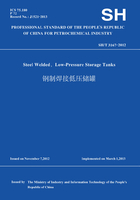
5 Design
5.1 General Requirements
5.1.1 Design temperature
Design temperature shall be determined according to the following requirements:
a)Design temperature shall be assumed to be the highest or lowest metal temperature of sidewalls and load-bearing elements under normal operating conditions;
b)Maximum design temperature of the tanks shall not be higher than 120℃;
c)The minimum design metal temperature of the tanks shall consider the minimum daily mean temperature at the site.For the tank without heat tracing and insulation,its design metal temperature shall be the minimum daily mean temperature at the site where the tank is constructed plus 13℃.Under design conditions,if the actual stress of load-bearing element does not exceed 1/3 of the allowable tension stress,consideration of the design metal temperature is not required for tank components that are not exposed to the liquid or vapor being stored.
5.1.2 Design pressure
Design pressure shall be assumed to be the pressure of gas or vapor space above the level in the tank(the volume of gas or vapor space above the highest level in the tank shall not be less than 2% of the volume of total liquid stored).Positive pressure shall not be less than the set pressure of relief valve,and negative pressure shall not be less than the maximum partial vacuum possibly developed in this space.
5.1.3 Loads
The following loads shall be considered in the design of tanks:
a)Hydrostatic head(density of liquid stored is the weight per cubic meter of liquid at 20℃.In any case,the minimum density shall not be less than 770kg/m3);
b)Positive gauge pressure and partial vacuum possibly developed during operation;
c)The weight of the tank and its contents;
d)Concentrated load,such as heavy duty instruments,valves installed on the top of the tank;
e)Dynamic load,such as loads resulting from the mixer installed on the top of the tank;
f)The supporting system,both local and integral,including the effect that is predictable from the nature of the foundation conditions;
g)Loads from platforms and stairways and where climatic conditions warrant,excessive snow;
h)Wind loads or seismic loads;
i)Loads resulting from connected piping;
j)The weight of any insulation and lining.
5.1.4 Thickness addition
The thickness addition shall be determined by formula(5.1.4):

where:c——Thickness addition(mm);
c1——Minus deviation of material thickness(determined in accordance with 5.1.4.1)(mm);
c2——Corrosion allowance(determined in accordance with 5.1.4.2)(mm).
5.1.4.1 Minus deviation of material thickness
The minus deviation of steel plate thickness shall be in compliance with the requirements specified in material standards.The minus deviation may be neglected,when it is not greater than 0.3mm,and not exceeds 6% of the nominal thickness.
5.1.4.2 Corrosion allowance
The corrosion allowance shall be considered to protect tank subjected to thinning by corrosion,erosion or mechanical abrasion.The requirements in details are prescribed in process datasheets.
5.1.5 Joint efficiency
Joint efficiency shall be determined based on type and position of joint and length ratio of the joint subject to the NDT.See Table 5.1.5.
Table 5.1.5 Maximum allowable efficiencies for arc-welding joints

Table 5.1.5(Continued)

