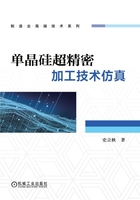
2.1 切削的基本理论
2.1.1 切削变形区
为便于对切削过程的分析,应首先了解切削变形区的划分。如图2-1所示,切削中的工件根据其塑性变形特性可分为以下三个变形区:
第Ⅰ变形区:这个区域的材料在进入该区之前只有弹性变形,进入之后发生剪切变形并随之出现加工硬化[59],因此又叫作剪切区。
第Ⅱ变形区:当切屑已经形成并沿刀具前面与工件材料分离时,切屑上底部的材料同前面接触受到强烈的挤压和摩擦,使这部分材料再次变形并流动变缓。
第Ⅲ变形区:已加工的工件表面受到切削刃下方的挤压和后面的摩擦,这个区域的材料再次发生变形。

图2-1 切削过程中的三个变形区
这三个变形区都随着刀具的向前运动而移动,且都集聚在切削刃附近。三个变形区的应力比较集中而且复杂,切屑与工件在第Ⅰ变形区分离,随后切屑在第Ⅱ变形区和已加工表面在第Ⅲ变形区分别受到前面和后面的挤压和摩擦。
2.1.2 超精密切削机理及最小切削深度
1.超精密切削机理
超精密加工就是在超精密机床设备上,对材料进行微量切削,以获得镜面和很高形状精度的加工过程,其精度从微米到亚微米,乃至纳米[60]。用金刚石刀具在精密机床上进行超精密切削,还可在芯片基底上加工出高精度的微纳结构。精密切削的切削深度非常小,最小切削深度可达到1nm。精密切削使用的单晶金刚石刀具要求刃口极为锋利,切削刃钝圆半径为0.5~0.01µm[61]。
在实际超精密切削工件材料时,切削刃和前面的主要任务是去除工件上的材料,刀具前角γ和切削刃钝圆半径ρ的大小直接影响塑性变形的程度和切屑形状,并对切削过程中产生的物理现象和已加工表面质量产生显著影响。超精密切削时,工件材料被通过分流点O且平行于已加工表面的分流线分为上、下两部分[62](见图2-2),分流线以上的材料(也称为切削层)沿前面向上移动形成切屑,分流线以下的材料(也称为塑性变形层)被O点以下的切削刃碾压和受到后面的摩擦后形成已加工表面。这个过程中被加工的工件材料经过后面的挤压产生压缩弹塑性变形,塑性变形不可恢复,已加工表面残留压应力,对已加工表面质量产生影响。三个变形区的应力状态十分复杂,应力集中造成工件材料中的位错集中,导致工件产生塑性变形和滑移分离。刃口半径越小,越能进行极薄的超精密切削加工,其切削刃前方的材料应力越集中,越易变形,加工表面质量好。

图2-2 精密切削原理
2.最小切削深度
超精密切除加工方法所能达到的加工精度取决于这种加工方法能够移除的极限最小切削深度hDmin。能切除的hDmin越小,工件材料抵抗塑性变形的能力越强,工件最终工序的最小切削深度应等于或小于零件的加工精度(允许的加工误差)。因此最小切削深度反映了它的精加工能力。
在精密和超精密切削中,极限最小切削深度hDmin与切削刃钝圆半径ρ有密切的关系[63],如图2-3a所示。A为极限临界点,A点以上的工件材料受到刀具挤压后,将堆积起来形成切屑,与工件分离。而A以下,被加工的材料经弹塑性变形而形成已加工表面。

图2-3 最小切削深度与切削刃钝圆半径关系图
现在对A点的受力情况进行分析。如图2-3b,在A点处工件受水平力Fx和垂直力Fy作用。这两个力也可分解为A点处的切向力µN(µ为摩擦因数)和法向力N,则N和µN可用下式计算:

化简后为

在实际摩擦力(µN)′大于µN为前提时,切削刃钝圆半径处的圆弧与正在切削加工中的材料没有相对滑移,分流线以上的材料将随切削刃前进,逐渐堆积,最后形成切屑而被切除。故:

极限最小切削深度hDmin应为

化简后为

分析上述方程可知,当切削刃钝圆半径ρ为某一值时,能切下的最小切削深度hDmin和临界点处的yF 比值、刀具工件材料间摩擦因数有关。当切削深度小于最小切削深度很多时,在工件表面产生弹性变形,随着切削的继续进行,已加工表面弹性恢复,没有切屑产生;随着切削深度的增加,切削深度仍然在最小切削深度以下,工件表面将会残留下刀具经过的塑性变形,此时也没有切屑产生;当切削深度大于最小切削深度时,便开始产生切屑。
切削时,A点处的F 比值一般在0.8~1范围内。对于用金刚石刀具的超精
密切削,根据经验可以取Fy=0.9Fx。由文献[64]可知金刚石刀具与单晶硅之间的摩擦因数µ是0.07。用前面的公式可以算出:在Fy=0.9Fx,µ=0.07时,hDmin=0.316ρ。
3.单晶硅单层膜的制备概述
在微纳机电系统中,单晶硅构件相对运动界面间的黏附、摩擦和磨损将影响系统的可靠性和寿命。为此,在单晶硅构件表面自组装一层低摩擦因数的结构,以改善单晶硅表面的黏附性,成为解决这类润滑问题的主要途径。微纳结构的加工是先按照人为设计的图案,通过机械刻划达到微纳结构在形状位置上的可控,同时结合在溶液中的有机分子的化学自组装技术,在机械刻划后的结构图形上连接不同末端基团的有机分子。利用机械-化学方法在单晶硅表面自组装单层膜和制造自组装微纳结构,这个过程需要在液态环境中进行,首先通过机械刻划(本书使用的是金刚石刀具刻划)使单晶硅表面的化学键如Si—O或Si—H、Si—Si键断裂,形成单晶硅的自由基,进而引发它们与溶液中含有的有机分子共价结合以形成表面单层膜结构和微纳结构,实现单晶硅表面的功能化。