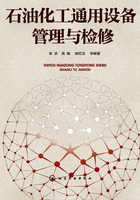
第五节 干 燥 设 备
一、干燥设备概述
干燥操作的目的是除去某些固体原料、半成品及成品中的水分或溶剂,以便于储存、运输、加工和使用。去湿是用热能加热物料,使物料中湿分蒸发而除去,这一过程称为干燥,是除去固体物料中湿分的一种方法。在石油化工生产中,多先用机械法最大限度地去除固体物料中的湿分,再用干燥法除去剩余的湿分,最后得到合格的固体产品。
1.干燥器按操作方法分类

2.干燥器按供热方法分类

(1)固定床干燥器结构如图2-62所示。图2-62中,虚线表示脉冲流。

图2-62 固定床干燥器结构图
1—干燥剂进口;2—干燥剂出口;3—干燥物料进口;4—干燥物料出口;5—加热介质(蒸汽)
(2)自由降落床干燥器结构如图2-63所示。

图2-63 自由降落床干燥器结构图
1—干燥剂进口;2—干燥剂出口;3—干燥物料进口;4—干燥物料出口
3.石化工业中的干燥方法
石化工业中的干燥方法主要有三类:机械除湿法、加热干燥法、化学除湿法。
(1)机械除湿法 是用压榨机对湿物料加压,将其中一部分水分挤出。它只能除去物料中部分自由水分,结合水分仍残留在物料中。因此,物料经过机械除湿后含水量仍然较高,一般达不到石油化工工艺要求的较低的含水量。
(2)加热干燥法 是化学工业中常用的干燥方法,它借助热能加热物料,汽化物料中的水分。物料经过加热干燥,能够除去其中的结合水分,达到石油化工工艺上所要求的含水量。
(3)化学除湿法 是利用吸湿剂除去气体、液体和固体物料中少量的水分。由于吸湿剂的除湿能力有限,仅用于除去物料中的微量水分,石油化工生产中应用极少。
二、回转圆筒干燥器
回转圆筒干燥器是一种干燥大量物料的干燥器。由于它能使物料在圆筒内翻动、抛撒,与热空气或烟道气充分接触,干燥速度快、运转可靠、操作弹性大、适应性强、处理能力大,广泛使用于冶金、建材、轻工等行业。在石油化工行业中,硫酸铵、硫化碱、安福粉、硝酸铵、尿素、草酸、重铬酸钾、聚氯乙烯、二氧化锰、碳酸钙、磷酸铵、硝酸磷肥、钙镁磷肥、磷矿等的干燥,大多使用回转圆筒干燥器。
(一)回转圆筒干燥器的工作原理
回转圆筒干燥器结构如图2-64所示。需要干燥的湿物料由皮带运输机或装斗式提升机送到料斗,然后经加料机构通过加料管进入进料端。加料管的斜度要大于物料的休止角,以便物料顺利进入干燥器内。干燥器圆筒是一个与水平线略成倾斜的旋转圆筒。物料自较高一端加入,载热体也由此端进入,与物料呈并流接触;也有载热体与物料呈逆流接触的。随着圆筒的转动,物料受重力作用向较低的一端移动。湿物料在筒内前移过程中,直接或间接得到了载热体的给热,使湿物料得以干燥。干物料卸出后,经皮带运输机或螺旋输送机送出。在圆筒内壁上装有抄板,抄板将物料抄起来又洒落,使物料与气流的接触表面增大,以提高干燥速率并促使物料前移。载热体一般为烟道气、热空气或水蒸气(在间接式加热时用)等。湿物料被蒸出的水蒸气混入烟道气内。烟道气排出干燥器后,一般需经旋风分离器将气体中所夹带的细粉捕集下来。如需进一步减少尾气含尘量,还应经过袋式除尘器或湿式除尘器后再放空。

图2-64 回转圆筒干燥装置
1—燃烧炉(或载热体加热器);2—定量给料器;3—湿料输送机;4—料斗;5—回转干燥器;6,12—膨胀环;7—斗式提升机;8—旋风除尘器;9—袋式除尘器(或湿式除尘器);10—引风机;11—尾气排空烟囱
回转圆筒干燥器一般适用于颗粒状、片状、块状物料的干燥,也可通过部分掺入干物料的办法,用来干燥黏性膏状物料或含水量较高的物料,并已成功地用于溶液物料(料浆)的造粒干燥中。
(二)直接传热转筒干燥器
直接传热转筒干燥器内载热体(如烟道气或干净热空气)以对流的方式将热量传递给与其直接接触的湿物料表面,在石油化工、建材行业使用很广泛。直接传热转筒干燥器如图2-65所示。湿物料与载热体的流向有并流或逆流两种。并流式是热风与物料同方向移动,即使入口处热风温度较高,因物料处于表面蒸发阶段,故物料温度仍然大致保持湿球温度;出口端的物料处于温度上升阶段,但因热风温度已下降,故产品的温度升高也有限,因此,即使用较高的热风温度,也不致损坏产品的质量。逆流式适用于将干燥产品加热到某一温度的场合,可以使产品含湿量很低。

