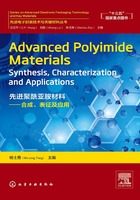
1.3 Thermal Curing of Polyimide Films
The production of aromatic polyimide films is usually performed by a two-step process. The first step involves the synthesis of PAA in aprotic polar solvents, such as DMF, DMAc, or NMP. In the second step, the conversion of PAA by either thermal or chemical imidization produces polyimides. In a typical process, PAA solution was cast on the support surface followed by thermal baking to give a self-standing gelled film. The cast PAA film is imidized to the corresponding insoluble polyimide films by either heating at temperatures in excess of 300 °C (thermal imidization) or through the addition of chemical dehydrating agents (chemical imidization) followed by heating at elevated temperature.
1.3.1 Thermal Imidization Process
During the thermal process, important factors that affect the ultimate properties of polyimide films include the solvent evaporation, polymer chain orientation, chemical conversion, water loss (resulting weight loss in the film), thickness reduction, and change in chain mobility (leading to the development of birefringence). It is very difficult to predict the effect of each factor on the final properties of the film, because all of these factors are interrelated and occur simultaneously. Therefore, a large number of studies have been devoted to investigating the influence under the initial conditions only, such as the chemical structure of the molecules, the thickness of cast films, and the solvents used in the reaction. However, the real-time changes in the backbone structures and the mechanical properties during the imidization process are still unclear.
The thermal imidization process of PAA solution derived from PMDA and ODA in NMP to form polyimide films is divided into three stages: the solvent evaporation stage, imidization stage, and annealing stage. The solvent evaporation stage (the first stage) occurs at low-temperature, the mechanical properties and Tg of polymer films were increased with removal of the solvent. The evaporations of hydrogen-bonded solvents on PAA and the dehydration during the imidization reaction occur above 150 °C (the second stage). During the imidization stage, the interplay between the solvent evaporation and the imidization was the key factor that determined the enhancement of the mechanical properties and Tg. The ID approached 94% when the temperature was increased to 250 °C. A “complete” imidization (the third stage) was achieved by annealing between 350 °C and 400 °C. The enhancement in the mechanical properties of final PI films may result from the increased Tg and the crystallized structure formed during the annealing stage.
Fig. 1.13 shows the ID of PI-(PMDA/ODA) films as a function of the temperature from 70 °C to 300 °C. The ID value started to evidently increase as the temperature increased from 150 °C and reached a constant value at approximately 220 °C. There was no apparent change in the ID above 220 °C because the uncertainty of the FT-IR method was at least 5%, which hindered the accurate determination of the ID at the late stage. According to the curing temperature, the imidization process can be divided into three stages: (1) T < 150 °C: solvent evaporation stage; (2) T = 150° C-250 °C: imidization stage; and (3) T > 250 °C: annealing stage.

FIGURE 1.13 Imidization degree of PI-(PMDA/ODA)films as a function of the temperature from 70 °C to 300 °C.
1.3.1.1 Solvent Evaporation Stage (T<150 °C)
In this stage, the imidization reaction hardly occurs before the temperature reaches 150 °C. The PAA films thermally treated at temperatures of lower than 100 °C are easily dissolved in NMP. The solvent-PAA interactions were established by Brekner and Feger [22,23]. The solvent molecules in PAA films exist in two forms: the free solvent molecules and the molecules that are hydrogen-bonded to the PAA molecules. First, the evaporation of the free solvent molecules occurs at a relatively low temperature to form a PAA film with 4:1 complexes between the solvent and the repeating unit of the PAA, as shown in Fig. 1.14. Then, the decomplexation of the two NMP molecules H-bonded to the amide moiety occurs firstly because they have lower decomplexation energy than the two additional NMP molecules attached to the carboxylic acid moiety. As the temperature increases further, the two additional NMP molecules H-bonded to the carboxylic acid decompose. Experimental results showed that the solvent contents of PAA films thermally treated at 80 °C/0 min and 80 °C/10 min. were between 4:1 and 2:1, indicating the presence of solvent molecules H-bonded to both the amide moiety and the carboxylic acid moiety. The PAA films thermally treated at 100 °C/10 min (PAA-100-10) showed a solvent content close to 2:1, implying that the solvent molecules H-bonded to the amide moiety were almost removed. Hence, the dissociation of H-bonds between NMP and the amide moiety of PAA occurs between 95 °C and 110 °C, and the dissociation temperature range of H-bonds attached to the carboxylic acid appears at approximately 165 °C, implying a difference in the decomplexation energy of these two types of H-bonds. The temperature range of imidization spans from 150 °C to 350 °C, and the maximum reaction rate occurs at approximately 205 °C. The imidization reaction has a broad tail on the high temperature side, and the symmetrical Lorentzian function cannot accurately describe this reaction.

