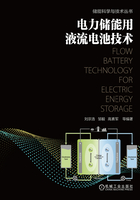
3.1.1 功率单元
电堆是全钒液流电池系统充放电反应发生的场所,是全钒液流电池系统内最为核心的关键部件。电堆是由多个单电池以叠加形式紧固的、具有多个管道和统一电流输出的组合体。单电池通常由端板、集流板、电极框、电极、离子传导膜、极板以及相关密封件构成。单电池结构如图3-3a所示。电堆由多个单电池串联的形式构成,两个单体电池之间由双极板实现连接,如图3-3b所示。
液流电池电堆分别设计了正负极电解液的进口和出口,以及电解液公共流道和分支流道,以便于正负极电解液在循环泵的驱动下将电解液在电堆内部各节单电池中均匀分配,实现多孔电极内部活性物质的循环更新,如图3-4所示。
电堆内部单体电池之间通过双极板实现连接。双极板是电子导电性材料,同时需具有液体和气体不透性,以便阻隔正负极电解液。双极板既是一个单体电池的正极,也是相邻单体电池的负极,充放电过程中,两个相邻单体电池正负极间电子的收集和传递通过双极板完成,最终实现电堆内部多个单体电池间的电子传递,以保证电堆内部各单体电池电化学氧化反应的正常进行。电堆内部的电极材料通常为具有多孔结构的碳材料,比如炭毡、石墨毡等,电解液在其中流过,活性物质离子在电极材料表面发生电化学氧化或电化学还原反应,电极材料不参与反应,只是为反应提供反应界面。活性物质离子发生电化学氧化还原反应过程中失去或得到的电子均由电极材料接收和提供。电极材料需要有较高的电导率、比表面积和电化学活性,以降低充放电过程中的欧姆极化和电化学极化,提高电堆的能量转换效率。每个单体电池正负极由离子传导膜隔开。离子传导膜不仅用于分隔正负极活性物质离子,避免电池内部短路,而且要保证电池内部电解质溶液中的质子或其他离子形成离子通路,维持充放电过程正负极电解液的电中性。为防止电池正负极电解质溶液中的活性物质发生互串,要求离子传导膜具有较高的离子透过选择性。对于活性物质离子,透过率越低越好,有利于提高电池的库仑效率。对于维持充放电过程中正负极电解液电中性的质子或特定离子,透过率越高,离子传导产生的欧姆极化越低,有利于提高电堆电压效率,从而最终提高电堆能量转换效率。

