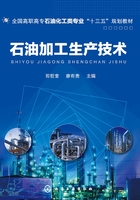
第二节 石油产品的使用要求
一、石油产品的分类
石油产品的种类繁多,用途各异,为了与国际标准相一致,我国参照ISO(国际标准化组织)发布的国际标准ISO/DIS 8681,制定了GB/T 498—2014《石油产品及润滑剂 分类方法和类别的确定》,将石油产品和有关产品总分类分为五类, 总分类列于表1-5中。
表1-5 石油产品和有关产品总分类

1.燃料
燃料包括汽油、喷气燃料、柴油等发动机燃料及灯用煤油、燃料油等。我国燃料占石油产品的85%左右,而其中约60%为各种发动机燃料,是用量最大的产品。按照GB/T 12692.1—2010《石油产品 燃料(F类)分类 第一部分:总则》将石油燃料分为五组,见表1-6。
表1-6 石油燃料的分组

新制定的产品标准,把每种产品分为优级品、一级品和合格品三个质量等级,每个等级根据使用条件的不同,还可以分为不同牌号。
2.润滑剂
润滑剂包括润滑油和润滑脂,主要用于降低机件之间的摩擦和防止磨损,以减少能耗和延长机械寿命。其产量不多,仅占石油产品总量的2%~5%,但品种和牌号却是最多的一大类产品。
3.石油沥青
石油沥青用于道路、建筑及防水等方面,其产品占石油产品总量的2%~3%。
4.石油蜡
石油蜡属于石油中的固态烃类态物质,是轻工、化工和食品等工业部门的原料,其产量约占石油产品总量的1%。
5.石油焦
石油焦可用以制作炼铝及炼钢用电极等,其产量为石油产品总量的1%~2%。
6.溶剂和石油化工原料
约有10%的石油产品用作石油化工原料和溶剂,其中包括制取乙烯的原料(轻油)以及石油芳烃和各种溶剂油。
二、石油燃料的使用要求
燃料的使用要求在于满足机械工作过程的要求,主要体现在安全、环保、经济、可靠等方面。在石油燃料中,用量最大、最重要的是汽油、喷气燃料、柴油等。其用途包括:
①点燃式发动机燃料——汽油,主要用于各种汽车、摩托车和活塞式飞机发动机等;
②喷气发动机燃料——喷气燃料,主要用于各种民用和军用喷气发动机;
③压燃式发动机燃料——柴油,用于各种大马力载重汽车、坦克、拖拉机、内燃机车和船舰等。
不同使用场合对所用燃料提出了相应的质量要求。产品质量标准的制定是综合考虑产品使用要求、所加工原油的特点、加工技术水平及经济效益等因素,经一定标准化程序,对每一种产品制定出相应的质量标准(俗称规格),作为生产、使用、运销等各部门必须遵循的具有法规性的统一指标。
(一)汽油机和柴油机的工作过程
汽油和柴油的使用要求主要取决于汽油机和柴油机的工作过程,汽油机以四冲程汽油机为例, 见图1-2,柴油机的原理构造见图1-3,均包括进气、压缩、燃烧膨胀做功、排气四个过程,活塞在发动机气缸中往复运动二次,曲柄连杆机构带动飞轮在发动机中运行一周。但柴油机和汽油机的工作原理有两点本质的区别:第一,汽油机中进气和压缩的介质是空气和汽油的混合气,而柴油机中进气和压缩的只是空气,而不是空气和柴油的混合气,因此柴油发动机压缩比的设计不受燃料性质的影响,可以设计得比汽油机高许多,一般柴油机的压缩比可达13~24,汽油机的压缩比受燃料性质的限制,一般只有6~8.5;第二,在汽油机中燃料是靠电火花点火而燃烧的,而在柴油机中燃料则是由于喷散在高温高压的热空气中自燃的。因此,汽油机称为点燃式发动机,柴油机则叫作压燃式发动机。
柴油发动机和汽油发动机相比,单位功率的金属耗量大,但热功效率高,耗油少,耗油率比汽油机低30%~70%,并且使用来源多而成本低的较重馏分——柴油作为燃料,所以大功率的运输工具和一些固定式动力机械等都普遍采用柴油机。在我国除应用于拖拉机、大型载重汽车、排灌机械等外,在公路运输、铁路运输上和轮船、军舰上也越来越广泛地采用柴油发动机。

图1-2 四冲程汽油机示意图

图1-3 柴油机的原理构造图
1—油箱;2—初滤清器;3—输油泵;4—细滤清器;5—高压油泵;6—喷油嘴;7—空气滤清器;8—进气管;9—气缸;10—活塞;11—进气阀;12—排气阀;13—排气管;14—消声器
(二)车用汽油的使用要求
汽油是用作点燃式发动机燃料的石油轻质馏分,对汽油的使用要求主要有以下几点。
①在所有的工况下,具有足够的挥发性以形成可燃混合气。
②燃烧平稳,不产生爆震燃烧现象。
③储存安定性好,生成胶质的倾向小。
④对发动机没有腐蚀作用。
⑤排出的污染物少。
汽油按其用途分为车用汽油和航空汽油,各种汽油均按辛烷值划分牌号。车用汽油按其辛烷值(RON)分,目前划分为89号、92号及95号三个牌号,它们分别适用于压缩比不同的各型汽油机。我国车用汽油的质量标准对比见表1-7。
