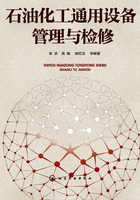
第四节 反 应 釜
一、反应釜概述
反应釜(或称反应器)是通过化学反应得到反应产物的设备,或者是为细胞或酶提供适宜的反应环境以达到细胞生长代谢和进行反应的设备。几乎所有的过程装备中,都包含反应釜。因此如何选用合适的反应器型式,确立最佳的操作条件和设计合理可靠的反应器,对满足日益发展的过程工业的需求具有十分重要的意义。
(一)反应釜的作用
反应釜的主要作用是提供反应场所,并维持一定的反应条件,使化学反应过程按预定的方向进行,得到合格的反应产物。
一个设计合理、性能良好的反应釜,应能满足如下要求:
(1)应满足化学动力学和传递过程的要求,做到反应速率快、选择性好、转化率高、目的产品多、副产物少;
(2)应能及时有效地输入或输出热量,维持系统的热量平衡,使反应过程在适宜的温度下进行;
(3)应有足够的机械强度和抗腐蚀能力,满足反应过程对压力的要求,保证设备经久耐用,生产安全可靠;
(4)应做到制造容易,安装检修方便,操作调节灵活,生产周期长。
(二)反应釜的分类
反应釜一般可根据用途、操作方式、结构等不同方法进行分类。例如根据用途可把反应釜分为催化裂化反应器、加氢裂化反应器、催化重整反应器、氨合成塔、管式反应炉、氯乙烯聚合釜等类型。根据操作方式又可把反应釜分为连续式操作反应釜、间歇式操作反应釜和半间歇式操作反应釜等类型。
最常见的是按反应釜的结构来分类,可分为釜式反应器、管式反应器、塔式反应器、固定床反应器、流化床反应器等类型。
1.釜式反应器
釜式反应器也称搅拌釜式、槽式、锅式反应器,主要由壳体、搅拌器和传热部件等组成。釜式反应器具有投资少、投产快、操作灵活方便等特点。
2.管式反应器
管式反应器一般是由多根细管串联或并联而构成的一种反应器。其结构特点是反应器的长度和直径之比较大,一般可达50~100,常用的有直管式、U形管式、盘管式和多管式等几种形式。管式反应器的主要特点是反应物浓度和反应速率只与管长有关,而不随时间变化。反应物的反应速率快,在管内的流速高,适用于大型化、连续化的生产过程,生产效率高。
3.塔式反应器
塔式反应器的高径比介于釜式反应器和管式反应器之间,约为8~30,主要用于气液反应,常用的有鼓泡塔、填料塔和板式塔。
鼓泡塔为圆筒体,直径一般不超过3m,底部装有气体分布器,顶部装有气液分离器。在塔体外部或内部可安装各种传热装置或部件。还有一种带升气管的鼓泡塔,是在塔内装有一根或几根升气管,使塔内液体在升气管内外做循环流动,所以称为气升管式鼓泡塔。
填料塔是在圆筒体塔内装有一定厚度的填料层及液体喷淋、液体再分布及填料支承等装置。其特点是气液返混少、溶液不易起泡、耐腐蚀和压降小。
板式塔是在圆筒体塔内装有多层塔板和溢流装置,在各层塔板上维持一定的液体量,气体通过塔板时,气液相在塔板上进行反应。其特点是气、液逆向流动接触面大、返混少,传热传质效果好,液相转化率高。
4.固定床反应器
固定床反应器是指流体通过静止不动的固体物料所形成的床层而进行化学反应的设备。以气固反应的固定床反应器最常见。固定床反应器根据床层数的多少又可分为单段式和多段式两种类型。单段式一般为高径比不大的圆筒体,在圆筒体下部装有栅板等板件,其上为催化剂床层,均匀地堆置一定厚度的催化剂(能改变化学反应速率,而其自身的数量和组成在反应前后保持不变的物质)固体颗粒。单段式固定床反应器结构简单、造价便宜、反应器体积利用率高。多段式是在圆筒体反应器内设有多个催化剂床层,在各床层之间可采用多种方式进行反应物料的换热。其特点是便于控制、调节反应温度,防止反应温度超出允许范围。
5.流化床反应器
细小的固体颗粒被运动着的流体携带,具有像流体一样能自由流动的性质,这种现象称为固体的流态化。一般,把反应器和在其中呈流态化的固体催化剂颗粒合在一起,称为流化床反应器。
流化床反应器多用于气固反应过程。当原料气通过反应器催化剂床层时,催化剂颗粒受气流作用而悬浮起来呈翻滚沸腾状,原料气在处于流态化的催化剂表面进行化学反应,此时的催化剂床层即为流化床,也叫沸腾床。
流化床反应器的形式很多,但一般都由壳体、内部构件、固体颗粒装卸设备及气体分布、传热、气固分离装置等构成。流化床反应器也可根据床层结构分为圆筒式、圆锥式和多管式等类型。
圆筒式的床层为圆筒形,结构简单、制造方便,设备容积利用率高,使用较广泛。圆锥式的结构特点是床层横截面从气体分布板向上逐渐扩大,使上升气体的气速逐渐降低,固体颗粒的流态化较好,特别适用于粒径分布不均的催化剂和反应时气体体积增大的反应过程。多管式的结构是在大直径圆筒形反应器床层中竖直安装一些内换热管,其特点是气固返混少,床层温度较均匀和转化率高。
流化床反应器气固湍动、混合剧烈,传热效率高,床层内温度较均匀,避免了局部过热,反应速率快。流态化可使催化剂作为载热体使用,便于生产过程实现连续化、大型化和自动控制。但流化床使催化剂的磨损较大,对设备内壁的磨损也较严重。另外,也易产生气固的返混,使反应转化率受到一定的影响。
(三)反应釜的工作过程
石油化工生产时,在反应釜中进行的不仅仅是单纯的化学反应过程,同时还存在着流体流动,物料传热、传质、混合等物理传递过程。在反应釜中,化学反应的机理、步骤和速率是根据化学动力学的规律进行的。如对于气液反应,反应速率除与温度和浓度有关外,还与相界面的大小和相间的扩散速度有关。对于气固反应,不论在什么条件下进行,气相组分都必须先扩散到固体催化剂的表面上,再在催化剂表面进行化学反应。化学反应过程是反应釜工作的本质过程。
由于化学反应时原料的种类很多,反应过程也很复杂,对反应产物的要求也各不相同。为满足不同的反应要求,反应釜的结构类型和尺寸大小也多种多样、大小不一,操作方式和操作条件也各不相同。如间歇式操作的反应釜,原料是一次性加入的;而连续式操作的反应釜,原料是连续加入的。不同结构形式和尺寸的反应釜及不同的操作条件和方式,必将影响流体的流动状态和物料的传热、传质及混合等传递过程。而传递过程是实现反应过程的必要条件。因此反应釜的工作过程就是以化学动力学为基础的反应过程和以热量传递、质量传递、动量传递为基本内容的传递过程同时进行、相互作用、相互影响的复杂过程。
二、反应釜的结构
反应釜主要由釜体、釜盖、传动装置、搅拌器、密封装置等组成,如图2-51所示。

