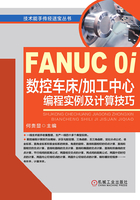
例1-11 圆弧连接类工件的加工(能用G71指令的尽量少用G73指令)。
如图1-11所示,该工件毛坯尺寸为ϕ40mm×50mm,材料为45钢,编写其加工程序。

图1-11 圆弧连接类零件
数学分析:
1)我们先来计算一下这个R13mm的圆,当X=11.34时Z的坐标值。根据圆的方程和直线的方程的联立,有

根据题意,解得Z=-19.356445548,和图样标注尺寸“19.36”还是相符的。我们在程序中使用Z-19.356这个值。
2)再来计算一下R8mm的圆心坐标,进而求出它的方程。
已知R13mm圆的圆心坐标为(0,-13),两个圆弧的外切点坐标为(11.34,-19.356445548),由R13mm圆心连接这个切点并延长,则R8mm圆心在这条延长线上,圆心和该切点距离8mm,根据R13mm圆心到切点的距离、切点到R8mm圆心的距离之间的比例关系,可以求出R8mm的圆心
X=(11.34-0)×(13+8)/13+0=18.31846154
Z=[-19.356445548-(-13)]×(13+8)/13+(-13)=-23.26810435
所以R8mm这个圆的方程是(X-18.31846154)2+(Z+23.26810435)2=82。
知道了该圆的方程后,就能解出当Z-30时,X=13.99624209,直径值为27.992mm,和图样所标注的“ϕ28”相差无几。
对这个图样,按照多数人的思路,编程是这样的:
O0032;
G97 G99 M3 S800 T101;工件伸出卡爪端面至少24mm
G0 X100.Z100.M8;
X45.Z2.;接近工件,两个轴均留有一定的距离
G1 Z0 F0.3;切削到平端面的起点上
X-2.F0.2;平端面
G0 X40.Z1.;定位到G71指令循环的起点上
G71 U2.R0.5 F0.22;设定背吃刀量、退刀量、进给量
G71 P1 Q2 U0.8 W0.1;设定精加工余量
N1 G0 X28.;
G1 X32.03 Z-1.F0.18 S1000;延长线倒角,加工到公差带的中间值,设定精加工进给量、转速
Z-15.05;加工到公差带的中间值
X36.;
X37.98 W-1.;加工到公差带的中间值
N2 Z-20.;
G70 P1 Q2;精加工
M9;
G0 X100.Z200.M5;退刀到安全点
M0;调头装夹,垫上铜皮夹持左端ϕ32mm,用卡爪端面顶紧ϕ38mm处,夹紧工件,用2号刀先轻轻平一刀,测量Z向的长度,如长度为48.5mm,比预想的长了0.5mm,则在2号偏置值里输入Z0.5,按[测量]软键;如果是批量加工,可以分成两个程序
M3 S800 T202;换上第二把刀,主偏角93°,刀尖角35°
G0 X45.Z2.M8;接近工件,两个轴均留有一定的距离
G1 Z0 F0.3;切削到平端面的起点上
X-2.F0.2;平右端端面
G0 X42.Z0.1.;定位到G73指令的定位点上,由于形状呈凹形,Z设得很小
G73 U19.5 W0.05 R13 F0.18;设定粗加工时两轴的加工余量,加工次数,进给量
G73 P3 Q4 U1.W0.01;设定精加工时两轴的加工余量
N3 G0 X0;
G1 Z0 F0.15 S1000;
G3 X22.68 Z-19.356 R13.;
G2 X27.992 Z-30.R8.;
G1 X36.;
N4 X40.W-2.;倒角,延长了1mm
G70 P3 Q4;
M9;
G0 X100.Z200.M5;
T101;
M30;
上述程序分析:
1)如果把这个工件左右两端作为一个程序,一定要注意N1、N2和N3、N4的程序段号不能重复;否则,系统会自动搜索到由G71、G73、G70指令指定的程序段号,机床将会发生不可预知的动作。若是作为两个程序,则没有这个限制。
2)该图样右边,精加工的最小直径尺寸是0,毛坯的尺寸是ϕ40mm,去掉精加工的直径余量1mm,还剩39mm,半径值是19.5mm,正是程序中编写的“U19.5”;根据实际情况,背吃刀量设为1.5mm,正好是13次分割切削,所以编写为“R13”。但这么编程,是不是因为切削循环用得顺手了?棒料用G73指令来编程,空走刀肯定少不了,效率大打折扣。其实,右边不用切削循环反而效率高,知道了两段圆弧的方程,其与不同直径坐标值的刀具轨迹的交点坐标很容易求得。