航空汽油分为100号、95号和75号三个牌号。100号及95号航空汽油用于有增压器的大型活塞式航空发动机,75号航空汽油用于无增压器的小型活塞式航空发动机。
表1-7 车用汽油(Ⅴ)标准与车用汽油(Ⅵ)标准对比(GB 17930—2016)

注:车用汽油(Ⅴ)标准2019年1月1日起废止,车用汽油(ⅥA)标准2019年1月1日起执行,车用汽油(ⅥA)标准2023年1月1日起废止,车用汽油(ⅥB)标准2023年1月1日起执行。
1.蒸发性
车用汽油是点燃式发动机的燃料,它在进入发动机气缸之前必须在化油器中汽化并同空气形成可燃性混合气。汽油在化油器中蒸发得是否完全,同空气混合得是否均匀,与它的蒸发性有关。
(1)蒸发性能的评定指标
馏程和蒸气压是评价汽油蒸发性能的指标。
汽油的馏程可用BSY-103ⅡA蒸馏测定仪(图1-4)进行测定,得到恩氏蒸馏数据,可测出汽油的初馏点及10%馏出温度、50%馏出温度、90%馏出温度和终馏点,各点温度与汽油使用性能关系十分密切。

图1-4 BSY-103ⅡA蒸馏测定仪结构(符合国家标准GB/T 6536)
1—温控仪表;2—冷凝管出口;3—注水孔;
4—温度计;5—蒸馏烧瓶;
6—观察窗;7—电源开关;8—电压调节;9—电炉电压;10—电炉升降
(2)汽油蒸发性的要求
汽油的初馏点和10%馏出温度反映了汽油的启动性能,我国规定车用汽油10%馏出温度不大于70℃。此温度过高,说明汽油内轻组分的含量不够大,发动机不易启动。
50%馏出温度反映了发动机的加速性和平稳性,我国车用汽油的50%馏出温度不大于120℃。此温度过高,发动机不易加速,当行驶中需要加速时,汽油就会来不及完全燃烧,致使发动机不能产生应有的功率。
90%馏出温度(不大于190℃)和终馏点(不大于205℃)反映了汽油在气缸中蒸发的完全程度。此温度过高,说明汽油中重组分过多,使汽油汽化燃烧不完全,这不仅增大了汽油耗量,使发动机功率下降,而且会造成燃烧室结焦和积炭,影响发动机正常工作。另外,还会稀释和冲掉气缸壁上的润滑油,增加机件的磨损。
2.抗爆性
汽油的抗爆性表明了汽油在气缸中的燃烧性能,是汽油的最重要的使用指标之一。它说明汽油能否保证在具有相当压缩比的发动机中正常工作,这对提高发动机的功率,降低汽油的消耗量等都有直接的关系。
(1)汽油机的爆震
爆震是汽油在汽油机中的一种不正常燃烧。正常情况下,发动机压缩终了时的混合气温度达300~450℃,压力达7×105~15×105Pa,此时气体中的烃类被氧化并生成一些过氧化物,经火花塞点燃后,火焰呈球面状以30~70m/s的速度向四周扩散,此时火焰经过的区域,温度、压力均衡上升,活塞工作正常。在某些情况下,当火花塞点燃混合气后,在火焰尚未传播到的混合气中,因受高温高压影响已形成大量自燃点较低的过氧化合物,在多个部位猛烈自燃,出现许多燃烧中心,同时燃烧是以爆炸方式进行,使火焰速度高达1500~2500m/s,温度、压力剧增,形成冲击波,如同重锤敲击活塞和气缸各部件,发出金属撞击声,此时由于火焰瞬间经过,使得某些部位的燃料燃烧不完全,排出带黑烟废气,此即爆震现象。爆震会损坏气缸部件,缩短发动机寿命,增加油耗量。
(2)产生爆震的原因
①主要是与汽油的化学组成和馏分有关,如果汽油中含有过多容易氧化的组分,形成的过氧化物又不易分解,自燃点低,就很容易产生爆震现象。
②与发动机的工作条件和机械结构(主要是压缩比)、驾驶操作和气候条件等有关。
汽油机的压缩比越大,压缩过程终了时混合气的温度和压力就越高,这就大大加速了未燃混合气中过氧化物的生成和积聚,使其更容易自燃。一定压缩比的发动机必须使用与其相匹配辛烷值的汽油,方能保证在不发生爆震的情况下,产生最大功率。

图1-5 吸气与压缩时气缸的容积
汽油发动机的热功效率与其压缩比有关。压缩比是指气缸吸气末期时活塞移动到下止点时最大容积V1与气缸压缩末期活塞移动到上止点时最小容积V2的比值,如图1-5所示。压缩比大,汽油机的效率和经济性就好,但要求汽油要有良好的抗爆性。
(3)汽油抗爆性的表示方法
汽油的抗爆性用辛烷值表示。试样在燃烧相当的标准燃料中,异辛烷(2,2,4-三甲基戊烷)的体积分数即为该试样的辛烷值。这里的燃烧相当指的是爆震强度相当。在测定车用汽油的辛烷值时,人为选择了两种烃作为标准物:一种是异辛烷(2,2,4-三甲基戊烷),它的抗爆性好,规定其辛烷值为100;另一种是正庚烷,它的抗爆性差,规定其辛烷值为0。在相同的发动机工作条件下,如果某汽油试样的抗爆性与含92%异辛烷和8%正庚烷组成的标准混合物燃料的抗爆性相同,此汽油试样的辛烷值即为92。汽油的辛烷值越高,其抗爆性越好。辛烷值分马达法和研究法两种。马达法辛烷值(MON)表示重负荷、高转速(900r/min)时汽油的抗爆性;研究法辛烷值(RON)表示轻负荷、低转速(600r/min)时汽油的抗爆性。同一汽油的MON低于RON。一些国家还采用抗爆指数来表示汽油的抗爆性,抗爆指数等于MON和RON的平均值。我国车用汽油的商品牌号是以研究法辛烷值来划分的 (GB 7930—2016)。