FIGURE 1.14 Schematic illustration of the evaporation of NMP from PAA solution.
1.3.1.2 Imidization Stage (T=150 °C-250 °C)
For an accurate determination of the ID at this stage, NMP molecules are first removed by washing the films with water for 24 h and drying under vacuum at 50 °C for 24 h because NMP is soluble in water. The TGA curves of PAA-100-10 (ID=0) without NMP and the “complete” imidized film PI-400-10 (ID=100%) are used as two references. The weight loss of PAA-100-10 at 400 °C is approximately 8.8%, indicating that NMP molecules have been completely removed (Fig. 1.15). Experimental results indicate that the solvent molecules attached to—COOH have been completely removed once treated above 200 °C for 30 min. The imidization peak is at 270 °C and the residual NMP molecules slightly accelerate the imidization due to the plasticization effect [24]. Therefore, the interplay between the solvent evaporation and the imidization reaction is the key factor that determines the improvement of the mechanical properties and Tg. Because the polyimide film still has an imidization peak near 400 °C in dynamic thermogravimetric ananlysis (DTGA), an annealing procedure is required in the fabrication of a fully imidized polyimide film. The changes in Tg with ID are an important issue during the thermal imidization. The interplay between Tg and ID is very complex. Tg increases as ID increases, and a higher Tg will prevent further imidization because the chain diffusion slows down below Tg.

FIGURE 1.15 Dependence of derivative weights on temperature.
DMA was used to determine the Tg [25,26]. The temperature, at which the maximum rate of turndown of the storage modulus (E′) occurs or the temperature at the loss modulus (E″) and tan δ peaks, can be considered to be Tg. As the temperature increases, E′ exhibits two drops, in which the first drop corresponds to the Tg of the samples, which is very close to the treatment temperature. Both the evaporation of the solvent and the imidization reaction can result in an increase of the storage modulus, thus, the drop in the E′ curves can be an indicator of the glass transition. The second drop that occurs at 370 °C may correspond to the Tg after the imidization is completed. It is supported by the result for PAI-250-30 (ID=94%), and there is only one drop on the E′ curve, which occurs similarly at 370 °C.
Lastly, PAI-150-30 (ID=19%) shows a very low solubility (~4%) in NMP, even after the sample is immersed in the solvent for 10 days. PAI-200-30 and PAI-250-30 are insoluble in NMP, indicating that the interchain imidization reaction forms a cross-linked percolation network at ID ~ 19% [27]. However, the form of intermolecular links and the relative proportions depend on the reaction conditions and the type of imide molecules used [22,23].
1.3.1.3 Annealing Stage (T>250 °C)
The annealing procedure is required for the fabrication of polyimide films because the imidization reaction has a broad tail on the high-temperature side. Because PI-400-10 is considered a complete imidization film, ID values of the other samples are calculated from the weight loss at 400 °C as 97% and 99% for PI-300-60 and PI-350-60, respectively. This reflects the clear temperature dependence of the imidization reaction. Fig. 1.16 shows the DMA results of the samples. E′ in the glass region is app roximately 2.9 GPa for PI-400-10. The Tg obtained from the tanδ curves gradually increases from 395 °C for PI-300-60 and from 440 °C for PI-400-10 and PI-400-60. Therefore, the elevated annealing temperature especially above Tg increases the Tg and the storage modulus, and the annealing treatment is critical to the final properties of the polyimide film. It should be noted that PI-400-10 and PI-400-60 does not display an E″ peak and their E′ decreases gradually during the transition region. These features may relate to the broad order-disorder transition.

FIGURE 1.16 DMA curves of the polyimide films at a frequency of 1 Hz and a heating rate of 5 °C/min.
Fig. 1.17 compares the mechanical properties of the polyimide films at different stages. Generally, the mechanical properties of the samples gradually increase as the thermal treatment temperature increases. At the solvent evaporation stage, the tensile strength and the Young’s modulus of PAA films increase from 38 MPa and 1.6 GPa to 68 MPa and 1.8 GPa, respectively. The improvement in the mechanical properties is mainly due to the removal of the solvent. At the imidization stage, the tensile strength and the tensile modulus of the PAI films increase to 100 MPa and 2.4 GPa (2.4 GPa for E′ from the DMA results). As the thermal temperature and the ID increase, the in-plane orientation of the molecular chain and Tg can be further improved [28]. Finally, the effect of the annealing temperature on the mechanical properties is obvious, although there is only a slight increase in ID. The tensile strength and the Young’s modulus for the PI samples increase from 120 MPa and 2.5 GPa (2.5 GPa from the DMA results) for PI-300-60 to 150 MPa and 2.8 GPa (2.9 GPa from the DMA results) for PI-400-10 without losing the elongation at breakage. However, the PI-400-60 film exhibits the highest Young’s modulus (3.0 GPa), but it loses the elongation at breakage. The mechanical properties of the films are closely related with the Tg (the right x-axis), and the improved mechanical properties may be the result of the ordered structure of the molecular chains, which are induced by annealing. Therefore, annealing near the Tg of the samples induces crystallization in polyimide films, and such a prominent annealing effect has been reported in the literature [29,30]. Conclusively, the imidization is completed by annealing at 400 °C and the crystallization degree increases as the annealing time increases. When annealing is conducted at 400 °C, the weight of the film decreases rapidly during the initial heating step due to the secondary imidization, and it continues to fall slowly as time elapses. This indicates that a long annealing time at 400 °C can cause the decomposition of the film, which may damage the properties of PI films. Thus, the optimized treatment condition may be between 350 °C/60 min and 400 °C/10 min.