图2-65 直接传热转筒干燥器
1—空气出口;2—加料口;3—托轮与挡轮;4—腰齿轮;5—传动齿轮;6—产品;7—抄板;8—密封环;9—加热器
(三)复式传热转筒干燥器
复式传热转筒干燥器一部分热量由载热体通过金属壁传给被干燥物料,另一部分热量则由干燥介质直接与物料接触而传递,是传导和对流两种传热形式的组合,热利用率较高。复式传热干燥器由内外两个圆筒构成。被干燥物料沿着内外圆筒的环形空间移动;热风先穿过内筒,然后折回穿过环形空间而与物料相接触。因此,物料一方面接受由中心管以热传导形式传递的热量,另一方面又接受以对流形式传递的热量。图2-66为复式传热转筒干燥器的结构示意。

图2-66 复式传热转筒干燥器
1—燃烧炉;2—排风机;3—外转筒;4—十字形管
(四)回转圆筒干燥器的操作和维护
回转圆筒干燥器在操作时应当控制好进料量的多少、进气温度的高低和风量的大小等,应按规定的最佳操作条件进行操作。否则,如进料量多、气体温度低、风量小都可能使物料达不到要求的干燥程度;如进料量少、气体温度高、风量大,就有可能使物料过热,并且浪费热能。
回转圆筒干燥器常见故障及处理方法如表2-12所示。
表2-12 回转圆筒干燥设备的常见故障与处理方法

三、流化床干燥器
在一个干燥设备中,将颗粒物料堆放在分布板上,当气体由设备下部通入床层,随着气流速度加大到某种程度,固体颗粒在床层内就会产生沸腾状态,这种床层称为流化床。采用这种方法进行物料干燥称为流化床干燥。
(一)流化床干燥的原理
流化床干燥是流化技术在干燥方面的应用,如图2-67(a)所示。颗粒状物料由床侧加料器加入,热气流由底部进入,通过多孔分布板与物料接触,当气流速度达到一定时,就会将物料颗粒吹起,并且使颗粒在气流中做不规则跳动,互相混合和碰撞。此时的气流速度称为临界速度。如果气流速度再增大,物料颗粒就会被气流带走,此时的速度称为带走速度。反之,若气流速度减小,物料颗粒就会下落。因此,流化床干燥器的气流速度应控制在临界速度范围内。
在流化床干燥过程中,气体激烈地冲动着固体颗粒,这种冲动速度具有脉冲性质,其结果就大大强化了传热和传质的过程。在流化床内传热和传质是同时发生的。图2-67(b)为两层沸腾床干燥器的结构,湿物料由第一层上方加入,热气流由筒底送入,与物料颗粒逆向接触。物料颗粒在第一层被干燥后经溢流管降入第二层,干、湿物料颗粒在每一层内部都相互混合,但层与层则不相互混合。由于第二层上的干物料是与温度较高、湿度较小的入口热气流接触,物料颗粒的最终含水量比单层流化床干燥器低。热气通过第二层干物料层后,进入第一层与含水量较高的进口湿物料接触,因此它在排出时的温度比单层的低,湿度比单层的高。这样便增大了热的利用率,节省了能源。

图2-67 流化床干燥器
(二)流化床的特点和分类
1.特点
(1)颗粒与热干燥介质在沸腾状态下进行充分的混合与分散,减少了气膜阻力,而且气固接触面积相当大,其体积传热系数一般在2300~7000W/(m3·K)范围内。
(2)由于流化床内温度均一并能自由调节,故可得到均匀的干燥产品。
(3)物料在床层内的停留时间一般为几分钟至几小时(有的只有几秒钟),可任意调节,故对难干燥或要求干燥产品含湿量低的物料特别适用。
(4)由于体积传热系数大,干燥强度大,故在小装置中可处理大量的物料。
(5)结构简单,造价低廉,没有高速转动部件,维修费用低,物料由于流化而输送简便。
(6)对于散粒状物料,其粒径与形状有一定的限制,如粒径范围为20~30μm至5~6mm是适宜的,形状以类似球形为佳。
2.分类
(1)按被干燥的物料分类 有散粒状物料、膏糊状物料、溶液和悬浮液等具有流动性物料。
(2)按操作情况分类 流化床可分为间歇式和连续式。
(3)按设备结构型式分类 流化床可分为单层流化床干燥器、多层流化床干燥器、卧式多室流化床干燥器、振动流化床干燥器、喷动床干燥器、惰性粒子流化床干燥器等,此外,还有带搅拌桨的以及内置热传导装置的流化床干燥器。
(三)单层和卧式多室流化床干燥器
单层和卧式多室流化床干燥器如图2-68所示。它适用于干燥各种难以干燥的粒状物料、热敏性物料,并逐渐扩展到粉状、小块状等物料。散粒状物料往往是经造粒机制成4~14目的大小,初始含湿量一般在10%~30%,干燥后的终湿量一般在0.02%~0.3%。当被干燥的物料在80~100目或更细小时,如聚氯乙烯,则干燥器上部需加以扩大,以减少细粉夹带,其分布板的孔径及开孔率也相应减小,以改善流化状态。