(4)汽油的抗爆性与其化学组成和馏分组成的关系
汽油由烃类组成,对分子量大致相同的不同烃类,辛烷值大小顺序为:正构烷烃<环烷烃<正构烯烃<异构烷烃和异构烯烃<芳烃。含芳香烃、异构烷烃多的轻质汽油的辛烷值高。烷烃分子的碳链上分支越多,排列越紧凑,辛烷值越高。对于烯烃,双键位置越接近碳链中间位置,辛烷值越高。同族烃类,分子量越小,沸点越低,辛烷值越高。汽油的终馏点降低,辛烷值会升高。
(5)提高汽油辛烷值的途径
①改变汽油的化学组成,增加异构烷烃和芳香烃的含量。这是提高汽油辛烷值的根本方法。一是改进工艺,如采用催化裂化、催化重整、异构化等加工过程来实现。二是调整工艺操作条件,如降低汽油终馏点、改变反应温度及反应时间、强化异构化、芳构化反应等。
②加入少量提高辛烷值的添加剂(即抗爆剂)。汽油抗爆剂根据其化学性质可分为不同种类,目前常见的主要有醇类、醚类、金属类、胺类、脂类和复配类。其按应用特性又可分为金属有灰和有机无灰型。
③调入其他的高辛烷值组分,如含氧有机化合物醚类及醇类等。这类化合物常用的有甲醇、乙醇、叔丁醇、甲基叔丁基醚(MTBE)等,其中甲基叔丁基醚在近些年来更加引起人们的重视。MTBE不仅单独使用时具有很高的辛烷值(RON为117,MON为101),在掺入其他汽油中可使其辛烷值大大提高,而且在不改变汽油基本性能的前提下,可改善汽油的某些性质。
3.安定性
汽油在常温和液相条件下抵抗氧化的能力称为汽油的氧化安定性,简称安定性。安定性差的汽油易呈现颜色变深,生成黏稠胶状沉淀物。使用这类汽油时,将严重影响发动机正常工作,例如:不蒸发的胶状物会沉积在油箱、导管、滤清器、进气阀等机件上,造成堵塞,影响供油;高温下胶状物变成积炭,聚积在进气阀、气缸盖和活塞顶等部位,增大了爆震的可能性。
车用汽油安定性的评定指标有实际胶质、诱导期。
①实际胶质 实际胶质是指100mL油品在规定条件下蒸发后残留的胶状物质的质量。实际胶质用以评定车用汽油使用时在发动机中生成胶质的倾向。汽油中的胶质主要包括两种:一种是黏附物质或沉渣,不溶于溶剂,所以可以通过过滤的方法分离出来;另一种是可溶胶质,可以溶解在汽油中,通过蒸发的方法可使其作为不挥发的物质残留下来。国家标准对车用汽油的实际胶质要求是不大于5mg/100mL,通常实际胶质不大于10mg/100mL时仍可正常使用,储存的车用汽油的实际胶质通过定期测定有上升倾向时,应尽快使用。
②诱导期 诱导期是指在精确测定的温度和压力下由试样和氧接触的时间算起,至试样开始吸入氧为止的一段时间,单位为分钟(min)。诱导期的数值反映燃料内易氧化组分(如烯烃)含量的多少。烯烃含量越多,汽油越易氧化变色,烯烃又是聚合反应的活泼反应物,所以诱导期也反映了汽油生胶的倾向。国家汽油标准烯烃含量要求在逐年下降,由最初的≤35%,下降到目前国Ⅵ标准的≤18%。
航空汽油常用碘值来评定安定性,不饱和烃中的双键与碘能定量反应,因此用与100g油起反应的碘用量(gI)表示油中不饱和烃含量,称为碘值,单位为gI/100g。碘值越小,汽油安定性越好,航空汽油要求碘值不大于12gI/100g。
4.腐蚀性
汽油的腐蚀性表征汽油对金属的腐蚀能力。汽油的主要组分是烃类,任何纯烃对金属都无腐蚀作用,但若汽油中含有一些非烃杂质,如硫及含硫化合物、水溶性酸碱、有机酸等,都会对金属有腐蚀作用。
评定汽油腐蚀性的指标有硫含量、铜片腐蚀、水溶性酸碱等。
严格控制汽油硫含量,主要是因为低分子硫醇、硫化氢和单质硫(统称为活性硫化物)具有强腐蚀作用,以及硫燃烧后生成的硫氧化物污染大气,危害人体。
铜片腐蚀是用铜片直接测定油品中是否存在活性硫的定性方法。
汽油的水溶性酸碱主要是在加工、储存、运输过程中从外界进入的可溶于水的无机酸或碱。其中,水溶性酸是指低分子有机酸和无机酸,低分子有机酸是由汽油氧化生成,无机酸是油品酸碱精制过程中的残留物。水溶性碱是指氢氧化钠和碳酸钠等。水溶性酸碱是强腐蚀性物质,对所有金属都有腐蚀作用。自从加氢精制工艺大规模使用和常减压蒸馏装置的碱洗水洗工艺退役后,油品的水溶性酸碱指标有了极大改善。目前如果说汽油中有微量的碱性物质,主要是因为催化裂化汽油碱洗工艺有微量残留,随着催化裂化汽油的调和比例下降,水溶性碱含量会越来越低。
5.其他指标
(1)苯含量
苯因为分子量小而极易挥发。因为车用汽油中含有苯,因此应防止车用汽油在储运过程中挥发苯而使人体中毒,苯已经被世界卫生组织确定为强烈致癌物质。国Ⅵ标准车用汽油对苯含量的要求是≤0.8%。