图2-51 反应釜结构
1—传动装置;2—釜盖;3—釜体;4—搅拌装置;5—夹套;6—工艺接管;7—联轴器;8—人孔;9—密封装置;10—蒸汽接管;11—减速机支架
(一)壳体
壳体由圆形筒体、上盖、下封头构成。上盖与筒体的连接有两种方法,一种是盖子与简体直接焊死构成一个整体;另一种是考虑拆卸方便用法兰连接。上盖开有人孔、手孔和工艺接孔等。壳体材料根据工艺要求来确定,最常用的是铸铁和钢板,也有的采用合金钢或复合钢板。当用来处理有腐蚀性介质时,则需用耐腐蚀材料来制造反应釜,或者将反应釜内表搪瓷、衬瓷板或橡胶。
(二)搅拌装置
在反应釜中,为加快反应速率、加强混合及强化传质或传热效果等,一般都装有搅拌装置。它由搅拌器和搅拌轴组成,用联轴器与传动装置连成一体。搅拌器形式很多,应根据工艺要求来选择,下面介绍几种常用搅拌器的形式、结构和特点。
1.桨式搅拌器
图2-52所示的桨式搅拌器由桨叶、键、轴环、竖轴所组成。桨叶一般用扁钢或角钢制造,当被搅拌物料对钢材腐蚀严重时,可用不锈钢或有色金属制造,也可采用钢制桨叶的外面包覆橡胶、环氧树脂或酚醛树脂、玻璃钢等材质。桨式搅拌器的转速较低,一般为20~80r/min,圆周速度在1.5~3m/s范围内比较合适。桨式搅拌器直径取反应釜内径Di的1/3~2/3,桨叶不宜过长,因为搅拌器消耗的功率与桨叶直径的五次方成正比。桨式搅拌器的最新标准为HG/T 2051.4—2013《搪玻璃搅拌器 桨式搅拌器》。当反应釜直径很大时采用两个或多个桨叶。