图2-68 单层和卧式多室流化床干燥器
1—引风机;2—卸料管;3—干燥器;4—旋风分离器;5—袋式分离器;6—摇摆颗粒机;7—空气过滤器;8—加热器
干燥器为一长方形箱式流化床,底部为多孔筛板,开孔率一般为4%~13%,孔径为1.5~2.0mm。筛板上方,按一定间距设置隔板,构成多室。隔板可以是固定的,或活动的(可上下移动),以调节其与筛板的间距。由于设置了与颗粒移动方向垂直的隔板,既防止了未干燥颗粒的排出,又使物料的滞留时间趋于均匀。每一小室的下部有一进气支管,支管上有调节气体流量的阀门。
湿物料连续加入到干燥器的第一室,床层中的颗粒借助于床层位差,通过流化床分布板与隔板之间的间隙向出口侧移动,被干燥的物料最后通过出口堰溢流连续排出。每一个室相当于一个流化床,卧式多室相当于多个流化床串联使用。
图2-69为卧式连续多室流化床干燥器,它将干燥后的细粉循环落到第一室,与初始进入的湿物料混合,可减少湿料结块造成的麻烦。

图2-69 卧式连续多室流化床干燥器
1—出口堰;2—隔板;3—引风机;4—旋风分离器;5—循环下料管;6—流化床分布板;7—空气加热器;8—空气过滤器;9—鼓风机
(四)多层流化床干燥器
连续多层流化床干燥器的结构与板式塔相似,如图2-70所示。一层板相当于一个流化床,湿物料自顶层加入,逐层下移,于底层排出。热空气由底部进入,向上通过各层,从顶部排出,物料与热风逆向流动。由于物料有规则地从上到下移动,停留时间分布均匀,物料的干燥程度均匀,易于控制产品质量。又由于气体与物料多次接触,所以尾气的水蒸气饱和度提高,热利用率较高。这种干燥器适用于干燥降速段的物料或产品要求含湿量很低的物料。连续多层流化床干燥器依其下料方式可分为溢流管式、穿流板式和错流式等,此外,还有多层串连式和翻板式。

图2-70 连续多层流化床干燥器
1—筒体;2—筛板;3—法兰;4—溢流装置;5—视镜;6—卸料管
(五)喷动床干燥器
喷动床干燥器如图2-71所示,其流动特征是一个向上的中心稀相流动床与一个四周向下的移动床的组合。喷动床干燥器底部为圆锥形,上部为圆筒形。气体以高速从锥底进入,夹带一部分固体颗粒向上运动,形成中央通道。在床层顶部颗粒好似喷泉一样,从中心喷出向四周散落,然后沿周围向下移动,到锥底又被上升气流喷射而上,如此循环以达到干燥的要求。
喷动床技术用途相当广泛,如干燥、造粒、冷却、混合等。喷动床技术用于干燥,根据物料特点及具体工艺要求,出现有几种形式的干燥装置。常用的喷动床干燥器有两种形式,即有分布板式和无分布板式。
图2-72(a)为无分布板式喷动床干燥器,加料口设在设备锥底的窄截面处,产品自上部圆筒形侧孔卸出,或者按干燥要求自顶部由尾气带出。在气体及物料进口的窄截面处,气流速度是大颗粒气流输送速度(即带出速度)的1.5~2.0倍。
图2-72(b)为有分布板式喷动床干燥器,物料从顶部加入,或在设备锥形底部靠近分布板处加入,产品通过锥形体处侧孔卸出,或在圆筒体处侧孔卸出。窄截面处气速接近于颗粒的带出速度,但在宽截面处则取最佳流化速度。

图2-71 喷动床干燥器结构示意

图2-72 喷动床干燥器
四、喷雾干燥器
喷雾干燥是采用雾化器将物料分散为雾滴,并用热干燥介质(通常为空气)直接将雾滴干燥成固体产品的一种干燥方法。料液可以是溶液、乳浊液或是悬浮液,也可以是熔融物、膏状物或滤饼。产品根据需要可制成粉体、颗粒、空心球或团粒。经过几十年的研究与实践,喷雾干燥技术已比较成熟,设备尺寸的计算与确定也有可靠的方法。
(一)喷雾干燥的工作原理
将溶液、乳浊液、悬浮液或浆料在热风中喷雾成细小的液滴,在它下落过程中,水分被蒸发而成为粉末状或颗粒状的产品,称为喷雾干燥。
喷雾干燥的原理如图2-73所示,在干燥塔顶部导入热风,同时将料液泵送至塔顶,经过雾化器喷成雾状的液滴,这些液滴群的表面积很大,与高温热风接触后水分迅速蒸发,在极短的时间内便成为干燥产品,从干燥塔底部排出。热风与液滴接触后温度显著降低,湿度增大,作为废气由排风机抽出。废气中夹带的微粉用分离装置回收。

图2-73 喷雾干燥原理示意图
(二)喷雾干燥器的维修
几种喷雾干燥的常见故障及处理方法如表2-13所示。
表2-13 喷雾干燥器常见故障及处理方法
