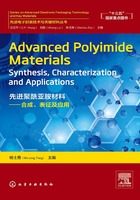
1.2 Chemistry of Polyimide Films
Because of the extended rigid planar aromatic and heteroaromatic structures, aromatic polyimides are usually infusible and insoluble. Hence, polyimide films are generally prepared by casting of polyimide precursor-PAA resin solution on the support surface to give self-standing gelled films, which are then imidized by thermally baking at <180 °C, as shown in Fig. 1.2. This process made it possible to bring the first significant commercial polyimide film product (Kapton H) to market, and it is still the method of choice in the majority of polyimide film production.
When an aromatic diamine and an aromatic dianhydride are mixed in dipolar aprotic solvent such as DMAc, DMF, or NMP, PAA resin is rapidly formed at ambient temperatures. The reaction mechanism involves the nucleophilic attack of the amino group on the carbonyl of the anhydride group, followed by the opening of the anhydride ring to form amic acid group, as shown in Fig. 1.3. This process is an equilibrium reaction and is irreversible because a high-molecular-weight PAA resin is readily produced. The reaction is much faster than the reverse reaction by several orders of magnitude. If there is not a large difference in reaction rate, the high-molecular-weight PAA is not produced. Hence, it is a key issue to examine the driving forces that favor the forward reaction over the reverse reaction. In addition, the acylation reaction of amines is an exothermic reaction and its equilibrium is favored at low temperatures. The forward reaction in dipolar solvents is a second-order reaction and the reverse reaction is first-order. The equilibrium is favored at high monomer concentrations to form higher-molecular-weight PAA resins.
The conversion of PAA to polyimide can be completed either by thermal imidization or by chemical imidization methods, which will be discussed in the following sections.
1.2.1 Thermal Imidization
The most commonly used pathway for conversion of cast PAA gelled films to the corresponding polyimide films is the thermal imidization. This method is suitable for production of continuous polyimide films thermally cured at elevated temperatures to allow the diffusion of by-product (water) and organic solvents without forming bristles and voids in the final polyimide films. In this method, the cast PAA film on the surface of a circular seamless steel support tape is dried and heated gradually to about 180 °C, and then cooled and peeled off to give a self-standing gelled film which is mono- or biaxially stretched and imidized by gradually heating from about 200 °C to 350 °C to give the fully polyimide films. It was noted that too rapid heating might cause the formation of bubbles and voids in the final polyimide film products. After the PAA solution in solvents such as DMAc or DMF is cast on the support surface and dried at low temperature (<180 °C) to a nontacky state, the resulted gelled film still contains a substantial amount of the solvent, typically up to 25% (w) depending on the drying conditions. In the subsequent heating, imidization reaction takes place not in a true solid state but rather in a very concentrated viscous solution, at least during the initial and intermediate stages of thermal imidization.
The residual solvent remaining in the gelled films plays an important role in the production of polyimide films. The thermal imidization proceeds faster in the presence of dipolar amide solvents such as DMAc or DMF, in which a specific solvation existed, allowing the favorable conformation of the amic acid group to cyclize [8]. The amide solvent also has a plasticizing effect, resulting in the increases in mobility of the reactive acidic groups due to its basicity and acceptability of protons. Because the protons of the carboxylic group are strongly hydrogen-bonded to the carbonyl group of the amide solvent, the cyclization of the o-carboxyamide group results in dihydrogen bonding and release of the solvent molecule along with water of condensation.
It should be mentioned that the thermal imidization process of PAA to polyimide is very complicated, and it is very difficult to describe with a simple kinetic expression. There are several interrelated elementary reactions and dynamically changing physical properties such as diffusion rate, chain mobility, solvation, and acidity, etc. The thermal imidization proceeds rapidly at the initial stage and tapers off to a plateau, which is a typical diffusion-limited kinetic process. With the imidization degree (ID) increaseing, the Tg or stiffness of the polyimide backbone chain increases. When the Tg approaches the reaction temperature, the imidization rate slows down rapidly. At a higher temperature, a higher ID is achieved.
At the initial stage, the imidization proceeded rapidly due to the five-member ring closure of amic acid in the favorable conformation (1), then the imidization rate slowed in the later stage due to the unfavorable conformation (2) (Fig. 1.3), in which there was a rearrangement of conformation (2) to conformation (1) before ring closure. Such a conformational rearrangement requires rotational motion of the adjoining polymer chain and strongly bound solvent molecules. The effect of the conformation of amic acid on the imidization rate is also consistent with the observation [8] that the thermal cyclization of model compounds N-substituted phthamamic acids was strongly influenced by the steric effect imposed by N-substituents. The vacuum thermolysis of neat N-substituted phthamamic acids afforded the corresponding imides and anhydrides. It was concluded that conformation required for imide formation is apparently influenced by the steric effect of the N-substituents.

