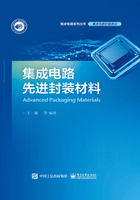
3.2 芯片黏接材料类别和材料特性
芯片的黏接方法主要有两种:黏接法和焊接法。
传统的芯片黏接材料按黏接方法不同、材料特性不同可分为有机贴片胶(导电胶、绝缘胶)、装片胶膜(导电胶膜、绝缘胶膜)、焊料和低温封接玻璃等。由于芯片黏接材料不同的特性,因此相应的芯片黏接方法各不相同,主要的芯片黏接方法及芯片黏接材料如图3-3所示。

图3-3 芯片黏接方法及芯片黏接材料
黏接法是指用高分子树脂(如环氧树脂)把芯片黏到焊盘上,使两者实现连接。因为环氧树脂属于稳定的高分子聚合物,所以大多数的树脂黏接剂采用环氧树脂作为主体材料。按物理状态不同,环氧树脂分为贴片胶和装片胶膜。
贴片胶(Die Adhesive,DA)广泛应用于塑封封装,虽然具有工艺温度低、成本低、热应力低、易返修等优点,但材料的热稳定性差,需要高温固化且工艺时间长。贴片胶分为导电胶和绝缘胶两大类。
导电胶(Conductive Adhesive)是一种具有一定导电性能的黏接剂,分为各向同性导电胶(Isotropic Conductive Adhesives,ICAs)和各向异性导电胶(An-isotropic Conductive Adhesives,ACAs)。导电胶的主要组成成分有导电填料(如Au或Ag导电粒子)和环氧树脂。导电胶除具有导电性和黏接性外,同时是热的良好导体。由于Ag具有较高的导电率、优异的物理化学性能、可接受的价格及其氧化物具有导电性能等特点,因此Ag被广泛用作导电填料。
绝缘胶(Non-conductive Adhesive,NCA)广泛用于集成电路封装中需要绝缘黏接、灌封的地方,如应用于芯片背面不需要导电的芯片黏接情况等。
装片胶膜(Die Attach Films,DAF)是一种超薄型薄膜黏接材料,其主要成分也是树脂,但与导电胶不同,其以胶膜的形式应用于芯片粘贴,可吸收热胀冷缩引起的应力而有效防止不同物质交界面的分层现象。装片胶膜可把集成电路芯片与封装基板、芯片与芯片连接在一起。装片胶膜可通过热焊接的方式封装倒装芯片,这让无法用底部填充料(Underfill)进行封装的问题得到了解决。装片胶膜按导电与否可分为导电胶膜和绝缘胶膜两类。
焊接法是指通过加热熔化焊料(Solder),利用液态焊料润湿母材,填充接头空隙并与母材相互扩散,从而实现芯片的黏接。焊料是集成电路封装技术中常见的一种黏接材料,一直在各级集成电路封装中被广泛使用。随着先进封装的发展,焊料应用其中。在倒装芯片结构中,裸芯片和衬底可以直接通过焊点在进行机械连接的同时实现电互连,省去了传统组装工艺过程中的贴片、打线过程,减小了封装体积并降低了成本。
低温玻璃(Low-Melting Sealing Glass)是指软化温度低于600℃的玻璃。低温玻璃作为芯片黏接和封接材料,可实现半导体、金属、陶瓷、玻璃间的相互封接,应用范围很大。
3.2.1 导电胶
导电胶是通过在高分子树脂基体中添加金属导电填料形成的。导电填料主要提供电学及热学特性,树脂基体则提供机械特性和密封性。通过调整金属导电填料和树脂的配比,导电胶可体现出截然不同的电学和机械性能,因此导电胶与金属焊料有明显的区别。导电胶如图3-4所示。
此外,区别于本征导电高分子,导电胶在一定的储存条件下具有流动性,经过印刷/点胶工艺后,需要进行加热或其他工艺,使导电胶固化方可起到一定强度的连接作用。

图3-4 导电胶
导电胶一般以高分子树脂及导电填料为主体,添加固化剂、增塑剂、稀释剂及其他助剂组成,其常用材料及功能如表3-1所示。
导电胶的导电机理主要有四种:渗流理论(导电通路学说)、隧道效应、有效介质理论和场致发射理论,其中渗流理论是目前研究最成熟、最多的导电机理。渗流理论认为,导电胶通过导电粒子在树脂基体中形成导电通路进行导电;导电胶的电导率并不随着导电粒子的浓度增加发生线性变化,而存在一个渗流阈值,阈值大小取决于导电粒子和树脂基体的类型,以及导电粒子在树脂基体中的分散状态。
表3-1 导电胶的常用材料及功能