图3-3 单电池及电堆结构

图3-4 电堆内部电解液循环示意图
在实际开发和应用电堆时,有两个技术参数指标需要重点关注,一个是标称功率指标,另一个是能量效率指标。电堆的标称功率和能量效率是密切相关的,在不同的充放电功率下,电堆的能量效率是不同的。另外,不同的充放电功率下,电堆实际运行的电流密度也是不同的。因此,描述一个电堆的性能指标需要在一定的限定条件下进行,充放电功率和能量效率缺一不可。
电堆的能量效率与其库仑效率和电压效率密切相关。库仑效率的主要影响因素涉及电堆内部离子传导膜针对活性离子的选择性、充放电过程中副反应程度以及电堆本体自身的漏电功率三方面。离子传导膜针对电解液中活性离子的选择性越高,在充放电过程中正负极活性离子通过离子传导膜的相互渗透量越低,电堆的库仑效率越高。电堆在充放电过程中,通常会在正负极电极表面发生不同程度的副反应。以全钒液流电池为例,如果出现充电电压上限过高或者电解液失衡等因素,会导致在正极电极材料表面发生析氧副反应,在负极电极材料表面发生析氢副反应。副反应的发生使得充放电过程中的电子没有得到有效利用,导致电堆的库仑效率降低。同时副反应的发生还会对电堆内部电极材料性能的长期稳定性产生不利影响。电堆正负极电解液在各个单电池内部的输送及分配由电堆内部的电解液公共管路和单电池分支管路完成。电解液公共管路的存在使得单电池之间通过具有离子导电性的电解质溶液将各自的正负极串联起来,形成了内部导电通路。多节电池串联形成的电压差,使得电堆内部产生了漏电电流。电堆因为漏电电流的存在,进一步产生能量的损耗,降低了电堆的库仑效率。
为了提高和改善电堆库仑效率,需要选择具有较高离子选择性的离子传导膜材料和较高析氢或析氧过电位的电极材料。在电堆充放电控制方面,要制定合理的充放电上下限电压,尤其是上限电压,以尽量降低副反应发生程度。为降低电堆内部漏电电流,要对其串联电压及电解液公共管路和分支管路结构和尺寸进行优化设计,提高公共管路和分支管路内的漏电电阻,降低漏电电流。同时还要兼顾电堆内部电解液在各单电池间的分配均匀性和活性物质的充分更新,最大程度降低浓差极化的产生,也会进一步降低电池副反应的产生。
电堆电压效率是在规定的条件下,电堆的放电平均电压与充电平均电压的百分比值。电压效率的主要影响因素是电堆充放电过程中的电化学极化、欧姆极化和浓差极化。电池有电流通过时,由于活性物质电化学反应进行的迟缓性,造成电极带电程度与可逆情况时不同,从而导致电极电势偏离的现象为电化学极化。电化学极化与电池电极材料的电化学活性、电流密度、温度等密切相关。电堆内部电解液、电极材料、离子传导膜、双极板等的欧姆电阻导致电堆内部欧姆极化的产生。充放电末期活性物质供应或更新的充足与否决定浓差极化发生的程度,活性物质供应不充分或更新速度较低都会导致浓差极化的产生,使得电化学反应发生的电势差更进一步加大,并促使副反应的产生。要想获得高的电压效率,需选择具有高电化学活性的物质作为电极材料,并开发与之相适应的具有高电导率的电解质体系,同时,尽量减小电堆内部离子传导膜、双极板等欧姆电阻及各部件间的接触电阻。另外,针对浓差极化,要制定合理的电解液流量策略,使得在充放电末期电堆内部保持充足的电解液流量,降低浓差极化发生的程度。
相比于固态电池,液流电池还有一个导致电堆电压损失的因素是电堆内部通过电解液公共管路产生的漏电电流。漏电电流的存在使得充放电过程中充电电压平台提高、放电电压平台降低,导致电压效率降低。因此,通过电堆内部电解液公共管路结构设计的优化,降低电堆内部电池间漏电电流也是提高电堆电压效率的有效手段之一。
提高电池的库仑效率及电压效率都有助于提高电池的能量效率。目前,针对提高电堆能量效率的研究开发工作均围绕如何改善和提高电堆的库仑效率和电压效率这两个方面开展。
电堆成本在液流电池储能系统总成本占有较大比重。如何有效降低电堆成本是目前电堆开发面向实际应用需要关注的重要问题。提高电堆充放电电流密度,开发高功率密度电堆是有效降低电堆成本的关键举措。需要说明的是,开发高功率密度电堆的前提是保持其能量效率在一定基准值的基础上。即电堆充放电电流密度的提高,不得以牺牲电堆的能量效率为代价。提出上述前提是因为电堆本身具有一定的过载能力,可以进行2倍和更高倍率的过载充放电,而在这种情况下的电堆能量效率会出现大幅下降。
高功率密度电堆的开发涉及较多方面的问题。随着电堆电流密度的提高,电堆内阻、电解液流量及分布、温度分布及热量管理等对电堆性能的影响敏感性都变得越来越高。为了解决上述问题,电堆设计需要从关键材料、电堆结构、流体供应与分布等多方面出发,提出降低电堆极化、改善电堆内部流体及温度分布均匀性、减小电堆内部漏电电流的解决方案,提高电堆工作电流密度的同时,兼顾电堆单电池间的一致性、可靠性等问题。
电堆的开发是国内外从事全钒液流电池技术研究的学术界及产业界的主要工作方向之一,通过技术进步,进一步开发高功率密度电堆,是提高电堆综合性价比的有效途径,相关工作概述如下。国内中科院大连化学物理研究所联合大连融科储能技术发展有限公司、上海电气有限公司、中科院金属研究所联合朝阳华鼎储能技术发展有限公司、中国工程物理研究院、北京普能世纪科技有限公司等单位均有kW以上级全钒液流电池电堆的报道。国外从事全钒液流电池技术产品的公司主要以日本住友公司为代表,面向全钒液流电池产品开发及应用,开发了一系列不同规格的电堆。
中科院大连化学物理研究所从21世纪初开始电堆的开发工作,先后开发了1kW、5kW、10kW电堆,其中2007年开发出的10kW电堆为国内首创,电堆充放电电流密度达到65mA/cm2,能量效率达到80%以上,如图3-5所示。
2008年,中科院大连化学物理研究所与大连博融控股有限公司联合成立大连融科储能技术发展有限公司,电堆技术开发及工程化能力得到快速发展。为满足大规模电池储能市场针对全钒液流电池高功率储能单元需求,在电堆电极框结构设计、模拟仿真、电极材料优选等方面投入了大量人力和物力,于2009年开发出国内最大的额定功率达22kW的全钒液流电池电堆,如图3-6所示。该电堆工作电流密度达到80mA/cm2,能量效率达到80%以上。该电堆通过国家能源局科学技术成果鉴定,鉴定结论认为该电堆达到国内领先、国际先进水平。

