应器,由几种厌氧反应器复合而成,目前已开发的多由升流式厌氧污泥床和厌氧生物滤池复合而成。
(1)工艺构造
1984年加拿大科学技术委员会生物科学部Guiot和den Berg等人开发了UBF,用来处理制糖废水。反应器上部1/3容积为填料层,填充的塑料环比表面积为235m2/m3,反应器下部1/3容积为污泥床。容积负荷在26kg COD/(m3·d)和51kg COD/(m3·d)时的CODCr去除率分别为93%以上和64%。其后,加拿大多伦多附近城市污水处理厂将原有厌氧工程改建为3400m3的复合床反应器,反应器上部2/3填充波纹板塑料,比表面积125m2/m3,波纹板的间距为1.3cm。处理的废水为丁氨二酸废水,进水CODCr为18000mg/L,停留时间50h,容积负荷为6kg COD/(m3·d),CODCr去除率达80%,未出现堵塞和短流情况,底部的污泥浓度(VSS)达50~100g/L。
(2)反应器特点
载体填料的存在为微生物的附着和生长提供足够空间,为反应器保持高浓度生物量,保证反应器的稳定进行和良好的出水水质;容积负荷较高,水力停留时间短,耐冲击能力较强,不易堵塞;颗粒污泥的存在保证了反应器停运后可实现快速启动。
(3)渗滤液处理设计案例
宜兴某生活垃圾发电厂渗滤液处理规模为150m3/d,采用“调节池+氨吹脱预处理+厌氧池(UBF)+SBR池+臭氧系统+膜处理系统(微滤+纳滤)”,其进水水质如表3.2所示。出水达到《污水综合排放标准》(GB 8978—1996)中一级排放标准。
表3.2 设计进出水水质

厌氧生物反应系统选用两级UBF,中温条件下消化。第一级的功能是:水解和液化固态有机物为有机酸;缓冲和稀释负荷冲击与有害物质,并将截留难降解的固态物质。第二级的功能是:保持严格的厌氧条件和pH值,以利于甲烷菌的生长;降解、稳定有机物,产生含甲烷较多的消化气,并截留悬浮固体,以改善出水水质。该系统使用潜水搅拌机作为内循环装置,池外设置污泥回流循环。
①进出水水质
②设计说明 UBF反应器的设计核心是容积负荷,一般情况下,一级UBF反应器容积负荷可以设置高一些,二级UBF反应器容积负荷设计值偏低一些,用于提高UBF反应器处理效果。
③设计参数
一级UBF反应器容积负荷:Nv1=6.5kg COD/(m3·d);
二级UBF反应器容积负荷:Nv2=2.0kg COD/(m3·d);
沼气产气率:0.35Nm3/kg COD;
沼气热值参考值:21000~25000kJ/Nm3;
污泥产率:X=0.04kg干泥/kg COD;
沼气产气总量:Q≈1410Nm3/d(CH4含量按65%考虑);
污泥总量:X=18m3/d(按99%的含水量考虑);
单格平面尺寸:LB=7.00m×5.50m;
设计总容积:V=1440m3;
总水力停留时间:HRT=8d;
有效水深:9.50m;
结构形式:半地下式钢筋混凝土结构;
数量:2座,每座分2格。
④设备清单及仪表
潜水搅拌机:Φ260,N=1.5kW,数量8台;
排泥泵:Q=10m3/h,H=16m,N=4.0kW,数量2台;
电动蝶阀:DN50,数量6台;
沼气点火器:Q=50m3/h,H=7m,数量1台;
阻燃器:DN100,数量1台;
安全阀:DN100,数量1台;
流量计:介质为气体,型号DN100,Q=30~200m3/h,数量1台;
半软性填料:Φ150,数量540m3。
UBF反应器中的填料为微生物的附着和生长提供足够空间,使反应器内保持高浓度生物量,对有机物去除率可达85%,出水指标较优。然而,其结构形式为半地下式,在运行后期排泥较为困难,致使污泥沉积在池底,堵塞布水管并影响池容。此外,填料容易结垢,在影响了处理效率的同时也为检修带来较大不便。
3.3.4 膨胀颗粒污泥床反应器(EGSB)