FIGURE 1.3 Reaction mechanism of polyimide formation.
The polycondensation of dianhydrides with diamines to produce poly(amic acid) is an exothermic reaction. On heating, the equilibrium shifts toward the left (Fig. 1.4). The reversion should result in a higher level of anhydride and amino groups, and a lower molecular weight. There are several factors that play important roles in the synthesis of PAA resins, such as the reactivity of monomers, solvents, moisture, monomer adding mode and molecular-weight distribution, etc.

FIGURE 1.4 Mechanism of thermal ring closure of amic acid to imide.
1.2.1.1 Reactivity of Monomers
The mechanism of polycondensation between dianhydride and diamine in amide solvent to form PAA resin is a nucleophilic substitution reaction at one of the carbonyl carbon atoms of dianhydride with diamine. Hence, the reaction rate is primarily governed by the electrophilicity of the carbonyl groups of the dianhydride and the nucleophilicity of the amino nitrogen atom of the diamine. The phthalic anhydride group is a strong electron acceptor and a relatively strong Lewis acid, in which the two carbonyl (CO) groups are situated at the ortho-position to each other, and their strong electron-withdrawing effects activate each other towards nucleophilic reaction. The effect is particularly enhanced by the preferred carbonyl conformation locked in the coplanar aromatic ring (Fig. 1.5).

FIGURE 1.5 Resonance effect on phthalic anhydride group
PMDA is the most reactive dianhydride monomer, because the four carbonyl (CO) groups attached to one benzene ring in a coplanar conformation, showing the strongest tendency to accept an electron. The electrophilicity of carbonyl carbons of each dianhydride can be measured in terms of the electron affinity, a tendency of the molecule to accept an electron. Table 1.1 compares the electron affinity (Ea) for various aromatic dianhydrides by polarographic measurement. PMDA exhibits Ea of 1.90, higher than DSDA (1.57) and BTDA (1.55). BPDA and ODPA show Ea of 1.38 and 1.30, respectively. The ether-bridged dianhydride ( BPADA, and EDA) possess Ea in the low level of 1.10-1.19.
TABLE1.1 Electron Affinity(Ea)of Aromatic Dianhydrides

Due to the strong electron-accepting property of dianhydrides and high electron density of amino groups of diamines, charge transfer interactions and electrostatic interactions between dianhydrides and diamines have obvious effects on PAA formation. The acylation of a diamine with a dianhydride is preceded by a charge transfer interaction in which diamine is a donor and dianhydride is an acceptor. The reaction mixture shows a strong color of charge transfer complex at the beginning, and the color gradually fades as the acylation proceeds. For the ether-bridged bisphthalic anhydrides, the ether-bridge group strongly reduces Ea of the dianhydride. Compared with BPDA, which lacks a bridge group, the electron-withdrawing bridge groups such as SO2 and C O increase the Ea values substantially. On the other hand, the electron-donating bridge groups such as — O significantly reduce Ea values. The dianhydrides with low Ea are not affected by the atmospheric moisture [9] while PMDA and BTDA must be handled under strictly moisture-free conditions at all times.
Unlike the Ea value of dianhydride, the ability of diamine to give off an electron, the ionization potential (I), does not seem to correlate well in a simple manner. The reactivity of diamines instead correlates well with its basicity (pKa) in a Hammett’s relation. The reaction rates (k) of various diamines toward PMDA are in relation to their pKa (Table 1.2). The chemical structures of aromatic diamines have significant effects on the rate of acylation reaction, moreso than those of aromatic dianhydride. The rate constants differ by four orders of magnitude between aromatic amines with electron-donating substituents and those with electron-withdrawing ones.
TABLE1.2 Basicity(pKa) of Aromatic Diamines and Their Reactivity Toward PMDA

