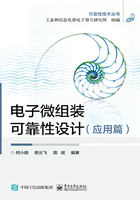
2.2.3 VDMOS热生成与微米尺度热区
VDMOS管(垂直双扩散场效应晶体管)是DC/DC实现直流电压高低变换的关键器件,采用开关工作方式提高变压器的工作效率。在DC/DC中,VDMOS的开关频率在100~200kHz范围内,感性负载下工作,承受高尖峰电压和大电流,具有较高的开关损耗和温升,引起VDMOS内部多种退化机制,是DC/DC的“短板寿命”器件之一。VDMOS的沟道温度是影响性能退化的最重要的应力因素,因此确定VDMOS的热生成区和尺度,是热仿真模拟的重要基础,也是评价VDMOS热性能和工作寿命的重要环节。
1.VDMOS热生成机制
VDMOS在开关工作中,由于存在能量损耗,在沟道内产生大量的热,使器件芯片沟道区域温度升高并产生局部热点,而沟道温度的高低,是影响VDMOS参数温漂和时漂的重要因素。
半导体器件的热生成有四种来源:焦耳热、复合热、汤姆逊效应和幅尔贴效应。在稳定状态下,半导体器件的热生成模型可以用式(2-7)[7]来表示。这一模型比较系统、详细地描述了晶体管内部的热生成机制:

式(2-7)右边的第一项,表示在器件有源区的焦耳热生成;第二项,表示电子和空穴的复合热生成;第三项,表示汤姆逊效应引起的热生成。
1)焦耳热生成
焦耳热生成是VDMOS的主要热生成机制,可以用电子、空穴及半导体晶格系统所组成的复杂热动力系统来解释。对于n沟道VDMOS器件,沟道区中可动电荷(电子)受到沟道水平加速电场及栅氧化层垂直电场的共同加速作用[8],所以电子的温度会因其平均能量比平衡时高很多而升高。同时,电子与电子、电子与声子、电子与材料界面以及电子与缺陷或者杂质原子之间在这一过程中都会发生散射,但其中电子与声子之间的散射,即晶格振动才有净能量损耗,因此晶格吸收了额外的能量而引起温升,这种由于电子与声子散射而产生热的过程就是焦耳热生成。
2)复合热生成
复合热生成在器件耗尽区也是一种热量的来源,产生于每个电子与空穴的复合过程。半导体器件的复合热来自R-G中心复合热、俄歇复合热、辐射热三种[9]。其中,R-G中心复热产生过程是在电子失去能量后,与空穴在价带同时消失,并且释放出热量,如图2-7所示;俄歇复合热产生过程是两个电子或两个空穴互相碰撞,直接复合释放能量,如图2-8所示。

图2-7 R-G中心复合

图2-8 俄歇复合
3)汤姆逊效应热生成
汤姆逊效应热生成决定于温度梯度的大小,是局部温度差异或者是掺杂浓度差所引起的[10]。局部温度差异引起的汤姆逊效应在低温环境下较为明显,从低掺杂区向高掺杂区过渡时需要考虑掺杂浓度差带来的影响。
上述三类热生成机制中,焦耳热生成的作用最为明显,复合热生成、汤姆逊效应的作用较小,计划可以忽略。所以,由式(2-7),VDMOS的热生成可近似用式(2-8)表示。

2.微米热区与3D建模
焦耳热生成是VDMOS器件的主要热生成机制,热耗散区域主要集中于每个单胞的沟道电阻区、积累层电阻区、颈部电阻区和外延层电阻区,构成了VDMOS每个单胞的导通电阻,如图2-9所示。VDMOS的沟道电阻区和积累层电阻区的电流密度分布最高,其次是颈部电阻区,最小的是外延层电阻区。
本案厚膜DC/DC用VDMOS的微观结构纵向剖面SEM分析结果,如图2-10所示。图中从上到下各膜层依次为金属Al层、SiO2钝化层、poly多晶硅层和SiO2栅氧化层,各膜层典型厚度分别为3μm、1μm、0.63μm和0.1μm[12]。由于VDMOS的芯片设计结构,由众多六边形单胞并联而成,因此在芯片热分析的实体建模中,将焦耳热最集中也是电流密度最高的沟道热生成区进行适当简化处理后建模,以VDMOS芯片表层μm级尺度(厚度),作为VDMOS的热生成加载区域。
建立VDMOS的3D实体模型如图2-11所示,其中:芯片尺寸为3.890mm×1.880mm×0.279mm。图2-12所示为VDMOS 3D实体模型横截面(宽度与厚度未按真实比例),沟道电阻区和积累层电阻热功耗加载区域有效厚度取1μm,宽度为单胞宽度的一半即940μm,颈部电阻区和外延层电阻区热功耗加载区域宽度均取470μm,厚度分别取91μm和182μm,芯片表面Al金属化层取1.4μm[14]。

图2-9 VDMOS单胞导通电阻构成

图2-10 VDMOS的微观结构纵向剖面SEM分析结果

图2-11 VDMOS的3D实体模型

图2-12 VDMOS 3D实体模型横截面