FIGURE 1.17 Tensile strain-stress curves of the films with different imidization degree.
Fig. 1.18 summarizes the changes in ID, tensile properties, and Tg of PAA films at three different imidization stages. In the solvent evaporation stage, the imidization reaction does not occur, and the effect of solvent evaporation determines the changes in mechanical and thermal properties that occur in the samples. The mechanical properties and Tg of the PAA films have been improved gradually due to the evaporation of solvent. Two types of solvents, which are attached to —NH or —COOH, can be distinguished by TGA and DTG. In the imidization stage, the ID of the samples can also be accurately monitored by TGA. The changes in the stiffness and the inplane orientation of the chains results from the imidization reaction. The tensile strength (100 MPa) and the Young’s modulus (2.4 GPa) of the PAI-250-30 sample (ID=94%, Tg=393 °C) are similar to the values obtained for the final PI films. The annealing at 350 °C-400 °C can further improve the properties of PI films due to the “complete” imidization and the development of the crystallized structures.

FIGURE 1.18 Changes of imidization degree,tensile properties and Tg of PAA films at three different imidization stages.
Overall, the imidization process include three stages. During thermal imidization, there are obvious influences of curing process conditions on the physical and chemical evolutions of PAA-(PMDA/ODA) in NMP. An optimized condition (100 °C/10 min, 250 °C/30 min and 400 °C/10 min) has been recommended to fabricate high-quality polyimide films by a discontinuous process. A TGA method is developed here to accurately determine the ID; moreover, it can quantitatively distinguish the locations of solvent evaporation and the imidization reaction. These methods can be used to investigate the thermal imidization process for other polyimide systems with different chain structures and/or different solvents.
1.3.2 Influence of Curing Temperatures on Film’s Properties
Table 1.6 compares the film properties of two different polyimides as a function of final curing temperatures ranging from 250 °C to 450 °C. At 350 °C, the stiff PI-(BPDA/PDA) film has a high birefringence (naverage=1.7637, Δn=0.1979), low CTE (αin-plane=(3±1)×10-6 °C-1), and high modulus (E=7.3±1 GPa), indicating that the polymer has high in-plane chain axis orientation. In contrast, the relatively flexible PI-(PMDA/ODA) film has a low birefringence (naverage=1.6869, Δn=0.0708), higher CTE (αin-plane=(26±1)×10-6 °C-1), and low modulus (E=2.3±1 GPa), consistent with low in-plane chain axis orientation. The PI-(BPDA/PDA) film shows a stress level (δ) of 2±1 MPa, much lower than PI-(PMDA/ODA) film (δ=17±1 MPa), probably due to the increase in the CTE mismatch between the polyimide film and the underlying substrate.
TABLE1.6 Properties of Polyimide Films as Function of Final Curing Temperatures of 250 °C-450 °C

The influence of final curing temperature on morphology and properties of polyimide films are dependent on the chemical backbone structures of the polyimides. PI-(BPDA/PDA) film (Tg=340 °C) shows increases in optical anisotropy (Δn), which is gradual from 0.1826-0.2186 with rising of the curing temperature from 250 °C to 400 °C. The PI-(PMDA/ODA) film remains relatively constant with curing temperature up to the glass transition temperature, and then increases dramatically from 400 °C to 450 °C above the glass transition temperature (Tg=420 °C).
Changes in the average refractive index are generally due to changes in density. Polyimide film increases its density with an increase in crystallinity. The average refractive index of PI-(BPDA/PDA) film increases only slightly with curing temperature up to 400 °C, while PI-(PMDA/ODA) film remains relatively constant with curing temperature up to 350 °C, and then increases significantly at higher curing temperatures. The crystallinity in PMDA/ODA film increases when cured above the glass transition temperature.
The stress in PI-(BPDA/PDA) film is low at a curing temperature of <350 °C, and then rises sharply at a higher curing temperature (400 °C) (Table 1.6). Similar results are observed in PI-(PMDA/ODA) film, where the stress increases only slightly at curing temperatures of lower than its Tg. The stress level rises significantly at curing temperatures of higher than Tg. This is attributed to the semicrystalline nature of the polyimide films. The semicrystalline polyimides can sustain stress above their glass transition temperatures because the modulus remains relatively high. In addition, shrinkage forces resulting from density increases contribute to increases in the in-plane stresses.
Fig. 1.19 compares the ID as a function of curing temperature for two different polyimide films (PI-(PMDA/ODA) and PI-(BTDA/ODA-MPD). At lower temperatures, the ID varies significantly with the chemical structures of the polyimide films. At 250 °C, all the polyimides show ID of over 95%. The ID increases gradually from 95% to 100% by heating at 250 °C-350 °C. The ID of PI-(PMDA/ ODA) material appears to decrease by about 4% from its maximum at 350 °C to 450 °C, probably attributable to the development of crystallinity. It was found that the imide group in PI-(BPDA/PDA) preferentially aligns parallel to the plane of the film [31].