1.2.1.2 Effect of Solvents
The most commonly used solvents are dipolar aprotic amide solvents such as DMF, DMAc, NMP. One of the important properties of the solvent selected is its basicity (Lewis base). The starting materials are weakly basic aromatic diamine monomers and dianhydrides, and the reaction product PAA is a strong aprotic acid. The ortho-amic acid is a relatively strong carboxylic acid because of the electron-withdrawing effect of the ortho-amide group and the stabilization by internal hydrogen bonding of dissociated carboxylate with amide hydrogen. Hence, the strong acid-base interaction between the amic acid and the amide solvent is a major source of exo-thermicity of the reaction, and one of the most important driving forces. The rate of PAA formation is usually faster in more basic and more polar solvents.
If solvent contains an amount of water as impurity, some anhydride groups are hydrolyzed to ortho-dicarboxylic groups which are unreactive end groups. As a result, the equivalent amount of amino groups will also be left in an unreactive state if the stoichiometric amounts of dianhydride and diamine monomers are used in the beginning. If an additional dianhydride equivalent to the unreacted amino group is added to the above solution, it reacts with the amino end groups, resulting in the increase in molecular weight of PAA. Although the ortho-dicarboxylic acid group is inactive at ambient temperature, it will thermally dehydrate to the anhydride and reacts with amine at high temperatures, thus giving an off-stoichiometric situation with the dianhydride in excess. Hence, the molecular weight of the polyimide product is primarily governed by the stoichiometric relation of the monomers.
1.2.1.3 Effect of Moisture
PAAs are known to undergo hydrolytic degradation even at ambient temperature. This is attributed to the presence of a small amount of anhydride groups existing in an equilibrium concentration, which plays an important role in the hydrolytic degradation of PAA. The anhydride group in PAA solution can be hydrolyzed to form ortho-dicarboxylic group in the presence of water. The reaction is driven by the enhanced nucleophilicity of water in a dipolar aprotic solvent and by strong acid-base interaction of the product with the dipolar solvent. The ortho-dicarboxylic groups are stable as one of the end groups of PAA and do not revert to the anhydride. After the anhydride groups are completely consumed, more anhydride groups are produced to reestablish the reaction equilibrium. It was found that water has a significant effect on the molecular weight of PAAs during polymerization [10]. The common source of water is in the solvents and the monomers as an impurity, and water can also be produced by the imidization of amic acid groups. Although the rate of the imidization and the formation of water is relatively slow at ambient temperatures, it is still significant enough to cause a gradual decrease in molecular weight over a long period of time. Hence, if long-term storage is necessary, PAA resin solution should be kept refrigerated.
1.2.1.4 Monomer Adding Mode
Dianhydride and dianmine monomer adding mode is an important factor for the preparation of PAA. If 25% (mol) of additional dianhydride (PMDA) or diamine (ODA) is added to the high molecular weight PAA solution, obvious decreases in the solution viscosity at 35 °C are measured, demonstrating that the addition of additional monomer could cause reequilibrium of the main equilibrium reaction. Addition of 25% (mol) PMDA resulted in a rapid initial decrease in its viscosity, but within 30 h the rate of the decrease tapered off at a higher level, and at 1000 h the viscosity was only slightly lower than that of the original sample after the equivalent aging period.
When a diamine-excess solution was compensated with the equivalent amount of additional dianhydride (PMDA), the viscosity of PAA solution was rapidly recovered to its original level. On the other hand, addition of diamine (ODA) to the dianhydride-excess solution resulted in a rapid decrease in viscosity to a much lower level. The diamine-excess condition can be corrected to restore the ultimate molecular weight, and the dianhydride-excess condition results in a permanent decrease in the molecular weight of PAA. Hence, the reactive dianhydride (PMDA) as a strong dehydrating agent is not stable in the presence of amic acid groups in solution, which can dehydrate the amic acid to the imide by hydrolyzing itself to the ortho-dicarboxylic acid; and the ortho-dicarboxylic acid group is unreactive in the presence of PAA, acting as a chain end group to control the molecular weight of the resulting polymers. Hence, the preferred mode of monomer addition during PAA preparation is to add the dianhydride to the diamine solution. In this manner, the reacting solution does not contain an excess of dianhydride at any time.
1.2.1.5 Effect of Molecular Weight Distribution
Although PAA solution should be kept at low temperature to maintain its viscosity without apparently change for further film processing, the long-term storage always results in its viscosity decreasing to some extent. The more rapid and significant decrease in viscosity occurs in the initial aging period. This cannot be explained by the effect of water or other inadvertently introduced contaminants such as impurities in the monomers (Fig. 1.6).