图3-5 10kW电堆

图3-6 22kW电堆
2013年,中科院大连化学物理研究所和大连融科储能技术发展有限公司在国家重大基础研发计划——“973”计划支持下,对于影响电堆性能的关键因素进行了深入分析,通过优化电堆结构和开发高活性电极材料,进一步降低了电堆内阻,开发出新一代31.5kW电堆,电堆工作电流密度达到120mA/cm2。该电堆工作电流密度相比22kW电堆,电流密度提高了50%,如图3-7所示。应用31.5kW电堆通过四串两并的方式构成250kW功率单元,目前已经在国内实施的多个微网项目中得到应用,电堆性能稳定,系统运行可靠。该电堆以及250kW功率单元也被应用在国家能源局大连200MW液流电池调峰电站项目中。
中科院大连化学物理研究所联合大连融科储能技术发展有限公司在多年电堆开发工作的积累上,在电堆工作电流密度上实现了进一步突破,于2017年开发了工作电流密度超过180mA/cm2的42kW电堆,如图3-8所示。融科公司采用该型号电堆集成出了125kW/500kWh全集装箱系统。该产品主要面向室外大规模全钒液流电池储能系统。

图3-7 31.5kW电堆

图3-8 大连融科42kW电堆
目前,中科院大连化物所研究团队正在致力于更高工作电流密度电堆技术的开发,通过持续的电池结构优化设计和材料创新,电堆工作电流密度已经提高至200mA/cm2,且电池能量效率达到了82%以上。该研究团队正在向工作电流密度达到或接近300mA/cm2的目标而努力。

图3-9 Gen1 5kW电堆
北京普能世纪科技有限公司是2007年创立的一家从事全钒液流电池储能技术研发、制造的公司。公司早期开发了5kW电堆,电堆能量效率达到75%,如图3-9所示。
普能公司为适应全钒液流电池技术在大规模新能源领域的推广应用,开发了功率达30kW以上的新型电堆,电堆工作电流密度得到一定幅度的提高。该电堆工作电流密度达到100mA/cm2,电堆能量效率达到75%以上,如图3-10所示。
上海电气有限公司于2017年开始从事全钒液流电池技术及产品的开发。致力于全钒液流电池在核能、风电等新能源与可再生能源领域的应用。目前,上海电气已经开发出了额定功率达31.5kW和50kW的全钒液流电池电堆(见图3-11),但电堆的工作电流密度及能量效率未见报道。