炼厂生产车用汽油的最后一道工艺是调和,主要是催化重整汽油和催化裂化汽油调和。重整汽油中的苯含量相对较高,约为8%,每个炼厂因为催化重整装置原料预处理工艺各有区别,导致重整汽油中苯含量有所不同。重整汽油苯含量的升高,主要原因是预分馏塔和蒸发塔的塔顶馏分切割较轻所致,重整反应系统温度过高、空速过小也是苯含量升高的一个因素。国内炼厂相继上马的苯抽提工艺,是实现国标汽油中苯含量从最初的2.5%降低到国Ⅵ标准0.8%的重要手段。因为微量的苯也可使人体的血液循环系统中毒,所以继续降低苯含量和苯抽提工艺的普及是总体趋势。
(2)甲醇含量
20世纪90年代,国内部分地区曾出现M15的甲醇汽油,甲醇的辛烷值较高,加工成本远低于汽油,因氧含量高而易完全燃烧,对发动机尾气排放减少减轻大气污染有一定的贡献,但是甲醇与汽油容易分层而混合不均,导致发动机会在某一时刻喷出甲醇含量超过燃料的15%,加之甲醇的蒸发潜热要远大于汽油,消耗热量多而导致燃油的雾化不良,造成冷启动不良、冷车运行不良等。如果甲醇喷入发动机后如不能快速着火燃烧,未燃甲醇将沿气缸壁下流,随润滑油混入润滑系统,将对气缸、发动机所有需要润滑的部件造成磨损而导致发动机寿命减损。更为严重的是甲醇有较强的毒性,对人体的神经系统和血液系统危害很大,它经消化道、呼吸道或皮肤摄入人体都会产生毒性反应。甲醇在人体内不易排出而发生蓄积,累计达到10g就能造成双目失明、肝肾衰竭,累计达到30g就能造成死亡。鉴于甲醇的这些危害且极易挥发,国家标准GB 17930规定:甲醇的检出量不大于0.3%(质量分数),并且明确规定不得人为加入甲醇。
(3)氧含量
国家标准对汽油中氧含量的限定,主要是限制汽油添加剂(主要是醚类)的添加量,目前国内主要使用的添加剂是甲基叔丁基醚(MTBE),国家标准规定汽油的氧含量不大于2.7%,相当于MTBE的最大添加量为15%。因为MTBE热值较汽油低,会影响汽车的续航里程,且会对地下水资源造成不可逆的污染,所以随着MTBE工艺的逐渐淘汰和加氢工艺的成熟,国内汽油氧含量的控制指标基本都会达标。
(4)铁、锰含量
汽车尾气处理的三元催化器可以将有害气体转变为二氧化碳、水和氮气。铁、锰金属化合物附着在三元催化器的催化剂载体表面上,可使催化活性大大降低。关键是要减少这些金属化合物附着在载体表面的机会,这与汽油中金属的含量以及车辆使用年限有关。国家标准对车用汽油的铁、锰含量的规定是分别控制在不高于0.01g/L、0.002g/L。
(三)车用柴油的使用要求
柴油是压燃式发动机的燃料,也是目前国内消费量最大的发动机燃料。我国柴油主要分为馏分型(轻柴油及重柴油)和残渣型两类。
轻柴油:用于高速发动机(>1000r/min),按凝点划分牌号为10#、5#、0#、-10#、-20#、-35#和-50#。
重柴油:用于中速、低速(<500r/min)发动机,按黏度进行分级。
残渣型:按黏度划分牌号,主要用于船用大功率、低转速柴油机。
绝大多数的柴油适用于汽车、拖拉机、铁路机车、坦克、工程机械等压燃式柴油发动机。柴油机的使用日益广泛,是因为柴油机有较高的压缩比,热功效率高,马力大而油耗小,加速性能良好,使用保养容易,工作可靠耐久,且柴油馏程宽、加工成本低,闪点比汽油高,在使用和保管时危险性较小。
柴油机对燃料的使用要求具体表现在以下几个方面:
①具有良好的雾化性能、蒸发性能和燃烧性能;
②具有良好的燃料供给性能;
③对发动机部件没有腐蚀和磨损作用;
④具有良好的储存安定性和热安定性。
我国车用柴油的质量标准见表1-8。
表1-8 车用柴油(Ⅴ)标准与车用柴油(Ⅵ)标准对比(GB 19147—2016)

注:车用柴油(Ⅴ)标准于2019年1月1日起废止,车用柴油(Ⅵ)标准于2019年1月1日起执行。
1.柴油的燃烧性能
柴油的燃烧性能是用蒸发性和抗爆性表示的。
(1)蒸发性
柴油的蒸发性能用黏度、馏程和闪点来表示。
柴油雾化程度越好,雾化后液滴的直径越小,液滴数量越多,其蒸发总表面积就会显著增加,因而蒸发速度也就迅速增大。柴油的雾化性能与馏分组成相关,馏分较轻、黏度较小的组分雾化和蒸发速度快,有利于柴油机气缸中混合气的形成,使燃烧速度快,启动性好。
但馏分过轻易造成自燃点过高,不利于混合气自燃,易形成爆震。馏分较重的燃料在燃烧过程中易形成积炭,既增加燃料消耗量,又缩短发动机使用寿命。
柴油黏度过小,喷油量会受到限制,喷油射程近而角度大,燃烧过程基本在喷油嘴附近完成,不能充分利用气缸中所有的压缩空气,使功率下降和排烟增加。黏度过大时,使油泵抽油效率降低,减少了供油量,喷射角度小而射程远,雾化形成的油滴平均直径大,与空气混合不均匀,燃烧不完全,形成积炭。黏度过大的柴油,其运动黏度和10%蒸余物残炭数值变化趋势是同步的,10%蒸余物残炭值大,说明柴油容易在喷油嘴和气缸零件上形成积炭,导致散热不良,机件磨损加剧,缩短发动机使用寿命。