图2-52 桨式搅拌器
1—桨叶;2—键;3—轴环;4—竖轴
桨式搅拌器适用于流动性大、黏度小的液体物料,也适用于纤维状和结晶状的溶解液,如果液体物料层很深时可在轴上装置数排桨叶。
2.框式和锚式搅拌器
图2-53为框式搅拌器,图2-54为锚式搅拌器。框式搅拌器可视为桨式搅拌器的变形,即将水平的桨叶与垂直的桨叶连成一体成为刚性的框子,其结构比较坚固,搅动物料量大。如果这类搅拌器底部形状和反应釜下封头形状相似时,通常称为锚式搅拌器。

图2-53 框式搅拌器

图2-54 锚式搅拌器
锚式搅拌器制造方法较多,一种是用扁钢或角钢弯制,搅拌叶之间、搅拌叶与轴套之间全部焊接;另一种是做成可拆卸式的搅拌器,用螺栓来连接各搅拌叶,检修时可拆卸。特殊情况下可采用整体铸造或管材焊制,如铸铁搅拌器和搪玻璃搅拌器。
框式搅拌器直径较大,一般取反应器内径的2/3~9/10,线速度约0.5~1.5m/s,转速范围约为50~70r/min。钢制框式搅拌器最新标准为HG/T 2051.2—2013《搪玻璃搅拌器 框式搅拌器》。框式搅拌器与釜壁间隙较小,有利于传热过程的进行,快速旋转时,搅拌器叶片所带动的液体把静止层从反应釜壁上带下来;慢速旋转时,有刮板的搅拌器能产生良好的热传导。这类搅拌器适用于大多数的反应过程,有利于传质与传热。
3.推进式搅拌器
图2-55是推进式搅拌器,常用整体铸造,加工方便,采用焊接时,需模锻后再与轴套焊接、加工较困难。因推进式搅拌器转速高,制造时要做静平衡试验。搅拌器可用轴套以平键(或紧固螺钉)与轴固定。推进式搅拌器通常为两个搅拌叶,第一个桨叶安装在反应釜的上部,把液体或气体往下压;第二个桨叶安装在下部,把液体往上推。搅拌时能使物料在反应釜内循环流动,所起作用以容积循环为主,剪切作用较小,上下翻腾效果良好。当需要有更大的流速时,反应釜内设有导流筒。
推进式搅拌器直径约取反应釜内径Di的1/4~1/3,线速度可达5~15m/s,转速范围为300~600r/min,搅拌器的材料常用铸铁和铸钢。推进式搅拌器的最新标准为HG/T 3796.8—2005 《推进式搅拌器》。

图2-55 推进式搅拌器
4.涡轮式搅拌器
涡轮式搅拌器有很多,图2-56为圆盘式。桨叶又分为平直叶和弯曲叶两种。搅拌叶一般与圆盘焊接(或以螺栓连接),圆盘焊在轴套上。搅拌器用轴套以平键和销钉与轴固定。涡轮式搅拌器的主要优点是当能量消耗不大时,搅拌效率较高,搅拌时液体流动的方向如图2-57所示。因此它适用于乳浊液、悬浮液等的搅拌。
涡轮式搅拌器速度较大,线速度约为3~8m/s,转速范围为300~600r/min,开启涡轮式搅拌器的最新标准为HG/T 3796.4—2005《开启涡轮式搅拌器》。

