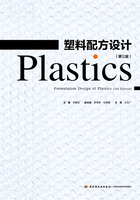
第三节 塑料摩擦改性配方设计
一、塑料的摩擦与磨损方式
塑料的摩擦性和磨损性是两个既相互独立又相互联系的概念。
摩擦是指两个接触物体之间有相对运动或相对运动趋势时,在其相互接触表面产生的阻碍相对运动的机械作用。摩擦可分为滑动摩擦、滚动摩擦和滑动与滚动同时存在摩擦,也可分为动摩擦和静摩擦,还可分为干摩擦和湿摩擦。衡量摩擦性大小的参数为摩擦因数,其大小与滑动介质、润滑状态、温度、介质表面粗糙度及负荷等因素有关。
塑料的耐磨性可用磨耗来表示,磨耗指两个物体在相对摩擦过程中接触面上物质不断损失的现象,也称为磨损。塑料的磨损方式通常分为四种类型:黏着磨损、化学磨损、磨粒磨损及疲劳磨损。在实际摩擦过程中往往是多种机理并存,其中一两种占主要地位。
(1)黏着磨损
这是一种最常见的磨损方式,其重要特征为软的聚合物向硬质摩擦副的转移。聚合物的内聚能大小,决定黏着磨损的转移方向,材料总是从内聚能小的材料向内聚能大的材料转移。
(2)化学磨损
聚合物的化学磨损主要是以化学降解和氧化的形式进行。降解的原因是滑动界面产生的高温使某些聚合物发生降解反应,另外在滑动过程中填料与聚合物、聚合物与摩擦副之间会发生化学反应,当这种反应使磨损量加大时,也是化学磨损的一种形式。
(3)磨粒磨损和疲劳磨损
两者都是由于粗糙的接触表面所导致,粗糙表面上凸起材料的刮削脱落,从而导致磨粒磨损。
材料表面的凸起材料也会引起材料的局部应力集中,在交变应力的作用下材料会发生疲劳磨损。
塑料与不同摩擦副配合时,其磨损程度和磨损方式不同,具体情况如下:
①塑料与较硬金属如钢配合时,黏着磨损较小。
②塑料与较软金属如黄铜、铝合金配合时的磨损较大。如金属表面不平,会产生所谓“剥蚀磨损”;如金属表面光滑如镜,则会产生“黏着磨损”。
③塑料与异种塑料配合时,黏着磨损很大。其具体磨损程度,视异种塑料与塑料的适应性而变化;如PBT和PA与POM的亲和性低,不易产生黏着磨损;而ABS和PP与POM的亲和性高,易于产生黏着磨损。
④塑料与同种塑料配合时,因其亲和性大,其黏着磨损很大,比与金属和异种塑料都要大。
二、塑料减摩、耐磨配方设计
减摩性塑料具有低摩擦、自润滑、耐磨、耐腐蚀、减震吸振、降低噪声、密度小、比强度高、加工简便、压缩和疲劳强度高、抱合性、嵌埋性、顺应性和抗胶合性等优点。减摩塑料可解决金属难以克服的许多问题,节省大量贵重金属,减轻设备质量,降低成本。
减摩性塑料的缺点为刚性、蠕变性、导热性和耐热性不高,只能用于低载荷、低转速、常温和界面散热条件好的场合使用。
减摩性塑料为在热塑性和热固性树脂中添加有机或无机减摩材料,最早的减摩材料开发于20世纪20年代的石墨填充酚醛树脂和可浸油的酚醛树脂,以后陆续开发了尼龙、PTFE、POM、PI、UHMWPE及环氧基减摩材料。
减摩性塑料复合材料的组成:
①基础树脂:PTFE、POM、PA、聚苯酯、氯化聚醚、UHMWPE、PI、PF及EP等;
②减摩润滑组分:PTFE、润滑油、石墨、二硫化钼、二硫化钨、铅、氧化铅及铟等;
③耐磨组分:石墨、二硫化钼及耐磨聚合物等;
④增强组分(硬度、强度、耐蠕变性):玻璃纤维及碳纤维等;
⑤导热组分:软金属如青铜粉、铅粉、氧化铅粉及炭黑等;
⑥热稳定组分:热稳定剂及抗氧剂等。
(一)基础树脂
常用的耐磨聚合物如表4-78所示。
表4-78 常用耐磨聚合物对干钢的摩擦系数和耐磨性

F4具有低摩擦因数(已知树脂中最低)、优异自润滑性、高度不黏性,但耐磨性差、压缩蠕变大、尺寸稳定性差、导热性差、力学性能一般,加工性能不好。
