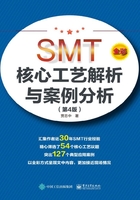
5.2 PCBA可制造性设计概述
概述
1.PCBA可制造设计的设计内容
PCBA可制造设计包括PCB的可制造性设计和PCBA的可组装性设计(或者说装配性设计)两部分内容,如图5-8所示。

图5-8 可制造性设计内容
PCB的可制造性设计侧重于“可制作性”,设计内容包括板材选型、压合结构、孔环设计、阻焊设计、表面处理和拼板设计等内容。这些设计都与PCB的加工能力有关,受加工方法与能力限制,设计的最小线宽与线距、最小孔径、最小焊盘环宽、最小阻焊间隙等必须符合PCB的加工能力,设计的叠层与压合结构必须符合PCB的加工工艺。因此,PCB的可制造性设计重点在于满足PCB厂的工艺能力,了解PCB的制作方法、工艺流程和工艺能力是实施工艺设计的基础。
而PCBA的可组装性设计侧重于“可组装性”,即建立稳定而坚固的工艺性,实现高质量、高效率和低成本的焊接。设计的内容包括封装选型、焊盘设计、组装方式(或称为工艺路径设计)、元器件布局、钢网设计等内容。所有这些设计要求,都是围绕更高的焊接良率、更高的制造效率、更低的制造成本来展开。因此,了解各类封装的工艺特点、常见焊接不良现象及影响因素非常重要。
不管PCB的可制造性设计还是PCBA的可组装性设计,都不能简单地围绕单独的设计要素来进行,比如元器件选型,0201对手机板而言是最常用的封装,而对通信板则不是,在进行设计时必须全面、系统地通盘考虑单板的工艺性,也就是本书一再强度的“一体化”设计概念!
2.PCBA可制造设计的设计流程
在PCBA的可制造性设计中,我们一般先根据硬件设计材料明细表(BOM)的元器件数量与封装确定PCBA的组装方式,即元器件在PCBA正反面的元器件布局,它决定了组装时的工艺路径,因此也称工艺路径设计;然后,再根据每个装配面采用的焊接工艺方法进行元器件布局;最后根据封装与工艺方法确定元器件之间的间距和钢网厚度与开窗图形设计,如图5-9所示。

图5-9 PCBA可制造设计流程
从图5-9我们可以看到以下几点:
1)封装是可制造性设计的依据和出发点
封装是可制造性设计的依据与出发点。不论工艺路径、元器件布局,还是焊盘、元器件间距、钢网开窗,都围绕着封装来进行,它是联系关联设计要素的桥梁。
2)焊接方法决定元器件的布局
每种焊接方法对元器件的布局都有自己的要求,比如,波峰焊接片式元件,要求其长度方向与PCB波峰焊接时的传送方向相垂直,相邻元件间距大于其相对比较高的那个元件的高度。
3)封装决定焊盘与钢网开窗的匹配性
封装的工艺特性,决定需要的焊膏量及分布。封装、焊盘与钢网等三者是相互关联和影响的,焊盘与引脚结构决定了焊点的形貌,也决定了吸附熔融焊料能力。钢网开窗与厚度设计决定了焊膏的印刷量,在进行焊盘设计时必须考虑到钢网的开窗与封装的需求。图5-10所示的两个图分别是0.4mm QFP不同钢网开口尺寸下焊膏熔融的结果,我们可以看到图5-10(a)比图5-10(b)设计要好,焊膏熔化后均匀地铺展到焊盘上,显示焊膏量与焊盘尺寸比较匹配,而图5-10(b)显示焊膏偏多,焊接时容易产生桥连。