国家规定-35#、-50#轻柴油的闪点(闭杯)不低于45℃,其余牌号不低于55℃。
(2)抗爆性
柴油机在工作中也会发生类似汽油机的爆震现象,使发动机功率下降,造成机件损害,但产生爆震的原因与汽油机完全不同。汽油机的爆震是由于燃料太容易氧化,自燃点太低,而柴油机的爆震是由于燃料不易氧化,自燃点太高。因此,汽油机要求使用自燃点高的燃料,而柴油机要求使用自燃点低的燃料。
柴油的抗爆性用十六烷值来表示。柴油十六烷值是在规定操作条件下,用标准试验在单缸柴油爆震机中测定的。规定标准燃料中只含有两种成分,即正十六烷和七甲基壬烷。正十六烷具有很短的发火延长期,自燃性能好,规定其十六烷值为100,而七甲基壬烷发火延长期较长,自燃性能较差,规定其十六烷值为15。然后将这两种化合物按不同比例掺和成标准燃料,用柴油爆震机一一测定这些不同标准燃料的十六烷值,并建立数据库。标准燃料的十六烷值按下式计算:
十六烷值=100β正十六烷+15β七甲基壬烷
式中,β为体积分数。
当测试的某种燃料试样的爆震强度与某一比例标准燃料的爆震强度相当时,此时对应的标准燃料的十六烷值,即为被测燃料试样的十六烷值。
汽油的辛烷值和柴油的十六烷值,都与油品的组成及分子结构有关。汽油中馏分分子结构越复杂,支链越多,辛烷值越高。而柴油中馏分分子结构越简单,支链越少,十六烷值越高,正构烷烃的十六烷值最高,然后依次为正构烯烃、环烷烃、异构烷烃、异构烯烃,稠环芳烃的十六烷值最低。辛烷值与十六烷值的变化规律相反,与燃料在发动机内燃烧特点有关:汽油机是点燃式发动机,而柴油机是压燃式发动机。国家标准规定柴油的十六烷值:5#、0#、-10#柴油不低于51,-20#柴油不低于49,-35#、-50#柴油不低于47。
柴油的十六烷值并不是越高越好,如果柴油的十六烷值很高(如60以上),由于自燃点太低,滞燃期太短,容易发生燃烧不完全,产生黑烟,使得耗油量增加,柴油机功率下降。
2.低温流动性能
柴油的低温流动性能不仅决定着柴油机燃料供给系统能否在低温下完成供油任务,而且与柴油在低温下的储存、运输等作业能否正常进行有着密切的关系。我国评定柴油低温流动性能的指标是凝点和冷滤点。凝点是在国家标准规定的条件下,试样开始失去流动性时的温度。冷滤点是在国家标准规定的条件下,当油品通过过滤器的流量每分钟不足20mL时的最高温度。在欧洲一些国家习惯用冷滤点来确定柴油标号,我国习惯用凝点来规定柴油牌号,如5#、0#、-10#、-20#、-35#、-50#。我国南方部分地区的炼厂因为常年温度较高,会生产少量10#、20#车用柴油满足企业内部自用,因为热值较高,续航里程较长,但是要兼顾好发动机的雾化效果和90%蒸发温度、95%蒸发温度不超标。
柴油在凝固之前,已经有正构烷烃结晶析出形成骨架凝固,因此在我国-8℃的地区柴油发动机使用-10#柴油未必能正常工作,也就是说凝点并不能确切表明柴油实际使用的最低温度。冷滤点接近车用柴油发动机的使用条件,可以粗略地判断油品使用的最低温度,而凝点温度时柴油完全失去流动性,所以柴油的凝点要比冷滤点的温度更低些。
柴油凝点、冷滤点与其化学组成密切相关。当碳原子数相同时,正构烷烃熔点最高,带长侧链的芳烃、环烷烃次之,异构烷烃则最小。所以,改善柴油低温流动性的手段之一是脱除正构烷烃(即脱蜡),但是加工成本较高,一般在需要液蜡产品时会考虑通过脱蜡工艺获得低标号柴油。
除采用脱蜡生产工艺外,还可在油品中加入降凝剂,这是一种十分经济有效的方法。柴油经冷却后,油中蜡随温度下降而析出,温度越低,析出的蜡越多,致使油全部失去流动性。含蜡油品在低温下失去流动性,是由于高熔点固体烃分子定向排列,形成针状或片状结晶,并相互黏结,构成三维网状结构,将低凝点油包于其中以致失去流动性。降凝剂主要是通过其分子上烷基侧链的共晶或吸附作用,改变蜡的生长方向和晶型,使其生成均匀松散的晶粒,从而防止导致油品凝固的三维网状结晶的形成。降凝剂种类很多,但常用的是烷基芳烃化合物、聚α-烯烃和聚甲基丙烯酸酯类。聚甲基丙烯酸酯类具有梳形化学结构的功能,而致其侧链烷基和蜡形成共结晶,烷基芳烃的芳基吸附于石蜡表面而改变其结晶生长的方向,而致油中石蜡不能形成三维网状结构而防止油品凝固。降凝剂主要是降低了油品的冷滤点,而使得柴油有更广泛的使用温度范围。不同的柴油对降凝剂的感受性不同,降凝的效果也会有所不同,正构烷烃含量少或正构烷烃在油品中分散性好的柴油,使用降凝剂的效果更为显著。
3.柴油的腐蚀性、安定性