图2-56 圆盘式涡轮式搅拌器

图2-57 涡轮搅拌时液流的方向
5.特殊形式搅拌器
图2-58为一种螺带式搅拌器,常用扁钢按螺旋形绕成,直径较大,常做成几条紧贴釜内壁,与釜壁的间隙很小,所以搅拌时能不断地将粘于釜壁的沉积物刮下来。对黏稠物料,采用行星传动的搅拌器,如图2-59所示。行星搅拌器的优点是搅拌强度很大,被旋转部分带动搅拌的物料体积很大,缺点是结构复杂。上述两种搅拌器目前使用较少。

图2-58 螺带式搅拌器

图2-59 行星搅拌器
(三)轴封
在反应釜中使用的轴封装置为动密封结构,主要有填料密封和机械密封两种,前者使用普遍,有丰富的使用经验,后者的使用范围已日趋广泛。
1.填料密封
填料密封结构如图2-60所示,填料箱由箱体、填料、油环、衬套、压盖和压紧螺栓等零件组成,旋转压紧螺栓时,压盖压紧填料,使填料变形并紧贴在轴表面上,达到密封目的。在石油化工生产中,轴封容易泄漏,一旦有毒气体逸出会污染环境,因而需控制好压紧力。压紧力过大,轴旋转时轴与填料间摩擦增加,会使磨损增大,在填料处定期加润滑剂,可减少摩擦,并能减少因螺栓压紧力过大而产生的摩擦发热。填料要富于弹性,有良好的耐磨性和导热性。填料的弹性变形要大,使填料紧贴转轴,对转轴产生收缩力,同时还要求填料有足够的圈数。使用中由于磨损应适当增补填料,调节螺栓的压紧力,以达到密封效果。填料压盖要防止歪斜,压盖的内径与轴的间隙为0.75~1.0mm。有的设备在填料箱处设有冷却夹套,可防止填料摩擦发热。

图2-60 填料密封
1—箱体;2—填料;3—油环;4—衬套;5—压盖;6—压紧螺栓
2.机械密封
机械密封在反应釜上已广泛应用,它的结构和类型繁多,但它们的工作原理和基本结构都是相同的。图2-61是一种结构比较简单的釜用机械密封装置。

图2-61 机械密封
1—弹簧座;2—弹簧;3—压盖;4—动环;5—静环;6—静环压盖;7—釜顶法兰
机械密封包括弹簧加荷装置、动环、静环及辅助密封圈等四个部分。机械密封工作原理如图2-61所示,机械密封一般有四个密封面,A处是静环座和设备之间的密封,是静密封,采用一般垫片就可以密封;B处是静环与静环座之间的密封,也是静密封,通常采用具有弹性的辅助密封圈来防止泄漏;D处是动环与轴(或轴套)之间的密封,这也是一个相对静止的密封,常用O形圈来密封。上述三处密封均是静密封,可以采取措施,防止泄漏。图2-61中C处是动环和静环间相对旋转时的密封,属于动密封,是依靠弹簧加荷装置和介质压力,在相对运转时使动环和静环的接触面(端面)上产生一个合适的压紧力,使这两个光洁、平直的端面紧密贴合,端面间维持一层极薄的流体膜(这层膜起着平衡压力和润滑端面的作用)而达到密封目的。
机械密封安装要点如下:
(1)动环与静环端面之间,初次启动时应加润滑剂,用手轻盘车,使端面形成油膜,防止干摩擦烧毁静(或动)环。
(2)油槽内油面高于静环面,在运转状态下,机械密封油槽应不产生连续小气泡。
(3)端面比压要调节适当,不可任意改变弹簧规格。
(4)在运转状态下,防止轴摆动量过大,静环端面对轴线允许垂直度误差小于0.05mm(主轴转速在200r/min以下)。
三、反应釜的生产维护
(一)维护
1.传动装置
反应釜用的搅拌器都有一定的转速要求,常用电动机通过减速器带动搅拌器转动。减速器为立式安装,要求润滑良好、无振动、无泄漏、长期稳定运转,因此日常的维护是很重要的。减速器的润滑如表2-8所示。
表2-8 减速器的润滑