膨胀颗粒污泥床反应器(Expanded Granular Sludge Blanket,EGSB),是第三代厌氧反应器,于20世纪90年代初由荷兰瓦赫宁根大学的Lettinga等率先开发。
(1)工艺构造
EGSB的构造与UASB有相似之处,主要由布水装置、三相分离器、出水收集装置、循环装置、排泥装置及气液分离装置组成。与UASB反应器的不同之处是,EGSB反应器设有专门的出水回流系统。EGSB反应器一般为圆柱状塔形,具有很大的高径比,宜在3~8之间。颗粒污泥的膨胀床改善了废水中有机物与微生物之间的接触,强化了传质效果,提高了反应器的生化反应速度,从而大大提高了反应器的处理效能。EGSB反应器结构形式如图3.4所示。

图3.4 EGSB反应器结构示意图
EGSB反应器进水应符合如下条件:①pH值宜为6.0~8.0;②常温厌氧温度宜为20~25℃,中温厌氧温度宜为35~40℃,高温厌氧温度宜为50~55℃;③进水CODCr浓度宜大于1000mg/L;④营养元素COD∶N∶P宜为(100~500)∶5∶1;⑤悬浮物含量宜小于2000mg/L,氨氮浓度宜小于2000mg/L,硫酸盐浓度应小1000mg/L,COD/S比值应大于10。
(2)工艺设计
①EGSB反应器的容积计算。对EGSB反应器容积的设计可由式(3-8)计算得出
(3-8)
式中 V——反应器有效容积,m3;
Q——EGSB反应器设计流量,m3/d;
Nv——容积负荷,kg COD/(m3·d),适宜范围为10~30kg COD/(m3·d);
S0——进水有机物浓度,mg COD/L。
②布水装置。布水装置宜采用一管多孔式布水和多管布水方式。一管多孔式布水孔口流速应大于2m/s,穿孔管直径应大于100mm,配水管中心距反应器池底宜保持150~250mm的高度;多管布水每个进水口负责的布水面积宜为2~4m2。另外,EGSB反应器的有效水深宜在15~24m之间;EGSB反应器内废水的上升流速宜在3~7m/h之间。
③三相分离器。EGSB宜采用整体式或组合式的三相分离器。整体式三相分离器斜板倾角范围为55°~60°;组合式三相分离器反射板与隙缝之间的遮盖应在100~200mm,层间距宜为100~200mm。EGSB反应器可采用单级三相分离器,也可采用双级三相分离器,设置双级三相分离器时,下级三相分离器宜设置在反应器中部,覆盖面积宜为50%~70%,上级三相分离器宜设置在反应器上部,出气管尺寸大小应满足从集气室安全、高效地收集沼气的需要。
④出水装置。出水收集装置应设在EGSB反应器顶部,圆柱形EGSB反应器出水宜采用放射状的多槽或多边形槽出水方式,集水槽上应加设三角堰,堰上水头应大于25mm,水位宜在三角堰齿1/2处,出水堰口负荷宜小于1.7L/(s·m)。EGSB反应器进出水管道宜采用聚氯乙烯(PVC)、聚乙烯(PE)、聚丙烯(PPR)、不锈钢、高密度聚乙烯(HDPE)等材料。若废水中含有大量蛋白质、脂肪或悬浮固体,宜在出水收集装置前设置消泡装置。
⑤循环装置。EGSB反应器设有循环装置,分外循环和内循环两种,二者均由水泵加压实现,回流比根据上升流速确定,上升流速按公式(3-9)计算。
(3-9)
式中 V——反应器上升流速,m/h;
Q——EGSB反应器进水流量,m3/h;
Q回——EGSB反应器回流流量,包括内回流和外回流,m3/h;
A——反应器横截面积,m2。
⑥排泥装置。EGSB反应器的污泥产率为0.05~0.10kg VSS/kg COD,排泥频率宜根据污泥浓度分布曲线确定。应在不同高度设置取样口,根据污泥浓度制定分布曲线。EGSB反应器宜采用重力多点排泥方式,排泥点宜设在污泥区的底部。排泥管管径应大于150mm,底部排泥管可兼作放空管。
(3)EGSB反应器特点