导电胶种类繁多,用途广泛,其分类方法有很多。
导电胶根据结构的不同分为本征型导电胶(结构型导电胶)和复合型导电胶(填充型导电胶)。本征型导电胶指的是分子结构本身具有导电功能的导电胶,这种类型的导电胶电阻率较高,而且导电稳定性及重复性较差,成本也较高,因此实际使用价值有限。复合型导电胶以高分子聚合物为基体,在其中加入各种导电物质,经过物理或化学方法复合后得到。其中所用的聚合物基体一般为环氧树脂、硅酮或聚酰亚胺等,加入的导电物质包括银、镍、铜、金等金属及炭黑、石墨等非金属。
从导电方向性上划分,导电胶可以分为各向同性导电胶(ICAs)和各向异性导电胶(ACAs)两类。ICAs在各个方向有相同的导电性能,多以Ag、Au、Ni、Cu和石墨为导电粒子,典型填料尺寸为1~10μm;ACAs可在单一方向进行导电,即线性导电,多以Au、Ni、Cu和金属镀覆粒子为导电粒子,典型填料尺寸为3~5μm。两者的区别来源于渗流理论的导电机理,导电填料体积占比不同及分散状态不同造成了两者的差异,ICAs 中的导电填料含量高于ACAs。导电胶连接示意图如图3-5所示。

图3-5 导电胶连接示意图
另外,根据基体(载体)材料的不同,导电胶可分为热固型导电胶和热塑型导电胶两类。根据不同的固化条件,导电胶分为热固化型导电胶(室温、中温、高温)、光固化型导电胶(紫外光固化)和电子束固化型导电胶。根据导电粒子的不同,导电胶分为金属导电胶(Ag系、Cu系、Ni系等)及非金属导电胶(碳系)等。
导电胶已广泛地应用在各种导电互连场合,尤其是在对布线的线分辨力和I/O密度有较高要求的高密度封装领域,导电胶比焊料具有更高的工艺精度。作为新一代绿色环保型电子封装材料,导电胶作为焊料的补充替代品有着广阔的前景。
导电胶除能满足导电和黏接这两项基本要求外,相比焊料还具有许多优点,如能在较低温度甚至室温下固化,避免了焊接高温对元器件的损害,可以用于对环境温度要求低的材料的组装及柔性基板贴装;导电胶的传递应力比较均匀,可避免在黏接部位出现应力集中而造成的机械破坏。
由于焊料与导电胶具有明显不同的表面特性,因此在一些应用场合下导电胶仍然无法取代焊料。相比于常规焊料,导电胶中的导电填料的含量与电阻率关联。在某个填料含量以下,导电胶因电阻过大而无法使用;然而过多增加导电填料的含量,会导致导电胶中树脂的含量相对减少,从而引起导电胶的抗冲击强度和黏接强度下降。导电胶在封装领域的进一步应用,还需要在导电、导热及力学性能和连接可靠性方面进行提升。
3.2.2 导电胶膜
为满足消费类电子产品更小、更薄和低成本封装的要求,未来的发展趋势将是逐步取消金属型的芯片载体,转而采用封装密度更高的表面布置有电路的聚合物基板。这类聚合物基板需要降低黏接温度,降低应力并避免对表面电路的污染。因此,装片胶膜技术应运而生。
在这一过程中,随着先进球栅阵列封装/芯片级封装(Chip-Scale Package,CSP)封装尺寸的增加,产生了很多新的技术问题。其中包括由基板、焊球和印制电路板组成的封装体结构的材料热膨胀系数不匹配,基板产生翘曲,并且封装体内外连接性变差等。在这一方面,装片胶膜材料担当了降低封装应力的角色。目前产业界和研究人员尤其关注低温和低弹性模量装片胶膜材料的研究开发,以满足先进封装技术的要求。
导电胶膜是热固型导电胶的一种,由导电粒子、树脂基体和添加剂组成,是一种具有导电性、黏接性的高分子聚合物薄膜,如图3-6所示。与导电胶相似,异电胶膜按照导电方向可以分为各向同性导电胶膜(Isotropic Conductive Films,ICFs)和各向异性导电胶膜(An-isotropic Conductive Films,ACFs)。