FIGURE 1.19 Imidization degree as a function of curing temperatures for three different polyimide films.
PI-(PMDA/ODA) film cured at 400 °C shows a broad glass transition at approximately 420 °C by DMA, compared with PI-(BPDA/PDA) with a broad and slightly more prominent glass transition observed at 340 °C. The broad glass transitions are attributed to the semicrystalline morphology, and the small magnitude is due to both the polyimide backbone stiffness and the presence of crystallinity. The Tg of PI-(PMDA/ODA) film was measured at about 420 °C, which is not affected by the changes in final curing temperatures. The magnitude of glass transition is also not affected by curing temperatures of up to 350 °C. However, the magnitude decreases slightly at the curing temperature of 400 °C and reduces sharply at 450 °C. This is attributed to the increase in crystallinity in PI-(PMDA/ODA) films cured near or above the glass transition temperature.
The (004) peak in X-ray diffraction patterns of PI-(BPDA/PDA) films cured at 400 °C is very prominent in transmission and absent in reflection. This is due to the preferential alignment of the chain axis in the plane of the film. The (002) diffraction peak of PI-(PMDA/ODA) film is prominent in transmission yet barely visible in reflection, due to the preferential alignment of the chain axis in the plane of the film. The reflection and transmission scans show some evidence of crystalline order. However, the crystalline peaks are not very prominent and are overshadowed by the more prominent broad amorphous peak. The (002) peak of PI-(PMDA/ODA) film in transmission increases in magnitude with changes in the curing temperatures. Other diffraction peaks are sharper and more prominent in the film cured at 450 °C, evidence of higher crystalline order. This behavior is consistent with the behavior observed by DMA.
PI-(PMDA/ODA) and PI-(BPDA/PDA) films are stiff and anisotropic with lower in-plane CTEs and stresses. These polyimides crystallize when cured above their glass transition temperatures. Due to the relatively high glass transition temperature (420 °C), PI-(PMDA/ODA) does not have appreciable crystallinity when cured using a standard heating rate of 2 °C/min up to temperatures as high as 400 °C. The birefringence and the average refractive index in PI-(PMDA/ODA) film remain relatively constant up to 400 °C. However, the birefringence decreases slightly at 400 °C, then increases significantly at 450 °C. PI-(BPDA/PDA) film is slightly more rigid and linear than PI-(PMDA/ODA). The stiffness and linearity of PI-(BPDA/PDA) lead to a higher degree of anisotropy. The birefringence increases gradually with curing temperature up to the region of the glass transition (350 °C). At 400 °C, the birefringence index and the average refractive index increase substantially. These increases are attributed to increases in crystalline order and in density.
The molecular anisotropy in polyimide films has a dramatic effect on both in-plane and out-plane CTEs. Because the coefficient of volumetric expansion (CVE) is constant, unaffected by orientation [32], the out-of-plane CTE increases while the in-plane CTE decreases with increasing in-plane chain axis alignment. The CVE can be measured from specific volume vs. temperature measurements. PI-(BPDA/PDA) film shows only a gradual increase in the slope of the specific volume data in the temperature range of the glass transition by DMA (340 °C), consistent with the less prominent and relatively broad glass transition observed by DMA. PI-(BPDA/PDA) film shows an in-plane CTE of 6×10-6 °C−1 and an out-of-plane CTE of 144×10-6 °C−1, compared with PI-(PMDA/ODA) film which has an in-plane CTE of 33×10-6 °C−1 and an out-of-plane CTE of 126×10-6 °C−1, respectively. The anisotropy nature of the CTEs is an important functional property which is extremely sensitive to molecular orientation. PI-(BPDA/PDA) film exhibits obvious anisotropy, has an out-of-plane CTE of 25 times larger than the in-plane CTE. This sensitivity of CTE to molecular orientation must be taken into account in designing polyimide films for microelectronic applications.