图3-10 普能30kW电堆

图3-11 上海电气研发液流电池电堆
中科院金属研究所联合朝阳华鼎储能技术发展有限公司开发出了10kW电堆,中国工程物理研究院也报道开发出了5kW电堆及10kW电堆工程化样机,但没有报道具体的工作电流密度。中国工程物理研究院电子工程研究所开发的10kW电堆工程化样机,如图3-12所示。样机运行能量效率达到71%。电堆能量效率同其他公司开发的电堆相比要较低一些。
日本住友电工从20世纪80年代开始开发全钒液流电池技术及产品,其中,全钒液流电池电堆开发是其技术开发的重点工作之一,开发了不同规格的电堆,并取得了多项电堆方面的专利。
住友电工在21世纪初开发了42kW电堆,如图3-13所示。该电堆应用在了2005年实施的4MW/6MWh风电场配套储能项目。据报道,该电堆能量转换效率达到了80%以上,工作电流密度约为60mA/cm2。

图3-12 中国工程物理研究院电子工程研究所开发的10kW电堆工程化样机

图3-13 日本住友电工42kW电堆
2007年,日本住友电工暂时停止了全钒液流电池储能技术及产品的开发,直至2011年恢复该项工作。随后几年内,先后在横滨和北海道建设了1MW/5MWh和15MW/60MWh全钒液流电池储能系统。储能系统采用的电堆如图3-14所示。电堆标称功率为31.25kW,具备2倍过载运行能力。电堆工作电流密度的数据未见报道。

图3-14 日本住友电工31.25kW电堆
如上所述,电堆是全钒液流电池储能系统内最为核心的关键部件。其性能及成本对于全钒液流电池系统的性能及成本具有重要影响。从提高电堆性能的角度出发,电堆开发的主要方向是提高能量效率。降低电池内阻、改善离子传导膜活性物质离子选择性,改进电堆结构降低电堆内部漏电电流等几个方面是提高电堆能量效率的关键技术开发方向。从降低成本的角度出发,电堆开发的方向是提高电堆的工作电流密度。提高电堆的能量效率与工作电流密度是相辅相成的、密切相关的。同一个电堆,在不同的工作电流密度下,呈现出不同的功率输出,因此,电堆能量效率与工作电流密度的标称,或者说与电堆额定功率的标称是相互关联的,在确定一个基准能量效率的前提下,确定电堆的工作电流密度或额定功率才是有意义的。额定功率标称值过高,电堆能量效率必然降低。而从储能技术应用的角度出发,过低的能量效率是不能够得到市场认可的。目前,通常情况下,电堆能量效率的基准值设定为不低于80%(直流)。在上述基准值的基础上,工作电流密度的提高或额定输出功率的增大会降低电堆的单位kW成本,有利于性价比的提高。
除了关注能量效率和工作电流密度之外,开发大功率电堆也是全钒液流电池产品发展的需求。通过开发大功率电堆,并通过串并联一定数量的电堆组成更大功率的功率单元,可为构建独立并网和接受调度的大功率全钒液流电池储能单元奠定基础,这对于电力系统用大规模电池储能系统的运行及管理具有非常重要的意义。从国内外公司电堆开发的历程中可以明显地看到上述趋势。然而,大功率电堆的开发,除了提高电堆工作电流密度之外,还需要通过增加电堆内电池电极工作面积或增加电池节数的手段实现。为增加电池的电极工作面积,电堆的部件比如电极框、双极板、电极材料、离子传导膜、密封材料等尺寸都要相应增加,而因电极工作面积放大导致的电堆内部流量分布不均、温度分布差异增大、密封难度增加等等问题的出现也是电堆开发需要关注和重点解决的问题。上述问题的解决对于电堆运行的长期稳定可靠具有重要意义。另外,随着电堆重量和体积的进一步加大,也会给电池系统产品在安装、运维时增加一定的难度,也是产品开发需要考虑的重要方面。因此,针对电堆的开发,应该从以上各方面进行统筹考虑。