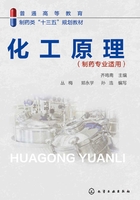
1.7 离心泵
1.7.1 离心泵工作原理
输送流体所需的能量 图1-43所示为一带泵管路。为将流体从低能位1处向高能位2处输送,单位重量流体需补加的能量为H,则
整理可得
(1-86)
式中

图1-43 输送系统简图
为管路两端单位重量流体的势能差,它包括了位能差和压强能差。
通常情况下(如图1-43所示),式(1-86)中的动能差一项可以略去,阻力损失∑Hf的数值与管路条件及流速大小有关
(1-87)
或
(1-88)
式中, 系数K为
其数值由管路特性决定。当管内流动已进入阻力平方区,系数K是一个与管内流量无关的常数。将式(1-88)代入式(1-86),有
(1-89)
式(1-89)称为管路特性方程,它表明管路中流体的流量与所需补加能量的关系。管路特性方程可图示表达成曲线,称为管路特性曲线,如图1-44所示。

图1-44 管路特性曲线
由式(1-89)可知,需向流体提供的能量用于提高流体的势能和克服管路的阻力损失;其中阻力损失项与被输送的流量有关。显然,低阻力管路系统的特性曲线较为平坦(曲线1),高阻管路的特性曲线较为陡峭(曲线2)。
流体输送机械的主要技术指标 压头和流量是流体输送机械的主要技术指标。输送流体,必须达到规定的输送量。为此,需补给单位重量输送流体以足够的能量,其数量应与式(1-89)的H值相等。通常将输送机械向单位重量流体提供的能量称为该机械的压头或扬程。
许多流体输送机械在不同流量下其压头不同, 压头和流量的关系由输送机械本身的特性决定。
离心泵的主要构件——叶轮和蜗壳 离心泵的种类很多,但因工作原理相同,构造大同小异,其主要工作部件是旋转叶轮和固定的泵壳(见图1-45)。叶轮是离心泵直接对液体做功的部件,其上有若干后弯叶片,一般为4~8片。离心泵在工作时,叶轮由电机驱动作高速旋转运动(1000~3000r/min),迫使叶片间的液体作近于等角速度的旋转运动,同时因离心力的作用,使液体由叶轮中心向外缘作径向运动。在叶轮中心处吸入低势能、低动能的液体在流经叶轮的运动过程中获得能量,在叶轮外缘可获得高势能、高动能。液体进入蜗壳后,由于流道的逐渐扩大而减速,又将部分动能转化为势能,最后沿切向流入压出管道(见图1-46)。在液体受迫由叶轮中心流向外缘的同时,在叶轮中心形成低压。液体在吸液口和叶轮中心处的势能差的作用下源源不断地吸入叶轮。

图1-45 离心泵装置简图
1—叶轮;2—泵壳;3—泵轴;4—吸入管; 5—底阀; 6—压出管

图1-46 液体在泵内的流动
液体在叶片间的运动 如图1-47所示,当离心泵输送液体时,液体在叶轮内部除以切向速度u随叶轮旋转外,还以相对速度w沿叶片之间的通道流动。液体在叶片之间任一点的绝对速度c等于该点的切向速度u和相对速度w的向量和。因此,液体在叶轮进、出口处的绝对速度c1和c2应满足图1-47所示的平行四边形。

图1-47 液体在离心泵内流动的速度三角形
离心泵的理论压头 当叶轮转速为n时,叶轮外缘的切向速度为u2=2πr2n。在理想流体、叶片无限薄、无限多等假定条件下,经数学推导得到离心泵的理论压头为
(1-90)
式中,A2=2πr2b2为叶轮出口处的流通面积;b2为叶轮出口的宽度;β2为叶轮出口处叶片的倾角。式(1-90)表示不同形状的叶片在叶轮尺寸和转速一定时,泵的理论压头和流量的关系。
根据叶片出口端倾角β2 的大小,叶片形状可分为三种:径向叶片(β2=90°);后弯叶片(β2<90°)和前弯叶片(β2>90°)。叶片形状不同, 离心泵的理论压头HT与流量qV的关系也不同(见图1-48)。后弯叶片的流体出口动能较小,在蜗壳中转化成为势能时的能量损失较小,能量利用率较高。因此,离心泵总是采用后弯叶片。
气缚现象 理论压头的影响因素都已清楚地表示于式(1-90)中,式中并不含有液体密度这一重要性质,表明理论压头与液体密度无关。这表明,无论输送何种液体,同一台泵所能提供的理论压头是相同的。但是,离心泵的压头是以被输送流体的流体柱高度表示的。在同一压头下,泵进、出口的压差却与流体的密度成正比。如果泵启动时,泵体内是空气,而被输送的是液体,则启动后泵产生的压头虽为定值,但因空气密度太小,造成的压差或泵吸入口的真空度很小而不能将液体吸入泵内。因此,离心泵启动时须先使泵内充满液体,这一操作称为灌泵。如果泵的位置处于吸入液面之下,液体可自动进入泵内,则毋须灌泵。

