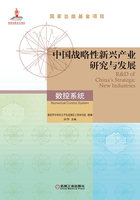
1.3.1 数控系统的工作原理
1.数控加工与传统加工的比较
在普通机床上加工零件的过程,是机床操作者根据工序卡及零件要求,在加工过程中不断改变刀具与工件的相对运动轨迹和加工参数(如位置、速度等),使刀具对工件进行切削加工,从而得到所需要的合格零件的过程。
在数控机床上,传统加工过程中人工操作均被数控系统自动控制所取代。其工作过程如下:首先将被加工零件图样上的几何信息和工艺信息数字化,即将刀具与工件的相对运动轨迹、加工过程中主轴速度和进给速度的变换、切削液的开关、工件和刀具的交换等信息,按规定的代码和格式编成加工程序,接着将该程序送入数控系统;数控系统按照程序的要求,先进行相应的运算、处理,然后发出控制命令,使各坐标轴、主轴动作及辅助动作相互协调,实现刀具与工件的相对运动,自动完成零件加工。
2.数控加工中的数据转换过程
数控系统的主要任务就是将由零件加工程序表达的加工信息(含几何信息和工艺信息)转换成各进给轴的位移指令、主轴转速指令和辅助动作指令,控制加工轨迹和逻辑动作,加工出符合要求的零件。数控系统工作原理如图1-1所示。

图1-1 数控系统工作原理
1)译码(解释)。译码部分的主要功能是以程序段为单位,将用文本格式(通常是ASCII码)表达的零件加工程序转换成刀补处理程序所要求的数据结构。该数据结构可用于描述一个程序段解释后的数据信息,主要包括X、Y、Z等坐标值,进给速度,主轴转速,G代码,M代码,刀具号,子程序处理和循环调用处理等数据或标志的存放顺序和格式。
2)刀补处理(计算刀具中心轨迹)。零件加工程序通常是按零件轮廓编制的,而数控机床在加工过程中控制的是刀具中心的轨迹,因此在加工前必须将零件轮廓变换成刀具中心的轨迹。刀补处理部分的功能就是完成上述转换。
3)插补计算。零件加工程序以数控系统规定的插补周期Δt定时运行,它将由各种直曲线(如直线、圆弧等)组成的零件轮廓,按程序给定的进给速度f,实时计算出各个进给轴在Δt内位移(如ΔX1、ΔY1……),并将该信息送给进给伺服系统,实现成形运动,插补计算部分的作用就是实现上述功能。
4)PLC控制。数控系统对机床的控制分为两类:一类是对各坐标轴的速度和位置的轨迹控制;另一类是对机床动作的顺序控制,或称逻辑控制。后者是指在数控机床运行过程中,以数控系统内部和数控机床各行程开关、传感器、按钮、继电器等开关量信号状态为条件,并按预先规定的逻辑关系对诸如主轴的起/停、换向,刀具的更换,工件的夹紧、松开,液压、冷却、润滑系统的运行等进行的控制。PLC部分就是实现上述功能的模块。
数控系统的工作原理是通过利用数字、文字和符号组成的数字指令来实现一台或多台机械设备的动作控制,包括位置、角度、速度、压力、温度等的控制。数控系统的主要任务就是将由零件加工程序表达的加工信息转换成各进给轴的位移指令、主轴转速指令和辅助动作指令,控制加工轨迹和逻辑动作,加工出符合要求的零件。