Notes:a See 7.3 for examination requirements.
b Regardless of any values given in this column,the efficiency for lap-welded joints between plates with surfaces of double curvature that have a compressive stress across the joint from a negative value of pg or other external loading may be taken as 1;such compressive stress shall not exceed 4.8MPa.For all other lap-welded joints,the joint efficiency factor must be applied to the allowable compressive stress,Sca.The efficiency for full-penetration butt-welded joints,which are in compression across the entire thickness of the connected plates,may be taken as 1.
c All main butt-welded joints(all longitudinal or meridional,circumferential or latitudinal joints between sidewall plates)shall be completely radiographed as specified in 7.3 and nozzle and reinforcement attachment welding shall be examined by the magneticparticle method as specified in 7.3.
d Thickness limitations do not apply to flat bottoms supported uniformly on the foundation.
e A circumferential or latitudinal joints shall be considered subject to the same requirements and limitation as are longitudinal or
meridional joints when such a circumferential or latitudinal joint is located:
1) In a spherical,tori spherical or ellipsoidal shape or in any other surface of double curvature;
2) At the junction between a conical or dished roof(or bottom)and cylindrical sidewalls,as considered in 5.5;
3) At a similar juncture at either end of a transition section or reducer.
f The efficiency factors shown for fillet welds and plug welds are not to be applied to the allowable shearing stress values shown in the Table 5.1.6.6 for structural welds.
5.1.6 Allowable stresses of materials and walls
5.1.6.1 Nomenclatures
M——Ratio of the compressive stress,Sc to the maximum allowable compressive stress,Scs(M=Sc/Scs),less than 1.0;
N——Ratio of the tension stress,St,to the maximum allowable stress for simple tension,Sts(N=St/Sts),less than 1.0;
R——Inner radius of the wall(mm);
R1——Radius of curvature of the tank wall in the meridional plane,at the level under consideration(mm);
R2——Length of the normal to the tank wall at the level under consideration,measured from the wall of the tank to its axis of revolution(mm);
R3——Horizontal radius of the base of the cone,at any level under consideration(mm);
Sc——General variable for indicating a compressive stress(which may be either an allowable or computed value,depending on the context in which the variable is used)(MPa);
Sca——Allowable compressive stress Sca is lower than Scs because of the presence of a coexistent tensile or compressive stress perpendicular to it(MPa);
Scc——Calculated compressive stress at the point under consideration(MPa);
Scs——Max allowable longitudinal compressive stress of the wall(for a cylindrical wall,it is determined in accordance with the thickness-to-radius ratio)(MPa);
St——General variable for indicating a tension stress which may be either an allowable or computed value depending on the context in which the variable is used(MPa);
Sta——Allowable tensile stress is lower than Stsbecause of the presence of a coexistent compressive stress perpendicular to it)(MPa);
Stc——Computed tensile stress at the point under consideration(MPa);
Sts——Max allowable stress for simple tension as given in Table 4.2.2(MPa);
T1——Meridional unit force of latitudinal arc,in the wall of the tank at the level under conside-ration(T1 is positive when in tension,and T1 is negative when in compression)(N/mm);
T2——Latitudinal unit force of meridional arc,in the wall of the tank at the level under consideration(T2 is positive when in tension,and T2 is negative when in compression,and in cylindrical sidewalls,the latitudinal unit forces are circumferential unit forces)(N/mm);
t——Design thickness of the wall(mm).
5.1.6.2 Maximum tensile stresses
The maximum tensile stresses in the outside walls of a tank shall not exceed the applicable stress values determined in accordance with the following provisions:
a)If both the meridional and latitudinal unit forces,T1 and T2,are tensile or if one force is tensile and the other is zero,the computed tensile stress,Stc,shall not exceed the applicable value given in Table 4.2.2;
b)If the meridional unit force,T1,is tensile and the coexistent latitudinal unit force,T2,is compressive or if T2 is tensile and T1 is compressive,the computed tensile stress,Stc,shall not exceed a value of the allowable tensile stress,Sta,obtained by multiplying the applicable stress value given in Table 4.2.2 by the appropriate value of N obtained from Figure 5.1.6.2-1 for the value of compressive stress(Sc=Scc)and the correlated ratio of(t-c)/R involved.However,in cases where the unit force acting in compression does not exceed 5% of the coexistent tensile unit force acting perpendicular to it,the designer has the option of permitting a tensile stress of the magnitude specified in a)instead of complying strictly with the provisions of this paragraph.In no event shall the value of Sta exceed the product of the applicable joint efficiency for tension as given in Table 5.1.5 and the allowable stress for simple tension shown in Table 4.2.2.

Figure 5.1.6.2-1 Biaxial stress chart for combined tension and compression(for 200MPa to 260MPa yield strength steels)
Notes:1 At no time can a compressive stress for a particular value of(t-c)/R exceed Screpresented by curve OABC;no values of compressive stress or N are permitted to fall to the left or above this curve.
2 See Figure 5.1.6.2-2 for relationship between M and N.
3 If compressive stress is latitudinal,use R=R1;if compressive stress is meridional,use R=R2.