图1-48 离心泵的HT~qV关系
泵在运转时吸入管路和泵的轴心处常处于负压状态,若管路及轴封密封不良,则因漏入空气而使泵内流体的平均密度下降。若平均密度下降严重,泵将无法吸上液体,此称为“气缚”现象。
1.7.2 离心泵特性曲线
泵的有效功率和效率 泵在运转中由于存在各种机械能损失,使泵的实际(有效)压头和流量均较理论值为低,而输入泵的功率较理论值为高。取He为泵的有效压头,即单位重量流体自泵处净获得的能量,m;qV为泵的实际流量,m3/s;ρ为液体密度,kg/m3;Pe为泵的有效功率,即单位时间内液体从泵处获得的机械能,W。
显然
Pe=ρgqVHe (1-91)
由电机输入离心泵的功率称为泵的轴功率,以Pa表示。定义有效功率与轴功率之比为泵的(总)效率η
(1-92)

图1-49 叶轮的类型
离心泵内的机械能损失主要有容积损失、水力损失和机械损失。容积损失是指叶轮出口处高压液体因机械泄漏返回叶轮入口所造成的能量损失。
在图1-49所示的三种叶轮中,敞式叶轮的容积损失较大,但在泵送含固体颗粒的悬浮体时,叶片通道不易堵塞。水力损失是由于实际流体在泵内有限叶片作用下造成的各种摩擦阻力损失,包括液体与叶片、壳体的冲击而产生旋涡,形成机械能损失。机械损失则包括旋转叶轮盘面与液体间的摩擦以及轴承机械摩擦所造成的能量损失。

图1-50 离心泵的特性曲线
离心泵的特性曲线 离心泵的有效压头He(扬程)、效率η、轴功率Pa均与输液量qV有关,其关系可用泵的特性曲线表示,其中尤以扬程和流量的关系最为重要。图1-50为离心泵的特性曲线。
离心泵的水力损失难以定量计算,因而泵的扬程He与流量的关系只能通过实验测定。离心泵出厂前均测定He~qV、η~qV、Pa~qV三条曲线,列于产品样本供用户使用。
图1-50中直线1为离心泵的理论压头,由图可见,在额定流量qVA下,压头损失最小,效率最高。
【例1-10】 离心泵特性曲线的测定
图1-51为离心泵特性曲线的测定装置,实验中已测出如下一组数据:

图1-51 离心泵特性曲线的测定装置
1—流量计;2—压强表;3—真空表
泵出口处压强表读数p2=0.21MPa;泵进口处真空表读数p1=0.02MPa;泵的流量qV=12L/s;泵轴的扭矩M=31.3N·m;转速n=1450r/min;吸入管直径d1=80mm;压出管直径d2=60mm;两测压点间的垂直距离z2-z1=80mm。
实验介质为20℃的水。
试计算在此流量下泵的压头He、轴功率Pa和总效率η。
解:如图1-51所示,在截面1与2间列机械能衡算式
液体黏度对特性曲线的影响 泵制造厂所提供的特性曲线是用常温清水进行测定的, 若用于输送黏度较大的实际工作介质,特性曲线将有所变化。因此,选泵时应先对原特性曲线进行修正。
比例定律 同一台离心泵在不同转速运转时其特性曲线不同。如转速相差不大,转速改变后的特性曲线可从已知的特性曲线近似地换算求出,换算的条件是设转速改变前后液体离开叶轮的速度三角形相似,则泵的效率相等。参见图1-52,由速度三角形相似可得
(1-93)
式中,c2r为叶片出口处液体绝对速度的径向分速度,m/s。