柴油中的硫化合物在燃烧后都生成SO2和SO3,与烃类燃烧生成的水蒸气一起会在气缸壁上形成硫酸薄膜,腐蚀气缸及其他机件。SO2和SO3还能促使气缸内生成沉积物,形成硬度更高的积炭,加大对发动机的磨损破坏作用。控制柴油中的硫含量,最有效的方法是加大柴油加氢装置精制反应深度,减少原料中延迟焦化柴油的比例,或是减少成品柴油中直馏柴油的调和量。国六标准规定,车用柴油硫含量不高于10mg/kg。
影响车用柴油安定性的主要原因是油品中存在着不饱和烃,以及含硫、含氮化合物等不安定组分。评价安定性的指标主要有总不溶物和10%蒸余物残炭。总不溶物反映了柴油在受热和有溶解氧的作用下发生氧化变质的倾向。多环芳烃可以加速柴油氧化变质,其多存在于10%蒸余物残炭中。
水的存在会大大提高柴油的浊点和凝点。在零下十几摄氏度以下的环境中,水分呈微小冰晶体悬浮于柴油中,即使没有蜡结晶析出,也会影响柴油的低温流动性,堵塞柴油机油路滤清器的滤网而影响正常供油。柴油中的机械杂质主要的破坏作用是加大高压油泵、喷油嘴等机件的磨损,缩短发动机寿命。水分和机械杂质多是在储存、运输和加工过程中混入柴油的。因此,在油品罐区加大盘管加温、沉降、切水也是很有必要的,加油时应增大过滤频次和提高精细度,防止冰结晶和机械杂质进入油箱中。国六标准规定,车用柴油不得含有机械杂质,水分只允许有痕量。
三、喷气燃料
喷气燃料(旧称航空煤油或航煤),是航空飞行器喷气式发动机的燃料,喷气式发动机是在高空、低温和低气压下工作的。喷气式发动机与活塞式发动机(汽油机及柴油机)有很大区别:一是活塞式发动机的燃料供给和燃烧是周期性间断进行的,而喷气式发动机的燃料和空气同时连续进入燃烧室,燃烧过程是连续进行的;二是活塞式发动机燃料的燃烧是在密闭的空间中进行的,而喷气式发动机燃料的燃烧是在高速的气流中进行的,其燃烧速度必须大于气流速度,否则会造成火焰熄灭。喷气燃料必须要具有较大的热值和密度,实现燃烧平稳、迅速、安全,且不产生积炭,不腐蚀机件。喷气燃料的使用性能有以下几点。
1.蒸发性能
燃料的蒸气压越高,蒸发性能越强,则燃料的启动性和燃烧安全性越好,低温性能也越好。但飞机起飞爬高过程中,气压急剧降低,将会导致油箱中燃料猛烈蒸发而造成气阻,因此闪点偏低(38℃)的喷气燃料,其10%回收温度应尽量接近上限值(205℃)。用10%回收温度、50%回收温度和闪点来反映喷气燃料轻组分的含量。
2.热值和密度
由于喷气式飞机飞行速度快,续航里程远,发动机功率大,要求燃料具有较大的能量以转化为推动力。如果燃料的热值低,必然导致油耗高、航程短或油箱容积过大。燃料热值与其化学组成和馏分组成有关。芳香烃体积热值最高,环烷烃次之,烷烃最低。但是芳香烃在燃烧时易生成积炭,所以必须限制它的含量。国家标准规定3#喷气燃料芳香烃含量不大于20%。
3.积炭性能
喷气式发动机机件产生积炭是非常危险的。喷油嘴上生成积炭,会使燃料雾化变差、火焰偏烧,促使火焰筒壁生成积炭,局部过热严重,会使筒壁变形甚至破裂;电点火器电极上形成积炭,会使燃烧室点火困难。燃料的积炭性能与其组成密切相关。各族烃中,芳香烃(特别是双环芳香烃)形成积炭的倾向最大。因此,在国产喷气燃料的相关标准中规定双环芳香烃(萘系烃)含量不能大于3%。此外,馏分变重、不饱和烃含量增加、胶质含量高或含硫化合物的存在,都会使生成积炭的倾向增大。反映喷气燃料积炭倾向的质量指标有实际胶质、烟点、辉光值等。在各族烃类中,馏分最重、沸点最高的稠环芳香烃生成积炭的倾向性最大,所以喷气燃料的实际胶质高,会显著增加积炭量。我国规定,喷气燃料中实际胶质含量不得高于7mg/mL。
烟点是在规定条件下,油品在标准灯中燃烧时,不冒烟火焰的最大高度,单位是毫米(mm)。烟点愈高,燃料生成积炭的倾向愈小。含芳烃少的燃料烟点高,积炭可能性小,国家标准规定喷气燃料的烟点不得小于25mm。
燃料燃烧时火焰中含有的炭微粒增加了火焰辐射能力,火焰中的炭微粒越多,辐射强度越大,温度就越高而易形成积炭。辉光值表示燃料燃烧时火焰的辐射强度。辉光值愈高,火焰辐射强度愈小,燃烧愈完全。各类烃辉光值的大小依次为:烷经>单环环烷烃>双环环烷烃>芳香烃。但因发动机动力和续航里程的需要,燃料的辉光值不可过低。国家标准规定,喷气燃料的辉光值不得小于45。
4.低温性能
喷气燃料需要具备在低温条件下能顺利地在发动机和燃料系统中用泵输送和通过滤清器的性能,称为低温性能。黏度的大小直接影响喷气燃料的低温流动性。喷气燃料的黏度过大,雾化不完全而导致燃烧不完全,增加燃料消耗;黏度过小,将会使燃料喷射时射程过近而引起局部过热。