FIGURE 1.6 Effect of excess anhydride on PAA formation.
The change in the molecular weight distribution of the initially produced poly(amic acid) was found to be the major cause [11]. When the insoluble dianhydride such as PMDA is added to the diamine (ODA) solution in the form of solid or slurry, the polycondensation reaction proceeds in a heterogeneous manner, giving a condition of interfacial polymerization between solid dianhydride and the solution of diamine. Because the reaction rate of PMDA and ODA is very fast and viscosity of PAA is very high, the interfacial polymerization is governed by the diffusion rates of two monomers approaching from the opposite sides of the interface. At the interface where the exact stoichiometry is satisfied, a high-molecular-weight PAA was obtained. After the polycondensation reaction is completed, the polymer solution contains some unusually high-molecular-weight fractions, which contribute more heavily to the weight average molecular weight (Mw) than to the number average molecular weight (Mn). During the polycondensation, the Mw is initially high and then decreases markedly in the initial rapid drop of the solution viscosity. However, Mn remains essentially constant at the same period. Hence, the polydispersity (Mw/Mn) is initially high and then decreases toward a value of 2, which is the most probable molecular weight distribution. For most polyimides, the viscosity average molecular weight is much closer to Mw than to Mn [12]. Hence, the solution viscosity decreases with Mw decreasing while Mn remains relatively unchanged.
1.2.2 Chemical Imidization
The cyclodehydration of PAAs to polyimides can be readily achieved using chemical dehydration at ambient temperature. The commonly used reagents are the mixtures of acid anhydrides and tertiary amines in dipolar aprotic solvents [2,13-16]. The dehydration agents include acetic anhydride, propionic anhydride, n-butyric anhydride, benzoic anhydride, etc, and the amine catalysts are pyridine, methylpyridines, lutidine, trialkylamines, etc.
High-molecular-weight polyimides can be obtained using trialkylamines with high pKa (>10.65) as catalyst. However, low basic tertiary amines usually result in lower-molecular-weight polyimides. The highest-molecular-weight polyimides can be obtained using heteroaromatic amines such as pyridine, 2-methylpyridine, and isoquinoline (5.23 < pKa < 5.68) as catalysts. The chemical imidization reaction seems simple, but the mechanism is quite complex. The polycondensation products are very different depending on the type of dehydrating agents, monomer components, reaction temperature, and other factors.
The use of N, N-dicyclohexylcarbodiimide (DCC) produces essentially quantitative conversion of amic acids to isoimides instead of imides [17]. The combination of trifleoroacetic anhydride- triethylamine and ethylchloroformate-triethylamine also afforded high yields of isoimides [17]. It was revealed that isoimides and imides are formed via a mixed-anhydride intermediate, which is formed by acylation of the carboxylic group of amic acid (Fig. 1.7).