图3-6 导电胶膜实物图(Henkel)
导电胶膜的主要性能指标是电学性能,尤其是电阻率。此外,导电胶膜的厚度及其均匀性也是重要的指标,因为导电胶膜的厚度决定了芯片—焊盘间距,紧凑的间距有助于封装器件中集成更多的芯片,符合集成电路产品小型化、薄型化发展要求。
目前,在集成电路组装领域的许多方面,导电胶膜正在逐渐代替传统的焊料和传统胶黏剂。导电胶膜主要具有如下优点:消除了侧边爬胶,减小了芯片和芯片焊盘之间的间距,提高了芯片设计密度,配套封装材料(如金丝、基板和塑封料)的用量显著减少,降低了生产成本;不需要高温互连,应力小,具有较高的柔性和抗疲劳性,可与多种基板连接;工艺简单,生产效率高;不含铅等有毒金属成分,减少了对环境的污染。
虽然导电胶膜有较多的优点,但其自身存在一些在应用上需要解决的问题。目前对导电胶膜的研究方向主要集中在对其基本性能(如黏接强度、电学性能、热学性能等)和特殊性能(如低吸湿性、低应力)的提高方面,研究内容包括导电粒子、基体树脂的组成、结构及固化工艺等的优化。
因为导电胶膜的主体构成成分是树脂,其电导率和热导率一般都较低,所以在应用中必然存在电阻、热阻都较高的问题,尤其是对功率器件而言,在工作中由于热阻较高,散热效果不好,器件容易过热烧毁。国内外的研究人员一般通过以下几种途径来提高导电胶膜整体的电导率和热导率,主要包括在固化胶体时使导电粒子之间紧密接触,在导电胶膜中形成更多的导电和导热通路;增加导电胶膜中金属粒子的填充量及采用纳米级的填充粒子达到低温烧结效果等。
导电胶膜的黏接效果会受到元器件、基板类型与结构等的影响,尤其是在间距较小的元器件互连结构中,如果黏接强度低,那么元器件的抗冲击能力会降低。一般会在树脂体系中加入偶联剂等以增加导电胶膜与元器件、基板等的结合力,或者提高导电胶膜与元器件接触表面的粗糙度以增大表面接触面积等来进行改善。
3.2.3 焊料
焊料是集成电路封装技术中的一种常用的互连材料,起到机械连接、电互连、热交换等作用,具有灵活、简单、设备投资少等优点。焊料的熔点(液相线温度)是一个重要参数,要求比被焊母材低。在焊接过程中,焊料的工作温度在焊料熔点与基板熔点之间,焊料熔化后浸润基板,并与芯片载体(基板)发生化学反应产生金属间化合物,从而实现两者的稳定互连。不同类型焊料实物图如图3-7所示。

图3-7 不同类型焊料实物图
焊料一般需要满足以下几项基本要求。
(1)熔点低于基板熔点,具有合适的熔化温度范围。
(2)具有较好的浸润性,覆盖母材表面的能力较好,铺展面积越大,焊接效果越好。
(3)焊接部位具有良好的抗热疲劳性能、电学性能、机械性能和物理、化学性能。
(4)化学成分稳定,可靠性高,有良好的抗氧化及抗腐蚀能力。
(5)成本低廉,供给能力足。
锡铅(Sn-Pb)焊料以其优良的焊接性能和低成本优势,早期广泛地应用在电子封装行业中。Pb作为主要成分,起到了降低焊料的表面张力,以及抑制Sn的相变从而提高焊点的可靠性的作用。图3-8所示为Sn-Pb二元合金相图,Sn-Pb二元合金的共晶点为183℃。常用的Sn-Pb焊料即Sn-37Pb共晶焊料(37表示Pb的质量百分比为37%)。目前,一些对可靠性要求高的军用、测井、航空航天等领域的电子产品仍优先选用Sn-Pb合金作为焊接材料。

图3-8 Sn-Pb二元合金相图
然而,由于铅会对人体和环境带来较大的破坏和污染,随着人们环保意识的提高,自2006年欧盟ROHS(电气电子产品中危害物质禁限用指令)和WEEE(废弃电气电子产品指令)的发布开始,欧洲、美国、日本等相继规定在电子组装行业中禁止使用含铅物质,我国也开始推行无铅化相关的条例或规定。Sn-Pb合金逐步被禁止用于集成电路封装行业,绿色环保的无铅焊料成为工业界和学术界应用及研究的热点。
目前研发及使用的无铅焊料通常以Sn为基础,多为二元、三元及以上的多元合金,其加工过程较Sn-Pb焊料复杂,而且熔点普遍较高。二元合金添加金属多为Ag、Cu、Bi、Zn、In等元素,三元及以上合金通过添加微量元素调整合金的熔点、力学性能和工艺性能等。目前,具有代表性的无铅焊料合金有Sn-Cu、Sn-Ag、Sn-Au、Sn-Zn、Sn-Bi、Sn-In等二元合金,以及Sn-Ag-Cu、Sn-Ag-Bi等三元合金。其中Sn-Ag-Cu三元合金焊料(简称SAC焊料)以其可焊性能好、抗热疲劳性能好等优点成为最有可能代替Sn-Pb合金的焊料,已大量应用到工业中。表3-2展示了一些可能取代Sn-Pb焊料的无铅焊料。
表3-2 一些可能取代Sn-Pb焊料的无铅焊料

