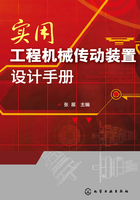
3.3 全断面岩石掘进机
3.3.1 ϕ5.8m全断面岩石掘进机简介
目前地下隧洞施工主要分为人工钻爆(简称DBM)和全断面掘进机(简称TBM)施工两种方式。TBM施工具有自动化程度高、掘进速度快、劳动环境好、无超挖、对围岩扰动小等特点,是先进的大型地下工程施工成套技术装备,受到世界各主要工业国家的高度重视。
我国自1985年以来,先后研制了19台全断面岩石掘进机,直径从ϕ2.5~ϕ6.8m,取得一定业绩,但远不能满足经济快速发展的需求,有待于进一步研制与开发。现以我国自行研制的ϕ5.8m全断面岩石掘进机为例,介绍其主要技术参数及主要部件的结构性能。
3.3.1.1 主要技术参数
ϕ5.8m全断面岩石掘进机主要技术参数见表3-3。
表3-3 技术参数

3.3.1.2 主要部件的结构与特点
(1)刀盘 刀盘包括刀盘内圈、铲斗、大轴承、刀具等部分(见图3-22)。

①刀具 为了提高刀具的承载能力和耐磨性,采用大刀圈、优质材料及合理的结构,增强刀座强度。此外,正刀和中心刀刀座采用埋入式保护,工作面形状为平面圆弧过渡,刀具布置为双螺旋线对称型,因而刀盘受力平衡。
a.正滚刀 结构为定轴单刃盘形滚刀,刀圈直径ϕ400mm,材料用基体钢或耐磨合金钢,轴承型号7620,金属浮动密封。
b.中心刀 结构为定轴双刃盘形滚刀,刀圈直径ϕ310mm,轴承型号7616,其余类似正滚刀。
c.边滚刀 采用不对称轴承结构的定轴单刃盘形滚刀,其余类似于正滚刀。
②大轴承和大密封
a.大轴承 为了提高轴承的承载能力,由轴承厂专门研制了378/1600型大锥角双排圆锥滚子轴承,额定寿命为5000h。
b.大密封 为防止泥浆进入大齿圈和大轴承,采用多道密封;并设计了充气密封,以提高密封效果,防止油液外泄,减少橡胶密封的磨损。其中橡胶密封专门研制。
(2)刀盘支承装置(图3-23) 刀盘支承装置由支承壳体、前支承、侧支承、护盾及挡尘板等组成。

①采用大包角的护盾和侧支承,加上前支承,这就在横断面上将整个隧洞的85%以上都支护起来,从而大大提高了机器的安全性和稳定性。
②各种支承面积大,易于通过破碎和松软地带,洞壁有窟窿和台阶时,也不会嵌入和拉坏,且挡碴性能好,可大大减少工作区域的漏碴。
③挡尘板外缘的车胎式橡胶密封,同护盾和侧支承的内壁接触,无相对摩擦,提高了寿命。我们在两个工地施工过程中均未更换过。
(3)传动系统 传动系统由4台150kW电动机通过联轴器、两级行星齿轮减速器和末级齿轮驱动大齿圈,带动刀盘回转。此外,机器上还装有一套刀盘液压启动装置。
①两级行星齿轮减速器 2K-H(NGW)型,采用中心轮浮动实现均载,传动比i=28.6,输出轴转速为51.6r/min。
②刀盘液压启动装置 采用油马达、超越离合器带动刀盘慢速转动,然后启动刀盘电机,从而缩短了启动的持续时间。当刀盘需要准确定位时,无需开动电机,只要点动油马达便可。该装置可以减少对电机、电器和传动系统的启动冲击,提高了元件的使用寿命。
(4)机架和机尾 支承水平框架的机架由上下大梁和前后立柱组成空间框架,经与上海交通大学协作,运用有限元法通过电子计算机分析计算,具有足够的强度和刚性,机尾与机架采用精配螺柱联接,以安置机房。
(5)除尘系统 设置旋风水膜除尘器和轴流通风机,将经过粉尘离析的空气送出洞外;同时,另有一路进风管路,将新鲜空气送到机器旁边,保证操作人员的环境卫生。
(6)液压系统(见图3-24)

①供油 由63CY14-1B型轴向柱塞变量泵,供掘进机各工作装置正常操作所需的压力油,另一只轴向柱塞变量泵供油缸快速移动和刀盘启动用的压力油,齿轮泵供给轴向柱塞泵和电液换向阀控制用压力油。
②操作系统 由电液换向阀控制各路油液动作,并对水平支撑缸、推进缸及后支承和刀盘之间实行电气联锁,避免因误操作带来机器事故。
(7)润滑系统 机器的润滑包括稀油和干油润滑两部分,大轴承和齿轮箱采用稀油润滑,大轴承还采用气动密封,由低压的油雾气充入橡胶密封唇口处,增加密封效果。大轴承润滑还有供油指示,润滑油失压,指示灯亮。支承壳体密封、大齿圈密封和导轨滑动面等由多点干油泵供应干油润滑。
(8)电气系统
①采用6kV高压电源,用UG-kV(3×25+1×16)橡套移动软电缆联接。
②洞口变电所用GG-1A高压开关柜和高压量电柜控制。机器上高压开关用ZN-6/600A真空接触器控制。
③机器主变压器JS-800kV·A,6/0.4~0.23kV;0.4kV低压总开关用DW10-1500/3自动空气开关;控制电源为交流220V。
④刀盘先由液压马达启动到刀盘规定转速1r/min时,再启动刀盘电机。
⑤机器装有电气测量及联锁、保护等装置。
(9)激光导向 激光发射装置采用J2-JD激光经纬仪,安装在机后洞壁上。该仪器分度盘精度高,移动位置后找正方便。机器上装有固定的前靶和后靶,根据激光束在两靶上位置的差别,判断机器方位的偏差。为防止仪器位置变动,引起方位指示差,在仪器与机器之间的洞壁上装有校正靶。
(10)机器方位调整
①掘进坡度调整 用前支承油缸伸缩调节,或在调换行程时利用后支承调节。
②水平方位调整 可利用推进缸节流,或水平缸浮动微调,也可利用左右侧支承的伸缩调整。
3.3.1.3 常用的传动装置(见图3-25~图3-27)