FIGURE 1.7 Mechanism of chemical imidization of amic acid to imide R:ethyl;Ar:phenyl.
The imidization process involves the simultaneous PAA imidization, solvent diffusion, and the development of ordering aggregation. There was complexation between solvent NMP and PAA. The imidization kinetics were investigated by isolation of the processes of decomplexation between NMP and PAA and imidization. The solvent content in the partially imidized film is crucial in determining the ordering degree and texture of the film. The ordering degree can be improved at higher heating rate and thicker film in the imidization. Different morphology in polyimide films can be obtained using thermal or chemical imidization [18]. The surface of the polyimide films by thermal imidization showed microdomains of an almost spherical shape, and their size and packing was dependent on the heating temperature, while it exhibited net structure by chemical imidization. The chemical structures of PAA resins can influence the combined properties of the final polyimide films; the control of ID of PAA resins in solution is especially important. After the mixture of acetic anhydride and pyridine were added into PAA solution, the imidization occurred immediately to yield a copolymer, i.e., poly(amic acid-imide) (PAAI), whose solubility is directly relative to ID. There is a critical point for ID, below which PAAI solution is homogenous and above which phase separation will occur immediately. Hence, homogeneous copolymer PAAI solutions with different IDs can be obtained before the critical point of phase separation in the imidization process; and the control of ID can provide a pathway to prepare polyimide films with the required morphology and properties.
In the imidization process, the solution viscosity was temporarily increased at the initial reaction stage due to the interchain mixed-anhydride formation, which was then gradually decreased back to the normal level with the cyclization reaction. Polyimide was formed by intramolecular nucleophilic substitution at the anhydride carbonyl by the amide nitrogen atom (Figs. 1.7, 1.8 and 1.9), while isoimides were formed as a result of substitution by the amide oxygen (Figs. 1.8 and 1.9).

FIGURE 1.8 Mechanism of rearrangement of isoimide to imide.

FIGURE 1.9 Effect of temperature on the solution viscosities of PAA-(PMDA/ODA) with different reaction times.
The cyclization of a model compound, N-phenylphthalamic acids, with acetic anhydride proceeds smoothly at room temperature in DMAc in the presence of a tertiary amine, in which the amine acts as a catalyst as well as an acid acceptor. The stoichiometric amount of amines in the PAA solution could still lead to the completion of imidization reaction, but only at a lower rate. Strong base, such as trimethylamine (pKa 10.6), as a catalyst produced exclusively normal imides, however, a mixture of imide and isoimide was formed if lower basic pyridine (pKa 5.2) was employed as a catalyst. The rate of formation of isoimide was faster than that of imide in the initial stage and the formation of imide overtook at the later stage. Hence, the isoimide should not be considered as the intermediate to the polyimide. After completion of the cyclization, the isoimide slowly rearranged to imide. The rearrangement reaction was found to be efficiently catalyzed by acetate ion [17], as shown in Fig. 1.8.
In the presence of stronger amines such as trimethylamine, a high concentration of acetate ions is formed, resulting in the concurrent transformation of the isoimide to the imide during the cyclization. In contrast, trifluoroacetic anhydride or N,N-dicyclohexylcarbodiimide as dehydrating agent affords exclusively isoimides for both model compounds and PAAs. In general, isoimides exhibit intense, bright-yellow, or yellowish-orange color derived from a strong absorption at around 350nm-400 nm in the UV-visible spectrum.
Polyimide films with different levels of anisotropy can be obtained by varying the level of imidization with catalysts prior to drying or by relieving the in-plane stress by unconstraining the films during cure. Bi-axially stretched polyimide films by thermal imidization method exhibit a higher degree of molecular orientation than films cured in an unconstrained state [19,20]. Since the degree of molecular orientation is the result of restricting the in-plane shrinkage of the polyimide film produced during the process of thermal curing, this technique can be used to prepare films with varying degrees of molecular orientation. Chemical imidization can also be used to prepare polyimide films with varying degrees of molecular orientation. The birefringence in PMDA-ODA films prepared by chemical imidization was about a factor of 3 higher than the that of films prepared by thermal imidization.
The varied degree of molecular orientations in PMDA-ODA films have been prepared both by varying the constraint on the films during the thermal curing and by varying the level of chemical imidization prior to cure. Polyimide films with a high degree of molecular orientation can be prepared by partially chemically imidizing PAA film prior to cure. Excess molar amounts of acetic anhydride and β-picoline were added to the PAA-(PMDA/ODA) solution in DMAc. The PAA solution was cast onto glass plates, followed by heating to 100 °C/30 min, then to 250 °C/30 min to give partly imidized films. The lifted film was fixed in a frame, and was then heated to 400 °C for 5 min to remove the last traces of solvent and complete the imidization.
It was found that the PAA films exhibit a large optical anisotropy, indicating preferential alignment of the long axis of the molecule in the plane of the film. Imidization increased the birefringence of the film by a factor of 2.5 and reduced the film thickness. The only parameter that affected the anisotropy of the films was the method of imidization. Chemical imidization was found to increase the birefringence by a factor of 3, indicating of a higher degree of molecular orientation parallel to the film surface. This effect was not observed in thicker (>25 μm) films using X-ray diffraction where the orientation function was independent of the method of imidization.
The chemical imidization pathways of polyimide (MPDA-ODA) and (BPDA-PDA) films were systematically investigated [21]. PAA resin solution was first mixed with dehydrating agents (the mixture of acetic anhydride and tertiary amine as the catalyst), and was then cast on the support surface to give a partly imidized PAA gel film. The gel film was then thermally converted to fully imidized polyimide films at high temperatures. The gel point was dependent on ID despite the temperature and the molar ratio of catalyst to acetic acid. Experimental results indicated that the ID was about 35% for PMDA/ODA and about 22% for BPDA/PPD. The effect of catalyst on imidization was in the order trimethylamine > 3-methylpyridine > pyridine > isoquinoline > 2-methylpyridine. The stretching of the films greatly reduced the coefficient of linear thermal expansion (CTE) either in the longitudinal or transversal direction. Compared to the film from PAA, the partly imidized film had greater stretching ratio, so that the unaxially stretched polyimide film from partly imidized PAA had higher tensile strength and tensile modulus, but lower elongation in the stretching direction.
1.2.2.1 Effect of Temperature on Viscosity and Gelation Time
The ID was calculated as the gelation of PAA resin occurring at a given temperature of ≤0 °C. Table 1.3 shows the gelation times at different temperatures and the ID of PAA-(PDMA/ODA) and PAA-(BPDA/PPD). Obviously, the gelation time depended on the temperatures. The higher the temperature, the shorter the gelation times. At 0 °C, PAA-(PMDA-ODA) exhibits a gelation time of 4 h, shorter than 8 h at –5 °C and 17 h at –10 °C, respectively. However, the ID value is almost constant no matter what temperature the gelation occurs at. PAA-(PMDA/ODA) shows ID of about 33.1%-37.2%, higher than PAA-(BPDA/PDA) (ID=21.2%-23.2%), which might be attributed to the backbone rigidity of the PAA resins. The rigid PAA-(BPDA/PDA) resin has low solubility, causing the gelation to occur at a lower level of imidization.
TABLE1.3 Dependence of Imidization Degree and Gelation Time of PAAs on Reaction Temperatures

