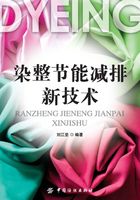
第一节 短流程前处理工艺
高效短流程前处理工艺起源于20世纪70年代,主要是受到当时的石油能源危机影响,西方国家的印染行业为了应对高能耗的前处理而研发的节能工艺。在随后的科技和精细化工发展的影响下,出现了各种高效前处理助剂和控制技术,使得前处理效率得到进一步提高,工艺流程缩短,为高效短流程前处理奠定了良好基础,并使其得到迅速发展。在高效短流程前处理工艺中,高效稳定剂和精练剂,以及不同设备单元优化组合起到了重要作用。通过缩短工艺流程,控制工艺条件,达到高效节能的目的。目前已成功应用的高效短流程前处理工艺,主要有一步法、二步法和酶氧无碱等工艺。其中一步法和二步法短流程工艺可节约水、电、汽30%~50%。
一、工艺过程及方法
织物高效短流程前处理,主要是通过浸轧→反应(冷堆法或汽蒸法)→洗涤三个基本过程,给予织物与处理液充分的反应条件,以获得高效、低能耗及良好的处理效果。织物在浸轧处理时可获得充分的吸透,并且带有较高的液量。织物轧堆后经历一个热处理过程,可保证堆置后织物上大量残存的助剂充分发挥作用,提高织物纤维的毛细效应。最后通过高效强力水洗,将织物上处理下来的杂质充分去除。为了保证这种“高、热、净”的处理效果,除了工艺上需要合理地确定处理液的组成,适当提高双氧水和烧碱的浓度,优选适合于新工艺的渗透剂、助练剂和稳定剂等外,设备还要配有与工艺相适应的高效短流程结构和装置。例如高给液装置、汽蒸以及高效或强力水洗单元等。通过这些单元对三个基本过程的有效作用,织物可在最低的能耗条件下达到最佳的处理效果。
缩短前处理工艺流程一般采用两种方法:一种是将传统的退、煮和漂合为一步,称为一浴一步法;另一种是织物经退浆后,将煮和漂合为一步,称为二浴一步法。二浴一步法工艺相对比较容易控制,但必须注意,在这之前,应选用棉籽壳少、退浆充分的半制品,否则难以取得良好的效果。水洗一般采用高效率水洗设备,可达到一次洗净效果。
通常,缩短前处理工艺流程会增加化学品的浓度,引发沉淀和分解,影响工作液在织物上的渗透扩散,给纤维织物、设备及操作带来了一定的风险性。对此,设法提高织物的带液量,就成为设备制造商的研究对象。提高织物带液量,可降低化学品浓度,并可避免织物在蒸箱中产生折痕。各种高给液的装置就是在这种背景下出现的。
二、一步法工艺
就是将传统的退浆、煮练和漂白三步过程改为退煮漂一浴汽蒸法进行,而退煮漂汽蒸一步半工艺则是先轧退浆液卷堆后,再轧碱氧液汽蒸1h(100~102℃)进行高效水洗。因堆置后是一步完成,故称为一步半工艺。有浆织物进行轧碱氧液堆置,轻浆轻薄织物则进行轧淡碱堆置。退煮漂一浴汽蒸的碱浓度和温度较高,双氧水的快速分解会造成织物损伤,需要降低烧碱和双氧水浓度,并加入性能优良的耐碱稳定剂。但是,对重浆和含杂量大的纯棉厚重织物难以达到所要求的处理效果,因此,该工艺仅适用于涤棉混纺织物和轻浆的中薄织物。
实施一步法前处理工艺,关键是要选用在较高碱浓度下对双氧水具有良好稳定效果的双氧水稳定剂。能够使双氧水在常温浓碱条件下,保持一定的稳定性,并在高温汽蒸分解过程中,只对织物中的浆料和纤维天然杂质产生氧化破坏作用,而不切断纤维素的大分子链,使纤维损伤程度控制在允许的范围内。
从目前应用的角度来看,实施一步法工艺必须建立在优化工艺、高效染化料和助剂、先进设备功能的基础上。因为一步法耗用的染化料和助剂量相对较大,并且有可能对纤维和织物的强度造成损伤,最后反而导致加工成本高,或产品质量下降。因而一步法工艺的推广应用还需要一个过程,尤其是一些中小型印染企业还缺乏这种条件。
三、二步法工艺