芳烃含量过多时,黏度过大,形成黏温凝固,燃料会失去流动性。正构烷烃含量过多,随温度下降析出结晶,形成骨架凝固也会影响燃料低温流动性。另外,水分在低温下形成冰晶也会不同程度降低燃料的低温流动性能。芳香烃,特别是苯对水的溶解度最大,环烷烃次之,烷烃最小。所以从降低结晶点的角度,也需要限制喷气燃料中芳香烃的含量。国家标准规定,芳香烃含量不能大于20%。喷气燃料国家标准中通过冰点来控制正构烷烃的含量,通过馏程来约束黏度大组分的含量。改善喷气燃料的低温性能的方法有:热空气加热燃料和过滤器,加入防冰添加剂等。国家标准规定,喷气燃料冰点不得高于-47℃。
5.安定性
因军事和政治需要,喷气燃料必须有相当数量的战略储备,因而要求燃料至少要储存2~3年以上不变质,然后再更新储存。因此要求喷气燃料无论是在储存、运输,还是在使用过程中要具备较强的抗氧化安定性。水的存在破坏力极大,它能增强燃料的腐蚀性,降低油品的低温流动性,还会破坏燃料在系统部件中所起的润滑作用,并能导致微生物细菌大量繁殖而堵塞过滤器。所以喷气燃料在加工生产和调和过程中,必须要做好水分的沉降分离,并减少人为以及额外工艺引入的水分。硫化物对发动机镀银机件腐蚀很明显,国家标准对喷气燃料的银片腐蚀强度做出了严格限制规定。喷气燃料在炼油调和工艺中加入一定量的抗氧化添加剂、金属钝化剂有利于长期储存。
6.防静电性
喷气式发动机的耗油量很大,每小时达几吨到几十吨。为节省时间,机场采用高速加油。在高速加油时,燃料与管壁、注油设备等剧烈摩擦产生静电。所以,从安全角度考虑,喷气燃料应具有良好的防静电性和良好的导电性。由于燃料本身的电导率较低,常采用的方法是添加很少量的防静电添加剂。
7.良好的润滑性能
喷气发动机的高压燃料油泵是以燃料本身作为润滑剂的,燃料还作为冷却剂带走摩擦产生的热量,因此要求喷气燃料具有良好的润滑性能。喷气燃料的润滑性能取决于其化学组成,烃类中以单环或多环环烷烃的润滑性能最好。直馏煤油中某些微量的极性非烃化合物,如环烷酸、酚类以及某些含硫和含氧化合物,它们具有较强的极性,容易吸附在金属表面上,降低金属间的摩擦和磨损,具有良好的润滑性能。但同时这些非烃化合物也影响了喷气燃料的燃烧性和安定性等,因此常采用精制的方法将它们除去。改善喷气燃料润滑性能的途径主要是加入少量抗磨添加剂,或调入一定量的直馏喷气燃料组分等。国产喷气燃料RP-3的主要质量指标见表1-9。
表1-9 国产喷气燃料RP-3的主要质量指标

四、润滑油
润滑油是以直馏减压馏分为原料,多用丁酮-苯溶剂脱蜡,再经过精制脱除杂质后调和而成。如果使用环境苛刻,还需要对润滑油基础油进行进一步的精制、加工和提纯。虽然润滑油的产量仅占原油加工量的2%左右,但其品种多达上千种,总体来说润滑油分为四大类:内燃机润滑油、齿轮油、液压油和工业设备用油。其中,内燃机润滑油用量最大,约占润滑油总量的70%以上。润滑油对内燃机有润滑、冷却、密封、卸荷及减震等保护作用。内燃机润滑油的质量要求很多,主要有黏度、抗氧化安定性、黏温性与低温流动性等。
1.黏度
两个做相对运动的机件表面之间产生的摩擦现象称为干摩擦,如轴在轴承里转动,活塞与气缸内壁的摩擦都是这种情况。干摩擦对设备造成严重的磨损,所以工作中绝不允许机械设备有干摩擦现象存在。加注润滑油后就会在摩擦面上形成相当厚的润滑油层(油膜),从而避免和减轻了机件表面的磨损和发热。润滑油的黏度太小,将会导致油膜厚度太薄而加大机件的磨损。流动着的润滑油不断地从摩擦面上流过,也能带走摩擦面上一定的热量,起到冷却作用。黏度过大的润滑油因为其流动性弱,会在一定程度上影响冷却效果。内燃机气缸壁与活塞环之间都有一定的间隙,当润滑油充满了这些间隙后,起到了密封的作用,黏度较大的润滑油,其密封性能较好。润滑油的黏度与其馏分组成有关,润滑油的馏程越高,黏度就会越大。
2.抗氧化安定性
相对运动的机件表面上涂了一层润滑油,就形成了一层保护膜,将金属表面覆盖住,能够隔绝周围的氧气或其他的腐蚀气体,使金属免受腐蚀,但是润滑油必须保证自身不变质。内燃机润滑油不仅使用环境的温度高,而且是循环使用的,不断与含氧的气体接触,很容易氧化变质。不饱和烯烃和芳香烃易与氧发生反应,所以烯烃和芳烃不是理想的组分,润滑油需要控制它们的含量以保证抗氧化安定性。
3.清净性
发动机润滑油的氧化是无法完全避免的,这就要求润滑油能及时沉淀氧化生成的胶状物和清洗掉炭渣,或者使它们分散悬浮在油品中,通过滤清器除掉,以保持活塞环等零件清洁,使不易卡环等。国家标准中用清净性衡量润滑油的这一性能,它是在专门的仪器中测定的,从0~6分为7个等级,级数越高,清净性越差。国家标准中规定,汽油机油的清净性不大于1.5级,通常是靠加入清净分散添加剂来满足使用要求。
4.黏温性与低温流动性