图1-52 不同转速下的速度三角形
式(1-93)是保持速度三角形相似的条件。当调节离心泵的流量,使其与转速的关系满足式(1-93)时,压头之比为
(1-94)
轴功率之比为
(1-95)
以上三式称为比例定律。
据此可从某一转速下的特性曲线换算出另一转速下的特性曲线,但是仅以转速变化±20%以内为限。当转速变化超出此范围,则上述速度三角形相似、效率相等的假设将导致很大误差,此时泵的特性曲线应通过实验重新测定。
1.7.3 离心泵工作点与流量调节
安装在管路中的泵的输液量即为管路的流量, 在该流量下泵提供的扬程必等于管路所要求的压头。因此,离心泵的实际工作情况(流量、压头)是由泵特性和管路特性共同决定的。
离心泵的工作点 若管路内的流动处于阻力平方区,管路中离心泵的工作点(扬程和流量)必同时满足:
管路特性方程
H=f(qV) (1-96)
泵的特性方程
He=φ(qV) (1-97)
联立求解这两个方程即得管路特性曲线和泵特性曲线的交点,见图1-53。此交点为泵的工作点。
流量调节 如果工作点的流量大于或小于所需要的输送量,应设法改变工作点的位置, 即进行流量调节。
最简单的调节方法是在离心泵出口处的管路上安装调节阀。 改变阀门的开度即改变管路阻力系数[(式(1-89)中的K值]可改变管路特性曲线的位置,使调节后管路特性曲线与泵特性曲线的交点移至适当位置,满足流量调节的要求。如图1-53所示,关小阀门,管路特性曲线由a移至a',工作点由1移至1',流量由qV减小为q'V。
这种通过管路特性曲线的变化来改变工作点的调节方法,不仅增加了管路阻力损失(在阀门关小时),且使泵在低效率点工作,在经济上不合理。但用阀门调节流量的操作简便、灵活, 故应用很广。当调节幅度不大而常需改变流量时,此法尤为适用。
另一类调节方法是改变泵的特性曲线,如改变转速(见图1-54)、换不同直径的叶轮。改变转速调节流量不额外增加管路阻力,且在一定范围内可保持泵在高效率区工作,能量利用较为经济,但调节不方便,一般只有在调节幅度大、时间又长的季节性调节中才使用。

图1-53 离心泵的工作点

图1-54 改变泵特性曲线的调节
当需较大幅度增加流量或压头时可用几台泵进行组合操作。离心泵的组合方式原则上有两种:并联和串联。下面以两台特性相同的泵为例,讨论离心泵组合后的特性。

图1-55 离心泵的并联操作
并联泵的合成特性曲线 设有两台型号相同的离心泵并联工作(见图1-55),且各自的吸入管路相同,则两泵的流量和压头必相同。因此,在同样的压头下,并联泵的流量为单台泵的两倍。这样,将单台泵特性曲线1的横坐标加倍,纵坐标保持不变,便可求得两泵并联后的合成特性曲线2。
并联泵的流量qV并和压头H并由合成特性曲线与管路特性曲线的交点a决定,并联泵的总效率与每台泵的效率( 图中b点的单泵效率 )相同。由图可见,由于管路阻力损失的增加, 两台泵并联的总输送量qV并必小于原单泵输送量qV(c点)的两倍。
串联泵的合成特性曲线 两台相同型号的泵串联工作时,每台泵的压头和流量也是相同的。因此,在同样的流量下,串联泵的压头为单台泵的两倍。将单台泵的特性曲线1的纵坐标加倍,横坐标保持不变,可求出两泵串联后的合成特性曲线2(见图1-56)。

图1-56 离心泵的串联操作
同理,串联泵的总流量和总压头也是由工作点a所决定。由于串联后的总输液量qV串即是组合中的单泵输液量qV(b点),故总效率也为qV串时的单泵效率。
组合方式的选择 如果管路两端的势能差大于单泵所能提供的最大扬程,则必须采用串联操作。许多情况下,
小于单泵所能提供的最大扬程,单泵可以输液,只是流量达不到指定要求。此时可针对管路的特性选择适当的组合方式,以增大流量。