根据退、煮、漂的不同组合形式,二步法工艺可分为两种。一种是织物先经退浆,再经碱氧一浴煮漂,即:浸轧退浆液卷装堆置,高效水洗,然后浸轧碱氧液汽蒸(温度100℃,时间45~60min),高效水洗;或者是轧堆退浆,高效水洗,再高给液浸轧碱氧液,高效汽蒸(102℃短蒸2~4min),高效水洗。该工艺的织物退浆是单独进行并经过充分水洗,可以减少对煮漂的影响,故可适于含浆率较高的厚重紧密纯棉织物。考虑到碱氧一浴中的碱浓度较高,会加快双氧水分解,必须慎重选择氧漂稳定剂。另一种是织物先经退煮一浴处理,然后再采用常规漂白处理。即:浸轧碱氧液及精练剂,在100℃温度下汽蒸50~60min,高效水洗,然后再浸轧双氧水常规漂白,在100℃温度下汽蒸50~60min,最后再经过一次高效水洗。该漂白过程是采用常规传统工艺,故对稳定剂的要求不高。为了减少碱对双氧水的影响,要求退煮后必须进行充分水洗。由于漂白是在碱浓度较低的条件下进行的,双氧水的分解速率比较缓慢,所以对织物纤维的损伤较小。该工艺适用于含浆率较低的中薄纯棉织物和涤棉混纺织物。
从二步法工艺流程来看,不管是先退浆,还是先退煮合一工艺,都必须浸轧退浆、煮练或氧漂工作液,以及渗透剂等必要的助剂。由于在进行前处理之前的织物,有可能是纯棉坯布、烧毛后轧碱灭火的或者经冷轧堆置过的,织物上难免附着一些灰尘、杂质等,也有的坯布存在拒水性能的差异,因而很难使织物大量均匀地吸附工作液。为此,除了依靠渗透剂的作用外,还必须依靠机械的浸轧作用,将织物纤维之间所充满的空气排除,并均匀地吸附或渗透足够的工作液。采用高给液装置,织物可在较短时间内获得高带液量,满足工艺对蒸汽浓度的要求,同时又可避免织物在蒸箱内产生折皱印。
四、酶氧无碱工艺
值得注意的是,在传统的和短流程的纯棉织物前处理工艺中,都选用烧碱、表面活性剂等化学药品,在高温条件下对织物进行去除杂质。冷轧堆前处理尽管是低温,但烧碱浓度很高。这些碱残留在废水中,必然对环境造成污染。因此,如何消除这种影响,就成为前处理工艺的一个新课题。采用生物酶工艺替代传统的烧碱工艺和短流程的碱氧工艺,是近年来发展起来的一项具有环保性的前处理工艺。该工艺利用生物酶制剂特有的专一性、高效性、反应条件低、可自然降解、耗水少易洗尽、去杂效果好等特性,不仅减少了对环境的污染,而且还可降低能耗。
酶氧无碱前处理工艺与传统的碱氧前处理工艺不同,使用的助剂是由多种对纤维素杂质有专一分解作用的酶和一些化学助剂制成的复合精练酶代替烧碱,并与双氧水配合使用,用于棉织物的退浆和煮练。这种复合精练酶是由多种生物酶如果胶酶、纤维素酶、脂肪酶和蛋白酶等组成,具有高效的生物催化特性,在精练过程中能够使双氧水的漂白pH维持在10.5~11。在一定条件下对某种物质有专一的高效催化分解作用,可使织物坯布上的浆料、蜡质、果胶等杂质裂解而易溶于水,并在机械力的作用下脱落,达到退浆、煮练的效果。若再通过双氧水对织物的漂白作用,就具备了退、煮、漂一浴一步法前处理工艺条件。由于酶的催化作用具有高度的专一性和严格的选择性,只对棉纤维表皮(即角皮层与初生胞壁)的杂质产生去除作用,而不破坏初生胞壁中的纤维素成分,因而对纤维的损伤程度比传统的烧碱练漂工艺要小得多。
酶氧一浴练漂前处理工艺流程:织物毛坯→生物酶氧练漂→水洗。工艺条件:温度95℃,保温时间50min。工艺处方:生物酶2.0g/L;27.5%H2O2 5.0g/L;渗透剂1.0g/L。
五、工艺条件及控制
短流程前处理工艺将传统三步工序组合为一步或二步,并且织物中所要除去的浆料、蜡质和果胶等杂质,必须集中在一步或二步中完成,因而增加了烧碱(浓度要高数10倍以上)和双氧水(用量要高2.5~3倍)的用量,加速了各类反应速率。此外,还有其他各种高效助剂的用量也高于传统工艺,如高效渗透剂、乳化剂等,并且还要选用耐强碱浴的高效稳定剂。这种工艺条件虽然有利于棉蜡质乳化、油脂皂化、半纤维素和含氮物质水解、矿物质溶除以及木质素和浆料的溶胀,但双氧水在强碱浴中加快了分解,提高了纤维素氧化速率,使棉纤维更容易受到损伤。因此,必须严格控制工艺条件,以达到最终的处理效果。其中温度、时间、pH、双氧水和稳定剂等,是影响工艺条件的主要因素,可通过有效控制碱氧浓度和温度、织物带液量以及强化水洗等手段,获得一个合适的反应速率,使各类去杂反应在一定时间内完成,并且在完成去杂反应的同时,对纤维产生的损伤最小。
