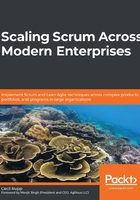
Summary
In this chapter, you have learned the basics behind Lean Thinking and its emphasis on adding value by eliminating waste. You now know that there are eight common forms of waste: waiting, overproduction, extra-processing, transportation, motion, inventory, defects, and unused human talent and intellect. And you have learned the five foundational principles behind Lean Thinking, including value, value streams, flow, pull, and perfection.
You should understand why value is always defined by the customer. With that understanding, you also know that the concept of design to value includes the specification of requirements and designs that maximize value as defined by the customer.
You've learned that a value stream is the set of all specific actions required to bring a product or service to the customer and that there are three critical value chains the organization must identify and analyze. These include value identification tasks, information-oriented tasks, and physical transformation tasks.
Next, you learned that Lean Thinking requires an organization to look at the efficiency of their flows across value streams. Flows include the efficiencies of movements and transactions of materials and information that participate in the activities spanning each value stream. Improvements to flow come from the elimination of batch processes, reductions in setup and changeover times, and matching capacities and throughput across each activity within the value stream.
Improving the efficiencies of flows is not the whole story. You now know that pushing information or materials into a value stream at a rate greater than the capacity of the slowest activity will break the value stream as a system. You've learned how to calculate production rates in the form of takt time.
Pushing orders into value creation and delivery activities causes queues to form, which delays throughput and hides defects that increase reworks and scrap. In addition, pushing in work just to fill large-scale batch processes increases costs and the probability that you will spend time and effort making things customers don't want. Instead, each value stream should pull items in at a rate that does not exceed customer demand, and never faster than the slowest activity in the value stream.
Finally, you've learned that seeking perfection is a desired goal that can never be obtained, but is always necessary. There are always things that can be improved, and sitting on one's laurels is a sure-fire way to slip back into bad habits and mediocrity.
We've spent enough time understanding the basic concepts of Lean Thinking. Since this is a book on scaling Scrum-Agile processes, let's see how Lean concepts help improve value and efficiency in software and systems development practices. That is the subject of the remainder of this section (in the next chapter).