图1-57 组合方式的选择
由图1-57可见,对于低阻输送管路a,并联组合输送的流量大于串联组合;而对于高阻输送管路b,则串联组合的流量大于并联组合。对于压头也有类似的情况。因此,对于低阻输送管路,并联优于串联组合;对于高阻输送管路,则适用串联组合。
1.7.4 离心泵安装高度
汽蚀现象 见图1-58,在液面0-0与泵进口截面1-1之间无外加机械能,液体借势能差流动。随着泵的安装位置提高,叶轮进口处的压强可能降至被输送液体的饱和蒸气压,引起液体部分汽化。

图1-58 离心泵的安装高度
实际上,泵中压强最低处位于叶轮内缘叶片的背面(图中K-K面)。泵的安装高度至一定值,首先在该处发生汽化现象。含气泡的液体进入叶轮后,因压强升高,气泡立即凝聚。气泡的消失产生局部真空,周围液体以高速涌向气泡中心,造成冲击和振动。尤其当气泡的凝聚发生在叶片表面附近时,众多液体质点犹如细小的高频水锤撞击着叶片;另外气泡中还可能带有一些氧气等对金属材料发生化学腐蚀作用。泵在这种状态下长期运转,将导致叶片的过早损坏。这种现象称为泵的汽蚀。
离心泵在产生汽蚀条件下运转,泵体振动并发生噪声,流量、扬程和效率都明显下降,严重时甚至吸不上液体。为避免汽蚀现象,泵的安装位置不能太高,以保证叶轮入口处压强高于液体的饱和蒸气压。
临界汽蚀余量(NPSH)c与必需汽蚀余量(NPSH)r 在正常运转时,泵入口截面1-1的压强p1和叶轮入口截面K-K的压强pK密切相关,从截面1-1至K-K列机械能衡算式
(1-98)
由式(1-98)可见,在一定流量下,p1降低,pK也相应地减小。当泵内刚发生汽蚀时,pK等于被输送液体的饱和蒸气压pv,此时的p1为最小值p1,min。在此条件下,式(1-98)可写为
或
(1-99)
式(1-99)表明,在泵内刚发生汽蚀的临界条件下,泵入口处液体的机械能比液体饱和蒸气压强能超出
。此超出量称为离心泵的临界汽蚀余量,并以符号(NPSH)c表示,即
(1-100)
为使泵正常运转,泵入口处的压强p1必须高于p1,min,即实际汽蚀余量(亦称装置汽蚀余量)
(1-101)
必须大于临界汽蚀余量(NPSH)c一定的量。
不难看出,当流量一定而且流动已进入阻力平方区时,临界汽蚀余量(NPSH)c 只与泵的结构尺寸有关。
临界汽蚀余量作为泵的一个特性,须由泵制造厂通过实验测定。式(1-100)是实验测定(NPSH)c的基础。实验时可设法在泵流量不变的条件下逐渐降低p1 (例如关小吸入管路中的阀),当泵内刚好发生汽蚀(按有关规定,以泵的扬程较正常值下降3%作为发生汽蚀的标志) 时测取压强p1,min,然后由式(1-100)算出该流量下离心泵的临界汽蚀余量(NPSH)c。
为确保离心泵工作正常,根据有关标准,将所测定的(NPSH)c加上一定的安全量作为必需汽蚀余量(NPSH)r,并列入泵产品样本。标准还规定实际汽蚀余量NPSH要比(NPSH)r 大0.5m以上。
最大允许安装高度[Hg] 在一定流量下,泵的安装位置越高,泵的入口处压强p1越低, 叶轮入口处的压强pK也越低。当泵的安装位置达到某一极限高度时,则p1 =p1,min, pK=pv, 汽蚀现象遂将发生。从吸入液面0-0和叶轮入口截面K-K之间(见图1-58)列机械能衡算式, 可求得最大安装高度
(1-102)
在一定流量下,上式中的∑Hf(0-1)可根据吸入管的具体情况求出。实际使用(NPSH)r +0.5代替(NPSH)c,相应可得最大允许安装高度[Hg],即
(1-103)
式中,(NPSH)r即泵产品样本提供的必需汽蚀余量。
必须指出,(NPSH)r与流量有关,流量大时(NPSH)r较大。因此在计算泵的最大允许安装高度[Hg]时,必须使用可能达到的最大流量进行计算。
【例1-11】 安装高度的计算
由泵样本查知,IS65-50-160型水泵,在额定流量qV=25m3/h时,(NPSH)r=2.0m。现用此泵输送某种ρ=900kg/m3,pv=2.67×104Pa的有机溶液。假设吸入管路阻力损失∑Hf(0-1)=3m液柱,而供液处液面压强p0为大气压,试求最大允许安装高度[Hg]。
解:由式(1-103)
1.7.5 离心泵类型与选用
离心泵的类型 离心泵的种类很多,我国原第一机械工业部汇编的泵样本中列有各类离心泵的性能和规格。
化工生产中常用的离心泵有:清水泵、耐腐蚀泵、油泵、液下泵、屏蔽泵、杂质泵、管道泵和低温用泵等。以下仅对几种主要类型作简要介绍。
(1)清水泵 清水泵是应用最广的离心泵,在化工生产中用来输送各种工业用水以及物理化学性质类似于水的其他液体。最普通的清水泵是单级单吸式,其系列代号为“IS”, 结构如图1-59所示。如果要求的压头较高,可采用多级离心泵,其系列代号为“D”,结构示意于图1-60。如要求的流量很大,可采用双吸式离心泵,其系列代号为“Sh”。