聚苯酯为聚对羟基甲酸苯酯,为芳香族聚酯系聚合物,高结晶、不溶不熔。耐热性好、分解温度530℃、可在300℃长期使用,具有良好的自润滑性、耐磨性,导热系数大(比PA、F4大3~5倍),耐辐射,耐一切有机溶剂,绝缘性优良。
(二)减摩组分
1.低摩擦因数聚合物
聚四氟乙烯聚合物,其摩擦因数仅为0.13。在PA6中加入15%的改性F4,其摩擦因数可由0.41降低到0.24。
2.有机润滑油和润滑脂
具体品种有石油系润滑油、合成润滑油、植物油、动物油、各种表面润滑剂等。其改性原理为:利用润滑剂向聚合物和摩擦副表面迁移和扩散,在聚合物和摩擦副表面形成转移油膜,使聚合物与摩擦副之间的摩擦转换成润滑剂本身的分子滑移,从而减小了聚合物与摩擦副之间的摩擦阻力,提高聚合物的耐磨性和极限PV值、降低摩擦因数、改善耐蠕变性能,特别适合于塑料与光滑金属表面配合,有效防止黏着磨损。不足之处为力学性能和硬度略有下降。
为提高润滑剂在聚合物中的分散性,防止在加工中油类析出,往往需要加入少量表面活性剂和超细的PT-FE、石墨、二硫化钼等作为吸油载体。
3.无机润滑剂
无机润滑剂主要包括:具有层状结构的石墨、氟化石墨、二硫化钼等,具有层状结构的无机润滑剂可在摩擦力和剪切力作用下,在层片之间发生相对滑移,在摩擦副表面生成转移膜,减小摩擦因数,提高耐磨性。
(三)耐磨组分
1.无机耐磨组分
①添加金属粉末,常用的金属粉末有:铅粉、青铜粉、铜粉、纳米铜粉、锌粉、锡青铜粉、巴氏合金、高锡铝合金、镍粉和硒粉等,但以纳米铜粉效果最好,它与聚合物基体的结合好,比界面产生的擦伤作用较弱,造成的磨粒磨损较小,使耐磨性有较大提高。例如,在PTFE中填充锌粉、镍粉和硒粉,可使其磨损率降低到1/1000。
②金属氧化物:主要为SiO2、B2O3、Al2O3、CuO、La2O3、Pb3O4及Fe2O3等。
③碳化物:主要为石墨、氟化石墨、二碳化三铬和碳化硅等。
④硫化物:主要为MoS2、CuS及Ag2S等。
⑤氮化物等:主要为氮化硅、粒径小于1μm球形陶瓷粉末及CuF等。
无机耐磨组分加入树脂中后,复合材料的耐磨明显提高。例如,用氧化铜、硫化铜、四氧化三铅填充HDPE,可使其磨损量降低到1/15。再如,用三氧化二钇、二氧化硅填充PTFE,可使其磨损量降低到1/1000。
2.耐磨聚合物
不同耐磨聚合物品种可以互相共混,以提高其耐磨性能。其具体改性原理为:耐磨性聚合物析出在主体聚合物的表层附近,使主聚合物表面与摩擦副表面之间的摩擦,转化为耐磨聚合物与摩擦副之间的摩擦,限制了摩擦副表面上较尖锐部分的磨损和磨粒对主体聚合物表面的嵌入深度,有效地抑制了犁切裂纹和疲劳断裂点的生成,防止诱发大面积的黏着磨损。
常用的耐磨聚合物有:聚苯酯、PI、UHMWPE、PBT、LCP、氯化聚醚、PPS、PAR等。例如在POM中加入20%UHMWPE,可使改性POM的自润滑性大幅提高,摩擦因数由0.26降为0.20,磨耗由3.5mg降为1.0mg。
(四)增强组分
添加玻璃纤维可提高聚合物的耐磨性、提高其力学性能和导热性能,但使摩擦因数增大。添加碳纤维的聚合物不仅力学改性效果更好、耐磨性显著提高,而且摩擦因数下降。添加芳纶纤维的聚合物在提高力学性能的同时,可显著降低摩擦因数,降低磨损率。添加纤维耐磨改性一般不单独使用,往往与PTFE或有机硅协同使用。
(五)导热组分
主要有金属粉、金属纤维、石墨、炭黑及碳纤维等。用于将动摩擦材料因摩擦起热产生的热量迅速转移,以免引起热裂解反应,降低材料的性能。
(六)几种常用减摩耐磨复合材料配方
1.PTFE
