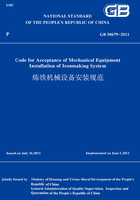
6.11 Installation of Large-diameter Coil-welded Steel Pipe
6.11.1 The installation of the large-diameter coil-welded steel shall be in accordance with the following requirements:
1 Fixed support shall be fixed before pre-stretching a compensator.The position,direction and prestretching value of the compensator shall meet the provisions of the design document.
2 The installation of sliding type support roller shall meet the provisions of the design document.The allowable deviation of the center line of the roller group is 10mm when there is no requirement in the design document.
3 The sliding surface of the guide support and the sliding support shall be clean as well as be free of deposit,skew and bite.The installation position shall meet the provisions of the design document.
4 The flange,welding seam and connecting piece on the pipe shall be set up to be convenient for construction and overhauling.The net distance between the ring welding seal and the support shall not be less than 50mm.
5 Filling(padding)between the flange joint surfaces shall meet the provisions of the design document.Before pipe lying,the flange sealing surface and the sealing gasket shall be checked and the pipe shall be free of scratch,spots and other defects that affect the sealing performance.Flange connection shall be in compliance with the relevant provisions of the current national standard GB 50235 Code for Construction of Industrial Metallic Piping Engineering.
6 The allowable deviation of installation of the large-diameter coil-welded steel shall be in accordance with the following requirements:
1)The allowable deviation of top elevation of the piping support is±15.0mm.The allowable deviation of the longitudinal and transverse centerline is 25.0mm.The allowable deviation of perpendicularity is 1/1000 of the height of the support and shall not be larger than 20.0mm.
2)The allowable deviation of elevation of the piping center line is±15.0mm.The allowable deviation of the longitudinal center lineis 20.0mm.The slope aspect and gradient shall meet the provisions of the design document.The allowable deviation of perpendicularity of the vertical pipe is 5/1000 of the effective length of the vertical pipe and shall not be larger than 30.0mm.
6.11.2 The pressure test of the large-diameter coil-welded steel shall be in accordance with the following requirements:
1 After completing the installation of the piping,the pressure test of piping shall be conducted and be in compliance with the provisions of the design document.The pressure test shall be taken by a pneumatic method when there is no requirement in the design document.
2 The pressure test of the large-diameter steel pipe of the blast furnace shall be taken in section and the classification of the test section shall be in accordance with the following requirements:
1)Plant cold blast pipe,from a distribution pipe of an air blower station to a cold blast discharge valve of the blast furnace.
2)In-plant cold blast pipe,from the cold blast discharge valve to a cold blast valve of the hot-blast stove and a mixed air stop valve.
3)From the washing tower and Venturi-tube washer to gas pressure regulating valve group and inlet valve of gas turbine of gas top pressure power generating set.
4)Clean gas main after gas pressure regulating valve group.
3 Before test,the pipes and temporary facilities for construction of process equipment shall be disassembled completely.The inside residues and garbage shall be cleaned up.The manhole cover,inspection hole cover and pipes of various metering meters and instruments shall be closed.The connecting bolt of the metal compensator shall be loosened.
4 The test shall be taken after the pipes in the pressure test section are installed completely and the welding seam has been passed through examination.Tapping and welding shall not be performed after test.
5 Warning line and obvious mark shall be set up in the pressure test area.The tested pipes shall not be beaten and clashed in the process of pressure rise and pressure stabilization.
6 The test pressure shall meet the requirements of the design document.When there is no requirement in the design document,the test pressure of the pneumatic method shall be 1.15 times of the working pressure,the pressure rise shall be gradually slow during test.When the pressure rises to 50% of the test pressure and no abnormality or leakage occurs,pressure rise shall be continued to perform gradually according to 10% of the test pressure,and the pressure shall be stabilized for 3min at every level till reaching the test pressure.After reaching the test pressure,the pressure shall be stabilized for 10min and then reduced to the design pressure.The pressure stop time shall be determined according to the requirements of leakage detection.A foaming agent shall be used for testing,and the test shall be qualified in case of no leakage tested.When the test pressure is below 0.010MPa,a U-shaped pressure meter should be adopted for testing.
6.11.3 The leakage test shall be taken from the hot blast main pipe,hot blast ring pipe,uptake duct,downcomer and dust remover to semi-clean gas pipe before the tower and be in accordance with the following requirements:
1 The leakage test shall be taken after the pressure test is qualified and the test medium shall be air.
2 The pressure for the leakage test shall be the design pressure.
3 The leakage test may be taken with the overall leakage test of the blast furnace together.
4 During leakage test,the welds,the flange joint,the socket threaded joint of measuring instrument,emptying valve,air release valve and drain valve shall be focused on checking with the foaming agent and they shall be qualified in case of no leakage.
6.11.4 The grouping of the hot air ring pipe shall be in accordance with the following requirements:
1 For the hot blast ring blast,the rack or the padding stool should be arranged around the blast furnace shell at the first layer of platform(taphole platform)of the lower frame for grouping.The upper surface of the rack or the padding stool shall be horizontal and the height difference shall not be larger than 2mm.
2 The height difference of the upper surface of the ring pipe shall be checked by level gauge,with the allowable deviation of 10.0mm.
3 Butt welding should be adopted between ring sections.The allowable deviation of alignment tolerance of joint is 2.0mm,and that of the joint end gap is-1.0mm to+2.0mm.