The effects of temperature on viscosity of PAA were measured using a 10% (w) PAA solution with an initial viscosity of 14.3 Pa·s, which contains dehydrating agents with mole ratios of n[PAA (calculated as repeating units)]: n(acetic anhydride): n(pyridine)=1:2.5:1.5. Fig. 1.9 shows the effect of temperatures on the plot of PAA solution viscosity versus reaction time. At lower temperature of −20 °C, the gelation time can extend to longer than 63.5 h for PAA-(PMDA/ODA), and 49 h for PAA-(BPDA/PDA). At 0 °C, the gelation time is only 4 h for PAA-(PMDA/ODA), and 3.5 h for PAA-(BPDA/PDA), respectively. Increasing the temperature from –20 °C to 0 °C reduced the gelation time from 63.5 h to 4 h for PAA-(PMDA/ODA), and 49 h to 3.5 h for PAA-(BPDA/PDA), respectively.
1.2.2.2 Effect of Molar Ratio of Pyridine to Acetic Anhydride on PAA Viscosity
PAA-(PMDA/ODA) solution (10% of solid concentration) in DMAc has a viscosity of 25.3 Pa·s at –15 °C, the effect of molar ratio of pyridine to acetic anhydride on viscosity is shown in Fig. 1.10. As the molar ratio of pyridine/acetic anhydride increased from 1.5:2.5 to 4.0:2.5, the gelation time decreased from 29 h to 18 h, indicating that the amount of the base catalyst can obviously accelerate the imidization of poly(amic acid) into polyimide.