最常用的减摩耐磨复合材料,其本身具有最低的摩擦因数和自润滑性,在润滑不良或无油润滑条件及苛刻工作环境下使用最广。PTFE的不足之处在于力学性能低、PV值低、易冷流蠕变、不耐磨、导热性差及热胀系数大等缺点,必须经过综合改性形成复合材料才可应用。
PTFE(又称F4)减摩耐磨复合材料常用的填充材料有:玻璃纤维、碳纤维、石墨、二硫化钼、青铜粉、铅粉及氧化铅粉等。主要目的改善材料的耐磨性、力学性能、导热性,提高PV值。例如,对于PTFE+青铜+铅(或氧化铅)复合体系,在摩擦热效应和青铜的催化作用下,会发生PTFE与铅(或氧化铅)化学反应,生产有机氟化物,在摩擦表面上形成牢固的附着膜,大幅度提高耐磨性。对PTFE减摩、耐磨性配方而言,实行多元填充的耐磨性好。
举一最佳配方如下:
PTFE:58%~62%;青铜:2%~4%;铅:36%~38%。
可使耐磨性提高250倍,摩擦因数降低30%。
其他PTFE减摩、耐磨配方见表4-79和表4-80所示。
表4-79 PTFE常用的减摩耐磨复合材料配方

表4-80 聚苯酯改性PTFE耐磨复合材料

为改善与共混物的相容性,F4的相对分子质量应该低,采用无自凝性且易分解的F4,粒度为5~30μm超细为好。聚苯酯的粒度越细,耐磨性越好。此配方的优点为不损伤对磨材料。
再举一个沉淀BaSO4填充F4耐磨配方实例:
F4:77%;沉淀BaSO4:23%。
磨痕宽度:4.62mm(纯F4为8.49mm);磨损量:2.4mg(纯F4为29.3mg);摩擦因数 μ:0.218(纯F4为0.195)。
2.PA
PA具有突出的自润滑性,其磨耗量和摩擦因数都很小,是理想的耐磨材料。
填充成分为:玻璃纤维、碳纤维、润滑油、炭黑、石墨、二硫化钼及金属粉末等,目的提高其强度、刚性、耐磨性、导热性和耐候性等。
例如MC尼龙用润滑油处理后,制成的含油MC尼龙摩擦因数为0.12,接近F4;相对磨损量为1,是纯MC尼龙的1/4。
又如PA6的玻璃纤维耐磨改性配方:
PA6:75;玻璃纤维:15;改性F4:10;铜粉:适量。
此配方的具体性能为摩擦因数0.24,热变形温度165℃,冲击强度9.8kJ/m2,弯曲强度91MPa。
再如UHMWPE改性PA6配方:
PA6:72; HDPE-g-MAH:8; UHMWPE:20。
还有,在PA1010中加入15%的La2O3,其摩擦因数会从0.87降低到0.33,磨损率降低一个数量级。PA1010/CF/CuO三者以70/20/10比例混合,其耐磨性和摩擦性能好。
3.POM
POM的摩擦性和耐磨性好,具有优异的自润滑性和较高的极限PV值。POM的减摩耐磨改性主要填充F4、UHMWPE、LDPE、玻璃纤维、碳纤维、润滑油、石墨、二硫化钼及金属粉末(铜、铅)等。例如含油POM的减摩耐磨性明显提高,摩擦因数由0.33~0.46降低到0.21~0.25,磨痕宽度由12.4降低为3.0~4.2,极限PV值(0.5m/s)由2.13提高到39。
(1)润滑油改性POM耐磨配方
①POM/30#机油/硬脂酸锂/石墨比例为92/5/0.5/2.5。
②POM/润滑油/硫酸钡比例为89/7/4。
③POM/19#压缩机油/3#表面活性剂比例为100/(5~7)/1。相关性能:摩擦因数0.21~0.25,磨痕宽度3.0~4.2mm/40min,极限PV值3.9(0.5m/s)。
④POM/70#机油/硬脂酸比例为100/10/0.5。
⑤POM/70#机油/硬脂酸钙比例为100/10/1。
⑥POM/石墨/锭子油比例为80/10/10。
⑦POM/二甲基硅油比例为100/2。
⑧POM/二甲基硅油/乙烯基硅橡胶比例为89/9/2。