EGSB反应器作为一种改进型的UASB反应器,虽然在结构形式、污泥形态等方面与UASB反应器非常相似,但其工作运行方式与UASB显然不同,高的液体表面上升流速使颗粒污泥床层处于膨胀状态,不仅使进水能与颗粒污泥充分接触,提高了传质效率,而且有利于基质和代谢产物在颗粒污泥内外的扩散、传送,保证了反应器在较高的容积负荷条件下正常运行。EGSB反应器的主要特点体现在以下几个方面:
①结构方面:高径比大,大大缩小占地面积;布水均匀,污泥床处于膨胀状态,不易产生沟流和死角;三相分离器工作状态、条件稳定。
②运行方面:反应器启动时间短,容积负荷率可达40kg COD/(m3·d),污泥不易流失;液体表面上升流通常为2.5~6.0m/h,最高可达10m/h,液固混合状态好,因而在低温、处理低浓度有机废水有明显的优势;反应器设有出水回流系统,更适合于处理含有悬浮性固体和有毒物质的废水;以颗粒污泥接种,颗粒污泥粒径较大、沉降性能好、活性较高,处理效果较好。
③适用性方面:对含有难降解有机物、大分脂肪酸类化合物、高盐量、高悬浮性固体的废水亦有优势;适合处理中低浓度有机废水。
生活垃圾焚烧厂渗滤液是一种高盐量、高悬浮性固体的废水,但因其还含有高有机物(CODCr在40000mg/L以上),因此,EGSB反应器在对生活垃圾渗滤液处理中应用较少。
3.3.5 内循环厌氧反应器(IC)
1985年,荷兰Paques公司开发了一种被称为内循环的反应器。IC反应器在处理中低浓度废水时,容积负荷可达20~40kg COD/(m3·d),在处理高浓度有机废水时,容积负荷可提高至35~50kg COD/(m3·d),这是对现代高效反应器的一种突破,有着重大的理论意义和实用价值。
(1)工艺构造
IC反应器的基本构造如图3.5所示。

图3.5 IC反应器构造原理图
1—进水;2—第一反应室集气罩;3—沼气提升管;4—气液分离器;5—沼气排出管;6—回流管;7—第二反应室集气罩;8—集气管;9—沉淀区;10—出水管;11—气封
IC反应器的构造特点是具有很大的高径比,一般可达到4~8,高度可达16~25m。IC反应器从功能上讲由四个不同的功能部分组成,即混合部分、污泥膨胀床部分、精处理部分以及回流部分,具体的说明如下:
①混合区:由反应器底部进入的废水与颗粒污泥、内部气体循环所带回的出水在该区域有效混合,使进水得到有效稀释和均质化。
②污泥膨胀床:污泥床的膨胀或流化是由上流进水、回流沼液和沼气造成的。废水和污泥之间有效地接触能够保持污泥较高的活性,提高容积负荷和反应器处理效率。
③精处理区:由低的污泥负荷率、相对长的水力停留时间和推流的水力特性,使进水在该部分得到二次处理。另外,该部分由沼气产生的扰动较小,生物可降解物质几乎可被全部去除。虽然IC反应器的水力负荷率常高于UASB反应器,但因内部循环流体不经过精细处理区,因此,IC反应器在精处理区的上升流速也较低,这两点为IC反应器二次处理进水提供了条件。
④回流系统:IC反应器利用气提原理完成内部回流,这是因为上、下层气室间存在压力差,回流比例由产气量决定的。大部分有机物是在IC反应器下部的颗粒污泥膨胀床内降解的,产生的沼气经由第一分离器收集,通过气体升力携带水、污泥进入气体上升管,至反应器顶部的液气分离罐进行液气分离,水与污泥经过中心循环下降管流向反应器底部,形成内循环。一级分离器的出水在第二级处理区(反应器上部)得到再处理,由此,大部分可降解有机物得到降解,产生的沼气被二级分离器收集,出水通过溢流堰流出反应器。
(2)IC反应器特点
一般而言,与UASB反应器相比,在获得相同处理效率的条件下,IC反应器具有更高的进水容积负荷和污泥负荷率,IC反应器的平均升流速率可达处理同类废水UASB反应器的20倍左右。在处理低浓度废水时,混合区水力停留时间可缩短至2.0~2.5h,反应器容积更趋小型化。IC反应器的优点如下:
①容积负荷率高:由于IC反应器存在内循环,第一反应区有很高的升流速率,传质效果好,污泥活性高,能够处理高浓度有机废水,当CODCr为10000~15000mg/L时,进水容积负荷率可达30~40kg COD/(m3·d)。处理低浓度有机废水,当CODCr为2000~3000mg/L时,进水容积负荷率可达20~50kg COD(m3·d),HRT仅为2~3h,其CODCr去除率可达80%。
②节省基建投资:IC反应器占地面积小,仅为UASB反应器的1/4~1/3,可显著降低反应器的基建投资,适用于占地面积紧张的厂矿企业。
③形成内循环:与流化床和膨胀颗粒污泥床反应器不同,IC反应器靠沼气实现混合液循环,无需外加动力,降低能耗。
④抗冲击负荷能力强:以IC反应器处理低浓度废水时,循环流量可达进水流量的2~3倍;处理高浓度废水时,循环流量可达进水流量的10~20倍。循环流量与进水在第一反应室充分混合,使原污水中的有害物质得到充分稀释,降低了有害程度,并可防止局部酸化,提高了反应器的耐冲击负荷的能力。
⑤具有强缓冲能力:相对于进水,内循环液体碱度增加,后者通过与进水混合,提高进水pH值,提高对低pH值进水的适应性,使反应器的pH值保持稳定。处理缺乏碱度的废水时,可减少进水的投碱量。
⑥出水稳定性好:IC反应器相当于两个UASB反应器串联运行,第一反应室有很高的容积负荷率,相当于起“粗”处理作用,第二反应室具有较低的容积负荷率,相当于起“精”处理作用,一般情况下,两级厌氧处理比单级厌氧处理的稳定性好。
同样地,IC反应器仍有以下问题亟待解决:内循环系统复杂,内部管路过多,控制繁琐,占用了反应器的有效空间,影响了反应效率,增大了反应器的总容积;三相分离器的结构缺陷:IC反应器三相分离器造价较高,施工困难,日常维护复杂;高径比问题:较大的高径比使得水泵运行费用增加,且基建费用高,单位反应器体积造价的初始造价较高。
在渗滤液应用方面,IC反应器对进水SS要求较高,而生活垃圾渗滤液的SS较高,使IC反应器在处理渗滤液时,不易形成颗粒污泥,影响其处理效率;另外,生活垃圾渗滤液的硬度较大,IC反应器因其内部管线和构造较为复杂,因此较易出现结垢等问题,导致检修频繁。故IC反应器在焚烧厂垃圾渗滤液处理系统中应用较少。
3.3.6 内外循环厌氧反应器(IOC)
内外循环厌氧反应器(Internal Out Circulation,IOC)在结构上主要沿袭IC反应器的特点,如较大的高径比、串联的双反应室、双层三相分离器等特点。但是,IOC反应器主要改进了IC反应器的三相分离器、布水系统、排泥系统等。降低了系统调试和排泥的难度,同时,更加方便地控制反应器的上升流速,已经在项目上取得了较好的效果。
(1)工艺构造
如图3.6所示,高效厌氧反应器(IOC)主要由底部布水系统、第一反应室、一级三相分离器、第二反应室、二级三相分离器、气水分离器、内循环系统、外循环系统、排泥系统、沼气系统等组成。

图3.6 IOC厌氧反应器示意图
与UASB类似,废水由IOC底部进入系统后在布水管道的作用下实现均匀布水。废水中有机物与底部污泥充分接触并被降解,产生的沼气随进水、污泥沿反应器上升至一级三相分离器,此时,大量沼气被收集,部分颗粒污泥被截留并下沉至反应器(第一反应室);同样地,通过一级三相分离器的废水继续上升至第二反应室完成精处理,精处理后经二级三相分离器实现三相分离。由一级、二级三相分离器分离得到的沼气携带大量的废水沿管道进入气水分离器,经过气水分离器的沼气被引至下游综合利用设备,而废水则回流至反应器底部形成内循环以提高第一反应室的上升流速。反应过程中产生的剩余污泥则通过排泥系统排入污泥池。
①布水系统。布水系统的合理设计对厌氧反应器的良好运转至关重要,布水系统兼有配水和水力搅拌的双重功能,为了实现此二功能,布水系统的设计需满足如下条件:确保单位面积进水量相同,防止短路等现象发生;尽可能满足水力搅拌需要,保证进水有机物与污泥迅速混合;根据实际应用情况及计算流体动力学(Computational Fluid Dynamics,CFD)模拟成果,完成布水管道的长度、角度以及开口位置的设计。IOC反应器布水系统采用外置可插拔式布水装置,通过调节倾角角度,使进水形成旋流,提高生化反应传质效率,改善布水效果,同时便于后期检修。