FIGURE 1.10 Effect of the molar ratios of pyridine to acetic anhydride on viscosities of PAA-(PMDA/ODA) at-15 °C n(Pyridine):n(acetic anhydride): △ 1.5:2.5;■ 2:3; □ 2.5:2.5●3:2.5; ○3.5:2.5; ▲ 4:2.5.
1.2.2.3 Effect of Catalysts on PAA Imidization
The catalysts play an important role in the PAA imidization. PAA-(PMDA/ODA) solution (10% (w) ) in DMAc with a viscosity of 14.3 Pa·s at –15 °C and a ratio of catalyst to acetic anhydride of 1.5:2.5 per mole of PAA was used to investigate the effect of catalyst on PAA imidization. It was found that there was an imidization reaction order: trimethylamine > 3-methylpyridine > pyridine > isoquinoline > 2-methylpyridine (Fig. 1.11). The gelation time for the three former catalysts was 4 h, 24.5 h, 29 h, and 47.5 h, respectively. However, 2-methylpyridine had a very low catalytic effect on imidization, the very weak imidization of PAA in solution could be observed after storage for several days at room temperature. This might be attributed to the steric effect of the methyl group located at the α-position of pyridine ring. Isoquinoline has a gelation time of 47.5 h at −15 °C, which can accelerate the imidization reaction at higher temperature and might be the good candidate for industrial catalyst for polyimide film production line.

FIGURE 1.11 Effects of catalysts on the imidization of PAA-(PMDA/ODA) ○ Triethylamine;● 3-methylpyridine; ■ pyridine; □ isoquinoline; ▲ 2-methylpyridine.
1.2.2.4 Effect of Initial Viscosity on Gelation Time
PAA-(PMDA/ODA) solution (10% (w)) in DMAc with a ratio of catalyst to acetic anhydride of 1.5:2.5 per mole of PAA was used to investigate the effect of initial viscosities on gelation time. The three PAAs with different initial viscosities of 25.3 Pa·s (PAA1), 20 Pa·s (PAA2) and 12 Pa·s (PAA3) at –15 °C was selected. Fig. 1.12 compares the dependence of gelation time on the initial viscosities. Apparently, the gelation time is independent of the initial viscosity. All the PAA solutions with different initial viscosities exhibited almost the same gelation time of 29 h at –15 °C.

FIGURE 1.12 Dependence of gelation time on the initial viscosity of PAA solution ■ PAA 1:25.3 Pa·s ● PAA2:20Pa·s;▲ PAA 3:12 Pa·s.
1.2.2.5 Properties of the Chemically Imidized Films
Table 1.4 compares the effect of stretching ratios on CTE of the fully imidized films. The stretched films exhibit greatly reduced CTEs both in the longitudinal direction (M) and in the transversal direction (T), although the M direction yields lower CTE than T direction. For instance, the unstretched PI-(PMDA/ODA) film has a CTE of 35.1×10-6 °C−1, much higher than the stretched films (8.5×10-6 °C−1 at M direction and 26.4×10-6 °C−1 at T direction with 1.20 stretching ratio). This might be attributed to the high degree of molecular orientation caused by the partial chemically imidized PAA films prior to curing and the stretch drawing during the imidization. The molecular orientation can enhance the polyimide’s dimensional stability and its mechanical properties.
TABLE1.4 CTE Values of the Stretched Polyimide Films(50 °C-250 °C)

Meanwhile, PI-(BPDA/PPD) films exhibit lower CTE than PI-(PMDA/ODA) films under the same conditions, attributed to the fact that the former has a more rigid molecular chain structure of PI-(BPDA/PDA) than the latter. Table 1.5 compares the mechanical properties of stretched polyimide films. Higher tensile strength and modulus have been obtained in the M direction. The films produced by chemical imidization can be stretched at higher stretching ratios, yielding higher strength and modulus than that by thermal imidization.
TABLE1.5 Mechanical Properties of Axially Stretched Films

Overall, the chemical imidization can produce aromatic polyimide films with lower CTE, higher strength and modulus, either in M direction or T direction, than thermal imidization. The gelation time of partly imidized PAA resin was dependent on the ID despite the temperature and the molar ratio of catalyst to acetic acid, it was about 35% for PAA-(PMDA-ODA) and about 22% for PAA-(BPDA/PPD). PAA-(BPDA/PPD) can produce fully imidized film PI-(BPDA/PDA) with higher tensile strength (up to 613 MPa), tensile module (up to 9.3 GPa) and lower CTE than PAA-(PMDA/ODA).