(2)聚四氟乙烯改性POM耐磨配方
①POM/聚四氟乙烯比例为100/10~20。
②POM/乳液聚四氟乙烯比例为100/5~20。
③POM/聚四氟乙烯/铅比例为100/5/10。
④POM聚四氟乙烯/铜比例为100/5/20。
⑤POM/聚四氟乙烯/锡比例为100/5/16。
⑥POM/聚四氟乙烯/锑比例为100/5/14.5。
POM/聚四氟乙烯的性能见表4-81所示,POM/聚四氟乙烯/金属粉的性能见表4-82所示。
表4-81 POM加入聚四氟乙烯的耐磨性

表4-82 POM/聚四氟乙烯/金属粉复合材料的耐磨性

(3)POM固体耐磨性配方
①POM/石墨比例为100/(5~20)。
②POM/石墨/氟化石墨比例为100/16/19。
③POM/二硫化钼比例为100/2。
④POM/二硫化钼/聚苯醚比例为100/3/3。
(4)POM酯类耐磨性改性配方
①POM/乙二醇碳酸酯比例为(80~99)/(1~20)。
②POM/二月桂酸1,3-丁二醇酯比例为98.75/1.25。
③POM/季戊四醇四醋酸酯比例为93/7。
(5)POM铁粉耐磨改性配方
POM(F30-03):100;氧化镁:0.1;抗氧剂1010:0.3;三聚氰胺:0.2;硬脂酸钙:0.2;铁粉(1μm,用2%的NDZ-201处理):4。
加工工艺:双螺杆挤出机造粒,注塑样品条。
相关性能:摩擦系数由0.13下降到0.1,磨损量下降50%。
4.PF
采用石墨、二硫化钼、氧化铅、石棉、F4、铜粉、铅粉、石英砂、玻璃纤维及碳纤维等,可使PF的耐磨性和PV特性得到改善。
具体配方如下:
改性PF:42%;石墨:15%;酸洗石棉:33%;六次甲基四胺:6.3%;二硫化钼:2.7%;油酸:1%。
具体性能:
①摩擦因数:干摩擦0.17,蒸馏水润滑摩擦0.035。
②磨痕宽度:干摩擦2.9mm,蒸馏水润滑摩擦1.15mm。
5.聚芳醚酮
表4-83 酚酞聚芳醚酮耐磨性改性配方

聚芳醚酮为摩擦和耐磨性优异的耐热性聚合物,为进一步提高其耐磨性,可用玻璃纤维、碳纤维、二硫化钼、铜粉、石墨及LCP等改性。以酚酞聚芳醚酮为例,其具体耐磨改性配方如表4-83所示。
6.聚苯硫醚
PPS虽然具有高的强度、耐热性和耐腐蚀性,但耐磨性和摩擦性都不高,其摩擦因数高达0.362,磨损体积高达13.60mm3,因此用于耐磨场合需要进行摩擦耐磨改性。
以含30%玻璃纤维PPS加入PA66为例,具体改性效果见表4-84。
表4-84 不同PA66含量对PP/PA66/GF(30%)体系性能的影响

7.UHMWPE
①纳米氧化物:主要为三氧化二铝、二氧化锆、氧化锌和二氧化硅等。如在UHMWPE树脂中加入10%的二氧化锆,磨损率下降64%;再如在UHMWPE树脂中加入2%的二氧化硅和2%的氧化锌,磨损率下降85%。
②碳纳米管(CNFs):如在UHMWPE树脂中加入0.5%的碳纳米管,磨损率下降45%。
③天然珊瑚:如在UHMWPE树脂中加入35的天然珊瑚,磨损率下降70%。
④交联改性:如UHMWPE在50kGy的电子束辐射下交联,磨损率下降46%;再如UHMWPE在300℃温度熔融后于150kGy的电子束辐射下交联,磨损率下降87%。
三、塑料摩阻配方设计
(一)摩阻性塑料复合材料概述
摩阻性塑料复合材料指具有较高摩擦因数、可以起到制动和传动作用的一类多组分材料。主要用于制造制动器上的制动衬片如汽车刹车片,传动装置上的离合器面片。
摩阻性塑料复合材料的主要性能指标如下。
1.较高的摩擦因数