合金粉末可用化学还原法、电(解)沉积法、机械加工法、合金雾化法等技术方法制造。目前无铅焊料粉末大多是用合金雾化法生产得到的。随着窄节距组装的发展,焊粉粒度需要达到20μm以下甚至更低。
焊料作为一种重要的集成电路封装连接材料,国外的主要供应商有日本千住金属工业株式会社、美国爱法公司和铟泰公司(Indium Corporation)等,千住金属工业株氏会社提供各种有铅及无铅金属焊片、焊膏、焊球及助焊剂;爱法公司提供各种有铅及无铅焊条、焊线、焊膏及助焊剂;铟泰公司提供各种焊接材料,包括高铅合金、锡锑合金、锌基合金、金基合金、铋基合金、银铟、银锡和铜锡及纳米银和纳米铜等助焊剂。国内的主要供应商有北京康普锡威科技有限公司、廊坊邦壮电子材料有限公司等。
3.2.4 低温封接玻璃
低温封接玻璃是指能将同类及不同类材料(如陶瓷、金属、复合材料和特种玻璃等)连接并密封的中间层玻璃,其软化温度显著低于普通玻璃,一般低于600℃。作为功能配套材料,低温封接玻璃有三方面的功能应用,分别是涂层、封装材料和填充材料。其中,封装材料方面的应用最为广泛,如真空玻璃的封边焊接剂,以及在MEMS中的最新应用等。低温封接玻璃粉如图3-9所示。

图3-9 低温封接玻璃粉
低温封接玻璃作为一种无机非金属材料,其气密性和抗高温性能优于导电胶/膜这类有机高分子材料,电绝缘性能优于焊料这类金属材料,因此在特定的封装领域内有很好的应用价值。国内应用广泛的铅系封接玻璃的组成与其对应的玻璃化温度(Tg)和软化温度(Tf)如表3-3所示。
表3-3 铅系封接玻璃的组成与温度特性

低温封接玻璃一般需要满足以下几项基本要求。
(1)软化温度要低,必须低于被封接材料所能承受的温度。
(2)与被封接材料的热膨胀系数匹配,这样封接后产生的热应力小,可避免应力集中引起元器件出现可靠性问题。
(3)与被封接材料的浸润性要好,良好的浸润性能保证封接的黏接强度,满足元器件气密性的要求。
(4)具备必要的化学稳定性,在大气环境中有较好的耐酸碱、耐湿性能。
(5)具备必要的电学性能,如较高的表面电阻、体积电阻,较高的耐击穿电压。
(6)工艺适应性。
与焊料的无铅化进程类似,考虑到铅对人体和环境的破坏及污染,低温封接玻璃的无铅化是今后的主要发展方向,新型低温封接玻璃的研究主要集中在磷酸盐、钒酸盐、铋酸盐、硼酸盐和铊酸盐玻璃等几种玻璃系统。
磷酸盐玻璃是以P2O5为主要原料形成的玻璃体系,具有较低的玻璃化温度(Tg=250~480℃)、较低的软化温度(Tf=270~510℃)及较高且范围较大的热膨胀系数(α=6×10-6~25×10-6/℃),是近年来研究比较多的无铅封接玻璃体系之一。但该体系成分中的P2O5极易吸水潮解,导致磷酸盐玻璃的化学稳定性较差,因此提高其化学稳定性是该玻璃体系成功使用的前提。
钒酸盐玻璃是以V2O5为主要原料形成的玻璃体系,同样具有较低的玻璃化温度(Tg=260~420℃)和软化温度(Tf=270~440℃),V2O5-B2O3-ZnO是其中较常见的体系,介电性能良好。钒酸盐玻璃的缺点是V2O5在蒸气状态下有毒,且价格相对较高,这些缺点限制了它的实际应用。
无铅磷酸盐玻璃和无铅钒酸盐玻璃的温度特性如表3-4、表3-5所示。
表3-4 无铅磷酸盐玻璃的温度特性

表3-5 无铅钒酸盐玻璃的温度特性