②三相分离器。三相分离器是厌氧反应器最有特点和最重要的装置。它同时具有两个功能:截留上浮的悬浮物,收集分离器下方反应室产生的沼气,保证反应器出水水质。若要同时实现上述两种功能,则三相分离器的设计要力求高效收集沼气,并避免沼气和悬浮物上升至沉淀区,造成出水混浊和活性污泥流失。
根据垃圾渗滤液有机物、悬浮物浓度高的特点,IOC反应器的设计借鉴了IC反应器的特点,设置了上、下两级三相分离器,并通过二者将反应器分为上、下两个反应室和澄清区,下部为第一反应室,第一反应室内活性污泥浓度高、上升流速快,是降解有机物、产生沼气的主要区域;上部为第二反应室,该反应室内污泥浓度低、上升流速慢,在进一步去除剩余有机物的同时,减少出水带泥,提高出水水质;最上部为澄清区,进入澄清区的污水,通过溢流排出系统。
③内、外循环系统。循环系统能有效提高反应器内液体上升流速,使污泥处于流化膨胀状态,增大其与污水中有机物的接触几率,提高了反应器的容积负荷。IOC反应器顶部增设气水分离装置,分离水由内循环系统引至反应器底部,在不消耗能源的条件下提高了第一反应室的上升流速,既满足高效厌氧反应器上升流速高的要求,又最大限度地节约了能源。
IOC反应器设有外循环系统,外循环系统由集水装置、循环管路、循环泵及布水系统等组成。在第二反应室中间位置设置外循环集水装置,由集水管取水汇至集水筒,由外循环管路送至外循环泵,在泵的作用下,打入反应器底部布水管网,实现外循环。
④排泥系统。厌氧消化过程中由于微生物不断繁殖和进水中不可降解悬浮固体的长期累积,导致系统内污泥量增多,为定期排出剩余污泥,IOC反应器有针对性地设计考虑了排泥系统。传统厌氧反应器大多采用穿孔管多点排泥的方式,这种方式容易在穿孔管开口位置形成堵塞,造成排泥不均和形成死角,导致污泥无法及时排出。IOC反应器采用中心桶排泥,中心桶通过多根吸泥管与底部污泥斗连接,中心桶可双向流动,由内及外为排泥,由外及内为冲洗。此种排泥方式管路简单、排泥均匀、不短流;排泥前启动冲洗和搅动,排泥顺畅、不沉积。
⑤沼气水封系统。IOC反应器的沼气输送管路上设置有水封系统,减少沼气压力波动,稳定沼气压力,同时亦可吸收沼气中的水分。沼气水封装置内的液位可通过液位控制阀门组调节,多余的水分可自动排出,防止沼气憋压。
(2)IOC反应器特点
污泥浓度高,微生物量大,并且在内、外循环的作用下,传质效果好,进水容积负荷为普通厌氧反应器的2~3倍;有机物去除率高,去除率基本在90%左右,出水水质稳定;IOC反应器高径比大,占地面积小;高容积负荷率使其罐体体积相当于普通厌氧反应器的1/3~1/2,大大降低了基建投资;在以IOC处理渗滤液时,内循环流量可达进水量的20~30倍,大量循环水和进水充分混合,使原水中的有害物质得到充分稀释,大大降低了毒性物质对厌氧消化系统的影响,使得IOC反应器抗负荷冲击能力强;IOC反应器结合内、外循环系统,在厌氧罐正常运行时,只靠内循环即可满足上升流速的要求,节约能耗;IOC反应器的有机物降解率高,沼气产率高。
(3)工艺设计
①有效容积设计。厌氧罐的有效容积计算公式如式(3-10)所示。
(3-10)
式中 V——反应器有效容积,m3;
Q——废水的设计流量,m3/d;
Nv——容积负荷率,kg COD/(m3·d);
C0——进水CODCr浓度,kg/m3;
Ce——出水CODCr浓度,kg/m3。
②反应器尺寸设计。本项目设计IOC反应器的高径比为1.9,体积计算如式(3-11)所示。
(3-11)
③循环量设计。反应器中的进水总水力停留时间计算见式(3-12)。
(3-12)