摩阻性塑料复合材料摩擦因数的大小,显示其制动和传动能力的强弱。摩擦因数的下限是保证使用要求的最低摩擦力界限,上限是避免因摩擦力过大而造成振动、卡死、龟裂等现象的最高摩擦力界限,一般摩擦因数在0.35~0.45之间比较理想。视具体应用场合的不同,摩擦因数的大小要求不一样,具体见表4-85所示。
表4-85 不同使用场合对摩阻性塑料复合材料摩擦因数的要求

2.较低的磨损率
人们希望摩阻性塑料复合材料具有较低的磨损率,以获得较长的使用寿命。表4-86为国家标准规定的摩阻性塑料复合材料在不同应用场合下的最高体积磨损率。
表4-86 不同使用场合对摩阻性塑料复合材料最高体积磨损率的要求 单位:mm3/(N·m)

3.摩擦因数和磨损率的热衰退性
摩阻性塑料复合材料摩擦因数和磨损率的热衰退性指随摩擦滑动时温度的升高,摩擦因数有所升高、磨损率有所上升且呈现不稳定性的特性。在实际应用中,摩擦导致的升温是不可避免的;如果其热衰退性大,在高温下摩阻材料的摩阻性能迅速下降,使其性能难以满足实际需要,甚至丧失使用价值。因此要求摩阻性塑料复合材料的热衰退性越小越好,减小热衰退性的具体措施如下。
(1)选用耐热优良的黏结性树脂
选用相对分子质量高(Mw>4000)、相对分子质量分布窄(多分散系数d=Mw/Mn在4~6范围内)的酚醛树脂。
选用耐热改性的酚醛树脂,如液体丁腈橡胶改性酚醛树脂、腰果油改性酚醛树脂、腰果油-三聚氰胺改性酚醛树脂、聚苯硫醚改性酚醛树脂及聚酰亚胺酚醛树脂等。
(2)选用热稳定性优良的增强剂
以石棉为增强剂的摩阻性塑料复合材料在200~250℃就发生明显热衰退,而用玻璃纤维、金属纤维为增强剂的摩阻性塑料复合材料在300℃以上才会有轻微的热衰退。用少量的碳纤维或聚芳香纤维与石棉纤维、玻璃纤维、钢纤维混合增强可明显改善其热衰退性。
(3)选用热稳定性好的摩擦性能调节剂
少选用有机摩擦粉如腰果壳油摩擦粉和废轮胎橡胶粉等,在高温下会发生脱水、相变、晶态变化等现象的无机填充剂也要少用。
4.摩擦因数的正常恢复性
摩擦因数的正常恢复性是指摩阻性塑料复合材料的摩擦因数在高温、高速、吸湿等情况下发生衰退后,在正常情况下迅速恢复到正常值的性能。不能恢复或恢复不好会使摩阻性塑料复合材料丧失其使用性能。
一般情况下,材料中含有硬度较大、粒度较大的填充组分,可提高摩擦表面的自洁性,有利于摩擦性能的正常恢复。
5.适当的硬度
要求洛氏硬度在50~100范围内。
6.足够的力学强度
摩阻性塑料复合材料应具有足够力学强度,以承受较大的压力、剪切力、冲击力的作用。由于复合材料中含有大量的填充剂和增强剂,具有较高的压缩强度,完全可满足实际需要。冲击强度要求在20kJ/m2以上,提高黏结树脂的柔性和增加纤维填充材料含量比例为提高柔性的有效方法。
7.无摩擦噪声
摩擦振动是产生摩擦噪声的重要根源。降低摩擦振动可在配方中加入软弹性、多孔性及层片状填料,具体如焦炭粉、海泡石及片状石墨等。另外,降低制品的相对密度、硬度,提高制品的刚度都可适当降低摩擦振动。
8.低热膨胀性
过度的热膨胀会造成制品加工中起泡、使用中易出现“负磨损”和“抱死”现象。要克服这类现象发生,需从以下几方面入手。
酚醛树脂中游离酚的含量要低于3%;固化剂六次甲基四胺的含量控制在7%~8%的范围内;保证制品有一定的孔隙和较低的相对密度。
9.对偶材料的低磨蚀性
摩阻性塑料复合材料对偶材料的造价都高于其本身,所以对其的磨损应尽可能低,以延长其使用寿命。避免对偶件升温过高、合理匹配两者硬度是保证对偶件低磨损的关键。
(二)塑料摩阻改性配方组成
1.黏接性树脂
黏接性树脂的作用为将增强剂和摩擦性能调解剂黏合在一起,赋予复合制品一定的强度,保证其可加工性能。