图1-59 IS型离心泵
1—泵体;2—泵盖;3—叶轮;4—轴;5—密封环;6—叶轮螺母;7—止动垫圈;8—轴盖;9—填料压盖;10—填料环;11—填料;12—悬架轴承部件

图1-60 多级离心泵
(2)耐腐蚀泵 输送酸碱和浓氨水等腐蚀性液体时,必须用耐腐蚀泵,耐腐蚀泵中所有与腐蚀性液体接触的各种部件都需用耐腐蚀材料制造,其系列代号为“F”。
(3)油泵 输送石油产品的泵称为油泵。因油品易爆易燃,因此要求油泵必须有良好的密封性能。 输送高温油品(200℃以上)的热油泵还应具有良好的冷却措施,其轴承和轴封装置都带有冷却水夹套,运转时通冷水冷却。油泵的系列代号为“AY”,双吸式为“AYS”。
(4)液下泵 液下泵安装在液体贮槽内(见图1-61),对轴封要求不高,适于输送化工过程中各种腐蚀性液体,既节省了空间又改善了操作环境,无须灌泵。其缺点是效率不高。液下泵系列代号为“FY”。
(5)屏蔽泵 屏蔽泵是一种无泄漏泵,它的叶轮和电机联为一个整体并密封在同一泵壳内, 不需要轴封装置,又称无密封泵(见图1-62)。在工业生产中屏蔽泵常用以输送易燃、易爆以及具有放射性的液体。其缺点是效率较低。

图1-61 液下泵
1—安装平板;2—轴套管;3—泵体; 4—压出导管

图1-62 管道式屏蔽泵
1—电机机壳;2—定子屏蔽罩;3—定子;4—转子;5—闭式叶轮;6,13—止推盘;7—下部轴承;8—止推垫圈;9—泵体;10—O形环;11—轴;12—转子屏蔽套;14—上部轴承
离心泵的选用 离心泵的选用原则有两条:
①根据被输送液体的性质和操作条件确定泵的类型;
②根据具体管路对泵提出的流量和压头要求确定泵的型号。
在泵样本中,各种类型的离心泵都附有系列特性曲线(又称型谱图),以便于泵的选用。图1-63 为IS型离心泵系列特性曲线。此图以H~qV标绘,图中每一小块面积,表示某型号离心泵的最佳(即效率较高的)工作范围。利用此图,根据管路要求的流量qV和压头H,可方便地确定泵的具体型号。例如,当输送水时,要求H=45m,qV=10m3/h,选用一清水泵。则可按图1-63选用IS50-32-200离心泵。

图1-63 IS型离心泵系列特性曲线