图3-25 行星减速器(日本小松制作所)

图3-26 两级行星减速器(美国罗宾斯公司制造,用于隧洞掘进机)

3.3.2 隧洞掘进机用行星齿轮减速器
国内外隧道开挖,石方开挖中用全断面硬岩掘进机,土方开挖中用顶管或盾构掘进机。其中主传动所用的传动型式大多为渐开线行星齿轮传动。由于行星齿轮传动采用功率分流,由数个行星轮承担载荷,采用合理的内啮合传动。与定轴传动相比,具有体积小、质量轻、承载能力大和效率高之优点。但在井下施工中,目前用的通用行星齿轮减速器仍感到体积和质量较大,不便于现场安装与维护,于是便设计出一种新型结构的行星齿轮减速器,即悬浮均载行星齿轮减速器。图3-28为2K-H型双级行星减速器。高速级采用行星架浮动,低速级采用太阳轮和杠杆联动机构浮动,该减速器用于梭式矿车。

3.3.2.1 传动原理与组成
悬浮均载行星齿轮减速器见图3-29。

图3-29 悬浮均载行星齿轮减速器
①传动原理 采用2K-H(NGW)型负号机构的行星齿轮传动,当高速轴由电动机驱动时,便带动太阳轮回转,于是带动行星轮转动,由于内齿圈固定不动,便驱动行星架作输出运动,行星轮在行星架上既作自转又作公转的行星传动,就以此同样的结构组成两级、三级或多级的串联行星齿轮传动。
②组成 由太阳轮Za、行星轮Zg、内齿圈Zb和行星架H所组成。以啮合方式命名为NGW型(其中N—内啮合、G—公用齿轮、W—外啮合)。以基本构件命名,即为2K—H型行星齿轮传动。所谓基本构件,在行星齿轮传动的各构件中,凡是轴线与定轴线重合,且承受外力矩的构件称为基本构件。因此传动是由两个中心轮2K和行星架H等三个基本构件组成,因而称为2K-H型行星齿轮传动。
3.3.2.2 主要特点
主要技术参数见表3-4,外形及安装尺寸见表3-5。
表3-4 主要技术参数

表3-5 外形及安装尺寸 mm

注:1. 2K-H27A带卧式底座。
2. 2K-H278C除输出轴键型式外其余尺寸同2K-H278A。
3. 2K-H300A,2K-H300C除输出轴键型式外其余尺同2K-H300。
①将前一级的行星架与后一级的太阳轮联成一体,无径向支承,呈悬浮状态,减少支承、简化结构、减少连接环节,并以行星架和太阳轮联合浮动,均载效果好,载荷不均衡系数Kp≤1.15。
②采用组合式焊接行星架,连接板、连接柱采用Q235A,而带太阳轮部分,则采用低合金钢,用无氧化渗碳淬火。简化结构、简化工艺、减轻质量。
③为了进一步简化结构,同时为满足等直径、等强度之要求,将末级内齿圈与前一级内齿圈做成一体,采用同一模数,简化工艺与加工要求,减少连接环节与零件。并以采用不同的行星轮个数np(np=3、4、5等)和不同的齿宽b,以实现等强度之要求。
④单位质量的承载能力为60~80kN·m/t,个别可达100kN·m/t,而国内以往设计的行星齿轮传动仅为20~30kN·m/t。
⑤传动平稳、可靠、噪声低和效率高,单级传动效率η=0.98,两级为η=0.96,三级为η=0.94。
⑥太阳轮、行星轮采用优质低合金钢,经无氧化渗碳淬火,齿面硬度为55~58HRC,采用精湛的工艺手段,使齿轮达到较高的精度。内齿圈用42CrMo。经调质处理,均能达到较高的精度。
3.3.2.3 减速器的润滑
油浴润滑的油量加至油标所示的位置,对于平行轴传动的减速器油量按中间级大齿轮浸油2~3个全齿高计算。
循环润滑的油量一般不少于0.5L/kW,或按热平衡、胶合强度计算。
润滑油的牌号(黏度)按高速级齿轮的圆周速度V或润滑方式选择。
当V<2.5m/s、或当环境温度在35°~50°之间时,选用中极压齿轮油L-CKC320(或VG320、Mobil632)。
当V>2.5m/s或采用循环润滑时,选用中极压齿轮油L-CKC220(或VG220、Mobil 630)。