表4-87 一步法和二步法酚醛树脂基复合摩阻材料的性能

酚醛树脂及其各类改性品种至今仍是首选,处于绝对主流地位。少量应用的橡胶主要为酚醛树脂的增韧剂。
最常选用的酚醛树脂为苯酚-甲醛类,也开发出其耐热改性品种,加入量为10%~20%。
酚醛树脂可分为一步法甲阶树脂和二步法线型酚醛树脂,一步法酚醛树脂主要适用于湿法生产,而二步法酚醛树脂用于干法及半干法生产。两者制品的性能比较如表4-87所示。
在具体选用时,应选酚醛树脂牌号中相对分子质量大的品种,一般其重均相对分子质量应大于4000,超过普通酚醛树脂的5倍以上;多分散系数(重均相对分子质量与数均分子量之比)小于5,普通酚醛树脂大都大于7;游离酚含量小于3%。国内摩阻性塑料复合材料专用酚醛树脂为济南圣泉-海沃斯化工有限公司生产的牌号为PF-6076的酚醛树脂。
酚醛树脂的改性品种主要有:腰果壳油改性酚醛树脂、腰果壳油-三聚氰胺改性酚醛树脂、烷基酚改性酚醛树脂、油改性酚醛树脂、硼改性酚醛树脂、酚醛树脂/丁腈胶等,主要改善其耐热性和增韧性。
2.增强剂
增强剂的作用为提高复合材料的整体强度、模量、导热性、耐高温性及耐磨损性等。
石棉因其综合性能、价格及来源都令人满意,曾一统天下,但因对人体健康的危害性和有限的耐热性,目前正被其他纤维取代。除石棉外,可替代石棉纤维独立作为增强剂的仅有玻璃纤维和钢纤维两种。其他还有碳纤维、矿物纤维、陶瓷纤维和有机纤维等,不能单独使用,只能作为主体增强剂的改性剂,与其掺混而用。
增强剂的加入量为70%左右。
(1)石棉纤维
石棉纤维用于摩阻塑料复合材料的品种为温石棉(蛇纹石石棉),纤维较柔软,使用前用水渗透及阴离子表面活性剂如十二烷基苯磺酸钠、十二硫醇酸酯钠及烷基萘磺酸钠等。
石棉的耐热性不好,在200℃以上,石棉中的氢氧基以水的形式开始慢慢析出;400℃时析出的是沸水或吸附水,纤维强度有显著下降;在600℃以上,石棉析出结晶水,其中氢氧化镁转变为氧化镁,纤维变脆。
石棉的导热性很差,易出现摩擦性能热衰退;另外摩擦热难以迅速消除,导致热衰退层变厚,磨损加剧。
石棉会造成环境污染,特别是直径小于3μm长度为100μm以下的石棉纤维会导致人体产生癌变,属于强致癌原料。因环境等原因,石棉正在逐步被淘汰,使用新的替代材料;但因其摩擦性能十分优异,淘汰需要一个过程,目前仍有部分应用。
(2)玻璃纤维
玻璃纤维是代替石棉纤维用于摩阻性塑料复合材料最广泛的增强剂,其优点为强度高、热稳定性好、对人体的危害性低,缺点为磨损率大、易损伤对偶材料、与树脂亲和性差、价格高于石棉。
作为摩阻性塑料复合材料增强剂的玻璃纤维为中碱玻璃纤维,并以短纤维、纤维束及玻璃布形式应用;其中短玻璃纤维主要用于刹车片和干法离合器片,玻璃布主要用于湿法离合器片。为满足多种性能要求,还开发出混纺玻璃纤维如掺铜丝混纺的半铜丝玻璃纤维布、全铜丝玻璃纤维布及双铜丝玻璃纤维布等。玻璃纤维与树脂的亲和性差,需用偶联剂如KH-550及KH-560等进行表面处理等。
(3)钢纤维
用钢纤维作为摩阻性塑料复合材料的增强材料始于20世纪60年代,所制材料称为半金属摩阻材料。目前,钢纤维是仅次于玻璃纤维代替石棉纤维的增强材料。
用钢纤维作为增强材料的摩阻性塑料复合材料具有韧性好、耐磨性、导热性好、有利于消声和消振、无人体危害等优点,缺点为相对密度大、易腐蚀、硬度大及绝缘性低等。
在半金属纤维增强摩阻性塑料复合材料中,钢纤维的用量为20%~30%,其余金属成分为铁粉和铜粉等。在盘式刹车片中应选用长度为3mm的短纤维,在鼓式刹车片中应选用长度为3~7mm的长纤维。
(4)其他纤维