图5-10 焊膏熔化后的铺展情况
4)可制造性设计与SMT工艺决定制造的良率
可制造性设计为高质量的制造提供前提条件和固有工艺能力(Cpk),这也是质量管理课程中提到“设计决定质量”的理由之一。
这些观点或逻辑关系是可制造性设计内在联系的体现,在可制造性设计时必须记住这些观点,以便以“一体化”的思想进行可制造性的设计。
3.PCBA可制造设计的基本原则
1)优选表面组装与压接元器件
表面组装元器件与压接元器件,具有良好的工艺性。
随着元器件封装技术的发展,绝大多数元器件都可以买到适合再流焊接的封装类别,包括可以采用通孔再流焊接的插装元器件。如果设计上能够实现全表面组装化,将大大提高组装的效率与质量。
压接元器件主要是多引脚的连接器,这类封装也具有良好的工艺性与连接的可靠性,也是优先选用的类别。
2)以PCBA装配面为对象,整体考虑封装尺度与引脚间距
对整板工艺性影响最大的是封装尺度与引脚间距。在选择表面组装元器件的前提下,必须针对特定尺寸与组装密度的PCB,选择一组工艺性相近的封装或者说适合某一厚度钢网进行焊膏印刷的封装。比如手机板,所选的封装都适合用0.1mm厚钢网进行焊膏印刷。
3)缩短工艺路径
工艺路径越短,生产效率越高,质量也越可靠。优选的工艺路径设计是:
(1)单面再流焊接;
(2)双面再流焊接;
(3)双面再流焊接+波峰焊接;
(4)双面再流焊接+选择性波峰焊接;
(5)双面再流焊接+手工焊接。
4)优化元器件布局
元器件布局设计主要指元器件的布局位向与间距设计。元器件的布局必须符合焊接工艺的要求。科学、合理的布局,可以减少不良焊点,可以减少工装的使用,可以优化钢网的设计。
5)整体考虑焊盘、阻焊与钢网开窗的设计
焊盘、阻焊与钢网开窗的设计,决定焊膏的实际分配量及焊点的形成过程。协调焊盘、阻焊与钢网三者的设计,对提高焊接的直通率有非常大的作用。
6)聚焦新封装
所谓新封装,不完全是指新面市的封装,而是指自己公司没有使用经验的那些封装。对于新封装的导入,应进行小批量的工艺验证。别人能用,不意味着你也可以用,使用的前提必须是做过试验,了解工艺特性和问题谱,掌握应对措施。
7)聚焦BGA、片式电容与晶振等应力敏感元器件
BGA、片式电容与晶振等属于典型的应力敏感元件,布局时应尽可能避免布放在PCB在焊接、装配、车间周转、运输、使用等环节容易发生弯曲变形的地方。
8)研究案例完善设计规则
可制造性设计规则来源于生产实践,根据不断出现的组装不良或失效案例持续优化、完善设计规则,对于提升可制造性设计具有非常重要的意义。
4.PCBA可制造性设计与制造的关系
PCBA可制造性设计与制造的关系可以归纳为两点:
(1)PCBA的可制造性设计决定PCBA的焊接直通率水平,它对焊接良率的影响是先天性的,较难通过现场工艺的优化进行补偿。
(2)可制造性设计决定生产效率与生产成本。如果PCBA的工艺设计不合理,可能就需要额外的试制时间和工装,如果还不能解决,就必须通过返修来完成。这些都降低了生产效率,提高了成本。
下面我们举一个0.4mm QFP的例子予以说明:
0.4mm QFP是广泛使用的一类封装,但它也是焊接不良排行前十的封装。主要的焊接不良表现为桥连和开焊,如图5-11所示。

图5-11 0.4mm QFP桥连和开焊现象
0.4mm QFP,之所以容易发生桥连,根本上是由于引线之间的间隔比较小,一般只有0.15~0.20mm,它对焊膏量的变动比较敏感。如果焊膏印刷稍微偏厚就可能引发桥连,因此,通常采取的改进举措是减薄焊膏印刷的钢网厚度,但这样做的结果可能带来更多的开焊。如果我们能够提供一个比较大的焊膏量工艺窗口,那么就可以有效地提高焊接的良率。
从工艺设计角度考虑,我们需要解决两个问题:一是如何控制焊膏量的变化;二是如何降低焊膏量对桥连的影响。如果我们能够解决这两个问题就能够很好地管控0.4mm QFP的焊接质量。
首先我们看一下0.4mm QFP的焊点结构与焊膏印刷的原理,如图5-12、图5-13所示。从图5-12我们可以看到,熔融的焊锡铺展在焊盘和引脚表面,焊盘的宽度决定吸附熔融焊锡的量。从图5-13可以了解到阻焊厚度对钢网与焊盘之间密封性的影响——如果阻焊层比较厚就会增加焊膏的量。
了解了这两点,我们就可以进行0.4mm QFP的工艺设计,具体讲就是通过对焊盘、阻焊和钢网的一体化设计,有效控制焊膏量的波动并降低焊膏量对桥连的敏感度。

图5-12 0.4mm QFP焊点截面结构示意图

图5-13 焊膏印刷原理
如果我们把焊盘设计得比较宽一点、钢网开窗设计窄点、去掉焊盘之间的阻焊,如图5-14所示,那么,就可以获得稳定的焊膏量(去掉了阻焊对焊膏印刷厚度的影响)、可以适应焊膏量变化的焊缝结构(宽焊盘窄的钢网开窗),从而为实现了少桥连甚至不桥连的工艺目标。实践证明,这样的设计完全可以解决0.4mm QFP的桥连问题。

图5-14 0.4mm QFP的工艺设计