4 After grouping and welding,an electric hoist track below the hot air ring pipe should be installed.
6.11.5 The installation of the hot air ring pipe shall be in accordance with the following requirements:
1 For the lifting of the hot blast ring pipe,means of drag lifting of winch for pulley block,lifting of tower crane or other cranes,and lifting of hydraulic lifting device of bearing steel string may be adopted at the top of the lower frame of the blast furnace.
2 After lifting in place,the lower elevation of the ring pipe shall be checked by level gauge,with the allowable deviation of±10.0mm.The allowable deviation of relative height difference of the ring pipe is 10.0mm.
3 The distance between the inner diameter surface of the ring pipe and the blast furnace shell shall be checked by steel ruler,with the allowable deviation of±20.0mm.
4 Various suspenders shall be installed perpendicular to the ground.
6.11.6 The blast furnace stub pipe for gas export shall be in accordance with the following requirements:
1 The blast furnace stub pipe for gas export and blast furnace shell of the gas cover section shall be tapped and welded at the plant and lifted in place on the installation site.
2 When supplying the stub pipe for gas export and the blast furnace shell of the gas cover section respectively,the stub pipe shall be positioned after installing the blast furnace shell of the gas cover section,and the steel wire and the pendant shall be hung according to the 4-core point of 0°,90°,180° and 270° to adjust and center.The tapping and welding works shall be performed according to the requirements of the design document,Section 6.2 and Item 1 of Article 6.8.10 of this standard after the stub pipe is installed on the furnace top cover.
3 For the installation of the stub pipe,the height difference of the upper opening shall be adjusted and checked,with the allowable deviation of 10mm.The allowable deviation of the center distance between two adjacent pipes is±10mm,and that of the difference of the two diagonal lines of the upper opening center is 15mm.
6.11.7 The installation of the gas uptake duct,downcomer,three-way pipe or five way ball of the blast furnace shall be in accordance with the following requirements:
1 The three-way pipe or five way ball and upper and lower elbow pipes and straight pipes should be subject to grouping on the installation site.The grouping platform shall be arranged in accordance with the requirements of Item 3 of Article 6.4.8 of this standard.The allowable deviation of grouping shall meet the relevant requirements of the design document and the current national standard GB 50372 Code for Installation Acceptance of Metallurgical Machinery Ironmaking Equipment Engineering.
2 When the uptake duct is provided with the pedestal on the furnace top platform,the uptake duct base and pipe should be installed after installing the rigid frame and shall be positioned according to the 4-core point of 0°,90°,180° and 270° of the blast furnace.The allowable deviation of elevation of the pipe base is±10mm,and that of center distance of the adjacent pipe bases is±10mm.The allowable deviation of difference of two diagonal lines is 15mm.For installation in section,the elevation,center distance and the diagonal line shall be checked section by section,and control shall be in due time.The uptake duct shall be installed perpendicularly.The allowable deviation of perpendicularity is 1/1000 and shall not be larger than 20mm.
3 For the blast furnace having two downcomers,the straight pipe section of the downcomer shall be installed in the upper elbow of the up down and the Y-pipe of the gravity dust remover after the temporary support is arranged for fixing,the elevation of the two pipe ends shall be checked and adjusted as well as meet the requirements of the design document,the center line of the two pipe ends shall be overlapped,and the straight pipe sections of the two downcomers shall be installed respectively after the actually measured interface space is suitable for the dimension of the straight pipe section.
4 The downcomer may be lifted by the single crane or the double cranes in position.When lifting by the single crane,the selection of the lifting point shall be adaptable to the installation state of the pipe,inclination regulating measure shall be taken,the inclination of the downcomer duct shall be adjusted according to the angle as specified in the design document,and the downcomer shall be lifted in place.
5 The three-way pipe and the blow-off valve may be subject to grouping on the ground and shall be integrally lifted in place.
6 The five way ball should be subject to grouping and welding on the installation site and stress relieving treatment according to the design document and be integrally lifted in place.After lifting in place,the longitudinal and transverse centerline shall be adjusted and checked,with the allowable deviation of 30mm.The allowable deviation of elevation is±30mm.
6.11.8 The installation of the perpendicular flange of the piping connected with the valve shall be in accordance with the following requirements:
1 The perpendicularity of the perpendicular flange face shall be checked by steel ruler by hanging the pendant,and that of the horizontal center line of the flange face and that of the pipe shall be checked by the special tool.When the diameter of the flange is not larger than 1000mm,the allowable deviation is 1.0mm.When the diameter of the flange is larger than 1000mm,the allowable deviation is 1.0/1000.
2 The position precision of the bolt hole of the flange face shall be checked by steel ruler through hanging the pendant.In Figure 6.11.8,A1 shall be equal to A2,the difference of B1and B2 shall not be larger than 1/1000 of the pitch diameter of the bolt hole on the flange face and 2.0mm.

Figure 6.11.8 Positioning of bolt hole on flange surface
1-Valve flange;2-Hung center line;3-Pendant
6.11.9 The installation of an expansion joint of a metal bellows shall be in accordance with the following requirements:
1 Before installation of the expansion joint of the metal bellows,the surface of the bellows shall be checked free of cracks,weld splashes and scratches larger than the lower deviation of the thickness of the steel plate,pits and other defects.
2 When the expansion joint of the metal bellows is connected with the piping and equipment through butt welding,the orifices at both ends shall be opened with joints of 30°±2.5°.The welding quality shall meet the requirements of the design document.When the connection between the expansion joint of the metal bellows and the pipe and the equipment is butt welding of dissimilar steel,the procedure qualification test shall be taken,and the requirements of Section 6.2 of this standard shall be met.