①聚芳酰胺(芳纶)纤维具有耐热好、高强度、高模量、抗冲击、尺寸稳定性高、低密度等优点,因此95%的芳纶纤维用于制造刹车片和离合器片。
②碳纤维在摩阻性塑料复合材料中不用之于增强材料,因其具有润滑作用而作为摩擦性能调节剂,并要控制加入量在5%以下。另外其成本高,会导致成本骤增,必须控制加入量。
③硅灰石纤维用于增强的长径比为15/1,因其性脆、强度低而不易单独用做增强材料,一般用硅灰石纤维与钢纤维、玻璃纤维、蛭石等混合使用。
④海泡石纤维可起到降低密度和噪声等作用,一般用少量海泡石纤维代替石棉纤维。也有全用海泡石纤维代替石棉纤维制成摩阻性塑料复合材料,具有综合性能良好、温度对摩擦因数不敏感、磨损率低等优点。
⑤玄武岩纤维具有类似玻璃纤维增强剂的优良性能,如较好的耐热性、绝热性、耐腐蚀性、阻燃性、价格低等,其强度与模量E与玻璃纤维相当,并随温度升高而增大,已成功用于摩阻性塑料复合材料,是一种有前途的新型增强材料。
⑥其他还有钛酸钾纤维和陶瓷纤维、纤维素纤维等。
不同类型纤维的特点见表4-88所示。
表4-88 各类纤维的特点

3.摩擦性能调节剂
摩擦性能调节剂是除黏结树脂、增强剂之外的第三组分,它们不起增强作用,因此也称为填料。摩擦性能调节剂的作用为调节摩阻性塑料复合材料的摩擦性能,如摩擦因数、磨损性的调节,特别是调节摩擦因数-温度、摩擦因数-速度、摩擦因数-压力的平稳,强度的调节,硬度调节,尺寸稳定性调节,摩擦噪声的调节,热传导性能调节,成本调节等。
摩擦性能调节剂品种繁多,以无机矿物、金属和金属化合物为主。按对摩擦因数的影响效果可分为减摩剂和增摩剂两大类。
减摩剂有:低熔点金属(如铅、锡、铋、锑、铜等)、二硫化钼等金属硫化物、金属(铜、铁、镍、钴等)磷化物、硫酸钡、石墨等。值得注意的是二硫化钼在高温下易被还原成金属钼,加速磨损。
增摩剂有:高熔点金属粉末(如铁、铬、钼等)、金属氧化物(三氧化二铁、三氧化二铝、三氧化二铬等)、金属氮化物(氮化钛、氮化锆等)、金属碳化物(碳化钛、碳化锆等)、金属硼化物、石英粉等天然矿石粉、石棉、橡胶粉及腰果壳粉等。
各类摩擦性能调解剂的性能各有所长,实际中往往选择几种配合使用。各类摩擦性能调解剂的总加入量为10%~20%。
常用的摩擦性能调节剂品种如下:
①重晶石粉:是应用最普遍的摩擦性能调节剂,用量达10%以上。其优点为与聚合物黏合力强、可使摩阻制品摩擦因数稳定、提高耐磨性、改善抗剥层性能、防止“咬死”。
②高岭土:添加量为5%~10%,其中Al2O3的含量越高,摩阻制品的摩擦因数越高。如直接加入3%的刚玉粉(人造Al2O3),其摩擦因数会更高,但却易导致对偶材料的损伤。
③长石粉:具有明显的增摩作用,广泛应用于摩阻制品中。
④硅藻土:降低制品的密度,减少摩擦噪声,保持高温下摩擦因数的稳定性,提高耐磨性。
⑤蛭石:加入量大时可作为石棉的代用品,起一定的增强作用;作为摩擦性能调节剂的作用为降低制品密度、硬度,提高热稳定效果。有报道用15%~20%蛭石和20%~25%硅灰石共同作为增强成分,制成无石棉刹车片,摩擦因数和磨损性达到国家标准,且抗热衰退性好。
⑥铸石:提高摩擦因数和热稳定性,降低制品成本,加入量为4~10份。因铸石硬度高,加入量高易刮伤对偶材料和产生摩擦噪声。
⑦锆石粉:少量加入可提高制品的摩擦因数和热稳定性。
⑧石墨:具有明显的润滑作用,可迅速降低制品的摩擦因数,一般将鳞片和粉末状石墨并用,总加入量控制在4%~10%。
⑨硫化物:包括二硫化钼、硫化亚铜、硫化钨、硫化锌、硫化锑、硫化锡、硫化铅等,都是固体润滑剂,尤其以二硫化钼最好。在摩阻材料中加入硫化物可降低摩擦因数、降低磨损性及提高耐热性等。