式中 V——反应器有效容积,m3;
Q——废水的设计流量,m3/d。
④厌氧反应器的沼气产量还可以通过公式(3-13)计算得到。
(3-13)
式中 Qa——沼气产量,m3(标准)/d;
Q——进水流量,m3/d;
η——沼气产率,m3(标准)/kg COD,一般为0.45~0.50m3(标准)/kg COD;
S0——进水有机物浓度,mg COD/L;
Se——出水有机物浓度,mg COD/L。
(4)渗滤液厌氧处理案例
常州某项目设计处理规模为400m3/d,采用“调节池+IOC厌氧反应器+MBR系统(A/O系统+外置管式超滤膜处理系统)+深度处理系统(纳滤系统+反渗透系统)”组合工艺,进水水质如表3.3所示。出水达到《城市污水再生利用 工业水水质》(GB/T 19923—2005)中表1敞开式循环冷却水水质标准,在全量处理渗滤液的同时,实现其全回用的目标。
表3.3 设计进出水水质

①进出水水质
②设计说明 渗滤液厌氧部分的设计核心要点是控制好污泥负荷,IOC厌氧反应器由上下两个反应室构成,当其应用于高浓度废水处理时,如渗滤液等,进水容积负荷可以达5~8kg COD/(m3·d)。厌氧反应器在实际应用中已经标准化,可根据渗滤液水量来合理选择不同规格的厌氧反应器,使得厌氧反应器各反应室的容积负荷处于合理的区间。此处,取容积负荷为5kg COD/(m3·d)。其中厌氧反应器第一反应室需去除总COD的80%,其容积负荷可适当放大。第二反应室去除总COD的20%,其容积负荷可以适当缩小。
以第一反应室有机负荷取6.8kg COD/(m3·d),第二反应室有机负荷取2.4kg COD/(m3·d)为例。在厌氧罐选型中,可根据有机负荷、水量由式(3-10)计算得第一、二反应室体积;由反应室总容积、厌氧罐高径比(经验值)计算出厌氧罐的直径,以确定厌氧罐的规格、尺寸,由厌氧罐直径及反应室容积等,可计算出理论第一、二反应室高度,考虑到厌氧罐三相分离器,出水堰等部件,可对厌氧罐的设计高度再进行调整,由式(3-11)计算;厌氧罐中渗滤液的水力停留时间可用式(3-12)计算;沼气产量可由式(3-13)计算所得。最终,通过一系列计算可得厌氧反应器的各项重要参数。其具体的计算过程如下所示。
③设计参数
设计规模:Q=400m3/d;
设计COD去除率:90%;
设计数量:2座;
结构形式:地上式钢结构。
则,单座厌氧罐的计算过程如下。
容积尺寸:
第一反应室有效容积:
第二反应室有效容积:
IOC反应器的总有效容积为V=V1+V2=1140+810=1950m3
本设计的IOC反应器的高径比为1.9。
则,取11m。
H=1.9×10.7=20.3m,有效高度取20.5m,设计高度取22m。
IOC反应器的底面积,则
第二反应室高,预留出水堰高度1.5m,取10m。
第一反应室的高度H1=H-H2=22-10=12m
设计水力停留时间:
沼气产量计算:
④主要设备及仪表
厌氧进水泵,Q=36m3/h,H=30m,N=7.5kW,2台;
厌氧循环泵:Q=200m3/h,H=9m,N=7.5kW,4台;
厌氧排泥泵:Q=49m3/h,H=17.5m,N=7.5kW,2台;
进水电动调节阀:DN65,2台;
排泥电动阀:DN150,pn=1.0MPa;
温度计:2台;
进水电磁流量计:DN65,2台;
循环电磁流量计:DN200,2台;
火炬:Q=600m3/h,N=3.0kW;
沼气压力传感器:1台;
沼气流量计:1台;
温度传感器:1台。
IOC厌氧反应器针对生活垃圾渗滤液的复杂性进行了针对性的设计,使其可以高效地处理生活垃圾渗滤液。在项目运行中,IOC对于有机物的去除率可达90%以上;对SS的截留效率较高,出水无带泥现象;通过结构形式的优化,可以大大降低反应器结垢速率。得益于以上优点,IOC在渗滤液处理行业内得到越来越多的应用。