减速器在转动时如发生振动,一般有以下原因,应及时检查并调整。
(1)釜内负荷过大或加料不均匀。
(2)齿轮中心距或齿轮侧隙不合适。
(3)齿轮表面加工精度不符合要求。
减速器试车中温升超过规定指标时,一般原因如下:
(1)轴弯曲变形。
(2)齿轮啮合间隙过小;轴套与轴配合过紧。
(3)密封圈或填料与轴配合过紧。
(4)轴承安装间隙不合适,轴承磨损或松动。
(5)润滑油质量不好;油量不足或断油。
2.搅拌器
搅拌器是反应釜中的主要部件,在正常运转时应经常检查轴的径向摆动量是否大于规定值。搅拌器不得反转,与釜内的蛇管、压料管、温度计套管之间要保持一定距离,防止碰撞。定期检查搅拌器的腐蚀情况,检查有无裂纹、变形和松脱。有中间轴承或底轴瓦的搅拌装置,定期检查项目如下:
(1)底轴瓦(或轴承)的间隙。
(2)中间轴承的润滑油是否有物料进入而损坏轴承。
(3)固定螺栓是否松动,松动会使搅拌器摆动量增大,引起反应釜振动。
(4)搅拌轴与桨叶的固定要保证垂直,其垂直度允许偏差为桨叶总长度的4/1000,且不大于5mm。
3.壳体(或衬里)检测
壳体(或衬里)的检测有以下几种。
(1)宏观检查 将壳体(或衬里)清洗干净,用肉眼或五倍放大镜检查腐蚀、变形、裂纹等缺陷。
(2)无损检测法 将被测点除锈、磨光,用超声波测厚仪的探头与被测部位紧密接触(接触面可用机油等液体作耦合剂)。利用超声波在同一种均匀介质中传播时,声速是一个常数,而遇到不同介质界面时,具有反射的特性,通过仪器可用数码直接反映出来,并可测出该部位的厚度。
(3)钻孔实测法 当使用仪器无法测量时,采用钻孔方法测量。可用手电钻钻孔实际测量厚度,测后应补焊修复。对用铸铁、低合金高强度钢等可焊性差的材料制作的容器,不宜采用本法测厚。
(4)测定壳体内、外径 对于铸造的反应釜,内、外径经过加工的设备,在使用过程中,发生的腐蚀属于均匀腐蚀。测量壳体内、外径实际尺寸,并查阅技术档案,来确定设备减薄程度。
(5)气密性检查 主要对衬里而言,在衬里与壳体之间通入空气或氨气,其压力为0.03~0.1MPa(压力大小视衬里的稳定性而定),通入空气时可用肥皂水涂于焊缝或腐蚀部位,检查有无泄漏;通入氨气时,可在焊缝和被检查的腐蚀部位贴上酚酞试纸,在保压5~10min后,以试纸上不出现红色斑点为合格。
(二)维护要点
1.常规维护要点
(1)反应釜在运行中,严格执行操作规程,禁止超温、超压。
(2)按工艺指标控制夹套(或蛇管)及反应器的温度。
(3)避免温差应力与内压应力叠加,使设备产生应变。
(4)要严格控制配料比,防止剧烈反应。
(5)要注意反应釜有无异常振动和声响,如发现故障,应检查修理并及时消除故障。
2.搪玻璃反应釜在正常使用中的注意事项
(1)加料要严防金属硬物掉入设备内,运转时要防止设备振动,检修时按GB 25025—2010《搪玻璃设备技术条件》执行。
(2)尽量避免冷罐加热料和热罐加冷料,严防温度骤冷骤热。搪玻璃耐温剧变小于120℃。
(3)尽量避免酸碱液介质交替使用,否则,将会使搪玻璃表面失去光泽而腐蚀。
(4)严防夹套内进入酸液(如果清洗夹套一定要用酸液时,不能用pH<2的酸液),酸液进入夹套会产生氢效应,引起搪玻璃表面像鱼鳞片一样大面积脱落。一般清洗夹套可用2%的次氯酸钠溶液,最后用水清洗夹套。
(5)出料釜底堵塞时,可用非金属棒轻轻疏通,禁止用金属工具铲打。对粘在罐内表面上的反应物料要及时清洗,不宜用金属工具,以防损坏搪玻璃衬里。
(三)常见故障与处理方法
反应釜常见故障与处理方法如表2-9所示。
表2-9 常见故障与处理方法