⑩铁粉:加入量5%~30%,除可稳定摩擦因数外,还可减少钢纤维的用量,降低生产成本。
⑪铜粉:加入量为1%~3%,起到降低摩擦因数的作用。
⑫铝粉:加入3~5份,对防止摩擦噪声有益。
⑬石油焦:可降低制品的密度、防止摩擦噪声、减少热膨胀,加入量2%~10%。具体选用低硫、低挥发、多孔海绵状煅烧石油焦。
⑭腰果壳粉:改善摩擦因数稳定性,耐磨性有所提高,防止材料的锈蚀。
(三)塑料摩阻改性配方设计
一般的塑料摩阻材料都包括树脂、增强剂和摩擦性能调解剂三大类。在具体设计配方时,应注意如下几点。
1.复合填充
除树脂外,增强剂和摩擦性能调解剂一般不单独加入,而是选用几种协同加入,既起到优势互补的作用,又可控制整体成本。
2.无石棉摩阻配方
可替代的增强剂有:选用玻璃纤维、碳纤维、云母纤维、钛酸钾纤维及玄武岩纤维等代替;选用几种纤维混合使用,如钢纤维与碳纤维、铜纤维与碳纤维、钢纤维与玻璃纤维等;选用表面镀金属的有机纤维和棉纤维;填充大量无机材料以完全取代石棉,或加入少量玻璃纤维和陶瓷粉。
3.树脂的特殊要求
对汽车用摩阻材料,因要求耐热性高,PF树脂的游离酚含量应在1.4%以下。
(四)塑料摩阻改性配方实例
1.车用鼓式刹车衬片
(1)配方1
PF树脂:15%~25%;腰果壳油摩擦粉:7%~13%;石棉:60%~80%。
(2)配方2
PF树脂:20%~30%;橡胶粉:3%~12%;石棉:50%~75%;黄铜:0~15%;腰果壳油摩擦粉:3%~12%;无机矿物粉:5%~10%。
2.车用盘式刹车衬片(%)
PF树脂:15%~22%;石墨:1%~3%;石棉:40%~60%;锌碎片:4%~8%;腰果壳油摩擦粉:15%~20%;无机矿物粉:0~10%;橡胶粉:8%~13%。
3.湿式离合器片
甲阶一步法PF树脂:17%;碳酸钙:20%;石棉:50%;硬脂酸锌:1%;丁腈胶乳:8%;铬铁矿粉:4%。
4.半金属塑料复合摩擦材料
PF树脂:10%~20%;钢纤维:0~70%;铁粉:20%~70%;石墨:10%~30%;腰果壳油摩擦粉:0~18%;硫酸钡:0~15%;橡胶粉:0~18%;无机填料:0~10%。
5.非石棉、金属纤维塑料复合摩擦材料
(1)配方Ⅰ
PF树脂:15%;石墨:4%;玻璃纤维:40%;二氧化钛(金红石):15%;橡胶粉:4%;氢氧化钙:5%;黄铜:7%;硫化铅:10%。
(2)配方Ⅱ
PF树脂:10%;黄铜:8%;玄武岩纤维:48%;硫化铅:9%;腰果壳油摩擦粉:15%;硫酸钡:10%。
(3)配方Ⅲ
PF树脂:7%;黄铜:10%;玻璃纤维:10%;石墨:20%;碳纤维:12%;硫酸钡:8%;橡胶粉:13%;无机矿物粉:20%。
6.混杂纤维摩阻材料Ⅰ
PF树脂:8%~14%;橡胶粉:0~7%;玻璃纤维:14%~16%;无机填料:7%~24%;矿物纤维:10%~14%;石墨:18%~30%;摩擦粉:0~7%;其他:34%。
7.混杂纤维摩阻材料Ⅱ
PF树脂:4%~13%;无机填料:20%;石墨:15%~40%;陶瓷粉末:2%~10%;金属粉(铁和铜):15%~40%;混杂纤维(有机纤维5%~10%、碳纤维、钢纤维、玻璃纤维):25%。
8.混杂纤维摩阻材料Ⅲ
PF树脂:8%~13%;混杂纤维:35%~40%;热裂解石墨:20%~30%;交联剂:10%~15%;橡胶:10%~15%;金属丝:3%~5%。
9.低成本增强摩阻材料
改性PF树脂:16%~19%;石墨:5%~8%;有机纤维:1%~5%;有机摩擦粉:10%~15%;膨胀蛭石片:40%~50%;无机填料:10%~18%。