为此,右端粗加工时我们仍使用1号刀,采用和G71指令类似的轨迹去编程:
第一刀,车到ϕ34mm,背吃刀量3mm,这一刀和两段圆弧均无交点,Z=-30.,留0.1mm的余量,编程为Z-29.9。
第二刀,车到比R13mm圆的最大直径ϕ26mm大1mm处的ϕ27mm,背吃刀量3.5mm,这一刀和R8mm圆[(X-18.31846154)2+(Z+23.26810435)2=82]有交点,代入方程的是X=13,恰似G71粗加工时给G70指令精加工时留了1mm的直径余量一样,解得Z=-29.244,留0.1mm的余量,编程为Z-29.144。
第三刀,车到ϕ21mm,背吃刀量3mm,这一刀和R13mm圆[X2+(Z+13)2=132]有交点,代入方程的是X=10,恰似G71指令粗加工时给G70精加工时留了1mm的直径余量一样,解得Z=-4.693,留0.1mm的余量,编程为Z-4.593。
第四刀,车到ϕ15mm,背吃刀量3mm,这一刀和R13mm圆[X2+(Z+13)2=132]有交点,代入方程的是X=7,恰似G71指令粗加工时给G70指令精加工时留了1mm的直径余量一样,解得Z=-2.046,留0.1mm的余量,编程为Z-1.946。
第五刀,车到ϕ9mm,背吃刀量3mm,这一刀和R13mm圆[X2+(Z+13)2=132]有交点,代入方程的是X=4,恰似G71指令粗加工时给G70指令精加工时留了1mm的直径余量一样,解得Z=-0.631,留0.1mm的余量,编程为Z-0.531。
3)R8mm这段圆弧对应的工件,半径最小处的值为(18.318-8)=10.318mm,该处粗加工后的半径值为13.5mm,留给T202的精加工背吃刀量为3.182mm,进给量小一点,一刀车过去是没有问题的。
参考程序如下:
O0034;
G97 G99 M3 S800 T101;工件伸出卡爪端面至少24mm
G0 X100.Z100.M8;
X45.Z2.;
G1 Z0 F0.3;
X-2.F0.2;平端面
G0 X38.5 Z1.;定位到外圆切削第一刀的起点
G1 Z-20.F0.22;车第一刀
G0 U1.Z1.;退刀
X32.5;定位到外圆切削第二刀的起点
G1 Z-15.F0.22;车第二刀
G0 U1.Z1.S1000;退刀,适当提高转速
X28.;定位到倒角的延长线上,准备精车
G1 X32.03 Z-1.F0.12;倒角1mm,较小的进给;加工到公差带的中间值
Z-15.05 F0.22;轴向长度加工到公差带的中间值
X36.;
X37.98 W-1.;倒角1mm
Z-20.;加工到公差带的中间值
G0 X50.Z2.M9;
M5;
X100.Z150.;
M0;调头装夹,垫上铜皮夹持左端ϕ32mm,用卡爪端面顶紧ϕ38mm处,夹紧工件,用1号刀先轻轻平一刀,测量Z向的长度,如长度为48.5mm,比工件最终尺寸长了0.5mm,则在21号偏置值里输入Z0.5,按[测量]软键;点POS键找到绝对坐标,把此时的X轴的绝对坐标值输入21号偏置的X里;如果是批量加工,可以分成两个程序
T121 M3 S800;调用这把刀具的另外一个偏置值
G0 X45.Z2.M8;
G1 Z0 F0.3;
X-2.F0.2;平右端端面
G0 X34.Z1.;
G1 Z-29.9 F0.22;第一刀
G0 U1.Z1.;
X27.;
G1 Z-29.144;第二刀
X29.;移动到比下一刀工件外形“ϕ28”大1mm的尺寸上
Z-29.9;
G0 U1.Z1.;
X21.;
G1 Z-4.593;第三刀
G0 U1.Z1.;
X15.;
G1 Z-1.946;第四刀
G0 U1.Z1.;
X9.;
G1 Z-0.531;第五刀
G0 X50.Z150.;
T202 M3 S1000;换上第二把刀,主偏角93°,刀尖角35°
G0 X0 Z1.;
G1 Z0 F0.2;
G3 X22.68 Z-19.356 R13.F0.15;背吃刀量较大且不均匀,刀片强度差,所以进给量较小
G2 X27.992 Z-30.R8.F0.12;
G1 X36.;
X40.W-2.;倒角,延长了1mm
M9;
G0 X100.Z200.M5;退刀到安全位置
T101;换上程序中的第一把刀
M30;
细节提示:
不用多说,这么编程效率高多了。所以说,编程要根据图样,考虑到刀具、工件、效率等情况,不要拘泥于使用切削循环。