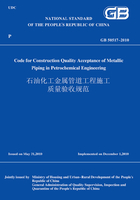
5.4 Examination and Acceptance for Other Piping Components
5.4.1 For quality certificates of other piping components,the following items shall be checked and shall comply with the requirements specified in product standards:
1 Chemical composition and mechanical properties;
2 Results of heat treatment and nondestructive test;
3 Other items specified in design documents and contract.
Method:check quality certificates.
5.4.2 Identifications including code number(trademark)of manufacturer,sizes,material grade and lot number shall be marked on exterior surfaces of piping fittings,and shall be consistent with quality certificates.
Method:visual examination,and check quality certificates.
5.4.3 Surfaces of piping fittings shall be smooth without any defects such as cracks and scale.Other defects on surface shall not exceed the permissible depth specified in the product standards.Machining accuracy of groove and threads shall meet the requirements specified in product standards.Welds of welded piping fittings shall be formed properly and rounded with base metal without any defects such as crack,incomplete penetration,incomplete fusion and undercut.
Method:visual examination and measurements checking.
5.4.4 Spectrum analysis or other tests shall be made for Cr-Mo alloy steel,cryogenic nickel steel,molybdenum austenitic stainless steel,nickel and nickel alloy,titanium and titanium alloy,zirconium and zirconium alloy piping fittings and flanges(blinds)to verify main alloy metal elements.5% of fabrication and at least one piece from each lot shall be spot examined.
Method:check test reports.
5.4.5 For piping fittings conveying extremely hazardous fluid or piping fittings at design pressure higher than or equal to 10MPa,proof nondestructive test shall be performedforexterior surfaces of piping fittings.5% of fabrication and at least one piece from each lot shall be spot examined.Test results shall conform to Grade I specified in current state standard JB/T 4730.4 Nondestructive Test of Pressure Equipment,Part 4:Magnetic Particle Test and Grade I specified in JB/T 4730.5 Nondestructive Test of Pressure Equipment,Part 5:Liquid penetration test.
Method:Checktest reports.
5.4.6 Quality of bends shall meet the following requirements:
1 No cracks;
2 No defects such as over-sintering and lamination;
3 Minimum wall thickness at bending shall not be less than 90% of the nominal thickness and the negative tolerance specified in design documents;
4 The dimension of bend after fabrication shall meet the requirements specified in design documents.Deviation of centerline of straight pipe shall not be more than 1.5mm/m and 5mm(Figure.5.4.6);
5 Bend flattening at any cross section shall conform to Table 5.4.6.
Method:visual examination and measurements checking.

Figure 5.4.6 Center deviation of bend
△-Centerline deviation of straight pipe
Table 5.4.6 Flattening of bend

Note:Flattening is the ratio of the difference between maximum outside diameter and minimum outside diameter at bending position after bending to outside diameter of pipe before bending.
5.4.7 Threads of bolts and nuts shall be intact without defects such as scratches or burrs.Machining accuracy shall meet the requirements specified in the product standards.Bolts and nuts shall be well engaged each other without loosing or seizing.
Method:visual examination.
5.4.8 Spectrum analysis shall be made for Cr-Mo alloy bolts and nuts used for piping at design pressure equal to or higher than 10MPa to verify and proof main alloy metallic elements.5% of fabrication and at lest one set of bolt and nut from each lot shall be spot examined.Hardness proof test shall be made for two sets of bolts and nuts from each lot.
Method:check spectrum analysis report and hardness test report.
5.4.9 Spectrum analysis shall be made for Cr-Mo alloy bolts and nuts used for piping at design pressure lower than-29℃to verify and proof main alloy metallic elements.5% of fabrication and at lest one set of bolt and nut from each lot shall be spot examined.Low temperature impact test shall be made for two bolts from each lot.
Method:check spectrum analysis report and impact test reports.
5.4.10 Spectrum analysis shall be made for Cr-Mo alloy bolts and nuts used for piping at design pressure higher than or equal to 400℃to verify and proof main alloy metallic elements.5% of fabrication and at lest one set of bolt and nut from each lot shall be spot examined.
Method:check spectrum analysis report.
5.4.11 Spot examination shall be performed for gaskets.At least one piece from each lot shall be examined and shall meet the following requirements:
1 Spiral wound gaskets shall be free from any loosing and warping,and gasket surfaces shall be free of any defects such as scratches,voids,irregularity and rust stains that may affect sealing performance;
2 Finished sizes,precision and smoothness of metal gaskets shall comply with design documents.Metal gasket surfaces shall be free of any defects such as cracks,burrs,recesses,radial scratches or rust corrosion;
3 The edges of non-metal gaskets shall be cut regularly,and the surfaces shall be flat and smooth without any defects such as porosities,lamination,wrinkles and scratches.
Method:visual examination and measurements checking.
5.4.12 Flanges shall be marked with identifications including standard number,sizes,materials and pressure rating,and shall be consistent with quality certificates.Flange facing shall be flat and smooth without any defects such as radial scratches.Lining connected to flange facing shall be flat,smooth and color uniform.
Method:visual examination,and check quality certificates.
5.4.13 Materials,sizes and types of compensating devices shall confirm to design documents.Dimensions and tolerance shall comply with the standards specified in design documents.
Method:visual examination and measurements checking.
5.4.14 Sizes,materials and identifications of breather valves,rupture disks and safety accessories shall confirm to design documents.The technical parameters included in quality certificates shall be consistent at design documents.Otherwise,they shall be rejected.
Method:visual examination,and check quality certificates.
5.4.15 Sizes,materials,types and identifications of other piping components shall comply with design documents.Quality acceptance criteria shall confirm to applicable product standards.
Method:visual examination,and check quality certificates.