四、反应釜的检修
(一)反应釜检修前的准备
凡进入装有易燃、易爆、有毒、有窒息性物质的釜内检修时,首先应该做到以下几点:
(1)切断外接电源,挂上“禁动”警告牌。
(2)排除釜内的压力。
(3)在进料、进气管道上安装盲板。
(4)清洗置换,经气体分析合格后(设有专人监护),方可进入釜内。
(二)反应釜的检修项目
反应釜检修项目包括:
(1)减速器检修。
(2)釜体检修。
(3)密封装置检修。
(三)反应釜的检修质量标准
1.传动装置
反应釜的传动装置一般采用行星摆线针齿减速器,其质量标准可参照《行星摆线针轮减速机维护检修规程》规定执行。
2.密封装置
(1)填料密封
①填料压盖与填料箱的配合为G7/a11。
②填料压盖孔与搅拌轴的间隙为0.75~1.0mm(轴径为50~110mm)。
③填料压盖的端面与填料箱端面间距应相等,间距允许偏差为±0.3mm。
④填料应充填均匀,盘根填料应等轴径绕制,开口准确,每层交叉放置,防止接至同一方位上重叠。
(2)机械密封
①机械密封端面比压要适当,不可任意改变弹簧的规格。
②静环端面对轴线垂直度允差小于0.05mm(转速在200r/min以下)。
③设备进行水压试验时,密封处的泄漏量不超过10mL/h为合格。
④设备进行气密性试验时,在转动状态下,机械密封的油槽应不产生连续小气泡为合格。
3.搅拌装置
(1)在密封处轴的径向摆动量:机械密封不大于0.5mm,填料密封如表2-10所示。
表2-10 填料密封处轴的径向摆动量

注:1kgf/cm2=98.0665kPa。
(2)轴的直线度偏差应不大于0.1mm/1000mm。
(3)搅拌扭转角建议控制在0.25°~0.5°/m。
(4)搅拌轴与桨叶垂直,其允许偏差为桨叶总长度的4/1000,且不超过5mm。
(5)转速高于200r/min的涡轮式、推进式搅拌器做静平衡后方可使用。
(6)涡轮式、推进式搅拌器的叶轮与搅拌轴的配合应采用H7/js6。
(7)轴套的轴径与配合间隙应如表2-11所示。
表2-11 轴套的轴径与配合间隙

(四)反应釜的试车与验收
1.试车前的准备
(1)设备检修记录齐全,新装设备及更换的零部件均应有质量合格证。
(2)按检修计划任务书检查计划完成情况,并详细复查检修质量,做到工完、料净、场地清,零部件完整无缺,螺栓牢固。
(3)检查润滑系统、水冷却系统畅通无阻。
(4)检查电动机、主轴转向应符合设计规定。
2.试车
空载试车应满足以下要求:
(1)转动轻快自如,各部位润滑良好。
(2)机械传动部分应无异常杂音。
(3)搅拌器与设备内加热蛇管、压料管、温度计套管等部件应无碰撞。
(4)釜内的衬里不渗漏、不鼓包,内蛇管、压料管、温度计套管牢固可靠。
(5)电动机、减速器温度正常,滚动轴承温度应不超过70℃,滑动轴承温度应不超过65℃。
(6)密封可靠,泄漏符合要求;密封处的摆动量不应超过规定值。
(7)电流稳定,不超过额定值,各种仪表灵敏好用。
(8)空载试车后,应进行水试车4~8h,加料试车应不少于一个反应周期。
3.验收
试车合格后按规定办理验收手续,移交生产。验收技术资料应包括如下内容:
(1)检修质量及缺陷记录。
(2)水压试验、气密性试验及液压试验记录。
(3)主要零部件的无损检验报告。
(4)更换零部件的清单。
(5)结构、尺寸、材质变更的审批文件。