Figure 5.1.6.2-2 Reduction of design stresses required to allow for biaxial stress of the opposite sign
5.1.6.3 Maximum compressive stresses
Except as provided in 5.5.2.3 for the compression-ring region,the maximum compressive forces in the outside wall of a tank shall not exceed the applicable stress values determined in accordance with the following provisions.These rules do not purport to apply when the circumferential stress on a cylindrical wall is compressive(as in a cylinder acted upon by external pressure).However,values of Scs computed as a)(R=R1 when the compressive unit force is latitudinal;R=R2 when the compressive unit force is meridional),in some degree form the basis for the rules given in b),c),d),which apply to walls of double curvature.
a)If a cylindrical wall,or a portion there of,is acted upon by a longitudinal compressive force with neither a tensile nor a compressive force acting concurrently in circumferential direction,the computed compressive stress,Scc,shall not exceed a value,Scs,established for the applicable thickness-to-radius ratio as follows;
For values of(t-c)/R less than 0.00667,

For values of(t-c)/R between 0.00667 and 0.0175,

For valuesof(t-c)/R greater than 0.0175,

b)If both the meridional and latitudinal unit forces,T1and T2,are compressive and of equal magnitude,the computed compressive stress,Scc,shall not exceed the value,Sca,established for the applicable thickness-to-radius ratio as follows.
For values of(t-c)/R less than 0.00667,

For values of(t-c)/R between 0.00667 and 0.0175,

For values of(t-c)/R greater than 0.0175,

For austenitic stainless steel low-pressure tanks,for values of(t-c)/R≤0.0175,if modulus of elasticity of the material at design temperature is less than 2×105 MPa,or its yield strength is less than 205MPa,the allowable compressive stress are reduced accordingly in the proportion of the ratio of the allowable compressive stress to 2×105 or 205 respectively;
c)If both the meridional and latitudinal unit forces,T1 and T2,are compressive but of unequal magnitude,both the larger and smaller compressive stress shall be limited to values that satisfy the following requirements:

where:
Sl——Larger compressive stress(MPa);
Ss——Small compressive stress(MPa);
Scs——Allowable longitudinal compressive stress,compuated per a),determined in accordance with the thickness-to-radius ratio;Formula(5.1.6.3-7)is for larger stress,Sl,and Formula(5.1.6.3-8)is for smaller stress,Ss(MPa);
Note:In the previous expressions,if the unit force involved is latitudinal,R shall be equal to R1,if the force is meridional,R shall be equal to R2.
d)If the meridional unit force,T1,is compressive and the coexistent unit force,T2,is tensile,except as otherwise provided in e),or if T2 is compressive and T1 is tensile,the computed compressive stress,Scc,shall not exceed a value of the allowable compressive stress,Sca;determined from Figure 5.1.6.2-1 by entering the computed value of N and the value of(t-c)/R associated with the compressive unit stress and reading the value of Sc that corresponds to that point.The value of Sc will be the limiting allowable value of Sca for the given conditions;
e)When a local axial compressive buckling stress in a cylindrical shell is primarily due to a moment in the cylinder,then the allowable longitudinal compressive stress Scs or Sca,as specified in a),b),may be increased by 20%.If the shell bending is due to wind(tank full or empty)or due to earthquake(tank empty),then in addition to the above allowed 20% increase,the allowable buckling stress due to a moment can be increased an additional 1/3.For tanks full or partially full of liquid and for an earthquake induced longitudinal compressive stress,the allowable compressive stress need not be limited for biaxial stress as otherwise may be required by Figure 5.1.6.2-1.
For seismic design,the tank full is usually the worst case.For wind loading,the tank empty and with internal pressure is usually the worst case for local,bending induced compressive force.
5.1.6.4 Maximum shearing stresses
The maximum allowable shearing stresses in welds used for attaching manways,nozzles and their reinforcements or other attachments to the walls of a tank and in section of manway or nozzle necks that serve as reinforcement attachment shall not exceed 80% of the value of the applicable maximum allowable tensile stress,Sts,given in Table 4.2.2 for the kind of material involved,and shall not exceed 90% of yield strength of the material in case of austenitic stainless steel.Such maximum shearing stresses are permissible only where the loading is applied in a direction perpendicular to the length of the weld and must be reduced where the loading is applied differently.
5.1.6.5 Maximum allowable stresses for wind or earthquake loadings
The maximum allowable stresses for design loadings combined with wind or earthquake loadings shall not exceed 133% of the stress permitted for the design loading condition,and this stress shall not exceed 80% of yield strength unless otherwise specified.
5.1.6.6 Maximum allowable stress values or structural members and bolts
Maximum allowable stress values for structural members and bolts shall meet the following requirements:
a)The maximum stresses in internal or external diaphragms,webs,trusses,columns,and other framing,as determined for any of the loadings listed in 5.1.3 or any concurrent combination of such loadings expected to be encountered in the specified operation,shall not exceed the applicable allowable stresses given in Tables 4.5.1,Table 4.6.2 and Table 5.1.6.6.
b)Except as provided in c),the slenderness ratio(the ratio of the unbraced length,L,to least radius of gyration,r),for structural members in compression and for tension members other than rods shall not exceed the following values:
For main compression members-120;
For bracing and other secondary members in compression-200;
For main tension members-240;
For bracing and other secondary members in tension-300.
c)The slenderness ratio of main compression members inside a tank may exceed 120,but not exceed 200.Provided that the member is not ordinarily subject to shock or vibration loads and that the unit stress under full design loadings does not exceed the following fraction of the stress value stipulated in Table 5.1.6.6 for the member's actual L/r ratio:
f=1.6-L/(200r)
d)The gross and net cross sections of structural members shall be determined as described in the following provisions:
1)The gross sections of a member at any point shall be determined by summing the products of the thickness and the gross width of each element as measured normal to the axis of the member.The net section shall be determined by substituting for the gross width the net width whick,in the case of a member that has a chain of holes extending across it in any diagonal or zigzag line,shall be computed by deducting from the gross width the sum of the diameters of all holes in the chain and adding the following quantity for each gauge space in the chain;
s2/(4g)
where:s——Longitudinal spacing of any two successive holes(mm);
g——Transverse spacing of the same two holes(mm).
2)In the case of angles,the gauge for holes in opposite legs shall be the sum of the gauges from the back of the angle minus the thickness;
3)In determining the net section across plug or slot welds,the weld metal shall not be considered as adding the net area;
4)For splice members,the thickness considered shall be only that part of the thickness of the member that has been developed by the welds or other attachments beyond the section considered;
5)In pin-connected tension members other than forged eyebars,the net section across the pinhole,transverse to the axis of the member,shall be not less than 135%;the net section beyond the pinhole,parallel to the axis of the member,shall be not less than 90% of the net section of the body of the member;The net width of a pin-connected member across the pinhole,transverse to the axis of the member,shall not exceed eight times the thickness of the member at the pin unless lateral buckling is prevented;
e)External structural,or tubular,columns and framing subject to stresses produced by combination of wind and other applicable specified in 5.1.3 may be proportioned for unit stresses 25% greater than those specified in Table 5.1.6.6,if the required section is not less than that required for all other applicable loads combined on the basis of the unit stresses specified in Table 5.1.6.6.A corresponding increase may be applied to the allowable unit stresses in the connection bolts or welds for such members;
f)Allowable design stresses for bolts are established that recognize possible stressing during initial tightening.For flange bolts,these design allowable stresses also recognize additional stressing during overload and testing.
Table 5.1.6.6 Maximum allowable stress values of structural members

Table 5.1.6.6(Continued)

Table 5.1.6.6(Continued)

Notes:a The variables in thecompressive force equations are defined as follows:
L1——Unbraced length of the column(mm);
r——Corresponding least radius of gyration of the column(mm);
Y——Y=1.0 for values of t1/R≥0.015;Y=(2/3)[100(t1/r)]{2-(2/3)[100(t1/r)]}for values of t1/R<0.015;
R——External radius of the tubular column(mm);
t1——Thickness of the tubular column(mm).
b The variables in thebending stress equations are defined as follows:
L2——Unsupported length of the member;for a cantilever beam not fully stayed at its outer end against translation or rotation,L2 shall be taken as twice the length of the compression flange(mm);
d——Depth of the member(mm);
b——Width of its compression flange(mm);
t2——Thickness of its compression flange(mm).
c The variables in theshearing stress equations are defined as follows:
h——Clear distance between web flanges(mm);
t3——Thickness of the web(mm).