内燃机正常运转时的温度范围较宽,可达到300℃高温,而在启动时温度比较低,尤其在高寒地区的冬季,室外的气温甚至低到零下几十摄氏度。如果润滑油的黏度随温度的变化太大,高温时太稀而不能保持必要厚度的油膜,将会加大机器的磨损;低温时又太稠,加之没有良好的低温流动性,润滑油便不能正常泵送,这样运动部件就不能形成正常的润滑状态而导致磨损。影响润滑油低温流动性的因素主要有两个方面:一是蜡结晶形成骨架影响流动性;二是因为温度低、黏度大、流动太慢而导致流动性差。润滑油的黏温性和低温流动性都与其自身分子结构和化学组成有关。
5.腐蚀性
润滑油的腐蚀作用主要由油品中酸性物质形成。这些酸性物质有些是原本就存在,有些是氧化反应的产物。发动机润滑油应对一般轴承无腐蚀,而且对于极易被腐蚀的铜、铅、镉、银、锡、青铜等耐磨材料,也应无腐蚀作用。通常用酸值、水溶性酸碱等表征润滑油腐蚀性的大小。对于润滑油,提高其抗腐蚀性的方法是加入抗氧防腐添加剂。
五、石蜡、石油焦、沥青
1.石蜡
石蜡主要包括液蜡、石蜡、微晶蜡。液蜡一般是指C9~C16的正构烷烃,室温下呈液态,它是由常减压蒸馏装置常二线直馏轻柴油馏分经分子筛脱蜡工艺而得到的。石蜡又称为晶形蜡,它是从减压馏分中经过脱油、精制而得到的固态烃类,其烃类碳原子数为C17~C35,平均分子量为300~450。微晶蜡(又称地蜡)是减压渣油经丙烷脱沥青后进一步精制加工得到的产品,它的碳原子数为C36~C60,平均分子量为500~800。石蜡的应用较为广泛,如橡胶制品、电信器材、复写纸、装饰板、食品及药品的包装、化妆品等的原料中都会用到石蜡。评价石蜡的主要性能指标一般有熔点、含油量和安定性。
石蜡的熔点是指在规定的条件下,冷却已熔化的石蜡试样时,冷却曲线第一次出现停滞期的温度。各种蜡制品都要求有良好的耐温性能,即在特定温度下不熔化和不软化变形。影响石蜡熔点的主要因素是石蜡本身碳原子数的多少,碳原子数越大,其熔点越高。此外,含油量越多的石蜡,其熔点越低。含油量是指石蜡中所含低熔点烃类的量。含油量过高会影响石蜡的色度和储存的安定性,还会使它的硬度降低。因此,从常减压蒸馏装置来的减压馏分油,需用发汗法或溶剂法进行脱油来制得成型蜡的原料,以降低成品石蜡的含油量。
由于石蜡含有在精制过程中未能脱除的微量非烃化合物、不稳定的烯烃和稠环芳烃,所以在精制工艺后的成型过程中处于高温热熔状态的石蜡,与空气接触很容易发生氧化反应而变质变色,即便在常温下使用时,光照石蜡也会变黄。因此,精品石蜡应具有良好的热安定性、氧化安定性和光安定性。
2.石油焦
石油焦是直馏减压渣油经延迟焦化而制得的黑色或暗黑色的固体,元素组成上含碳90%~97%,含氢1.5%~8.0%,其余为少量的硫、氮、氧和金属,广泛应用于冶金、化工等领域,作为制造石墨电极或生产化工产品的原料,也可直接用作燃料。评价石油焦产品质量的指标主要有挥发分、硫含量和灰分等。
挥发分是将石油焦试样放入850℃高温炉内加热3min后损失质量的百分比。挥发分越大,表明石油焦硬度越小,轻组分含量越多,在煅烧时焦炭易于破碎。挥发分侧面也反映了延迟焦化工艺的加工损失程度。石油焦在生产电极的过程中,高温时会释放硫使电极晶体膨胀,低温时会吸收硫发生收缩,导致电极破裂。所以,用于生产电极的石油焦要严格控制硫含量,一般控制在0.5%以下。灰分对石油焦的固态性状和硬度有影响,进而也会影响到产品电极的机械强度。另外,石墨电极中灰分的存在还会影响冶金产品的纯度。
3.沥青
石油沥青多数是直馏减压渣油经过溶剂脱除蜡油以上组分后经过氧化制得,在常温下是黑色或黑褐色的黏稠液体、半固体或固体。石油沥青按用途可分为:道路沥青、建筑沥青、防水防潮沥青以及其他专用沥青等。评价沥青质量指标主要有针入度、延度、软化点和脆点等。
石油沥青的针入度以标准针在荷重100g,时间为5s及25℃条件下垂直穿入沥青试样的深度来表示,单位为0.1mm。针入度反映出沥青的黏稠程度或软硬程度。
石油沥青的延度是将熔化的沥青试样注入专用的模具中,在25℃下以5cm/min的速度拉伸试样至断裂时的长度,其单位是厘米(cm)。延度表示沥青在应力作用下断裂前扩展和拉伸的能力。延度大,表明沥青的塑性变形性能好,不易出现裂纹,即使出现裂纹也容易自愈。
沥青的软化点和脆点可以认为是使用温度的上下限。在规定的仪器和测定条件下,将一定尺寸和质量的钢球放置在规定尺寸的金属环内的沥青试样上,在加热介质中以恒定的速度升温,随温度升高沥青试样逐渐软化,钢球在重力作用下慢慢下坠,当沥青软化到钢球下坠幅度达到25mm时的温度称为石油沥青的软化点,其单位是摄氏度(℃)。脆点是测定沥青在低温下引起脆性破坏的温度,脆点实质上反映出沥青由黏弹态变为弹脆体(即玻璃态)的温度。脆点越低,软化点越高,沥青使用的温度范围越广,但是沥青的软化点过高,则会因不易熔化而造成施工困难。