1.碱氧浓度 短流程前处理工艺的碱氧浓度控制非常重要,因为它直接影响到织物的处理效果和纤维的损伤程度。碱浓度过低会影响到织物纤维的毛细效应,过高又会影响织物白度,并且会降低织物纤维的强力。一般可采用中心旋转法进行工艺优化,以最少的试验次数获得最大的信息量。然后再通过回归方程的预测值,利用计算机绘出二维恒值图,优化出最佳工艺条件的某个区域,并能够直观地分析和比较各变量的影响大小及相互关系。在工艺优化选择过程中,应注意所使用的试验仪器和条件在整个试验过程中保持一致。为了使织物的去杂程度达到半制品质量要求,并且不损伤织物纤维,必须严格控制双氧水反应速率,并且要合理确定工艺处方(如烧碱、双氧水和各种助剂用量)。
2.碱氧液温度 在浸轧碱氧液时,其溶液温度不能高于织物温度,应保持在室温条件下。如果碱氧液温度高于织物温度,那么织物浸入溶液中,其纤维空隙中所含的空气将受热膨胀,就会阻止碱氧液的渗入。此外,碱氧液温度低还可防止双氧水的分解。
3.织物带液量 要达到短流程前处理工艺效果,应设法提高被处理织物的带液量。特别是未经处理的纯棉纤维具有拒水性时,必须加入适当的渗透剂,提高处理液对纤维渗透能力。考虑到处理液的碱性较强,应选用耐碱稳定性较好的渗透剂。尽管如此,还必须借助机械的浸轧作用,在较短的时间内将织物内的空气排出。采用高轧液率轧车可排出织物内部空气,在织物内外形成压力差,使处理液能够很快渗透到织物纤维内部,达到较高的织物带液率。此外,为了保证打卷时织物带液量、张力和线速度的前后一致性,应采用中心驱动的打卷方式。
4.强化水洗 短流程前处理工艺必须采用高效强化水洗,特别是冷堆后首先必须经过102℃的高温热碱处理,然后进行高效强化水洗。可采用高温低水位蛇形逐格倒流的高效水洗设备。
六、工艺实例
短流程前处理工艺在目前生产实践中已经得到了应用,并且获得了较好的节能减排效果。这里列举了一些印染厂的工艺应用实例。可能因各印染厂设备和工艺条件存在一定差异,因而具体工艺也有所不同。
1.针织物平幅练漂 织物:18tex纯棉单面针织物。
工艺流程:
进布→渗透除油→水洗→浸轧氧漂剂→汽蒸氧漂→热水洗→温水洗→水洗→轧水出布
使用设备:德国欧宝泰克(Erbatech)斯考特(Scout)平幅湿处理机。
工艺处方及工艺条件见表2-1。
表2-1 工艺处方及工艺条件
2.纯棉弹力薄型织物退煮一浴二步法工艺 工艺流程分为二步,工艺处方及工艺条件见表2-2。
表2-2 工艺处方及工艺条件
第一步流程:
平幅进布→单辊浸渍→2格高效平洗→浸渍→汽蒸→单辊浸渍→4格高效平洗→平幅落布
第二步流程:
单辊浸渍→浸渍槽→汽蒸→单辊浸渍→3格高效平洗→平洗→烘燥→平幅落布
3.纯棉厚重织物退煮一浴二步法工艺 工艺流程为二步,工艺处方及工艺条件见表2-3。
第一步流程:
平幅进布→单辊浸渍→2格高效平洗→浸渍→汽蒸→单辊浸渍→4格高效平洗→平幅落布
第二步流程:
单辊浸渍→浸渍槽→汽蒸→单辊浸渍→3格高效平洗→平洗→烘燥→平幅落布
表2-3 工艺处方及工艺条件
4.酶氧两段工艺 即酶退浆、碱氧煮漂二步法。织物品种:纯棉机织物29tex×36tex(20支×16支)、14.6tex×14.6tex(40支×40支)、4.4tex×5.8tex(133支×100支)。
工艺流程:
进布→平洗(浸轧酶,90℃)→轧车→平洗(浸轧酶,90℃)→轧车→酶堆(90℃、5min)→蒸洗箱→轧车→蒸洗箱→轧车→蒸洗箱→轧车→水洗箱→重轧车→过落布架→进布→浸氧漂液(平洗槽)→轧车→双层网带汽蒸箱(100℃、40~45min)→红外对中→4台蒸洗箱(配套3台轧车1台重轧车)→烘筒烘干→落布
工艺处方及工艺条件见表2-4。
表2-4 工艺处方及工艺条件
续表
与常规退、煮、漂三段工艺及低碱两段(碱氧)工艺相比,酶氧两段工艺主要有两点不同:一是原工艺退、煮段汽蒸主要采用双层网带汽蒸箱,存布量高达6000m。而现在选用新型高温松堆小蒸箱代替双层网带汽蒸箱后,容布量仅为300m,是原来的5%,缩短了生产周期;二是原工艺退、煮网带汽蒸箱前有三个蒸洗箱,后有五个蒸洗箱(四个热洗一个冷洗)。而酶氧工艺设备无须网带汽蒸箱,用高温酶堆箱代替,三个蒸洗箱只用两个平洗槽代替。由于酶退浆易水洗,原退浆后5个箱洗蒸,现只用4个蒸洗箱(三个热洗一个冷洗)。全机流程缩短,比原工艺设备排列长度缩短了15m。